1開發目標
從2011年起,Volkwagen公司開始用新型EA211標準部件發動機替代EA111結構系列的3缸和4缸汽油機,新發動機在高端系列和橫置模塊化標準部件平臺的功率和效率方面樹立了新標桿。
在開發EA211標準部件時,最初考慮將新型3缸增壓燃油分層噴射(TSI)汽油機作為小型化策略的重要組成部分。為滿足輕型、緊湊、高效和低成本方面的要求,并鑒于全球日益嚴格的廢氣排放法規,確定了以下開發目標:(1) 高升功率(85kW/L)和升扭矩(200N·m/L);(2) 盡早盡快提升扭矩;(3) 最佳的瞬態加速響應性能;(4) 燃油耗和CO2排放達到最佳水平;(5) 在整個特性曲線場中摩擦功率最低;(6) 無需附加質量平衡機構,曲柄連桿機構的運轉平穩性就能達到4缸機水平;(7) 整車達到Volkswagen公司A00-A級水平;(8) 可全球使用的堅固動力總成設計,并在慣性質量較大的轎車上具有較高的承載能力;(9) 使用燃油的靈活性。
此外,還面臨要大量應用EA211標準部件作為通用件參與全球制造裝配的挑戰。參考先前項目的開發經驗,將發展技術用于附加功能組合部件,以提高目標值。
2014年底,Volkswagen公司首次將新型3缸1.0L-TSI汽油機配裝于Polo轎車,其功率等級為70kW和80kW,CO2排放量從94g/km起[3]。自2015年5月起,作為藍驅技術機型(用于美國市場能滿足最嚴格廢氣排放法規的清潔機型),這種動力總成將配裝于Volkswagen公司Golf轎車,其功率為85kW,CO2排放量低于100g/km。該機型的主要技術規格列于表1。
表1 1.0L-TSI汽油機的主要技術規格
項目參數氣缸布置及氣缸數直列,3缸每缸氣門數4排量/mL999缸徑/mm74.5行程/mm76.4主軸承直徑/mm45.0連桿軸承直徑/mm47.5缸心距/mm82行程缸徑比1.025壓縮比10.5額定功率/kW70/81/85(5000~5500r/min)最大扭矩/(N·m)160/200(2000~3500r/min)升扭矩/((N·m)·L-1)160/200燃油(研究法辛烷值)ROZ95發動機電控系統MED17.5.21排放水平歐6。
2發動機系列設計方案
這種緊湊的全鋁4氣門汽油機采用EA211標準部件的模塊化結構設計,其關注點是降低摩擦、功能集成度高,以及更緊湊更輕的發動機結構,從而獲得了集成排氣歧管的3缸TSI氣缸蓋,并與水泵模塊相互配合達到了快速加熱、降低摩擦損失,并在實際使用中獲得了節油效果。所有對外密封軸密封裝置都配備了摩擦優化的徑向密封環。
凸輪軸由1條密封灰塵、免維修和摩擦小的齒形皮帶傳動,氣門則通過滾輪搖臂驅動,集成為氣門驅動模塊。直徑減小的凸輪軸滑動軸承減少了摩擦損失,剛性緊湊的軸承結構型式對氣門驅動的動力學產生了有利影響。進氣或排氣凸輪軸在配氣傳動機構側的第1道軸承承受皮帶的附加力,出于降低摩擦的原因,采用向心球軸承。
圖1 新型3缸1.0L-TSI汽油機
基礎發動機上的輔助設備布置緊湊,沒有額外支架,并且都使用標準部件的零件。圖2以新型1.0L-TSI發動機為例,示出了EA211發動機系列典型的發動機模塊組合部件,只在81kW機型和85kW機型的廢氣渦輪增壓器和氣門傳動機構中應用了高價值材料,以提高其負荷承載能力。
圖2 EA211發動機結構型式
3氣缸體曲軸箱
氣缸體曲軸箱采用AlSi9Cu3鋁合金壓鑄成形的開放式頂面結構型式,鑲鑄的氣缸套使用全球通用燃油可靠運行。為優化散熱性能,氣缸套外圓被設計成粗糙表面,一方面能增大與鋁制缸體的結合表面積,同時使2種材料貼合得更為緊密。為減小摩擦,氣缸套采用中心架珩磨工藝加工,因此,即使活塞環組的切向力較小,仍具有良好的表面貼合性,使機油消耗量和曲軸箱通風量都較少。
氣缸套曲軸箱具有許多鑄造成形的通道,用于供應壓力機油、機油回油、冷卻液循環和曲軸箱通風等,機油冷卻器也可通過氣缸體曲軸箱中專用通道與機油和冷卻液相通。曲軸箱幾乎僅在發動機內部進行部分通風(圖3),為阻擋機油飛濺,氣體從曲軸箱空間進入安裝在曲軸箱中的機油分離器,分離出的機油在機油液面下回流到油底殼中,而氣體則通過氣缸體曲軸箱中的1條上升通道引導到氣缸蓋和整體式氣門驅動機構,從而進入廢氣渦輪增壓器。因去除機油的曲軸箱通風氣體在機內流動,因此,能確保在低溫下發動機運行時不會結冰,而且曲軸箱通風氣體量較大。在吸氣行程時,曲軸箱通風氣體從與機油分離器相連接的通道經過集成在進氣管中的止回閥直接進入發動機進氣歧管。這種機內的曲軸箱通風系統可靠性較高,因為從一開始就避免了出現缺陷。
圖3 氣缸體曲軸箱的通風系統
為了避免即使在頻繁的短途交通情況下出現冷凝情況,在氣缸體曲軸箱真空下,新鮮空氣不斷從空氣濾清器凈化空氣側,通過氣缸蓋罩中的止回閥由發動機吸入,發動機暖機時泄漏的曲軸箱氣體被新鮮空氣流攜帶通過機油分離器進入氣缸燃燒。
4曲軸連桿機構和活塞組
曲柄連桿機構具有運動質量輕和摩擦小的特點,因而能取代3缸發動機上常用的平衡軸,并無損于舒適性。與4缸機一樣,曲軸的連桿軸頸也鉆成空心,即使需要較高的功率,因優化了主軸承和連桿軸承的設計,仍可進一步減輕發動機質量和降低曲柄連桿機構的摩擦,并對燃油耗產生有利影響。所采用的4個平衡塊降低了曲軸的內部應力和軸承負荷,此外,有針對性的質量平衡能較為明顯地降低傳動系統中的振動激勵。
EA211標準部件中的新型技術組件是無小頭孔襯套連桿,這是首次在1.0L-TSI和具有主動氣缸管理系統(ACT)的1.4L-TSI-ACT汽油機上應用。采用由Volkswagen零部件公司開發的有利于降低成本的滾壓工藝加工連桿小頭孔,與浮動支承并有類金剛石石墨涂層的活塞銷相配合進一步降低活塞支承摩擦,同時,通過活塞頂的平坦設計減輕了活塞質量,并改善了溫度分布。
5氣缸蓋
1.0L-TSI汽油機的氣缸蓋采用翻轉式金屬模鑄造方法制成(圖4),為確保獲得高品質的金相組織,采用AlSi10Mg(Cu)鋁合金并經過熱處理,燃燒室周圍采用橫流式冷卻。與1.0L多點噴射式(MPI)汽油機相比,集成排氣歧管的氣缸蓋針對散熱和消除冷卻系統節流進行了重新設計和優化,因此,能使發動機快速達到其運行溫度,并在正常運行時冷卻廢氣流。在上述條件下,幾乎在整個特性曲線場范圍內都能達到過量空氣系數λ=1的燃油空氣比,從而降低了CO2排放和用戶實際使用燃油耗。
圖4 集成排氣歧管的氣缸蓋
將屋頂式燃燒室上方的進氣門傾斜21°,排氣門傾斜22.4°,由滾輪搖臂操縱。氣門桿直徑為5mm,進氣門座角度為90°,而排氣門座角度為120°,以確保使用代用燃料時的耐磨性。功率81kW以上機型均使用鈉冷卻的排氣門,并采用AR20D材料的高耐磨性氣門座圈,在功率為75kW的基本機型上,整個氣門都采用X45高強度合金鋼,氣門座圈采用燒結材料制成。氣缸蓋上的氣門機構由整體式氣門傳動模塊驅動。
6冷卻系統
沿用EA211標準部件發動機中由機內高溫循環回路和低溫循環回路組成的冷卻系統。電動冷卻液泵全柔性地按需調節,供應低溫循環回路中的增壓空氣間接冷卻及發動機停機后廢氣渦輪增壓器后冷卻所需的冷卻液,而高溫循環回路中的發動機冷卻則由整體式水泵-節溫器模塊調節,借助于免維護的齒形皮帶由排氣凸輪軸驅動。
整體式水泵-節溫器模塊中包括1個進水道和2個回水通道。節溫器殼體采用PA6.6材料制成并用螺栓與鋁壓鑄件連接,能容納2個節溫器,以及與冷卻器進水或回水和采暖熱交換器連接的管接頭。冷卻水從水泵經過氣缸蓋中的連接通道,進入氣缸體曲軸箱中的水道,主冷卻水流在87℃溫度下通過氣缸密封墊引入氣缸蓋,與冷卻燃燒室的橫流水流和平行冷卻整體式排氣歧管的第2股冷卻水流相遇,2股水流在節溫器前匯合,并流入主節溫器前的混合室。
圖5 冷卻水泵-節溫器模塊及冷卻水循環回路
冷卻液在氣缸體曲軸箱起始點從水道直接流入發動機機油冷卻器,并在第1缸前又流回水道,在相同位置有1個流入第1缸水套的進水口,氣缸側第2個冷卻回路從這里開始,沿著縱向在流經氣缸2和氣缸3后流入節溫器殼體,并經過第3個連接通道流到曲軸箱節溫器前,該節溫器在105℃時打開,冷卻液就能流入主節溫器前的混合室,而主節溫器還調節流經汽車散熱器的冷卻水流動。
7配氣機構
整個配氣機構的零部件均沿用EA211模塊化發動機標準部件。曲軸通過免維護的齒形皮帶驅動凸輪軸,皮帶松弛邊由永久張緊導輪兩側的止推凸肩導向,而拉力邊則由剛性的轉向輪維持皮帶的平穩運行。
正如該發動機系列中的3缸1.0L-MPI汽油機,進排氣凸輪軸的V形皮帶驅動輪幾乎完全消除了旋轉不均勻性,并明顯降低了皮帶拉力,但仍能保證最小動態皮帶力始終處于有利的范圍內,因而確保了齒形皮帶與齒形皮帶輪之間的附著力。
為了優化高低轉速范圍內的功率輸出,進排氣凸輪軸都應用葉片式液力相位調節器。進氣凸輪軸相位調節器的調節范圍為50°CA,排氣凸輪軸相位調節器的調節范圍為40°CA,這樣就能在低轉速時獲得大扭矩,而在高轉速范圍內達到高功率。
8機油循環回路
Volkswagen公司首次應用按特性曲線場無級調節的機油泵(圖6),其特點是內部摩擦較小而使驅動功率減小。將葉片式機油泵集成在前端密封法蘭中,并套過曲軸軸頸安裝在氣缸體曲軸箱上。機油壓力是由安裝在曲軸軸頸上的內轉子驅動的葉片形成的油室建立起來的,而機油泵吸油側通過直接安裝的塑料吸油管從油底殼吸入機油。油底殼由鋁整體壓鑄后經熱處理制成,并通過有針對性地設計加強筋優化聲學特性。機油從泵的壓力側通過氣缸體曲軸箱中的通道抵達固定在油底殼上的機油濾清器,輸入主油道,再從主油道分配到主軸承和連桿軸承,并經過上升通道進入氣缸蓋上的配氣機構,由氣缸蓋中的2條油道給滾輪搖臂供應機油,機油再通過鉆孔分流通道抵達凸輪軸軸承和凸輪軸相位調節器的進油閥。在變速器端,壓力機油經過最后一道主軸承通過鉆孔向外輸送,在那里的導管能確保向廢氣渦輪增壓器供應機油。并僅在機油壓力水平較高時才向活塞頂噴射機油冷卻。
圖6 機油循環回路和按特性曲線場調節的
機油泵
機油泵的機油壓力由液壓和電子調節回路調節。通過從主油道至機油泵的連接進行外環區域的液力壓力調節,而電子控制的比例電磁閥則按需將機油壓力調節在0.10~0.33MPa之間,位于氣缸蓋上升通道中的機油壓力傳感器為此提供所需信息,這種由機油泵控制的特性曲線場根據轉速和負荷需要進行設計。
9廢氣渦輪增壓器
在開發渦輪增壓器時,低轉速時的大扭矩和具有豐滿扭矩特性曲線的瞬態性能起著主導作用。針對集成在氣缸蓋中的排氣歧管中廢氣熱焓較少的狀況,采用單流道渦輪增壓器,其轉子特點是外形尺寸和慣性力矩較小,效率水平較高。廢氣渦輪增壓器由高耐熱奧氏體合金鑄鋼制成,能承受高達1050℃的廢氣溫度,而渦輪葉輪采用MAR-M246鎳基合金。
1.0L-TSI汽油機的增壓壓力最大可達到 0.16MPa (相對壓力),是EA211發動機系列中的最高值。增壓壓力由新開發的電動廢氣放氣閥調節器調節,無須依賴增壓壓力進行控制,因此廢氣放氣閥在低轉速時能可靠關閉,并能確保順利建立起較陡的扭矩特性曲線。在部分負荷范圍內,因廢氣放氣閥完全打開使廢氣背壓很低,從而降低了換氣損失。
10熱力學:充量運動和滾流
以4缸TSI汽油機量產進氣道為基礎,運用Volkswagen公司研究中心的發動機零部件自動優化開發工具進一步提高了進氣道的滾流數,而對流量系數沒有明顯的不利影響。圖7示出了用穩態和非穩態計算流體力學(CFD)模擬計算,結果得出的進氣道方案的包絡曲線帶、基本進氣道和用于1.0L-TSI汽油機的目標進氣道都位于包絡曲線帶的最上方。
圖7 氣道方案的包絡曲線
圖8示出了新滾流進氣道提高的流動速度。特別注重抑制不位于滾流主軸上的擾動成分(Ω擾動),從而確保流入空氣對燃油噴束的均勻席卷、高均質化程度和點火上止點時的擾動動能水平。
圖8 滾流氣道的流動設計
11混合氣形成和燃油噴射
1.0L-TSI汽油機的開發目標是在低轉速和寬廣的轉速范圍內提供大扭矩(圖9)。燃燒空氣通過汽車上的進氣口進入安裝在發動機進氣管和氣缸蓋上方的空氣濾清器。增壓空氣通過直徑為44mm的電控進氣門接管進入集成增壓空氣冷卻器的進氣管。燃油系統中的燃油蒸氣經過燃油箱通風閥進入發動機進氣管,直接位于進氣門后,能確保進入的燃油蒸氣均勻地分配到3個氣缸。
圖9 功率和扭矩特性曲線
在EA211系列發動機上首次應用最高噴油壓力為25MPa的高壓噴油系統。高壓燃油泵和不銹鋼共軌與提高的系統壓力相匹配,并采用5孔電磁閥噴油器實現高壓噴油。借助于CFD模擬計算,針對新的滾流進氣道優化了燃油噴束的貫穿度、零件潤濕和均質化程度,而模擬計算的有效性借助整機和玻璃透明試驗發動機上的光學測量技術予以驗證。高噴油壓力使噴油器能獲得最小噴油量和最佳的噴油持續期。在部分負荷和全負荷時,以及催化轉化器加熱期間,運用多達3次的多次噴射能進一步降低廢氣排放,并減少燃油摻入機油的數量,同時提高了燃燒穩定性,其中通過發動機電控單元中的特殊功能將噴油量的誤差降至最低。
12結語
Volkswagen公司開發了新型3缸1.0L-TSI汽油機(圖10),在開發期間就考慮到未來用于燃油品質較低的市場,用于乙醇和壓縮天然氣運行的部件和零件改進也被考慮其中,因此,新機型現已具備寬廣應用范圍,可用于不同車型平臺。
圖10 EA211模塊化直噴式汽油機
持續不斷地利用EA211模塊化標準部件,以及全球統一的制造工藝,使產品開發成本低、周期短,并能利用Volkswagen公司車間中的成套工藝裝備進行生產。
為Polo和Golf轎車開發的新型高度模塊化和經濟性的動力總成,將TSI典型的高品質、高效率和駕駛樂趣相結合。與老機型相比,配裝3缸TSI汽油機的Polo轎車的CO2排放降低了17%,同時升扭矩較高使其具備良好的急加速性能,獲得了TSI車型典型的駕駛樂趣,并且,在具有出色的運轉平穩性的同時,獲得了優異的行駛舒適性。
新型3缸TSI汽油機具有緊湊的結構型式,其出色的扭矩和功率輸出與較低的CO2排放相結合,是EA211發動機系列發展中的又一個里程碑。
-
燃油
+關注
關注
0文章
42瀏覽量
17647 -
汽油機
+關注
關注
0文章
58瀏覽量
11529 -
渦輪增壓器
+關注
關注
3文章
90瀏覽量
11682
發布評論請先 登錄
相關推薦
ECU調校對汽車性能的影響
直噴發動機的優缺點有哪些
直噴發動機和電噴發動機的區別
電控燃油噴射系統的工作過程
共軌電控噴射系統的特點有哪些
激光淬火技術在硬化缸筒的工藝應用
汽車發動機上的電控技術主要包括什么
STM8S003外部干擾,頻繁復位重啟怎么解決?
奧迪S3 2024款性能優化,搭載全新RS3扭矩分配器
福特野馬旗艦性能版回歸中國,搭載5.0L Coyote V8自然吸氣引擎
伺服電缸和伺服壓機區別 伺服電缸能取代液壓油缸嗎

廢氣渦輪增壓系統的檢修方法
廢氣渦輪增壓系統的主要組成
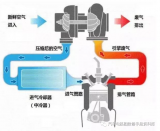
評論