??
隨著自動測試設備成為電子裝配過程整體的一部分,DFT必須不僅僅包括傳統的硬件使用問題,而且也包括測試設備診斷能力的知識。
為測試著想的設計(DFT, design for test)不是單個人的事情,而是由設計工程部、測試工程部、制造部和采購部的代表所組成的一個小組的工作。設計工程必須規定功能產品及其誤差要求。測試工程必須提供一個以最低的成本、最少的返工達到僅盡可能高的第一次通過合格率(FPY, first-pass yield)的策略。制造部和品質部必須提供生產成本輸入、在過去類似的產品中什么已經做過、什么沒有做過、以及有關為產量著想的設計(DFV, design for volume)提高產量的幫助。采購部必須提供可獲得元件,特別是可靠性的信息。測試部和采購部在購買在板(on-board)測試硬件的元件時,必須一起工作以保證這些元件是可獲得的和易于實施的。通常把測試系統當作收集有關歷史數據的傳感器使用,達到過程的改善,這應該是品質小組的目標。所以這些功能應該在放置/拿掉任何節點選取之前完成。
參數
在制訂測試環境的政策之前,準備和了解是關鍵的。影響測試策略的參數包括:
可訪問性。完全訪問和大的測試焊盤總是為制造設計電路板的目標。通常不能提供完全訪問有四個原因:
板的尺寸。設計更小;問題是測試焊盤的“額外的”占板空間。不幸的是,多數設計工程師認為測試焊的可訪問性是印刷電路板上(PCB)較不重要的事情。當由于不能使用在線測試儀(ICT, in-circuit tester)的簡單診斷,產品必須由設計工程師來調試的時候,情況就會是另一回事。如果不能提供完全訪問,測試選擇是有限的。
功能。在高速設計中損失的性能影響板的部分,但可以逐步縮小在產品可測試性上的影響。
板的尺寸/節點數。這是當物理板得尺寸在任何現有的設備上都不能測試的時候。慶幸的是,這個問題可以在新的測試設備上或者使用外部的測試設施上增加預算來得到解決。當節點數大于現有的ICT,問題更難解決。DFT小組必須了解測試方法,這些方法將允許制造部門使用最少的時間與金錢來輸出好的產品。嵌入式自測、邊界掃描(BS, boundary scan)和功能塊測試可做到這點。診斷必須支持測試下的單元(UUT, unit under test);這個只能通過對使用的測試方法、現有測試設備與能力、和制造環境的故障頻譜的深入了解才做得到。
DFT規則沒有使用、遵守或理解。歷史上,DFT規則由理解制造環境、過程與功能測試要求和元件技術的一個工程師或工程師小組強制執行。在實際環境中,過程是漫長的,要求設計、計算機輔助設計(CAD)與測試之間的相互溝通。這個泛味的重復性工作容易產生人為錯誤,經常由于到達市場的時間(time-to-market)壓力而匆匆而過。現在工業上已經有開始使用自動“可生產性分析儀”,利用DFT規則來評估CAD文件。當合約制造商(CM, contract manufacturer)使用時,可分類出多套規則。規則的連續性和無差錯產品評估是這個方法的優點。
測試設備的可獲得性
DFT小組應該清楚現有的測試策略。隨著OEM轉向依靠CM越來越多,使用的設備廠與廠之間都不同。沒有清楚地理解制造商工藝,可能會采用太多或太少的測試。現存的測試方法包括:
手工或自動視覺測試,使用視覺與比較來確認PCB上的元件貼裝。這個技術有幾種實施方法:
手動視覺是最廣泛使用的在線測試,但由于制造產量增加和板與元件的縮小,這個方法變得不可行。 它的主要優點是低的預先成本和沒有測試夾具,而它的主要缺點是高長期成本、不連續的缺陷發覺、數據收集困難、無電氣測試和視覺上的局限。
自動光學檢查(AOI, automated optical inspection),通常在回流前后使用,是較新的確認制造缺陷的方法。它是非電氣的、無夾具的、在線技術,使用了“學習與比較(learn and compare)”編程來使裝料(ramp-up)時間最小。自動視覺對極性、元件存在與不存在的檢查較好,只要后面的元件與原來所“學”的元件類似即可。它的主要優點是易于跟隨診斷、快速容易程序開發、和無夾具。其主要缺點是對短路識別較差、高失效率和不是電氣測試。
自動X光檢查(AXI, automated X-ray inspection)是現時測試球柵陣列(BGA, ball grid array)焊接質量和被遮擋的錫球的唯一方法。它是早期查找過程缺陷的、非電氣、非接觸的技術,減少了過程工作(WIP, work-in-process)。這個領域的進步包括通過/失效數據和元件級的診斷。現在有兩種主要的AXI方法:兩維(2-D),看完整的板,三維(3-D),在不同角度拍攝多個圖象。其主要優點是唯一的BGA焊接質量和嵌入式元件檢查工具、無夾具成本。其主要缺點是速度慢、高失效率、檢測返工焊點困難、高的每塊板成本、和長的程序開發時間。
制造缺陷分析儀(MDA, manufacturing defect analyzer)是一個用于高產量/低混合環境的好工具,這里測試只用于診斷制造缺陷。當沒有使用殘留降低技術時,測試機之間的可重復性是一個問題。還有,MDA沒有數字驅動器,因此不能功能上測試元件或者編程板上的固件(firmware)。測試時間比視覺測試少,因此MDA能夠趕上生產線的節拍速度。這個方法使用一個針床,因此可以接著診斷輸出。
其主要優點較低的前期成本、較低WIP、低的編程與程序維護成本、高輸出、容易跟隨診斷、和快速完全的短路與開路測試。其主要缺點是不能確認材料清單(BOM, bill of material)是否符合在測單元(UUT, unit under test)、沒有數字式確認、沒有功能測試能力、不能調用固件(firmware)、通常沒有測試覆蓋指示、板與板線與線之間的可重復性、夾具成本、以及使用問題。
ICT將找出制造缺陷以及測試模擬、數字合混合信號的元件,以保證它們符合規格。許多設備具有編程在板(on-board)內存的能力,包括系列號、通過/失效和系統數據(genealogy data)。有些設備使得程序產生較容易,它是通過把工具嵌入到易于使用的圖形用戶接口(GUI, graphical user interfaces),和存儲代碼到一個專門文件來使得可以實現多版本測試和固件(firmware)變換容易的。有些設備具有復雜的儀器裝備,它將確認UUT的功能方面,以及與商業可購買的儀器的接口。現在的測試設備具有嵌入的計算機輔助設計(CAD)接口和一個非多元環境來縮短開發時間。最后,有些測試機提供深入的UUT覆蓋分析,它祥述正在測試或沒有測試的元件。
ICT的主要優點是每個板的測試成本低、數字與功能測試能力、高輸出、良好的診斷、快速和徹底的短路與開路測試、編程固件、缺陷覆蓋報考和易于編程。其主要缺點是,夾具、編程與調試時間、夾具成本、預期開支和使用問題。
飛針測試機(flying-probe tester)在過去幾年已經受到歡迎,由于在機械精度、速度和可靠性方面的進步。另外,現在對于原型(prototype)制造、低產量制造所要求的快速轉換、無夾具測試系統的市場要求,已經使得飛針測試成為所希望的測試選擇。最好的探針方案提供學習的能力(learn capability)以及BOM測試,它在測試過程中自動增加監測。探針的軟件應該提供裝載CAD數據的簡便方法,因為X-Y和BOM數據在編程時必須用到。因為節點可訪問性可能在板的一面不完整,所以測試生成軟件應該自動生成不重復的分割程序。
探針使用無向量(vectorless)技術測試數字、模擬和混合信號元件的連接;這個應該通過使用者可用于UUT兩面的電容板(capacitive plate)來完成。
飛針測試機的主要優點是,它是最快速的到達市場時間(time-to-market)的工具、自動測試生成、無夾具成本、良好的診斷和易于編程。主要缺點是低產量、局限的數字覆蓋、固定資產開支和使用問題。
功能測試(functional test),可以說是最早的自動測試原理,在重要性上已經看到恢復活力。它是特定板或特定單元的,可用各種設備來完成。幾個例子:
最終產品測試(final product test)是最常見的功能測試方法。測試裝配后的最后單元是開支不大的,減少操作的錯誤。可是,診斷是不存在的或者困難,這樣增加成本。只測試最終產品,有機會損壞產品,如果沒有自動測試所提供的軟件或硬件的保護。最終產品的測試也是慢的,通常占用較大的空間。當必須滿足標準時通常不使用該方法,因為它通常不支持參數測量。
最終產品測試的主要優點是最低的初始成本、一次裝配、和產品與品質的保證。其主要缺點包括低診斷分辨、缺乏速度、高長期成本、FPY、由于不發覺的短路引起的板或機器的損壞、返修成本高、以及無參數測試能力。
最新實體模型(hot mock-up)通常放在不同的裝配階段,而不是只在最終測試。在診斷上,它好過最終產品測試,但由于必須建立專門測試單元而成本較高。實體模型可能比最終產品測試更快,如果程序調試只測試一個特定的板。不幸的是,由于缺少保護,如果短路在前面的過程中沒有診斷處理則可能損壞測試床。
其主要優點是低初始成本。主要缺點是空間使用效率低、維護測試設備的成本、由于短路而損壞UUT和無參數測試能力。
軟件控制、可商業購買的儀器(software-controlled, commercial available instrument)通常叫做“堆砌式”測試("rack and stack" test),因為儀器是分別購買,然后連接起來的。同步設備的軟件通常完全用戶化。商業可購買的儀器比較集成方案是不貴的,如果正確完成,允許獨立的UUT有效性。但這個“自制的”系統通常較慢,工程更改與生產現場支持困難,因為這些應用是內部存檔的(under-documented)。
其主要優點是保護UUT的損壞、較快的輸出、要求占地空間小、和獨立的/工業可接受的校驗。主要缺點是費時、支持困難、在遠距離設施上更新與使用。
商業、用戶集成系統(commercial, custom integrated system)在一個測試平臺上耦合軟件與硬件,例如,IEEE、VXI、Compact PCI 或 PXI。文件存檔、軟件支持和標準制造概念使得這些系統易于使用和支持。前期成本比內部建立方案較高,但這個成本是可調節的,因為較高的性能、輸出和可重復性。它也易于生產現場和新產品開發期間的支持。
主要優點是快速輸出、要求較少地面空間、最容易支持和重新設定、最好的可重復性、和提供獨立的工業可接受較驗。主要缺點是高初始成本。
諸如激光系統這樣的非接觸測試方法是PCB測試技術的最新發展。該技術已經在空板(bare-board)區域得到證實,正考慮用于裝配板(populated board)的測試。該技術只用視線(line-of-sight)、非遮蓋訪問(non-masked access)來發現缺陷。每個測試至少10毫秒,速度足夠用于批量生產線。
快速輸出、不要求夾具、和視線/非遮蓋訪問是其主要優點;未經生產試用、高初始成本、高維護和使用問題是其主要缺點。
表一總結了所描述的測試方法。
表一、PCB測試設備
測試設備 要求板的可訪問性 夾具 NRE成本 維護成本 輸出能力
程序成本 夾具成本
MDA 全部1 針床 低 高 中 高
ICT 全部2 針床 中 高 中 高
手工視覺 視線 無 低 無 低 低
AOI 無 無 低 無 低 中
飛針系統 全部1 無 中 無 中 低
X光 無 無 高 無 高 低
最終產品測試 只有產品使用 無 低 無 低 低
實體模型 只有產品使用 無 低/中 中 中/高 低
集成方案 只有產品使用 最小或針床 高 高 高 中/高
堆砌式 只有產品使用 最小或用戶 高 高 極高 低
激光系統 視線,非覆蓋 無 低 低 高 高
需要用于100%測試覆蓋
需要用于100%測試覆蓋,除非使用在機(on-device)硬件。??
測試方法與缺陷覆蓋
重要的是在制訂測試策略之前要理解現有的測試方法和缺陷覆蓋。有許多缺陷覆蓋范圍不同的電氣測試方法。
短路與開路。MDA和ICT善長找出短路 - 它們有針床達到每個電氣節點,可測量網點之間的電阻以確認短路。空板測試機使用對地電容(capacitance-to-ground)技術,如果只限于空板的話,其效率和速度是高的。飛針測試使用了電容技術(capacitor technique)和近似短路技術(proximity shorts technique);前者對多數制造設施的可重復性不夠,缺乏良好的診斷。最好的近似測試使用原始的CAD數據來確認跡線位置,允許編程者選擇測試點之間最大的距離。這提供對測試速度的一定程度的控制;可是,應該推薦的是,功能測試設備具有鉗流(current-clamping)或雙折電纜(fold-back)電源來防止板或測試機的損壞,因為通過元件的低阻抗短路只在短路測試期間可能不能發覺。
無源模擬(passive analog)通過確認UUT已焊接于板上和安裝正確參數的元件來保證可接受的過程品質。這個測試經常在只有很少數量的WIP時進行的,因此在大量問題產品出現之前可以更正問題。不給板供電,用選擇性的無源或有源保護(guard)來使并聯電流通路的電流為零。對UUT與周圍的保護(guard)位置,需要有針床的入口。
視覺系統提供設備級的(device-level)診斷。它們使用一個樣板(golden board),將其與沒有電氣測試的UUT進行比較。MDA提供電氣測試和元件級(component-level)診斷,再一次與已知好的板比較。ICT進行電氣測試,提供設備級診斷,與BOM比較值和誤差。功能測試機按照設計者的規格(通常叫做樣板golden board)進行測試。如果功能測試徹底的話,它保證產品可以發運出去。可是,如果FPY不是特別高,制造者的代價將是不良產品、浪費和昂貴的手工診斷與返修費用。
有源模擬(active analog)。給板供電的ICT、功能測試機和非針測試擅長查找壞的有源模擬元件。ICT和飛針測試,雖然提供引腳級的(pin-level)診斷,但是不能測量一些關鍵的制造商規格(如,帶寬、輸入偏置電流等)。功能測試機測量輸出特性,而不提供引腳級診斷。MDA借助無向量技術的幫助,視覺系統只確認元件的存在。X光提供焊接質量的診斷。
數字與混合信號元件的測試。視覺、X光和MDA只診斷開路和短路。ICT使用各種方法,決定于元件、電路和可訪問性。它只能對連續性使用無向量技術,當有全部的入口時,對連續性和元件確認使用BS。通過手工向量生成來為一個特定元件建立模型可能是費時的,并且可能不夠覆蓋缺陷來判斷效果。對連續性的無向量技術和保證元件運行的有限向量測試相結合的策略可用來使覆蓋范圍最大,而限制開發時間。
功能系統按照設計規格測試電路/模塊,但缺乏將降低引返修費用的腳級/元件級診斷。在大多數情況下,功能測試不提供需要用于過程改進的深層數據。功能與ICT兩者都編程在板(on-board)閃存(flash)、在系統(in-system)可編程和在板內存元件(表二)。
表一、測試設備與所期望的覆蓋范圍
測試設備 短路/開路 焊接 存在/丟失 無源模擬 有源模擬 數字/混合 在板元件編程 功能的
MDA 是1 無 電氣 是 是 可能 無 無
ICT 是1 無 電氣 是 是 是 是 看產品
手工視覺 只可見 無 是 存在 存在 存在 無 無
AOI 只可見 部分2 是 存在 存在 存在 無 無
飛針系統 近似3 無 電氣/有限視覺 是 是 是 可能4 有限
X光 是 是 是 存在 存在 存在 無 無
最終產品測試 無診斷 無 無診斷 無 無診斷 無診斷 是 是
實體模型 無診斷 無 無診斷 無 無診斷 無診斷 是 是
集成方案 部分/完全5 無 可能5 可能5 可能5 可能5 是 是
堆砌式 部分6 無 可能5 可能5 可能5 可能5 是 是
激光系統 是 無 無 無 無 無 無 無
需要用于100%測試覆蓋
示系統而定 - 無BGA覆蓋
相鄰引腳短路。可能對跡線、測試焊盤和通路近似,在測試生成工具上用CAD數據
使用第三方工具。
可能針床入口與手工生成。
通常局限于電源地的覆蓋。??
制造的測試戰略
沒有一個策略將或應該適合所以的制造商。當開發一個測試和工藝改進策略時,必須考慮到無數的變量。
制造缺陷譜的確認應該是有工廠特殊性和產品特殊性。這些數據,如果是相關的和可靠的話,將減少人員與報廢成本,增加顧客信心。缺陷數據應該收集、編輯和在正常的品質小組舉行的會議上討論。該數據也應該用來開發一個測試策略,查找常見的可預防的缺陷。這些數據應該包括工廠的和現場的失效,標記以日期。應該監視新產品的缺陷,而成熟產品應該監測,改善FPY和供應商品質。缺陷數據應該作長期的與短期的內部比較,連同其它場所一起改進總的品質。天氣條件、人員、供應商和生產線改變的數據應該跟蹤,因為這些通常是潛在的品質因素。
兩個重要的品質因素是有關的數據收集和分布性試驗。一個傳感器收集將作為改善品質的數據的能力,和數據管理者把數據傳達給正確的小組部門的能力,影響著現在與將來的產品。正確數據的定義決定于設施與產品。測試機起傳感器的作用,監測過程。一個有效的分布測試策略找出盡可能靠近根源的過程問題,減少壞品的生產數量。
- 現代PC(5028)
相關推薦
詳解PCB分層策略及PCB多層板的設計原則

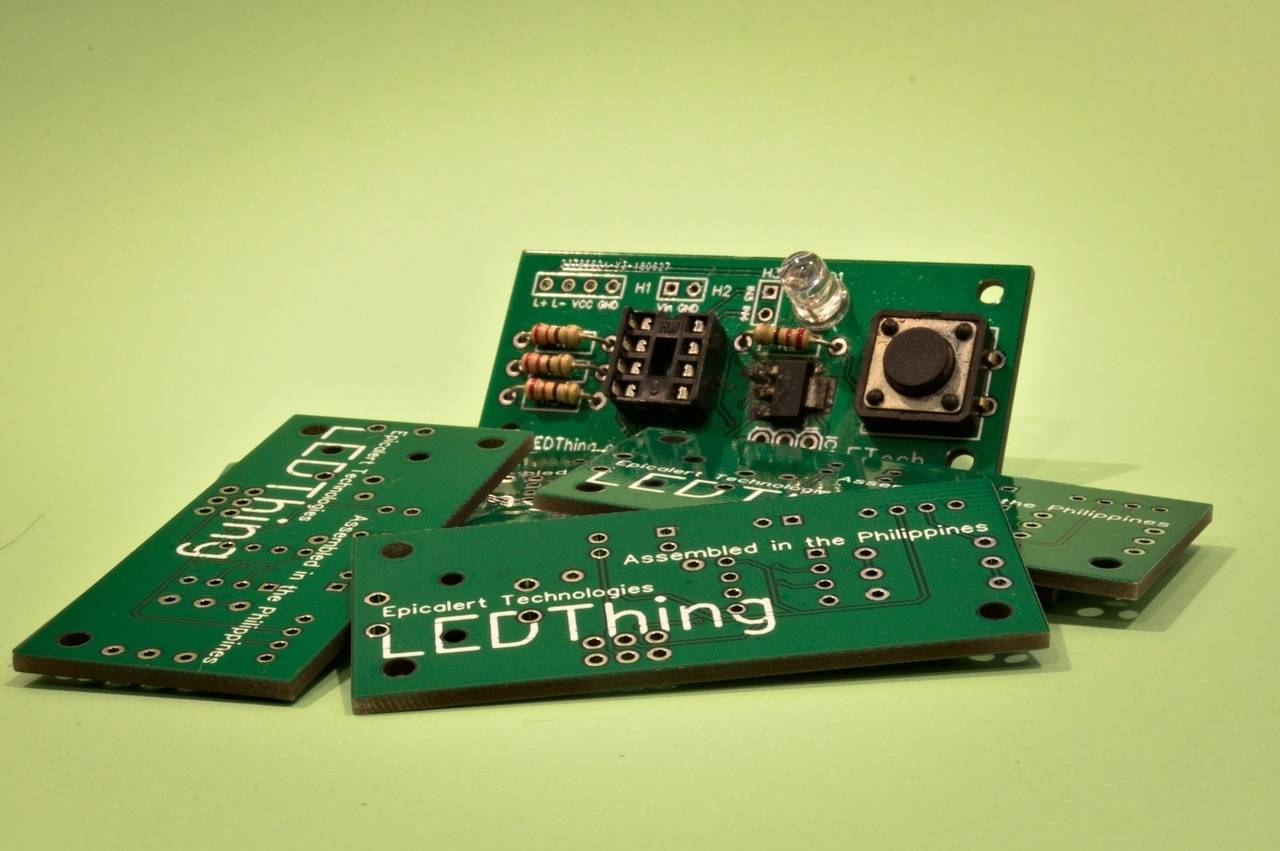
PCB Layout三個方面的走線策略
PCB Layout的走線策略怎么優化?
PCB測試機詢價
現代PCB測試的策略
TD-HSDPA準入策略的外場測試的目的是什么?有哪些步驟?
UCC28056架構和突發模式怎么滿足現代電源要求?
[原創]PCB Layout中的走線策略
【FPGA】 UART測試平臺的實現代碼----測試流程的控制
【轉】高速PCB抄板與PCB設計策略
什么是PCB的測試點?
在PCB設計中,PCB層堆疊在控制EMI輻射中的作用及其設計策略
如何設計PCB測試機硬件電路?
求教Altium PCB修改策略
淺析cache控制器的分配策略與替換策略
高性能永磁交流伺服電機系統控制策略資料分享
高速PCB抄板與PCB設計策略
pcb應力測試全方位PCB檢測分析儀TSK-64-16C
PCB走線策略

PCB飛針測試詳細介紹 什么是飛針測試?

無線MIMO測試開發策略

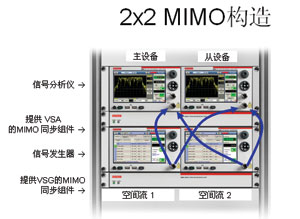
基于FPGA的PCB測試機硬件電路設計研究

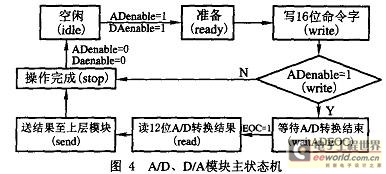
PCB通用測試技術分析

PCB阻抗測試,是怎么測出來的

IA服務器測試技術的策略與方法

基于差分信號的PCB布線優點和策略簡析

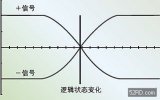
高密度印刷線路板的實施功能測試應考慮的因素及應對方法策略介紹

PCB電路板可測試性設計的三個策略介紹

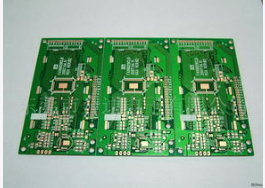
PCB飛針測試程式的制作的步驟方法解析

PCB互連設計測試技術解析

PCB設計時Layout有什么走線策略

PCB產品設計的策略分享

pcb測試方法

模擬和數字布線策略之間的區別

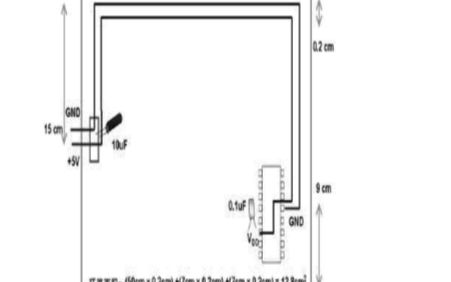
PCB設計的功能測試

現代混合信號PCB設計的電路布線方法解析

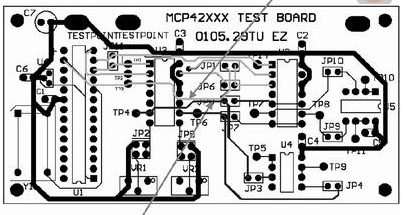
設計可靠性測試和降低風險策略的實施

PCB測試方法與作用

PCB測試:以在線和功能測試為重點

PCB測試之電磁元件

電容測試法在PCB電性能測試中的應用研究

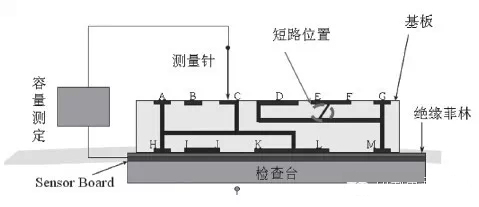
嵌入式軟件接口怎么測試,嵌入式系統接口測試策略.doc

了解PCB常用的13種測試方法

現代測試系統具有豐富的數據管理策略

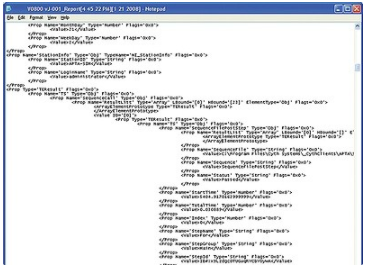
解決Vivado implementation擁塞的策略方法

PCB板應力應該如何測試

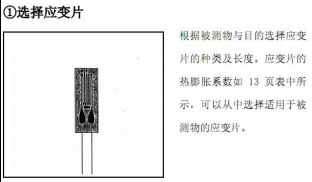
盤點16種常見的PCB可靠性測試,您的板經得起測試嗎?

PCB設計:使輻射最小化的布線策略

PCB的兩種電性測試方法

PCB測試架和PCBA測試架的原理與用途

為什么要在PCB中使用測試點?

7種常用PCB測試技術總結

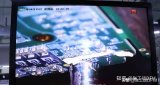
常見的PCB測試方法

PCB板應力是如何測試的

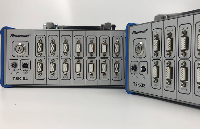
【PCB測試】PCB制造常用的13種測試方法

PCB與PCBA測試架的區別

高功率PCB中EMC的處理與優化策略

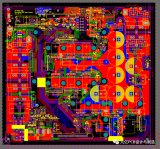
評論