pcb內層短路的原因
一、原材料對內層短路影響:
多層PCB材料尺寸的穩定性是影響內層定位精度的主要因素。基材與銅箔的熱膨脹系數對多層PCB的內層影響也必須有所考慮。從所采用的基材的物理特性分析,層壓板都含有聚合物,它在一定的溫度下主要結構會發生變化,通稱為玻璃化轉變溫度(TG值)。玻璃化轉變溫度是大從數聚合物的特有性能,僅次于熱膨脹系數,它是層壓板最重要的特性。在通常使用的兩種材料比較分析,環氧玻璃布層壓板與聚酰亞胺的玻璃化轉變溫度分別為Tg120℃和230℃,在150℃以下的情況,環氧玻璃布層壓板的自然熱膨脹大約0.01in/in,而聚酰亞胺自然熱膨脹只有0.001in/in。
從有關技術資料獲知,層壓板在X、Y方向熱膨脹系數每增高1℃為12-16ppm/℃之間,而Z方向熱膨脹系數是100-200ppm/℃,它的數值比X、Y方向增大一個數量級。但在測試過程中發現當溫度超過100℃時層壓板及孔體之間的Z軸方向膨脹是不一致的,并且差異變大。電鍍通孔要比周圍的層壓板的自然膨脹率要低。由于層壓板熱膨脹比孔體快,這就意味著通孔體沿層壓板形變方向被拉伸。這個應力條件在通孔體中產生了張力的應力,當溫度升高時,該張力應力將繼續增高,當應力超過通孔鍍層的斷裂強度時,鍍層將會斷裂。同時層壓板較高的熱膨脹率,使內層導線及焊盤上的應力明顯增加,致使導線與焊盤開裂,造成多層PCB內層短路。所以,在制造適用BGA等高密度封裝結構對PCB的原材料的技術要求,要特別進行認真的分析,選擇基材與銅箔的熱膨脹系數基本要達到相匹配。
二、定位系統的方法精度對內層短路的影響
在底片生成、電路圖形制作、疊層、層壓和鉆孔過程,都必須進行定位,至于采用何種形式的定位方法,需要進行認真的研究和分析。這些需要定位的半成品都會因為選擇的定位精度的差異,帶來一系列的技術問題,稍有不慎就會導致多層PCB內層產生短路現象。究竟選擇何種定位方法,應由所選用的定位的精度適用性和有效性而定。
三、內層蝕刻質量對內層短路的影響
內層蝕刻過程易產生末蝕刻掉的殘銅點,這些殘銅有時極小,如果不采用光學測試儀進行直觀的檢測,而用肉眼視覺很難發現,就會帶到層壓工序,將殘銅壓制到多層PCB的內部,由于內層密度很高,最容易使殘留銅搭接到兩導線之間而造成多層PCB內層短路。
四、層壓工藝參數對內層短路的影響
內層板在層壓時必須采用定位銷來定位,如果裝板時所使用的壓力不均勻,內層板的定位孔就會產生變形、壓制所采取的壓力過大產生的剪應力和殘余應力也很大,層縮變形等等原因,都會造成多層PCB的內層產生短路而報廢。
五、鉆孔質量對內層短路的影響
1、孔位誤差分析
為了獲得高質量、高可靠性的電氣連接,鉆孔后焊盤與導線的連接處最小要保持50μm。要保持這么小的寬度,鉆孔的位置精度要很高,產生的誤差要小于或等于工藝所提出的尺寸公差技術要求。但鉆小孔的孔位誤差主要由鉆床的精度、鉆頭的幾何形狀、蓋、墊板的特性和工藝參數而定。從實際生產過程所積累的經驗分析是由四個方面造成的:相對孔的真實位置鉆床的振動造成的振幅、主軸的偏移、鉆頭進入基板點所產生的滑移和鉆頭進入基板后由于受玻璃纖維的阻力和鉆屑引起的彎曲變形。這些因素都會造成內層孔位偏移而產生短路的可能性。
2、根據上述所產生的孔位偏差,為解決和排除產生誤差超標的可能性,建議采用分步鉆孔的工藝方法,可以大減少鉆屑排除的效果和鉆頭溫升。因此,需要改變鉆頭的幾何形狀(橫截面積、鉆芯厚度、錐度、排屑槽角、排屑槽和長度與刃帶比率等)來增加鉆頭的剛度,孔位精度就會大改善。同時還要正確的選擇蓋墊板和鉆孔的工藝參數,才能確保鉆孔的孔位精度在工藝規定的范圍以內。除了上述保證條件外,外因也是必須注視的焦點。如果內層定位不準,在鉆孔時通孔偏位,也同樣導致內層斷路或短路。
-
PCB內層
+關注
關注
0文章
5瀏覽量
6239
發布評論請先 登錄
相關推薦
輸入端子電源短路的原因
TAS5766M DVDD對地短路然后芯片發熱,是什么原因引起的呢?
基于BQ76952的電池包短路保護DSG FET損壞原因及優化方法
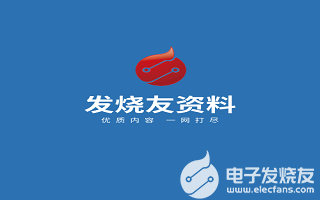
什么原因會引起LM358芯片內部電路短路?
TLV3801的2腳與3腳短路的原因?
電樞繞組線圈怎么短路的
交流信號電容短路的原因有哪些
貼片電容開裂和短路的原因
Micro SD卡短路原因分析及預防措施
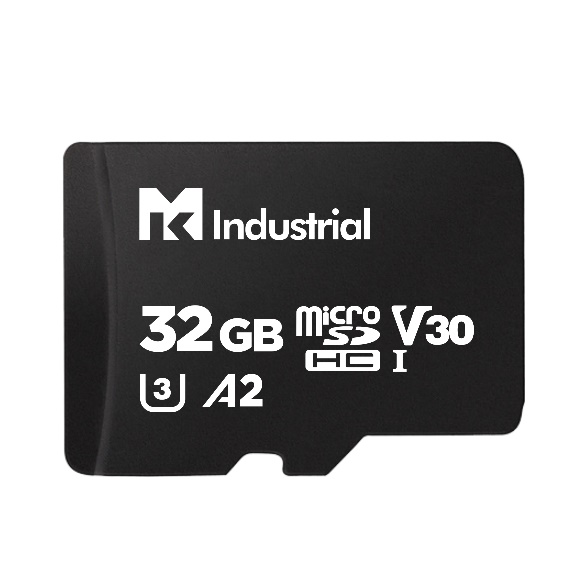
評論