摘要:為了實現較好的動力和環保性能,開發了1種小型化1.5 L渦輪增壓發動機。該發動機旨在替代1.8~2.4 L的自然吸氣發動機。在小型化渦輪增壓發動機中,混合氣均勻性對抑制爆燃和減排十分重要。特別是在發動機高負荷運行時,創造快速燃燒和均勻混合氣是關鍵的技術。采用了長行程直噴發動機作為滿足這些要求的基本機型,它具有顯著的快速燃燒能力和較高的熱效率。將長行程與高滾流氣道和支持滾流的淺盆形活塞相結合,增強了混合氣在氣缸內的流動。建立的燃燒系統包含1個能減少爆燃的充鈉排氣門和1個有利于形成均勻混合氣和減少燃油濕壁的多孔(6孔)噴射器。依靠快速燃燒,能夠實現很高的缸內壓力,因而能提高平均指示有效壓力,即使在轉速1 500 r/min全負荷下推遲點火正時的情況下也是如此。雙氣門正時控制(VTC)有可能為不同的發動機轉速和負荷設定最佳的進排氣門重疊角和氣門正時。VTC與上述燃燒系統相結合實現了220 g/(kW·h)-1的最低比油耗和38%的最大熱效率。還介紹了發動機的動力輸出性能和燃油經濟性,以及為達到低排放、減少振動和噪聲、實現輕量化和整車性能采用的技術。
本田汽車公司的目標是要開發一些具備駕駛樂趣,同時又能滿足全球越來越嚴的環保法規的發動機。為此,本田汽車公司開發了1種熱效率和輸出性能較好的1.5 L小型化渦輪增壓發動機。該發動機旨擬用來替代1.8~2.4 L的自然吸氣發動機。本文將特別探討在本田汽車(Civic)緊湊型轎車上用這種發動機取代1.8 L自然吸氣發動機的好處。設定的4個發展目標如下:
(1)實現一種由進氣道產生缸內高速滾流的新型燃燒系統;
(2)能在發動機低轉速范圍產生充裕扭矩的功率特性;
(3)一流的燃油經濟性和排放性能;
(4)通過使用輕量化、高剛性的發動機框架結構達到卓越的振動和噪聲水平。
本文將介紹發動機的技術規格、燃燒概念、輸出特性、燃油經濟性、降低排放、降低振動-噪聲、輕量化和車輛性能等方面的情況。
1發動機技術規格
本田汽車選擇現有的1種1.5 L自然吸氣發動機作為基本機型,以實現比以前幾種1.8 L自然吸氣發動機更好的驅動性和燃油經濟性。該項開發的出發點是采用1.5 L自然吸氣發動機作為參考機型來實現高熱效率。長行程結構可提供相當快速的進氣流,因而能增加燃燒室內的紊流。通過這種方式,能快速燃燒和抑制爆燃。
尤其是在渦輪增壓發動機中,該爆燃對策在高增壓壓力條件下能帶來更高的熱效率。因此,這就能通過長行程(行程/缸徑比為1.22)和小缸徑(直徑73 mm)的結構配用渦輪增壓器來得以實現,這正是上述燃燒的優點。圖1所示為這種小型化渦輪增壓發動機在熱效率和平均有效壓力(BMEP)方面的優越性能。發動機的技術規格列于如表1,圖2為發動機的外觀視圖。
圖1 1.5 L小型化渦輪增壓發動機的性能位置
(圖中所示3種發動機的相應參數列于表1中)
圖2 1.5 L小型化發動機的外觀視圖
采用雙VTC能夠為各種不同的發動機負荷和轉速提供最佳的進/排氣門重疊角和氣門正時。通過調整內部EGR量和充氣效率,能使發動機達到目標燃油經濟性和輸出功率。并采用汽油直噴射器來提高熱效率和形成均勻的混合氣。發動機設計成可使用普通汽油運行,在壓縮比為10.6的情況下燃油耗與動力性達到最佳平衡。
為了激活排氣催化劑使之較早起燃,在排氣門到催化器的所有通路上都采用了低熱質量結構(圖3)。該結構包括1個直接安裝在氣缸蓋整體式排氣歧管上的單流道渦輪增壓器,與1個在其下游的雙床催化器直接緊耦合。發動機向后傾斜7°,而這些排氣系統組件均布置在發動機的前端。
表1 發動機主要技術規格
圖3 在從排氣門到催化器的所有通路上
采用的低熱質量結構
2燃燒概念
建立的燃燒系統由高滾流氣道(在小型化渦輪增壓發動機所需的高負荷下產生快速燃燒和均勻的混合氣)、淺盆形活塞(支持滾流)、充鈉排氣門(減少爆燃),和多孔噴射器(減少氣缸燃油濕壁)組合而成(圖4)。
圖4 燃燒系統的組件
圖5所示為渦流比與流量系數之間的關系。與其他進氣道相比,新型進氣道的定位是高渦流比。圖6所示為渦輪增壓發動機與基本機型1.5 L自然吸氣發動機進氣道和活塞形狀的差異。與自然吸氣發動機相比,渦輪增壓發動機進氣道的傾斜角度更大。其空氣流大多沿排氣門下面的單坡斜面流動,對面的氣流被限制進入氣缸。這一效應是由設置在進氣道下側周圍與氣門座腔相連的被稱為突變斜坡刃口(圖6細節A)造成的。如此可以限制逆向滾流(即限制空氣反向回流)。
圖5 在渦流比與流量系數的曲線圖上
新型滾流氣道所處的位置
新開發的渦輪增壓發動機還采用淺盆形活塞。這種淺盆形頂部形狀由平緩的曲面和上坡面組成(圖6細節B)。曲面是要在進氣行程期間使滾流流動方向變換成向下,后面的上坡形狀用于引導氣流向上流動。通過這種方式,活塞頂部的形狀就能在壓縮行程期間產生滾流。圖7所示為由計算流體動力學(CFD)里卡多VECTIS 3.12方法獲得的轉速1 500 r/min全負荷時的缸內氣流形態。圖8比較了這兩種發動機的渦流比和紊流動能。
觀察到在活塞方向有一股強氣流,它在進氣過程的前半部分(曲軸轉角100°CA)形成。活塞頂面的淺盆能使這股氣流反向流動,產生滾動渦流。在壓縮過程中(曲軸轉角270°CA)觀察到的滾動的渦旋,在上止點前-60~0°CA BTDC單坡被擠入屋脊斜面,并轉化成紊流動能,從而促進火焰傳播,接近壓縮上止點時的紊流動能大約是自然吸氣發動機的2倍。
圖6 進氣道和活塞形狀的比較
圖7 缸內流動形態(轉速1 500 r/min倒拖運行)
選擇的直接多孔噴射器能給噴霧形態提供了很大自由度。選用的1種噴油器與高速滾流結合,能夠降低缸套濕壁(會影響機油稀釋)和活塞濕壁(導致碳煙)。表2所示為考慮到的幾種典型的噴霧形態。它會根據進氣行程中的滾流主流方向提出3個噴霧方向:向上(朝缸套),向下(朝活塞)和向中間。這些以混合均勻性和燃油濕壁量為指標,利用CFD計算來選擇噴霧方向。這臺發動機選擇了C型噴霧形態。
表2提出了3種燃油噴霧形態。表中的燃油噴霧布局圖表示,x軸值是為橫向角位移量,y軸值為縱向角位移量。
圖8 渦流比和紊流動能
(轉速1 500 r/min倒拖運行)
表2 3種燃油噴霧形態
注:++,好;+,中等;-,差
3輸出性能
新型1.5 L渦輪增壓發動機最大輸出功率為130 kW,比1.8 L自然吸氣發動機的最大功率增加了21%,扭矩增加了26%,且發動機最大扭距轉速下降了2 600 r/min。轉速2 000 r/min時的扭矩與2.4 L發動機的大致相同。這有助于確保車輛在城市地區方便操縱,以足夠的功率實現舒適的高速加速(圖9)。這些結果可能是因為采用了上述燃燒的規格、雙VTC,以及低慣性和高響應度的緊湊型渦輪增壓器而獲得的。
渦輪增壓器的1個獨特之處是進氣壓力大于或等于其排氣壓力。利用這一特性進行的掃氣過程是增加低速扭矩的1種有效手段。在相對較高的進氣壓力條件下,采用較寬的進排氣門疊開角,能使殘余氣體從缸內清除到排氣系統。這可使氣缸充入更多的新鮮充量并減少爆燃。同時,掃氣流能提高渦輪的轉速(圖10)。
圖9 性能曲線的比較
圖10 轉速1 500 r/min全負荷時
1.5 L渦輪增壓發動機的掃氣效果
其結果是,在1 500 r/min時,開發的發動機的扭矩大約要比1.8 L自然吸氣發動機的高30%。此外,針對這種掃氣將空燃比設定為化學計量比,可以通過催化器來凈化廢氣。圖11比較了1 500 r/min全負荷時1.8 L自然吸氣基本型發動機和1.5 L渦輪增壓發動機的氣缸壓力曲線。增壓壓力補償了由于小型化導致的平均指示有效壓力(IMEP)的損耗,這意味著即使在行程容積很小的情況下,也能產生高氣缸壓力。由圖12顯示,即使在因增壓壓力上升而推遲點火正時的情況下,快速燃燒也能達到很高的熱效率。
圖11 1.5 L渦輪增壓發動機和1.8 L
自然吸氣發動機的p-V圖比較
(1 500 r/min全負荷)
圖12 1.5 L渦輪增壓發動機和
1.8 L自然吸氣發動機放熱率的比較
(1 500 r/min全負荷)
在圖13中,發動機中、高轉速從2區到4區氣門疊開角逐漸減小。這就能抑制因排氣壓力上升而導致的殘余氣體增加。在加速期間,將電動放氣閥控制成立即完全關閉,因而有可能快速增加增壓壓力。
圖13 雙VTC的控制策略
4燃油經濟性
圖14為1.8 L自然吸氣發動機和1.5 L小型化發動機有效比油耗(BSFC)曲線圖譜的比較。圖中顯示,BSFC 240 g/(kW·h)的區域擴展到了包括較高和較低的扭矩以及較高和較低的發動機轉速的范圍。新開發的發動機的最小比油耗為220 g/(kW·h),最高熱效率為38%。
圖14 1.5 L渦輪增壓發動機與
1.8 L自然吸氣發動機BSFC圖譜的比較
因此,此項開發已經達到了在1 500 r/min和70 N·m(重點運轉工況)下比油耗減少10%的目標。此外,由于小型化發動機是要取代排量較高的發動機,所以它不僅需要在日常的負荷下,而且還要在高負荷下運行,并提供良好的燃油經濟性。與1.8 L自然吸氣發動機相比,新開發的發動機在轉速1 500 r/min并接近全負荷140 N·m的情況下,燃油經濟性降低了16%。圖15所示為燃油耗減少的細分情況。
圖15 有效比油耗改善的因素
在自然吸氣發動機中,通常會采用較濃的空燃比來增加全負荷的輸出功率。然而,增加小型化渦輪增壓發動機的輸出功率則有可能通過調整增壓壓力來實現。對于該發動機,可以通過將空燃比設定為化學計量比使BSFC改善57%。通過降低冷卻損失和泵氣損失能使指示熱效率提高42%,并使摩擦損失減少1%。雙VTC在寬廣的負荷范圍內對上述燃油經濟性的改善發揮了重要作用,通過提供最佳的內部EGR增強熱效率。
另一方面,據預測,按此方式使用內部EGR將會導致進氣門和進氣道表面積碳的問題。產生這方面問題的一個因素是運行竄漏氣體中包含有機油霧。此外,據報道稱,機油霧會導致發動機低轉速運行和高負荷行駛時出現低速早燃(LSPI)。采用圖16和圖17所示的一種收集機油霧的結構有可能限制積碳和LSPI。圖16所示為呼吸系統的通路。為了從竄漏氣體中分離機油霧,在氣缸蓋罩上設置了2個分離腔。
壓力控制閥(PCV)腔位于進氣歧管的上游,呼吸腔位于壓氣機前的進氣管上游。圖17所示為PCV和呼吸腔的內部結構。這兩個稱為渦流室的腔室,由兩部分組成。一個設置在氣缸蓋罩內,另一個是專用室蓋,并分別設有筋條。上部和下部的筋條可使氣流扭轉路徑。當竄漏氣體通過該腔室時,會產生2個渦旋流。當這些氣流被轉到左右和上下時,竄漏氣體中的機油霧就能靠撞壁作用從氣體中分離出來,最終成為液態機油返回到凸輪室中。
5低排放
小型化發動機與渦輪增壓器相結合是解決燃油經濟性和提高功率輸出的有效方法。但另一方面,由于渦輪增壓器熱質量增加會使冷起動后催化器溫度上升緩慢。圖18示出了為達到LEV3-SULEV30排放目標而采取的幾種NMOG+NOx減排措施。基本的NMHC+NOx水平由以前幾種滿足LEV2-SULEV法規的1.8 L自然吸氣發動機機型決定,這些發動機采用了相當于渦輪增壓器熱質量的排氣系統。
圖17 設置在氣缸蓋罩上
用于捕捉油霧的渦旋室結構
圖 18 幾種 NMOG+NOx的減排措施和
FTP-75測驗時的效果
圖19所示為在冷起動時(1 500 r/min,快怠速負荷,水溫25℃)燃燒波動和碳煙量與點火正時的關系。高滾流形成的混合氣均勻性和提高的湍流動能也有穩定延遲燃燒的效果。相比于常規的1.8 L自然吸氣發動機,渦輪增壓發動機在大尺度延遲燃燒時更為穩定。此外,在低溫情況下,燃油沒有直接噴射到活塞頂面,所以也能降低碳煙。將點火正時設定為比1.8 L自然吸氣發動機延遲12°CA,即使排氣系統中渦輪增壓器會增加熱質量,還是可以確保催化器溫度上升所需的熱排氣(圖20)。
圖19 IMEP變化率和碳煙量
與點火正時推遲的關系
(轉速1 500 r/min,水溫為25℃,
快速怠速臺架試驗時)
圖20 冷起動后排廢氣溫度和
催化器溫度的變化過程
圖21所示為催化器的結構和細節說明。最新的催化器能夠激活其自身的早期點火。這種催化器由載體和最近開發的催化涂層組成,前者能在很小的熱量下升溫,后者即使在低溫下也具有可靠的還原性能。該載體具有55%的孔隙率,比常規載體高27%~35%,這可以使熱質量降低30%~38%。最近開發的催化涂層中的鉑系金屬分散性更好,它能增強鉑系金屬的反應活性。因此,該催化劑能在催化器溫度約30℃的情況下,比常規催化器的溫度低,卻能達到相同的還原水平(圖22)。
圖21 催化器結構和細節說明
圖22 采用新開發的催化器
提高了HC和NOx的還原率
6振動和噪聲減少
在1臺小型化發動機上,要同時實現高輸出、輕量化結構、降低噪聲和振動是頗具挑戰的。新開發的發動機采用軸頸直徑較小的長行程曲軸有助于確保低摩擦和高熱效率。采用獨立的曲軸軸承蓋,這種軸承支承系統有助實現更輕的質量。利用本田公司自己開發的工具對各種部件的形狀進行優化,以處理振動和噪聲問題。通過修改曲軸的形狀實現了剛性更高的結構,并且通過修改曲軸皮帶輪的規格,減少了發動機主要運動系統的振動。如重新設計獨立軸承蓋的形狀(圖23)。對不同軸頸的軸承蓋作了改進,旨在減少它對振動傳遞的影響。采用這種方式使之具有足夠的剛性,使之在降低質量的同時減少振動。
此外,快速燃燒和使用直噴系統對研發提出了另外一個挑戰——高頻輻射噪聲。通過優化鏈條箱零件的表面形狀,以及在那些會產生噪聲輻射的零件上采用氨基甲酸酯隔層。新開發的發動機在同類機型中實現了最低的噪聲輻射(圖24)。
圖23 為減振、降噪和輕量化而優化的軸承蓋
圖24 新型小型化1.5 L增壓發動機在聲壓與
發動機扭矩關系圖上的位置
(輻射噪聲水平為轉速3 000~5 000 r/min
全負荷的平均值)
7輕量化結構
降低發動機質量還會對車輛的燃油耗產生重大影響。通過研究降低發動機質量,其質量相比同等輸出功率的常規自然吸氣發動機減輕了約30 kg。下面介紹采用的具體技術。
7.1排氣門高滾
發動機零部件要在因增壓導致熱量上升情況下保持可靠耐用十分重要。該發動機采用充鈉的中空頭部排氣門。為了確保氣門頭部的熱量有效地向下端傳遞,并防止排氣門和附近的結構過熱,充鈉一直延伸到了氣門頭部(傳統氣門只在閥桿中充鈉)。這有助于降低氣門的溫度。其結果是在不改變1.5 L自然吸氣發動機氣門材料的情況下,氣門材料更耐用且質量減輕18%(圖25,圖26)。
圖25 充鈉排氣門橫截面
圖26 排氣門的溫度和強度(最大功率點)
7.2加強工字梁桿身區的連桿強度高滾
為了承受增壓產生的高氣缸燃燒壓力,連桿的工字梁桿身區域采用了新鍛造技術,并采用適應渦輪增壓發動機的局部加強鍛壓法工藝。過程由兩步鍛造工藝組成的。第一步鍛壓為正常的熱鍛,桿身工字梁的橫截面鍛函比最終設計尺寸稍大。第二步鍛壓為冷鍛,鍛壓過程僅在桿身梁區施壓,采用非常精確的模具進行沖壓控制,使連桿能夠承受高負荷。這一效果相當于連桿抗彎強度增加了約30%。
增加強度的典型措施通常是替換連桿材料,或者使用某種類型的熱處理工藝,如回火。與此相反,本發動機使用的連桿僅在工字梁區得到了加強,大小端的材料硬度則與常規材料的相同。這就能在提高連桿強度和減重15%的同時,使得大小端在的機加工過程中較為容易操作(圖27)。圖28為不同連桿的比較。
圖27 加強工字梁區的連桿
7.3輕量化的中冷器連接高滾
傳統上,中冷器前后的管子都采用鋁材來制造,但新開發的發動機改為采用吹塑成型的PP-GF15樹脂。將丙烯酸橡膠(ACM)軟管做成波紋管的形狀,因而縮短了總長度,并有助于吸收管子的振動。與傳統結構相比,這種管子的成本更低,質量可減輕20%(圖29)。
8車輛性能
由于1.5 L小型化的渦輪增壓發動機采用了上述改善燃油經濟性和減輕發動機質量的措施,配裝該發動機的車輛達到了表3中所列的性能。
圖28 不同連桿的比較
圖29 采用輕質材料的中冷器連接管
表3 車輛性能
9結論
為了實現良好的行駛性能和環保理念,開發了一種1.5 L小型化渦輪增壓發動機。該發動機旨在用來替代1.8~2.4 L自然吸氣發動機。采用高滾流氣道、淺盆形活塞和多孔噴油器與長行程結構相結合,實現了快速燃燒和均勻的混合氣。雙VTC和小渦輪增壓器的應用增強了低端扭矩,能使用戶在使用普通汽油的情況下獲得駕駛的樂趣。該發動機達到的性能指標如下:
(1)最大輸出功率130 kW,比1.8 L自然吸氣發動機的功率提高了21%。同時,扭矩增加了26%,而最大扭矩時發動機轉速下降了2 600 r/min。
(2)發動機的最小比油耗是220 g/(kW·h),最大熱效率為38%。
(3)能達到LEV3-SULEV30排放標準。
-
中冷器
+關注
關注
0文章
4瀏覽量
6386 -
渦輪增壓發動機
+關注
關注
0文章
17瀏覽量
3293
發布評論請先 登錄
相關推薦
自制渦噴發動機,真有人敢玩!
直噴發動機:奔跑在市場與技術之間
關于1.5L雙燃燒循環自然吸氣發動機性能分析和應用
渦輪增壓發動機壽命影響因素_渦輪增壓發動機保養方法
渦輪增壓發動機與自然吸氣發動機兩款發動機有什么區別呢?
渦輪增壓發動機是什么?渦輪增壓發動機怠速與積碳的關系
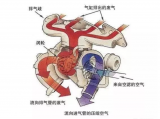
評論