Challenges of Backpanel Plating
Introduction
Hopefully, this will be the first in a series of articles relating to challenges faced when plating backpanels, and other more technically advanced, multi-featured pwbs. For purposes of this discussion, we’re assuming a minimal backpanel thickness of .250” (6.35 mm); however, as being noted in later articles, plating a .350”-.400” (8.89-10 mm) board can present some
additional challenges.
When medium technology pcb firms succeed in plating (to spec) pane ls in the .125” (3.17 mm)
range with an 8:1 aspect ratio, they often assume that progressing from this level to backpanels will involve a series of logical steps, but with few obstacles. Unfortunately, this is NOT the case, and speaking from our experiences as designers/manufacturers of automated plating and pulse equipment, we have had the luxury of viewing these situations from a perspective as “total systems’ suppliers” where we have seen firsthand the large number of important variables that MUST to be considered when plating backpanels with DC, (even more so with pulse). Presumably, this and subsequent articles will provide the reader with a reasonable overview so that many of these matters will be at least considered in advance of moving ahead.
Backpanels Plating
Often, the first realization that “things are truly different when plating backpanels” comes when one attempts to physically lift one of these larger panels by hand, perhaps doing so in a manual, prototyping plating tank, as the size, weight, and even the particular circuit pattern likely is not conducive to be run concurrently with other panels on an existing automated line which is dedicated to more “average,” thinner boards. Additionally, the average board, rack, anode dimensional “windows” will typically be inadequate to accommodate these much larger panels. It is also likely, if processed on a manual tank, that vertical spline racks will be a necessity on both sides of the panel, due to the physical challenges of carrying the weight, and adequately bringing current to the board. It is interesting to note, also, that most recently designed/built automated platers utilize top loading racks only. This will likely be a difficulty requiring inherent flexibility in the control systems, where different workbars with different racks can be brought to potentially different plating stations, and allow the work to be plated for widely varying plating times.
There are various sorts of issues that need to be discussed (chemical, physical, scheduling, etc.,), however, in this first article, we will limit our discussion primarily to SOME of the many “physical” issues unique to plating backpanels. The number and kinds of physical issues should NOT be minimized, as these can be far reaching. For example:
- A pwb manufacturer considering the purchase of a new automated line which MAY need to run
some backpanels, should allow for sufficient depth to accommodate a potentially deeper board. It may or may not make sense to provide this added depth and elongated anodes in every cell, which goes back to the matter of the inherent intelligence of the main control system. - Similarly, one must determine if the plating line will be equipped in whole (or part) with
vibration, as the more robust and flexible of these can be very expensive. Therefore, one may wish to provide only specific workbars (or specific plating stations) that may be used for backpanels or boards with very small holes, thus saving money. Additionally, one must decide whether to use exclusively vertical spline racks rather than top-loading types, recognizing that the latter DO have an advantage in terms of surface distribution due to their “continuous” surface (no interruption). Our experience has been that top-oading racks will work for backpanels but only when there is either a bottom support member, or tooling provisions are made to actually “engage” the panels with registration holes at the top, insuring the boards cannot be vibrated “off”
the rack. There is a debate (even with bottom support and tooling) about whether vibration using top-loading racks can be as effective as when using top quality vertical racks. - There are many designs for vibration, some on the workbar and others on the tank rim or support structure. There are even patented designs requiring expensive frequency drives for each station allowing the workbar (via the main control system) to cycle through a wide range of frequencies, thereby optimizing the results).
- Depending on whether one elects to panel or pattern plate the boards, one should re-check the assumptions relative to maximum panel circuit density so as to determine if existing rectifiers (and/or pulse equipment) is adequately sized. Two things to consider here:
- Backpanels (vs. normal pattern plated work) often have large groundplanes on one side which require more amperage.
- Backpanels often have significant numbers of holes. This can be very deceptive, as the surface area of a large number of holes in a very thick panel can, in some cases, exceed the surface area of the circuitry on the panel, and often does. Unless thought about in advance, this might mean that rectifiers on an existing line need to be replaced to accommodate backpanels.
- If pulse plating IS utilized (beware that this is, in and of itself, a VERY involved topic that will only be minimally touched upon in this first article), then one will, by definition, be plating at a much higher current densities than with DC plating, another instance where existing rectifiers may be very much undersized!
- The design and quality of racks is also a potential concern, especially if pulse plating, as one needs to be certain there is adequate current carrying capacity, and that the integrity of the contacts are sufficiently robust to both transmit the current and vibration.
- Another advantage to using vertical racks with backpanels is the ability to design these with the ability to readily affix the required “shielding” or “thieving.” Unlike simpler panels that are normally “mass-produced” and even automatically loaded and unloaded, one should anticipate that the “payload” on a workbar of backpanels will likely be less. The value added on these types of panels dictates the care that needs to be taken when processing (vs. simpler panels).
- The additional amperage loading on the system required by these higher amperage panels
(especially if using pulse) also requires investigation of existing tank saddles, on-tank bussing (and if pulse is utilized the potential of inductive loads), cooling, etc., - Consideration of methods of both mechanical and solution agitation are also much more critical with backpanels as the need to transport and avoid depletion of the metal ions within the deeper holes is more challenging. Hopefully, this first article which discusses the more obvious “physical-only” issues relating to plating backpanels (vs. thin, less complicated boards), provides the reader with a preview of some of the more involved technical challenges that can be anticipated with these kinds of products. In the next article we will attempt to visit some chemical issues, and touch on IST testing and the
physical properties of the copper electroplating deposit, as well as the advantages (vs. additional challenges) of utilizing pulse when plating backpanels vs. DC plating. While the results with pulse are significantly better than with DC (see the cross section this page), one MUST view this additional challenge within the context of truly a “total systems’ approach,” as ALL of the physical issues discussed here are still in effect, but further complicated with when utilizing pulse.
By
Neil Baker
President
Baker Technology Associates Incorporated
Respectfully Submitted:
Jacket Wu
Executive Vice President
U-TAH Industrial Co., Ltd.
- CHAL(5832)
相關(guān)推薦
如何使用環(huán)境變量進(jìn)行Linux提權(quán)的方法詳細(xì)資料概述

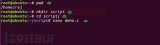
20位1 MSPS隔離模擬輸入數(shù)據(jù)采集參考設(shè)計(jì)包括BOM及層圖
3GPP W-CDMA系統(tǒng):設(shè)計(jì)和測(cè)試
3G無(wú)線電的ADPA和數(shù)字收發(fā)器的設(shè)計(jì)和測(cè)試
Agilen的E6474A無(wú)線網(wǎng)絡(luò)優(yōu)化平臺(tái)
DDR內(nèi)存概述,開(kāi)發(fā)周期和挑戰(zhàn)
DVB-T和DVB-T2發(fā)射機(jī)測(cè)試挑戰(zhàn)
DVB-T和DVB-T2接收機(jī)測(cè)試挑戰(zhàn)應(yīng)用筆記
IP和VoIP技術(shù)
Keysight acceSS7:US West使用監(jiān)控和故障排除
N1996A CSA頻譜分析儀演示指南
N4915A-005串行總線開(kāi)關(guān)應(yīng)用
PAM4設(shè)計(jì)挑戰(zhàn)及其對(duì)測(cè)試的啟示
PCI Express 3.0 Testing Approaches for PHY and Protocol Layers
RF和微波:PCB中的設(shè)計(jì)挑戰(zhàn)-Design Challenges in PCBs
STM32的加解密硬件模塊
五項(xiàng)新技術(shù)將徹底改變高速系統(tǒng)
使用是德科技的無(wú)線數(shù)據(jù)優(yōu)化服務(wù)N4145A,最大限度地提高數(shù)據(jù)網(wǎng)絡(luò)性能
光纖數(shù)字I/O技術(shù)的測(cè)試挑戰(zhàn):如何減低升級(jí)到光纖技術(shù)的風(fēng)險(xiǎn)
關(guān)注802.11ax
印刷電路板測(cè)試和檢驗(yàn)解決方案
基于電感式傳感LDC的事件計(jì)數(shù)設(shè)計(jì)
如何測(cè)試USB Type-C Alt模式及其運(yùn)行標(biāo)準(zhǔn)
存儲(chǔ)器接口生成器(MIG)解決方案
微波放大器設(shè)計(jì)資料全集 PDF下載
抖動(dòng)基礎(chǔ):Keysight 81250 ParBERT抖動(dòng)注入和分析功能
支持高達(dá)1.5A的快速充電電流和低至1mA的充電精度TIDA-050007
有限訪問(wèn)板下一代ICT解決方案
測(cè)試混合模式UE:Keysight的DO-cdma2000測(cè)試解決方案
混合動(dòng)力和電動(dòng)汽車DC:DC轉(zhuǎn)換器設(shè)計(jì)和測(cè)試的新興解決方案
混合動(dòng)力和電動(dòng)汽車DC:DC轉(zhuǎn)換器設(shè)計(jì)和測(cè)試的新興解決方案白皮書(shū)
移至1500 V光伏逆變器的優(yōu)勢(shì)應(yīng)用說(shuō)明
精確的混頻器轉(zhuǎn)換損耗測(cè)量技術(shù)
緊湊的24位RGB到OLDI/LVDS接口TIDA-010013
美國(guó)西部新矢量集團(tuán),使用監(jiān)控和故障排除
解決醫(yī)療設(shè)備的設(shè)計(jì)和測(cè)試挑戰(zhàn)解決方案手冊(cè)
調(diào)試DDR設(shè)計(jì)中的信號(hào)完整性和協(xié)議層
ALLEGRO PCB ROUTER L, XL

CADENCE SIP DIGITAL SI

CADENCE SIP RF LAYOUT

CADENCE SIP RF ARCHITECT

Future Challenges For Research And Teaching In Pow-1.

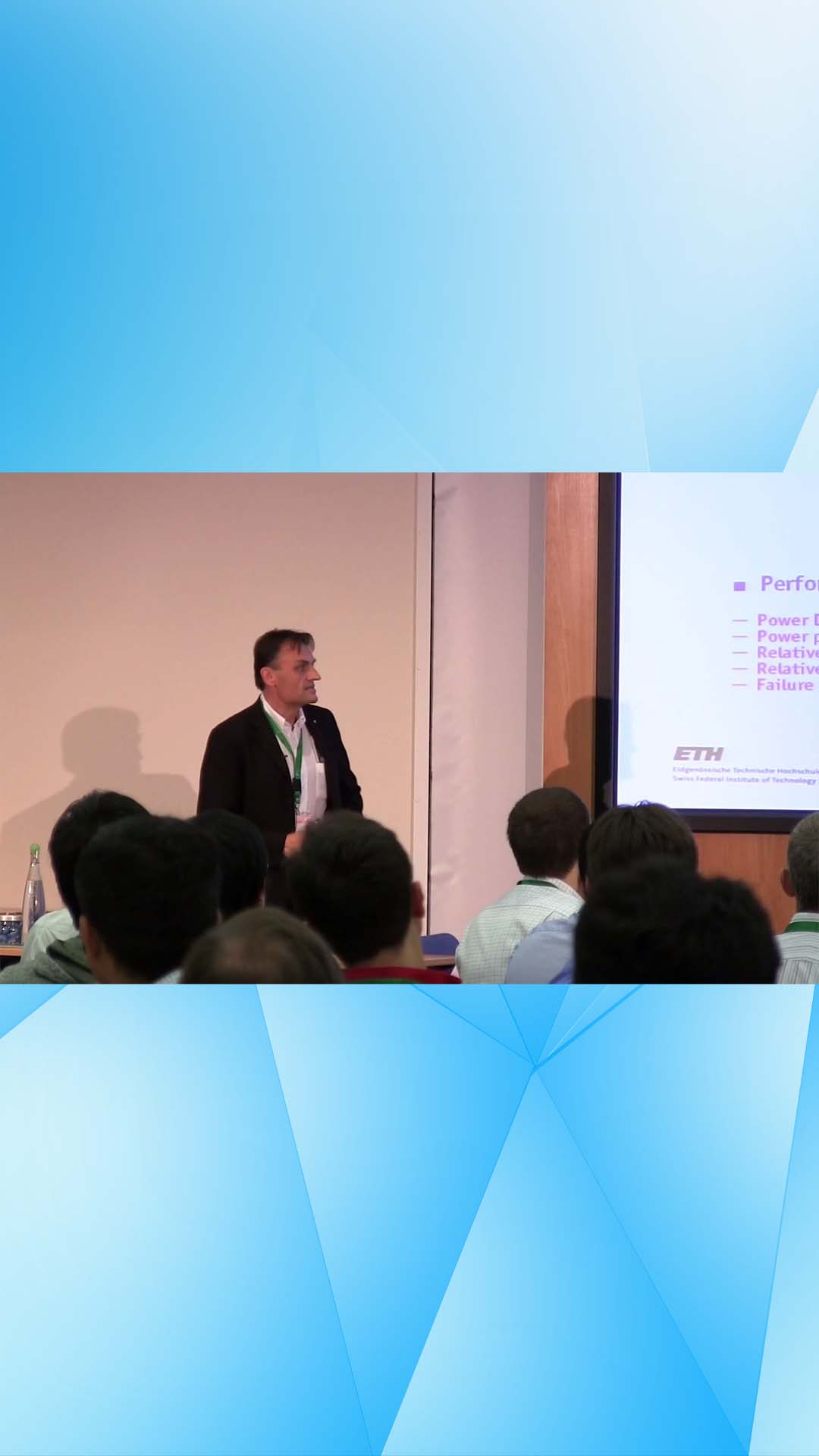
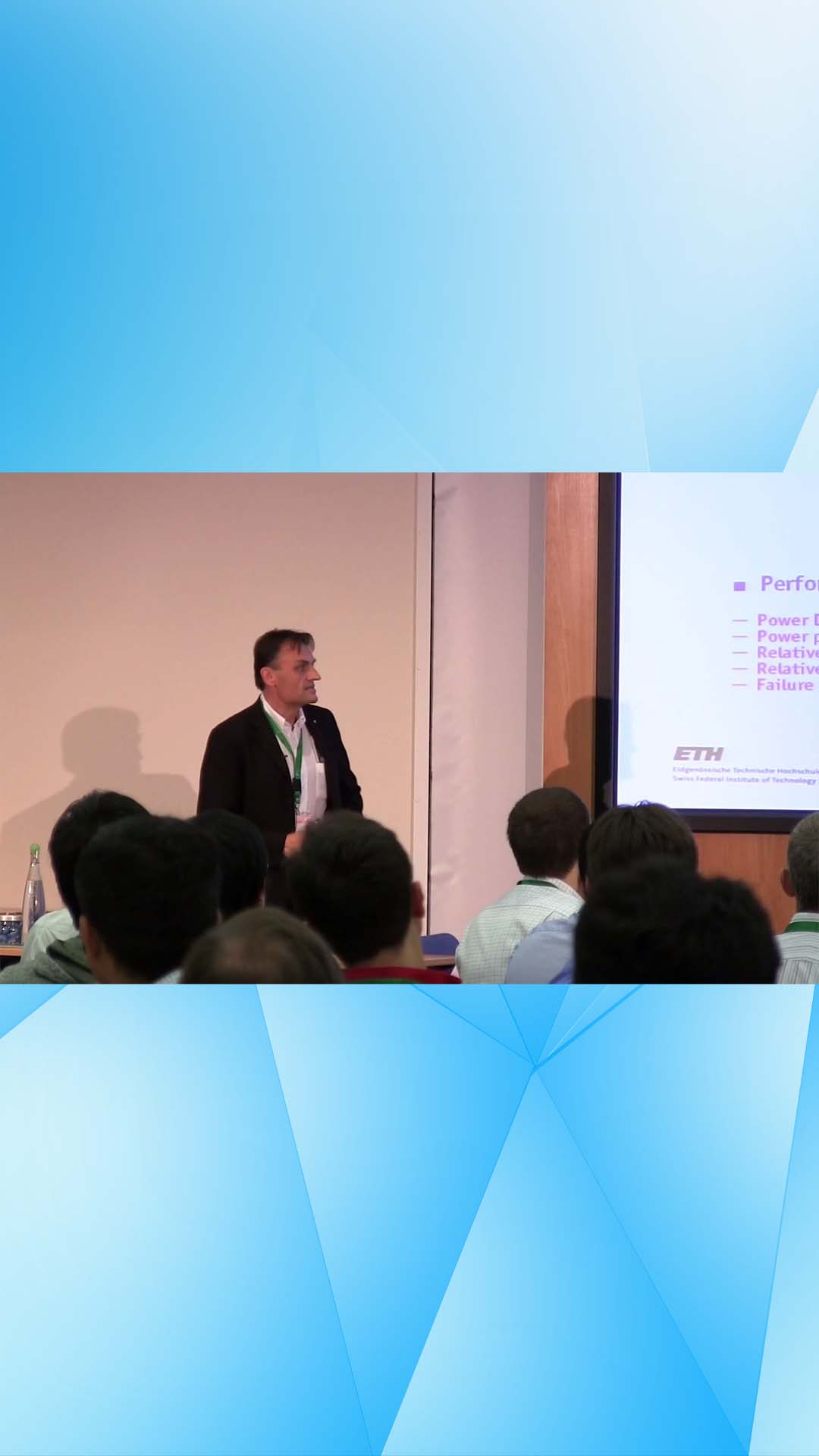
Future Challenges For Research And Teaching In Pow-2.

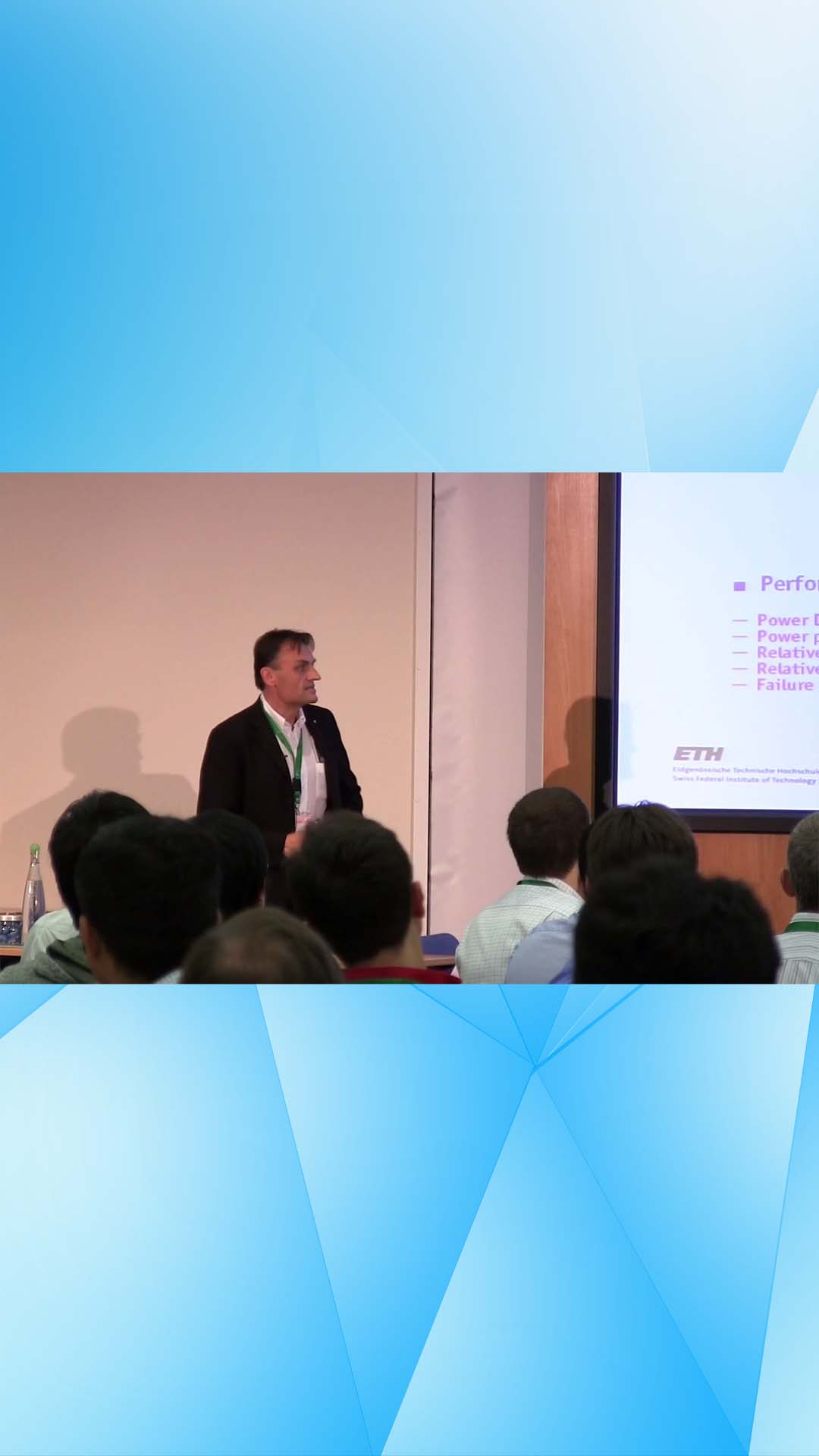
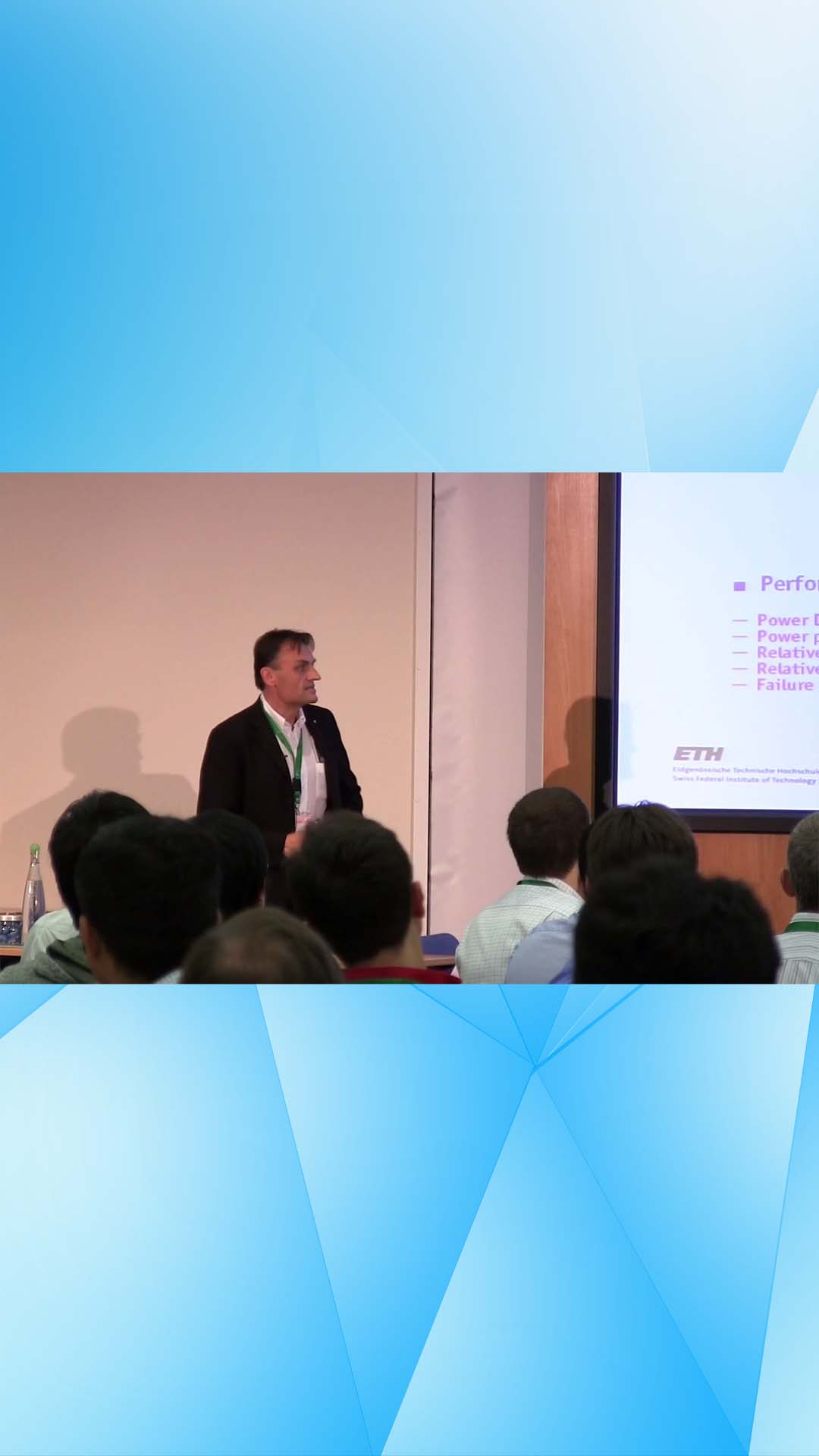
Future Challenges For Research And Teaching In Pow-3.

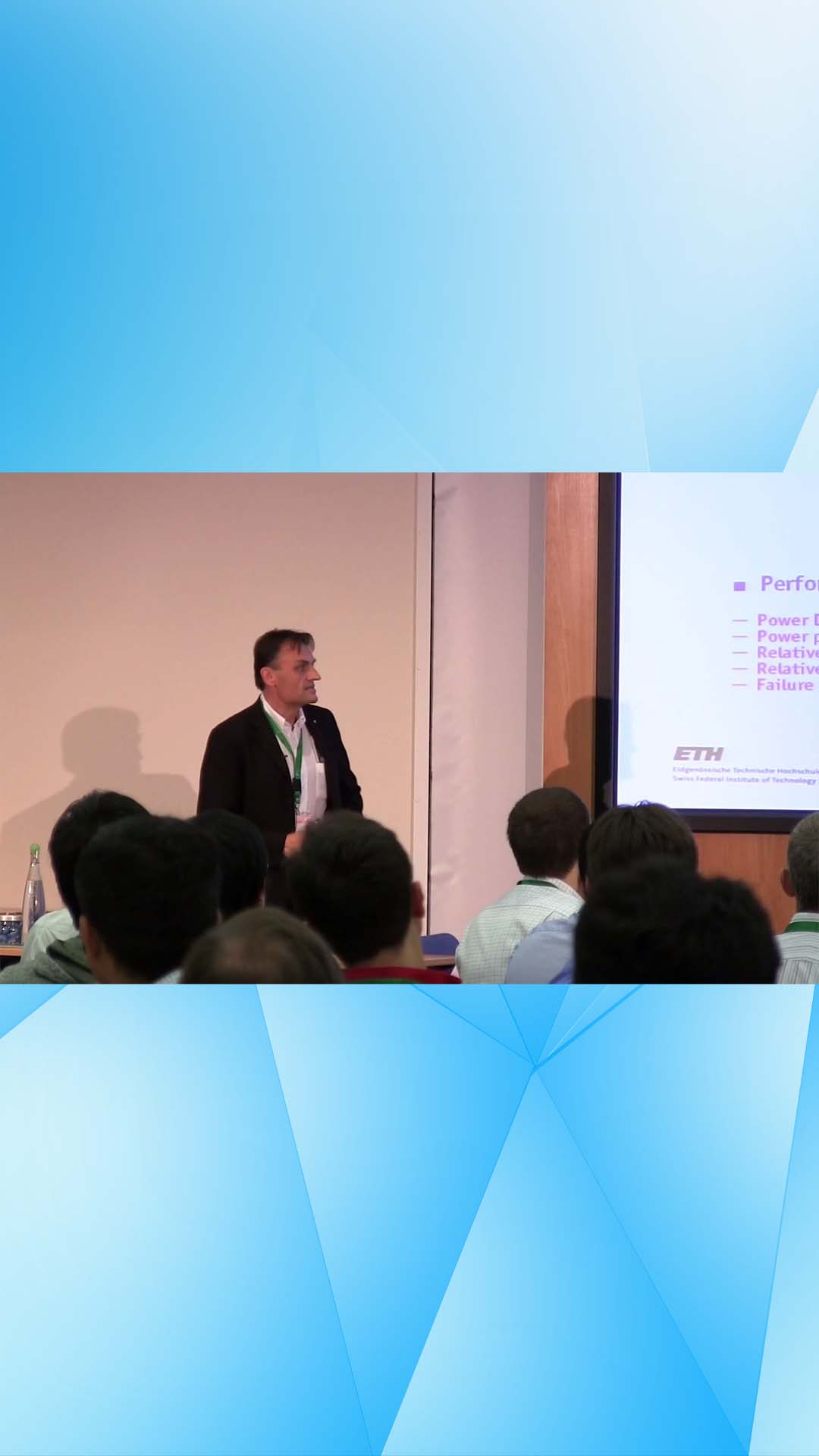
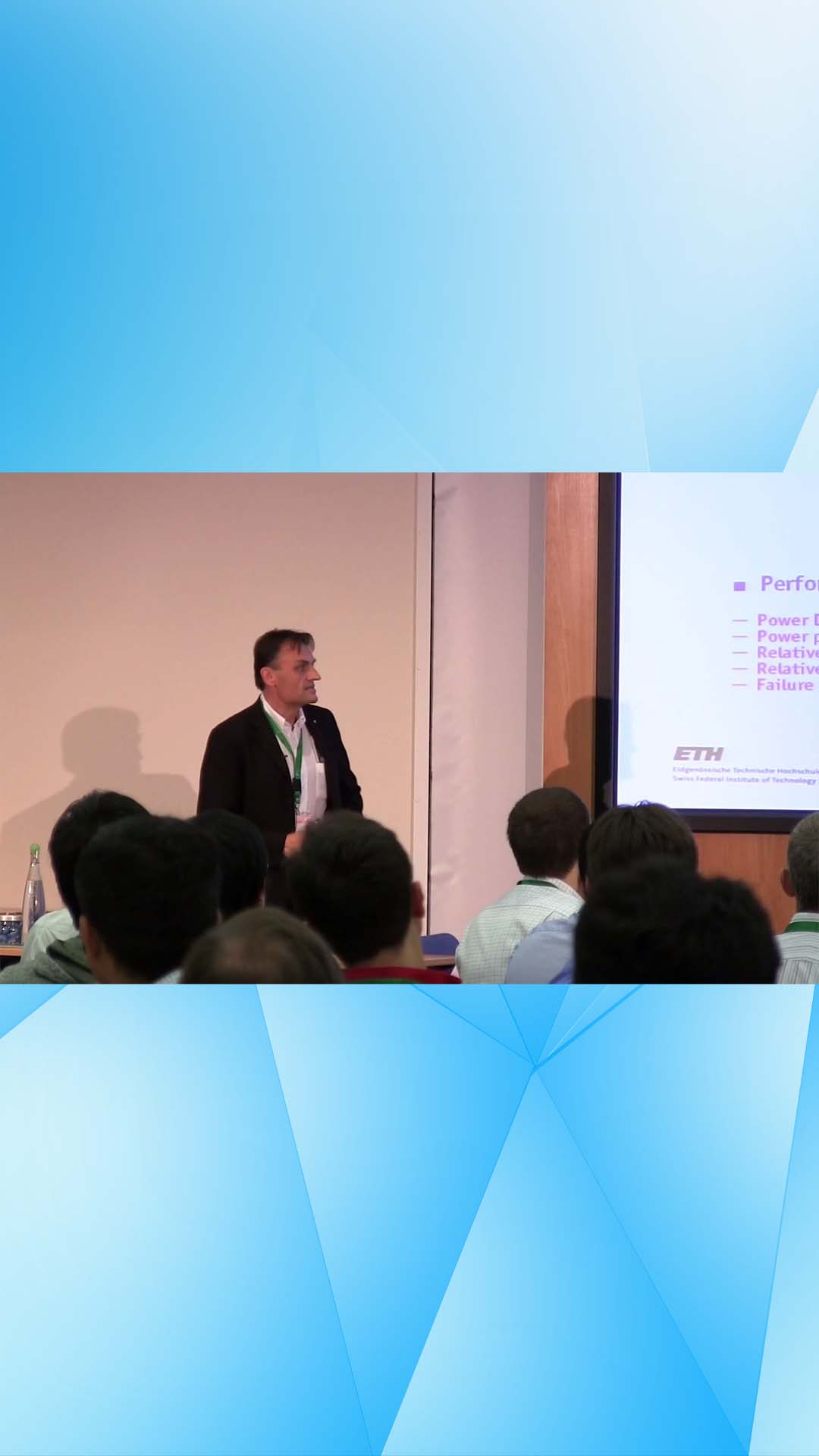
Future Challenges For Research And Teaching In Pow-4

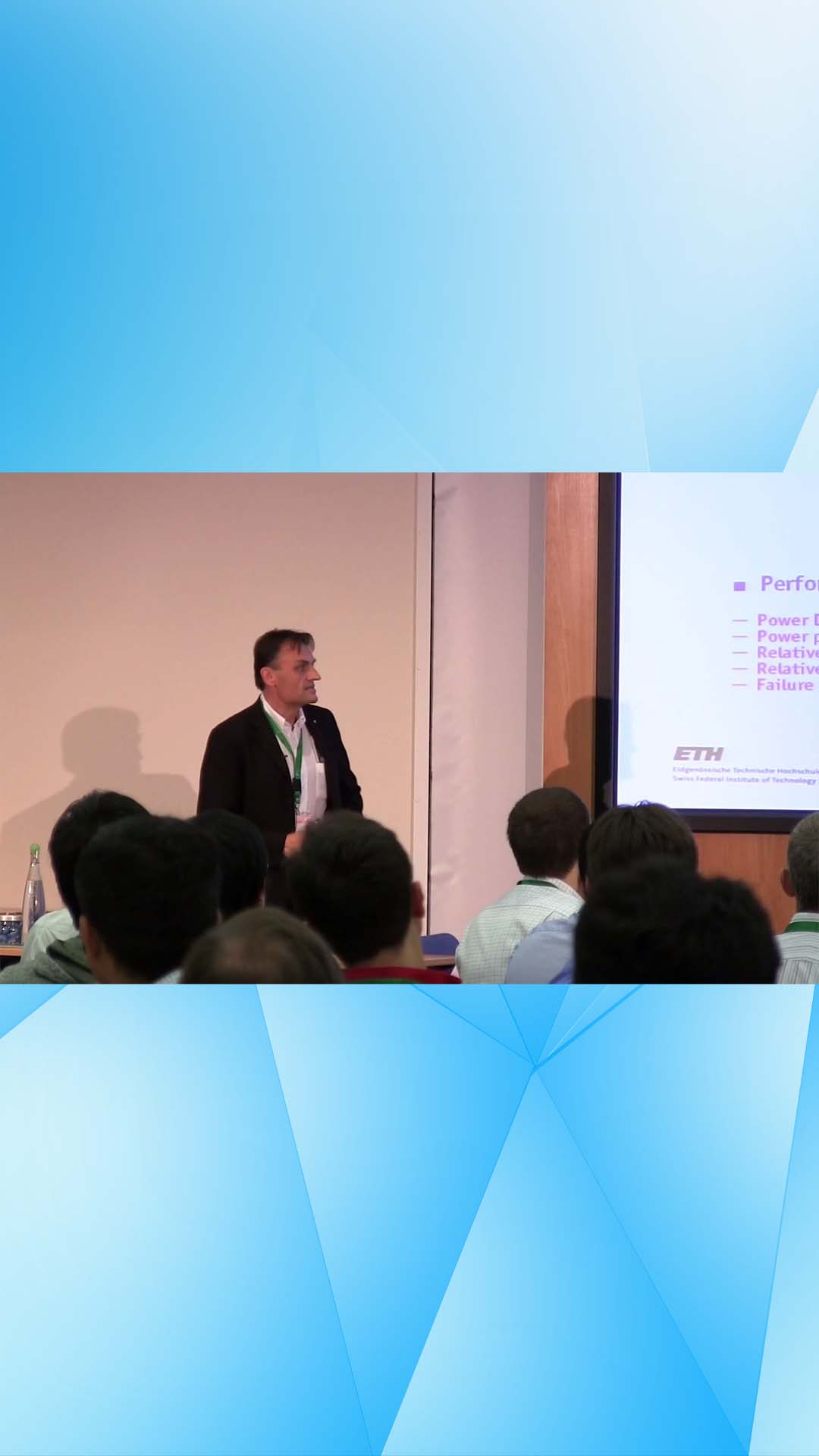
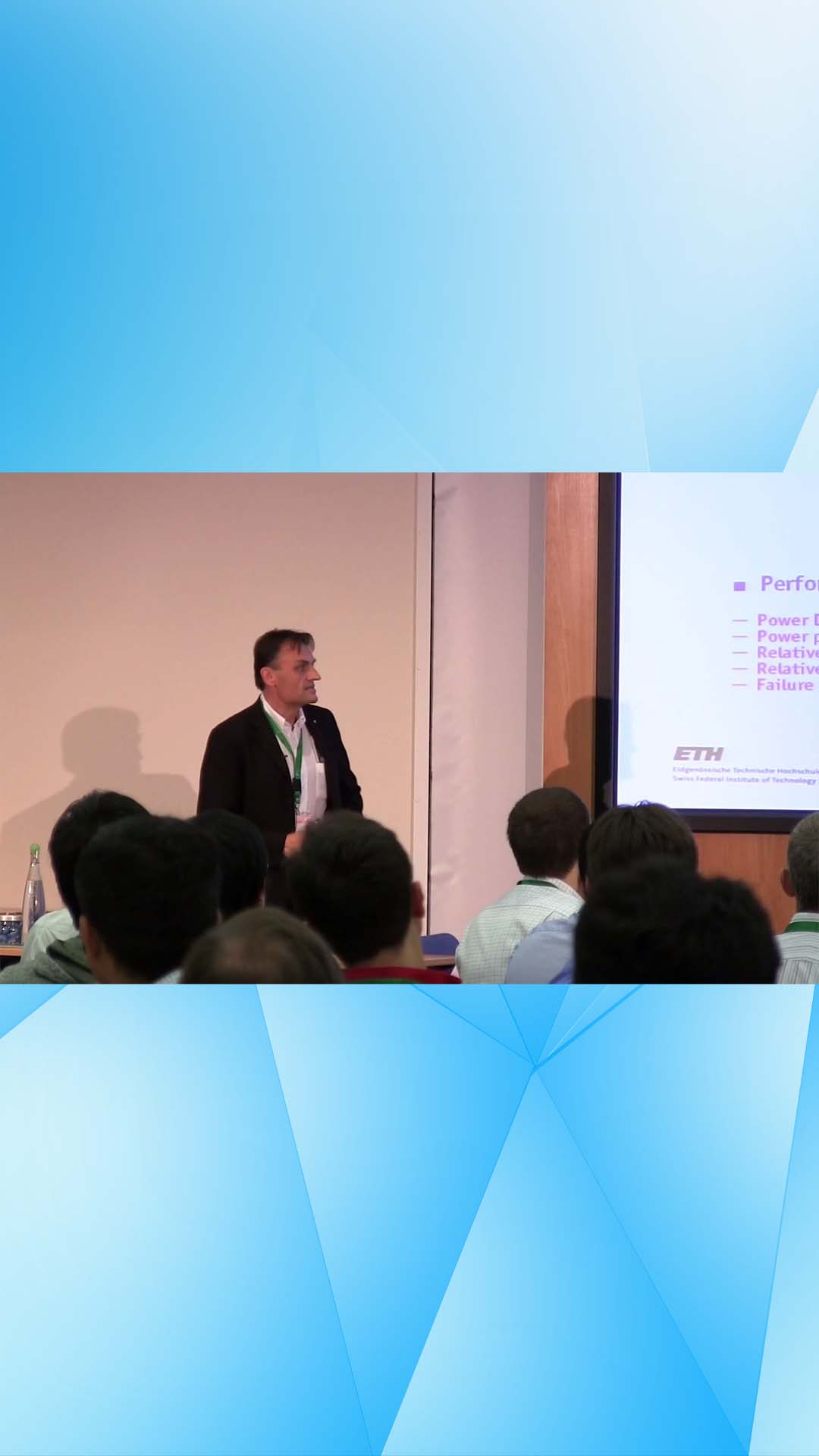
Future Challenges For Research And Teaching In Pow-5

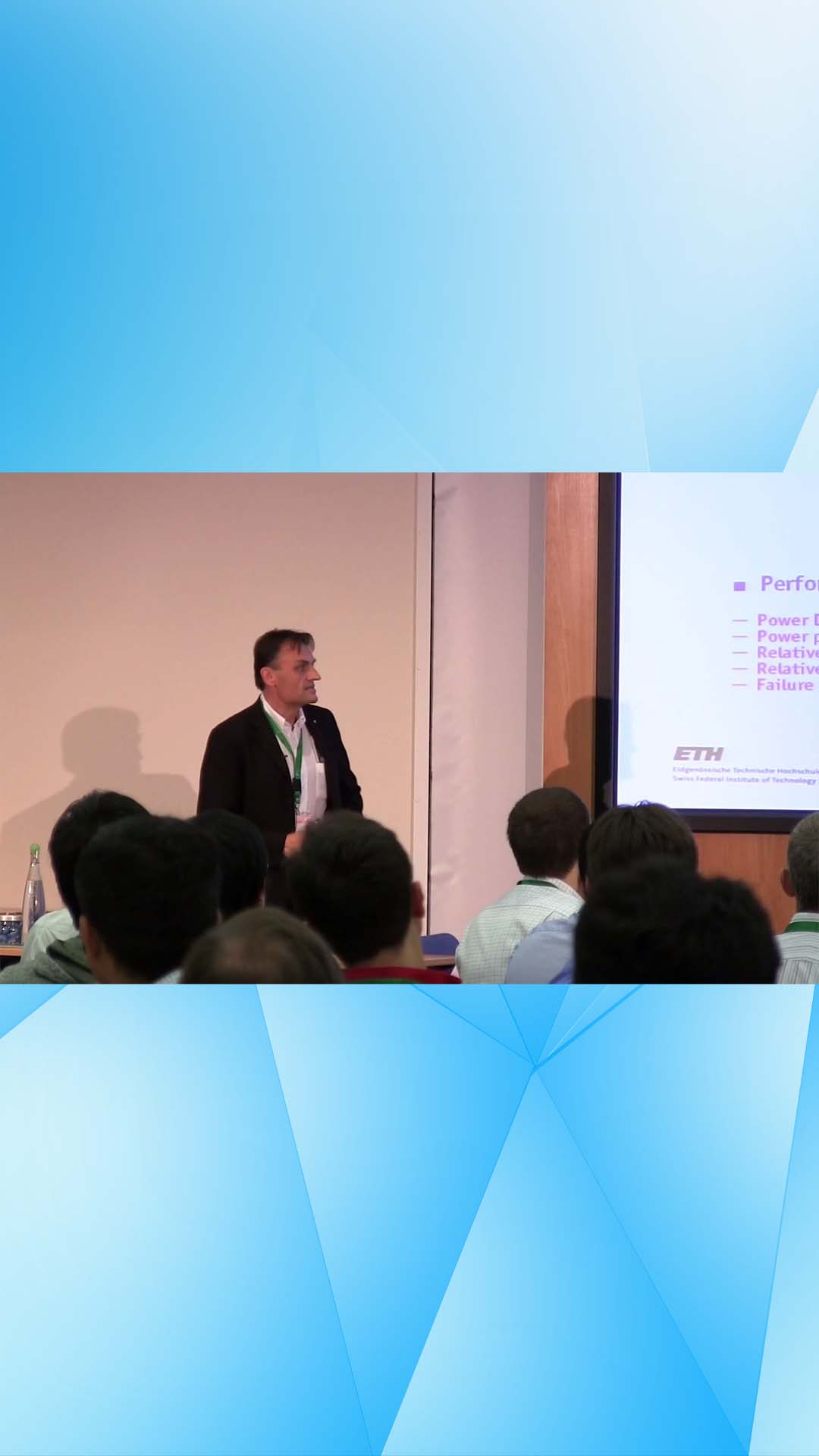
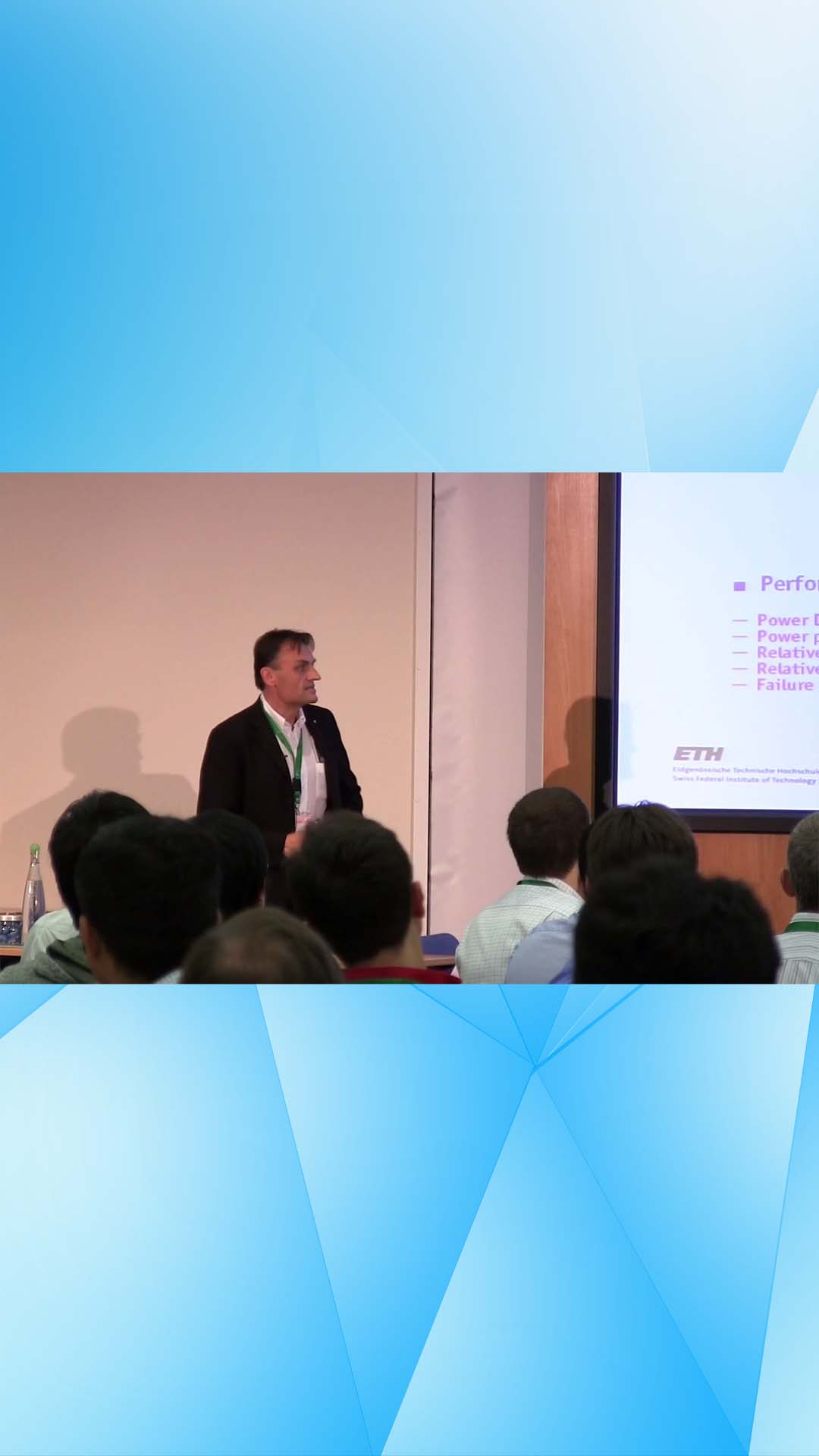
HIP6003 PWM控制器適合作奔騰微處理器的穩(wěn)壓器模塊

△∑A D轉(zhuǎn)換器ADS121X系列的入門指南

82786圖形協(xié)處理器與8051的接口

Design of an Audio Power Syste

Assertion based Design 2nd Edition

斷言基礎(chǔ)設(shè)計(jì)第二版

LANs to WANs:The Complete Mana

局域網(wǎng)到廣域網(wǎng):完整的管理指南

SolidMatrix 0603 Fast Acting S

LED TV: Technology Overview an

Optimizing Power Management fo

Design Compiler Ultra

Building DSP Free VoIP End-Poi

Femtocells Challenges & Opport

New Measurement Requirements f

Ultra Low Current DC Character

The ‘Need for Speed’ in Compon

Debugging Serial Bus Systems w

Agilent GS-8300 Wireless LAN M

10 Good Reasons to Switch to L

Agilent TS-5020 Automotive Ele

標(biāo)準(zhǔn)清晰度和高清晰度數(shù)字視頻測(cè)量指南

Memory Effects in Microwave Co

汽車電源管理解決方案 (Automotive Power M

Zero-Drift Instrumentation Amp

Zero-Drift Instrumentation Amp

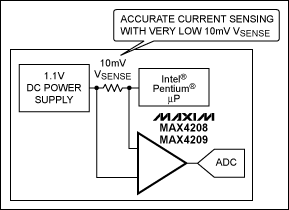
Technology Changes: From a Por

運(yùn)算放大器的輸入-Operational Amplifier

Continuous-Wave Doppler (CWD)

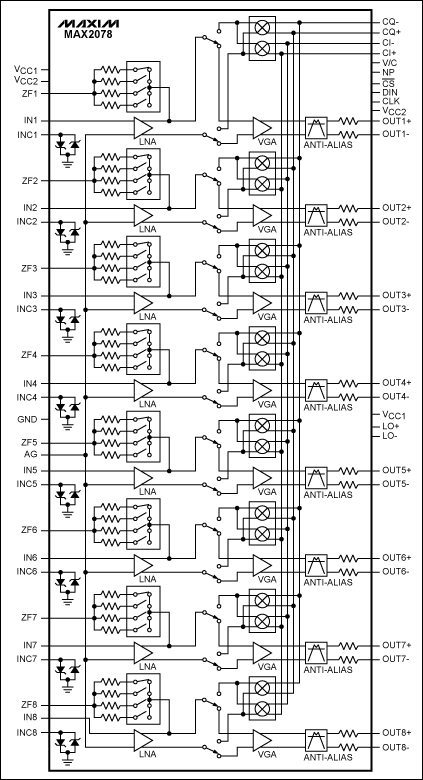
利用零漂移儀表放大器(IA)應(yīng)對(duì)傳感器測(cè)量的設(shè)計(jì)挑戰(zhàn)

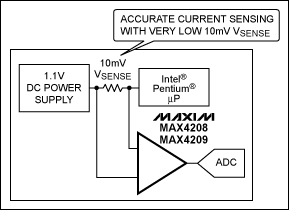
Overcome the Challenges of Int

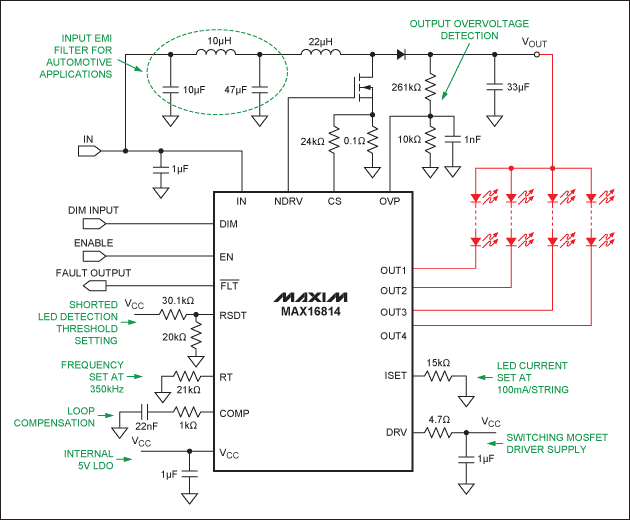
LED TV技術(shù)回顧與DLP分析

便攜多媒體設(shè)備電源管理優(yōu)化

LVDS應(yīng)用手冊(cè)

利用MAX36025克服下一代系統(tǒng)的安全性挑戰(zhàn)

ADS原理圖版圖聯(lián)合仿真Cosimulation_with_layout

Incisive? Enterprise Specman Elite? Testbench Tutorial

先進(jìn)汽車電子設(shè)計(jì)及仿真之EEsof EDA解決方案

The Challenges of Indoor Positioning

RFID開(kāi)發(fā)套件踢啟動(dòng)新設(shè)計(jì)

支持有線網(wǎng)絡(luò)構(gòu)建無(wú)線回程鏈路的挑戰(zhàn)

無(wú)線系統(tǒng)的回路控制的實(shí)現(xiàn)

編碼現(xiàn)代化的個(gè)人方法

CPU,GPU,F(xiàn)PGA:用英特爾線程構(gòu)建塊管理字母表

在當(dāng)今變化的應(yīng)用環(huán)境中的數(shù)據(jù)分析、機(jī)器學(xué)習(xí)和高性能計(jì)算

利用高性能計(jì)算技術(shù)加速大數(shù)據(jù)處理

新興的高性能計(jì)算集群庫(kù)

應(yīng)用說(shuō)明:Ambient Light and Proximity_AN000709_1-00.pdf

2022第五期“心寄源”開(kāi)源法律沙龍成功召開(kāi)

評(píng)論