OM654機型是Daimler公司推出的全新開創性發動機系列。介紹其技術理念和新發動機系列中首款機型的創新,OM654機型是未來柴油機的代表。
1發動機設計
在新柴油機系列的設計理念中,除了提高功率、減輕質量和降低摩擦之外,開發需求主要集中在面向未來的低排放理念和降低燃油耗。為此,需要開發全新的燃燒系統、廢氣再循環系統和排氣后處理系統。
2發動機系列的結構設計理念
新Mercedes-Benz動力總成結構設計的目標是,將動力總成統一布置在當前和未來車系的汽車內,并近發動機布置排氣系統。
基礎發動機的缸徑、行程和氣缸間距等主要尺寸決定了發動機安裝長度、高度,以及發動機整體的緊湊設計。
考慮下列因素將缸徑和行程分別設定為82.0mm和92.3mm: (1) 單缸排量接近500cm3;(2) 鋁制曲軸箱承受的最高壓力可達20.5MPa;(3) 考慮到燃燒和摩擦的最佳曲柄連桿比。
由于發動機前端的正時驅動系統在很大程度上決定了安裝高度,所以沿用原4缸柴油機的傳動側布置方式。為了將發動機放置在汽車下部,在曲軸的左右兩側安裝蘭徹斯特平衡軸。此外,為了在安裝時不受車輛限制,新機型的機油泵與原機型保持一致,安裝在曲軸旁邊。
發動機的垂直安裝和曲柄連桿機構偏置,使汽車右側有足夠的排氣系統安裝空間。由于排氣系統和渦輪增壓器放置在發動機右側,因而換氣部件(空氣濾清器、進氣分配器和水-空中冷器)、高壓泵、空調壓氣機和發電機安裝在左側。
在汽車系列中統一布置發動機是實現部件高度通用化和汽車接口統一設計(如真空、水、燃油或空氣)的重要步驟,因而變速箱凸緣在汽車中的位置不變。
因此,采用Mercedes-Benz動力總成結構設計(圖1),并且在汽車系列中統一布置發動機和與變速箱凸緣相關的零部件;并確保系列的高度通用化和近發動機布置排氣系統。同時,大幅減少排氣系統變化和受影響的部件,并統一汽車媒體接口。
3OM654型發動機
下文介紹新發動機系列的首款機型OM654的設計。
3.1技術與創新
根據開發目標進一步提升OM654機型的性能、摩擦和噪聲-振動-平順性(NVH)性能。為滿足燃油耗和排放要求,需要進行熱力學和排氣后處理方面的創新(圖2)。
3.2基礎發動機
Mercedes-Benz基礎發動機的結構設計采用了大量新部件和新方法。
3.2.1采用蘭徹斯特平衡軸的曲柄連桿機構
基于90mm的氣缸間距將空心曲軸設計為主軸承直徑為55mm、寬為20mm的鋼鍛造部件。相應的連桿軸承尺寸直徑為52mm,寬度為19mm。
由滾動軸承支承的位于底部的2個平衡軸來平衡二階慣性力。單平衡軸由過盈安裝在曲軸第8曲柄臂上的主動輪和預緊安裝在各個平衡軸軸端的斜齒輪嚙合驅動。
3.2.2采用雙絲電弧噴涂技術和軸承架的全鋁曲軸箱
采用優化的“Nanoslide”涂層的全鋁曲軸箱是種全新設計。曲軸箱采用深裙結構設計,并通過油底殼進行加固和密封。“Nanoslide”優化工藝的關鍵點是,氣缸壁處理工藝由原來的高壓水噴射轉換為機械粗加工。
3.2.3采用階梯式燃燒室的鋼活塞
6缸柴油機首次搭配使用“Nanoslide”涂層與鋼活塞,這為新發動機系列的所有柴油機機型奠定了基礎。鍛焊式鋼活塞采用42CrMo4合金鋼。OM654的帶階梯式燃燒室的鋼活塞首次被應用于乘用車領域(圖3)。
3.3“冷端”
為實現高升功率,對進氣至渦輪增壓器壓氣機的所有空氣管路的壓力損失進行優化,使空氣流量盡可能增大。發動機控制裝置也集成在空氣濾清器中(圖4)。
另一個重要的設計理念是,優化從廢氣渦輪增壓器的壓氣機至氣缸蓋的增壓空氣管路設計,最大程度地提高進氣密度。集成的水-空中冷器發揮重要作用,它將額定功率時的壓縮空氣溫度降至50℃。
4熱力學
OM654機型將采用階梯式燃燒室的燃燒系統首次應用于乘用車柴油機,下文將介紹其零部件及使用方法。
4.1燃燒室
燃燒室的設計目標是使活塞凹坑在總壓縮容積中的比重(即k因子)最大化,也就是使燃油噴束無法到達的盲區最小化,從而實現最大的空氣利用率和較小的炭煙值。
在概念階段已決定采用新的燃燒系統,這是首次將帶階梯式燃燒室的活塞用于乘用車。由于活塞與氣缸蓋之間的擠流區域非常狹窄,因而采用相對較小的避閥坑來防止活塞與氣門碰撞。氣門向燃燒室(活塞)方向偏移可以減小氣缸蓋附近的盲區,由此導致相應的凹坑容積增大4%左右。在單缸機及仿真中已驗證,較深的活塞避閥坑對燃燒室進氣運動產生的消極影響(渦流減少)可忽略不計。在這種情況下采用鋼活塞也是有利的,鋼活塞的頂岸高度明顯比鋁活塞更低,使得盲區大幅減少。
通過采取這些措施,盡管氣門總體傾角達到了10.5°,凹坑容積占用仍有77%,僅比氣門垂直布置時(理論上可達79%)略低一點,但避免了氣門垂直布置時產生的進排氣影響和其他結構限制的缺點。
4.2燃燒系統
OM654機型的燃燒系統為全新開發,是Daimler公司首次在乘用車領域采用帶階梯式燃燒室的燃燒系統,其主要特征是活塞凹坑采用階梯式設計。新燃燒系統的優點是空氣利用率極高且顆粒排放較低。燃燒速度比ω燃燒室更快,因而效率更高。同時,凹坑形狀產生的氣體保護層減少了機油積炭和氣缸壁燃油浸濕現象。由于改善了燃燒室的流動情況,所以氣缸壁熱損失降低,氣缸蓋溫度分布更均勻,氣門座孔之間部位的高應力得到緩解。總體來說,降低氣缸壁熱損失,有利于提高效率。
4.3燃油噴射技術
噴油器采用已通過檢驗的帶8孔噴嘴的壓電噴油器CRI3,并進一步改進熱力學、流量和噴孔幾何結構,使其適用于新的燃燒系統,系統最高壓力達205MPa。高壓泵采用Bosch公司的CP4單柱塞泵。
4.4增壓
發動機右側的排氣系統與集成的霍尼韋爾單級廢氣渦輪增壓器GTD1449組成協作單元,以確保壓力損失和熱量損失最小化。通過與發動機和排氣系統的主要高溫氣體部件絕緣,溫度敏感部件的較高熱負荷降至安全水平。采用水冷式軸承殼防止增壓器油炭化。
與現今常用的功率級和排量級的渦輪增壓器相比,低于1800r/min轉速范圍內可獲得近70%更好的增壓壓力梯度。結合低壓EGR,可以達到二級增壓原機型在瞬態特性方面的高要求。
4.5多路EGR
新一代柴油機的1個重要研發目標是降低顆粒物排放。為此,除了可靠的燃燒系統,還需要1個高效的多路EGR系統。多路EGR系統由兩條EGR路徑組成(圖5)。這種組合方式能在非常寬廣的特性圖區域實現效率優化并滿足未來的顆粒物排放要求。
主動冷卻的高壓EGR與“熱端”的排氣歧管相連接并接入“冷端”的增壓空氣供給管路,按照最短路徑連接方式布置在發動機前端(圖4)。同樣冷卻的低壓EGR布置在發動機后端。
高壓EGR路徑采用傳統布置方式,從排氣歧管中提取廢氣,通過EGR控制閥經旁通或經冷卻器進入進氣管。
低壓EGR路徑從SCR系統后的管路提取清潔廢氣,同樣通過控制閥和冷卻器輸送清潔廢氣,在壓氣機上游與新鮮空氣混合。為了提供必要的壓力梯度,在排氣系統中集成無級可調排氣閥。
這兩種EGR路徑的設計重點是,制造可以確保快速瞬態響應的體積最小化的較短部件和可以確保最佳換氣的優化壓力損失的部件。例如,在多路EGR運行時,無需采用節流閥調節高壓EGR。
進氣道建模和控制策略允許高壓EGR和低壓EGR在發動機性能脈譜圖區域內進行完全可變混合運行,因此也為穩態優化的燃油耗設置用于瞬態區域打下了基礎。
圖5所示的EGR率反映出燃燒系統的潛力,顯示出顆粒物排放水平降低(尾管排放大幅減少)。
4.6全負荷性能
盡管EGR作用于全負荷工況點,但未對發動機動力性能產生太大的影響,新EGR發動機仍以143kW的功率刷新了2L單級渦輪增壓發動機的記錄(圖6)。
5排氣系統/排氣后處理系統(“熱端”)
排氣后處理部件是新發動機的重要組成部分,是采用高度通用化的低排放概念的基本模塊。為滿足未來排放法規(WLTP和RDE),對發動機尺寸、結構及功能布置進行系統設計。“熱端”由1系列的單個模塊組成,這些模塊構成1個單獨的模塊化系統(圖7)。
通過隔離措施(溫度、噪聲)和改善的催化劑涂層,在冷起動和低負荷運行時不再需要發動機溫度管理。除了排放方面的優勢,還可以減少CO2排放量,尤其是路程較短時減排更為明顯。在DPF中集成SCR功能可有效降低NOx,即使排氣溫度較低,仍有利于低負荷范圍的排放性能。
SCR催化轉化器位于sDPF之后,使高負荷范圍的性能最佳。不同于原機型,這種“熱端”有非常大的載體作用截面,降低了約40%的排氣背壓。
6AdBlue制備與均勻分布
研發重點是提高AdBlue制備效率并降低背壓。由于安裝空間受限,要確保在非常小的空間里實現無沉淀物的AdBlue還原劑制備,并且除了蒸發、熱解和水解,還在相對較大的催化轉化器截面下實現均勻分布。為了確保在寬廣的特性圖區域中有較高的NOx轉化率,要求無逸氨催化轉化器(ASC)的系統的NH3均勻分布指數大于98%,以實現系統的可靠控制與監測。
為了滿足上述功能要求,針對安裝空間限制研發出創新的AdBlue蒸發與混合概念,并獲得專利(圖7)。
利用這種概念布置了多個在流動方向上的蒸發器板,蒸發器板在空間上交錯布置,每個蒸發器板都會接收到部分噴射錐,從而實現還原劑初始均勻化。蒸發器板的排列、AdBlue噴射器的精確布置,以及噴射錐的定位都是完全匹配的。蒸發器板沿排氣流線布置,從而使蒸發裝置的壓力損失比傳統裝置減少30%以上。
在蒸發裝置下游,排氣流入1個橢圓形通道,并形成對稱的雙渦流。由于產生渦流,所以還原劑保留時間增加,同時還實現有效混合。通過這種方式,即使在劑量較多的情況下也能避免產生沉淀物,同時在較大的sDPF橫截面下實現較高的NH3均勻分布指數(0.97~0.99)。
7排放值
OM654機型采用高效EGR系統、新燃燒系統、增強的EGR兼容性和近發動機布置的排氣系統,使SCR系統的運行范圍大幅擴展,并進一步顯著提升高負荷范圍內的實際功率,可在整個發動機工作范圍內實現極低的排放。RDE工況下的NOx與原車型相比大幅減少(圖7)。
8噪聲情況
除了對發動機機體結構、變速箱總成連接、齒輪傳動及空氣導管采取大量設計方面的優化措施,還采用了塑料發動機支架,這些措施可實現新的最優值。
9發動機質量
盡管有技術指標要求,OM 654機型仍采取各項措施達到減輕質量的既定目標(圖8)。相比功率為125kW的OM651原機型,新機型不僅將功率提高到143kW,質量還減輕了35.4kg。
10摩擦損失
通過部件與系統評估以及計算推論,對開發發動機的摩擦損失和功率損失進行早期評估。總體而言,與原機型OM651相比,OM654基礎發動機的摩擦有明顯改善(圖8(c))。與相應的批量生產4缸柴油機的摩擦平均有效壓力FEV分布圖進行競爭比較(圖8(b)),可看出措施的實施很成功。
在相應的摩擦扭矩特性圖中,OM654機型顯示出明顯的與負荷的相關性。特別是摩擦損失的大幅降低時,為了滿足客戶和未來適用的WLTP測試循環(比NEDC要求的負荷更高)對更高負荷的需求。大幅降低的摩擦損失使新發動機比OM651機型節省燃油約6%。
11整車效果
通過采用新燃燒系統、更小的廢氣渦輪增壓器設計、摩擦措施,以及大幅降低整個換氣的節流損失,為靈活的發動機響應特性創造了必要的設計條件。由于進一步優化調節變扭器和變速箱,并使發動機質量減輕17%,所以搭載OM654機型的車型在起步時有明顯的扭矩優勢(圖9)。
同樣,OM654機型傳動系統是具有最佳行駛性能的高效傳動系統。對0~100km/h的加速時間進行評估,搭載新機型的車型行駛性能比搭載相應原機型的車型改進了10%以上,加速時間相當于縮短了將近1s。
12燃油耗
如圖10所示,從油耗值表現可看出所采用技術的效果。采用可靠的帶階梯式燃燒室的燃燒系統、高效的EGR、降低摩擦與質量的措施,以及近發動機的排氣后處理,可使排放值大幅降低,并產生新的最佳油耗值,CO2排放量為102g/km。
13結語
新型OM654 2.0L 4缸發動機是新發動機系列的首位成員,隨著它的推出,Daimler公司在柴油機領域樹立了燃油耗、行駛性能、舒適性和排放的新標準。
新型發動機首次應用將搭載在新E級車型,隨后將用于更多車系。基于新發動機系列的其他功率級和排量級的發動機正在研發中。
-
發動機
+關注
關注
33文章
2473瀏覽量
69275 -
柴油機
+關注
關注
1文章
171瀏覽量
26256 -
熱力學
+關注
關注
0文章
43瀏覽量
9313
發布評論請先 登錄
相關推薦
發動機參數采集與分析系統的matalb仿真
發動機總成包含哪些部件_發動機總成包括什么_發動機總成圖解
深度評測大眾EA888發動機
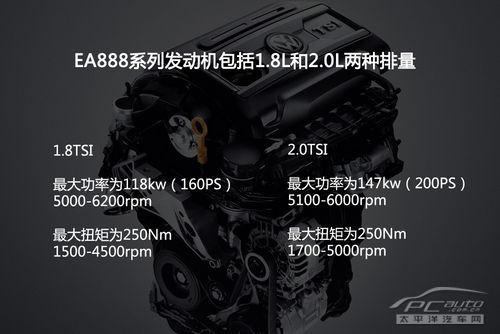
關于奔馳發動機換代的常規解讀詳解
關于“上汽π”發動機性能簡介
關于1.5L雙燃燒循環自然吸氣發動機性能分析和應用
關于Mercedes-Benz大型載貨車用柴油機2性能分析
Mercedes-Benz公司開發M936G型天然氣發動機性能分析
關于Mercedes-Benz公司4缸增壓直噴式汽油機性能分析
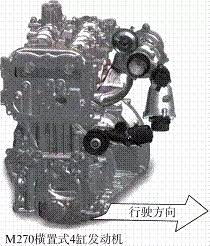
評論