由于美國將從2021和2024年起將頒布溫室效應氣體排放法規并建議實施歐Ⅶ廢氣排放標準,加重了商用車柴油機制造商降低CO2排放的壓力,為此必須提高發動機效率,同時降低機械系統摩擦。而用于發動機低速化的新的變速器設計又使任務變得更加繁雜,而由活塞、活塞環和氣缸套組成的活塞系統對于提升耐磨性和降低摩擦起著重要的作用。
1 初始狀況
為實現降低摩擦的目標,通常會以活塞系統(PCS)為研究對象,其產生了源于基礎發動機的大部分機械損失,即使該系統的摩擦損失已相對較低,但是仍能進一步優化摩擦。采用類金剛石碳涂層(DLC)活塞環與光滑氣缸工作表面相匹配能降低活塞環-氣缸副的摩擦,而具有最佳裙部接觸和低摩擦裙部涂層的緊湊型活塞則可減小活塞的摩擦,此類活塞系統具有最多將摩擦降低達37%的潛力。除了數字優化方式之外,有一種創新方法是按照浮動缸套原理測量單缸柴油機的摩擦力,測試機型以30 kW/L升功率的13 L發動機為基礎,并在整機上進行曲軸箱竄氣量和機油耗的測量。
2 活塞設計
鑒于降低商用車發動機的摩擦功率,KS Kolbenschmidt公司提供了定制活塞的結構,以滿足不同用戶的需求。在現有情況下使用通過壓縮高度以降低摩擦的Weldteks式活塞設計,通過較小的高度以減輕活塞質量,對側壓力產生較為有利的影響,并與加長型連桿相互配合以降低發動機摩擦功率,而通過摩擦功率優化的較小活塞環組就能將活塞環區設計得較為緊湊(表1)。
表1 用于2021車型年度LF PCS的活塞設計
采用數字模擬優化活塞設計就能使活塞在發動機運行中實現協調變形,與傳統設計相比還能降低摩擦,而且通過數字模擬可將活塞裙部廓線導致的接觸壓力和摩擦優化到最低程度。現代數字模擬優化工具能確保活塞設計所必需的疲勞強度而無需多次重復優化設計。
與量產活塞相比,Weldteks活塞能使壓縮高度縮短17 mm,從而使質量減輕達23%,而且還因發動機氣缸體高度也可相應降低17 mm從而進一步擴大了減輕質量的效果。
3 活塞摩擦模擬
現代商用車發動機實現低速化的趨勢相應提高了采用有限元(FE)模擬設計低摩擦活塞的要求。為了即使在低轉速時也能確保活塞裙部完全建立起流體動力學壓力,在活塞設計上需仔細地調整活塞的細節輪廓,并結合機械負荷和熱負荷所引起的變形,加工的輪廓就決定了活塞與氣缸之間接觸區域的機油油膜分布。與多體系統算法相結合,彈性流體力學接觸模型考慮了活塞在氣缸中的運動以及隨曲軸轉角變化的由氣體壓力和慣性力所產生的負荷。作為對上述效果的補充,摩擦損失計算包括了轉換到混合摩擦狀態時表面粗糙度的影響。
1 025 r/min的轉速和100 kW的功率對于道路行駛工況下燃油耗的降低具有重要意義,采用圖1中所示的低摩擦(LF)活塞顯示出了明顯的優勢。良好的流體動力學壓力的建立導致在360°CA和540°CA之間工作行程中的機油油膜厚度得以增加。在裙部表面被機油潤濕的同時,LF活塞的累積平均摩擦壓力從量產活塞的3.1 kPa降至2.0 kPa,即降低了35%。
在額定功率時采用LF活塞方案的總體優勢是其具有相同的數量級,但是在側壓力較高的工作行程中其主要是由混合摩擦損失減少引起的。不同運行條件下的模擬節油效果通常在0.11%~0.20%范圍內,對此與OEM制造商在商用車行駛循環中的測量值0.15%具有良好的一致性。
圖1 道路行駛時量產和LF活塞的機油膜分布和平均摩擦壓力
4 活塞環設計
針對降低工作表面摩擦的目標,利用降低活塞環高度、減小切向力和應用DLC涂層等方法,而設計出了具有較低摩擦的LF活塞環組(表2)。與量產活塞環相比,LF活塞環組的第一和第二道活塞環具有較小的環高,分別為2.5mm和 2.0 mm,以此相應減小了活塞環內徑上的氣體壓力和對氣缸的接觸表面。刮油環的高度并未得以改變,當然其圓錐形環岸明顯減小了有效接觸表面,因此對機油進行剪切的有效表面將變得較小,并且降低了流體動力學摩擦力。
表2 活塞環設計
總摩擦較小的活塞環組使切向力降低了33%,從而降低了摩擦。正如在活塞系統試驗結果一節中所言,在整機上成功地防止了因活塞環張力過小而使機油耗增加的風險。總體而言,橫截面較小的活塞環對其形狀貼合能力產生了較為有利的影響。
第一道活塞環和刮油環的工作表面均涂有DLC涂層。由于DLC涂層的摩擦系數較低,降低了混合摩擦而產生的摩擦力,同時因DLC涂層具有較高的耐磨性,使活塞環能比量產的鉻基方案更長地保持最初的工作表面廓線,這類輪廓運行時間更為持久,即使經過長時間的運行仍能保持低摩擦的優越性。因此,LF活塞環組滿足了現代商用車柴油機對可靠性和耐磨性的要求。
5 氣缸工作表面設計
由活塞環形成的光滑摩擦副與有利于降低摩擦的涂層和用于活塞環-氣缸套低摩擦的氣缸工作表面相配對,目前已應用于汽油機,而對于其在商用車柴油機領域的應用而言,還必須具有較高的抗拉缸性能和耐磨性,而且耐腐蝕性也會帶來相關優勢。KSKolbenschmidt公司的鐵基金屬絲熱噴鍍能滿足這些要求:最佳的均勻分布的氣孔具有足夠的含油容積并可減少磨損,而硬質組織和合金元素則可滿足耐磨性和抗腐蝕性的要求。
氣缸套鏡面珩磨工作表面可減小摩擦系數,其優先選擇的配對工作對象是DLC涂層活塞環,其不含合金成分,與氣缸工作表面上的旋轉噴涂單金屬絲涂層(RSW)進行匹配工作。圖2示出了RSW氣缸套工作表面巴氏干涉儀的照片,這種涂層與表2中的LF活塞環組配對成功地經受了機油耗、疲勞強度和降低摩擦等方面的考驗。
圖2 氣缸工作表面:RSW涂層和鏡面珩磨
6 活塞環摩擦模擬
必須預先為DLC涂層活塞環和氣缸鏡面珩磨RSW涂層配對的新摩擦副擬定模擬邊界條件。為測定摩擦系數在活塞環-氣缸摩擦儀上測試Stribeck曲線并予以評估,由表面巴氏干涉儀分析模擬微觀流體動力學摩擦系數,應用一種全新開發的Kori3D方法進行摩擦模擬。
圖3示出了LF活塞環組降低摩擦的模擬結果與量產活塞環組的比較。在具有代表性的道路行駛工況點和當前變速器設計的情況下LF活塞環組摩擦可降低達21.8%,而在未來用于低速化的變速器速比情況下則可降低26.8%。
在額定功率情況下活塞環組摩擦可分別降低28.6%或37.6%。在所考察的運行條件下降低摩擦主要歸因于LF活塞環組的混合摩擦較小,其影響因素是LF活塞環組的切向力較小以及DLC涂層與RSW涂層摩擦副的摩擦系數較小,而且RSW氣缸工作表面較小的粗糙度明顯減少了相對運動時的固體接觸。
圖3 額定功率和道路行駛時的活塞環摩擦
按照發展趨勢,LF活塞環組與RSW氣缸工作表面之間的流體動力學摩擦將會有所增加,因為氣缸光滑的RSW工作表面較小的粗糙度使得活塞環與氣缸之間潤滑油膜較薄,當然LF活塞環組的潤濕接觸表面減小補償了流體動力學摩擦方面的缺陷。
7 活塞系統的試驗結果
在一臺2015車型年度商用車柴油機上進行由Weldteks活塞、DLC涂層LF活塞環和RSW氣缸套組成的活塞系統(LF PCS)的性能試驗。為了補償活塞壓縮高度降低而使用了加長連桿。圖4示出了LF PCS和量產型的機油耗和曲軸箱竄氣量及其共同的限值線。兩種活塞結構型式的機油耗都相對較好,而LF PCS的曲軸箱竄氣量卻比量產型的具有明顯改善。
圖4 LF PCS機油耗和曲軸箱竄氣量在
量產條件下與量產方案的比較
KS Kolbenschmidt 公司采用一臺按浮動氣缸套原理工作的單缸柴油機來測量活塞系統的摩擦力。這種供測量用的發動機氣缸由軸向方向上的4個力接收器支撐著,按照Furuhama方法(譯注:以日本發明者名字命名的一種測量摩擦損失的方法)氣缸壓力的軸向分力在氣缸上端由補償牽引來平衡,而氣缸工作表面通過改變使用的合金、涂層和表面輪廓而予以調整。
圖5示出了在1 000 r/min和9 MPa氣缸峰值壓力時在浮動氣缸套中測得的量產和LF PCS活塞系統在整個工作循環中的摩擦力曲線,從中可以清楚地看出LF PCS活塞系統在工作循環所有曲軸轉角相位時的優勢,特別表現在壓縮和膨脹階段,其中減小的接觸表面與較低的摩擦系數相結合產生了較小的摩擦力,從而導致了較低的平均摩擦壓力。
圖5 在1 000 r/min和9 MPa氣缸峰值壓力時
在浮動氣缸套中測量的摩擦力
8 活塞系統中的摩擦
圖6以平均摩擦壓力示出了在額定功率和道路行駛運行條件下的活塞系統摩擦,左側兩個柱狀圖標表示在當前變速器速比運行條件下的摩擦損失,而右側兩個柱狀圖標則分別表示為2021年美國溫室氣體法規設計的未來變速器速比下低速化機型的摩擦損失,藍色代表活塞摩擦,紅色代表活塞環-氣缸副摩擦。因為量產型活塞已實現摩擦優化,為了實現進一步改善,特別是針對低速化作為可能行之有效的措施僅關注優化整個活塞系統。減小活塞裙部接觸表面并與非常光滑的氣缸工作表面相匹配,兩對摩擦副的摩擦份額至少能降低22%。
與量產活塞相比,根據運行條件的不同LF PCS活塞系統明顯降低了平均摩擦壓力,在當前的變速器設計和道路行駛條件下可降低25%,而在未來的變速器設計和額定功率條件下則可降低36%。在道路行駛條件下摩擦至少降低25%。若在損失功率平衡中考慮到低速化特征的話,則在道路行駛中LF PCS活塞系統僅損失0.148 kW,而量產活塞系統在當前的變速器速比情況下卻要損失0.234 kW,這相當于具有37%的優勢,此時LF活塞僅呈現微不足道的混合摩擦損失。
圖6 活塞系統的平均摩擦壓力和
混合摩擦份額
為了在較低發動機轉速下(在未來變速器速比下低速化)達到相同的輸出功率,必須具有較高的氣缸峰值壓力,以此加大了混合摩擦份額,正如圖6下方圓形蛋糕圖例中所示的那樣,LF PCS活塞系統有效補償了量產活塞系統在低速化時混合摩擦的增加。
圖7示出了預測的LF PCS活塞系統相對于量產活塞系統所降低的CO2排放:額定功率時為0.27%和0.40%,道路行駛時為0.33%和0.38%。
圖7 LFPCS活塞系統降低的CO2排放
9 結論
通過改善活塞系統的摩擦狀況以降低燃油耗是一種挑戰,特別是在考慮未來發動機設計低速化的情況下,其成功的關鍵是活塞系統優化方法以及應用模擬方法以采取最有效的降低摩擦措施優化和組合系統。
德國KS Kolbenschmidt公司與日本Ricken公司采用摩擦優化的活塞和活塞環設計,并在活塞裙部、活塞環工作表面(RickenDLC)和氣缸工作表面(鏡面珩磨RSW)上應用最新的降低摩擦涂層,達到了使摩擦降低達37%的效果,通過用于商用車的單缸測試發動機證實了發動機運行時可充分降低摩擦的實際效果,整機試驗也證實了其在機油耗和曲軸箱竄氣量方面的良好效果。
-
柴油機
+關注
關注
1文章
171瀏覽量
26256 -
摩擦
+關注
關注
0文章
13瀏覽量
7655
發布評論請先 登錄
相關推薦
農用柴油機原理使用及維護 pdf電子書
車用增壓柴油機VNT和EGR系統匹配試驗研究
柴油機電控燃油噴射系統開發與研究
6105柴油機連桿及連桿螺栓遷都分析
柴油機預混合燃燒機理的研究
[原創]2011中東商用車展/迪拜商用車展/商用車零配件展/商用車
[原創]2011中東商用車展/迪拜商用車展/商用車零配件展/商用車
柴油發電機組常見的錯誤操作(一)
柴油機使用中應注意的問題
聞香識女?聽音辯故?10種聽聲音知道柴油機故障的方法
農用柴油機原理使用及維護
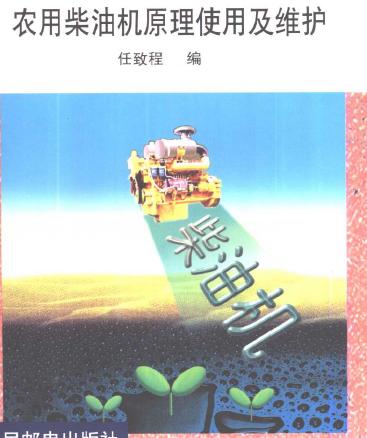
基于KPCA-SVM的柴油機狀態識別方法
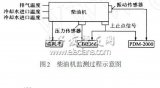
柴油機轉速信號動態模擬電路分析與設計
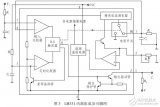
評論