豐田汽車公司正在開發一系列符合經濟型高熱效率燃燒(ESTEC)開發理念的發動機。繼2.0L缸內直噴渦輪增壓發動機8AR-FTS投放市場后,介紹8NR-FTS發動機的開發。8NR-FTS發動機為1.2L直列4缸火花點燃式的小型化渦輪增壓缸內直噴汽油機。基于8AR-FTS發動機相同的基本理念,8NR-FTS發動機集成了各種節能技術,諸如集成排氣歧管的氣缸蓋、通過帶有中間鎖止裝置的智能廣角可變氣門正時系統(VVT-iW)實現的阿特金森循環,以及為實現快速燃燒采取的缸內強化渦流。該發動機采用缸內直噴的直噴渦輪增壓(D-4T)系統,替代了兼備進氣道噴射和缸內直噴的渦輪增壓高版本汽油機(D-4ST)系統。結合單渦道渦輪增壓器和VVT系統的控制,實現了發動機低速工況下的高扭矩特性。該發動機還采用了起停控制策略,通過在第一個壓縮的氣缸內分層噴射,實現了快速無沖擊重新起動。發動機可以匹配6檔手動變速器(6MT)或無級變速器(CVT)。尤其在CVT模式下,通過換檔控制,減小了渦輪增壓器的滯后期;通過“常規”和“運動”兩種駕駛模式的轉換,能夠實現具有駕駛樂趣的動力性能和出色的燃油經濟性。
繼2.0L直噴渦輪增壓8AR-FTS發動機投放市場后,豐田汽車公司開發了新型1.2L直列4缸小型化缸內直噴渦輪增壓汽油機8NR-FTS。該發動機于2015年3月在日本上市,2015年5月在歐洲上市,替代現有的1.6~1.8L自然吸氣式發動機。表1示出新型8NR-FTS發動機與8AR-FTS發動機的主要區別。新型8NR-FTS發動機配置了IHI渦輪增壓器公司制造的單渦道渦輪增壓器,是自2003年開發3GR/4GR-FSE發動機以來,豐田公司首次開發的無進氣道噴射的新型缸內直噴發動機。發動機匹配6 檔手動變速器(6MT)或無級變速器(CVT)。
1 發動機規格和燃燒理念
表2為8NR-FTS發動機主要規格參數,屬于豐田ESTEC發動機系列(ESTEC為豐田下一代發動機技術的代名詞,指“高效燃燒的低燃油耗”技術)。發動機壓縮比為10,使用研究法辛烷值(RON)為95或以上的燃油,滿足歐6和J-SULEV排放法規。
這些發動機實現快速燃燒的基本途徑是提高進氣流量和增強缸內渦流。8NR-FTS發動機是豐田公司最小排量的缸內直噴發動機,缸徑相對小。因此,為了使燃油噴霧在接觸氣缸壁前與空氣混合,需要更強烈擾動的進氣流。為提高進氣道形狀設計的靈活性和安裝便利,該發動機采用了無進氣道噴射的缸內直噴技術。如圖1所示。采用這種配置可對氣道形狀進行優化,提高進氣流量,增強缸內滾流。此外,在為使催化器快速起燃而推遲點火正時的條件下,為實現穩定燃燒,將傳統的淺盤型活塞改為碟盤曲線形活塞,而且不會減弱缸內滾流(圖2)。這些措施防止了滾流衰減并加強了缸內壓縮行程后期的渦流(圖3)。
該發動機采用了與豐田公司其他缸內直噴發動機相同的扇形噴霧。不同的是斜巢噴孔和油膜厚度更窄(圖4),這項噴霧改進增加了燃油和空氣之間的剪切力,促進了燃油的霧化。與傳統扇形噴霧相比,噴霧長度下降了23%,從而降低了氣缸壁上的燃油附壁量。此外,為減少燃油對進氣門的沖擊,以及減少燃油通過氣門頭部背后散射到氣缸壁上的燃油,優化了氣門傾角和噴油角度(圖5)。
此外,將單個循環內的燃油噴射分為多次噴射,減小了噴霧油束的長度。圖6示出不同發動機和不同噴油器的機油稀釋率。燃油噴霧和配氣機構的優化減少了燃油附壁量,改善了機油稀釋問題,同時也改善了混合氣的空燃比。
2 渦輪增壓器和排氣系統
將排氣歧管集成于氣缸蓋實現了緊湊的排氣系統。為改善冷起動工況下的催化性能,將催化器置于渦輪增壓器出口附近。
在渦輪側,為確保發動機在極低轉速下具有大扭矩特性和高瞬態響應性,采用了在較寬渦輪轉速范圍內高效率低慣性的單渦道渦輪增壓器。此外,采用了能夠靈活控制廢氣旁通閥(WGV)開度的主動控制式廢氣旁通系統。發動機起動時,WGV打開向催化器提供高溫燃氣,減少催化劑起燃時間。為減小排氣損失,在發動機低負荷運行區域也打開WGV。通過降低泵氣損失和改善燃燒特性(減小缸內殘余廢氣量),提高了燃油經濟性。
2.1 空燃比傳感器安裝位置和流道形狀
為了能夠在WGV 任意開度、任意旁通比和流量條件下精確檢測空燃比,對空燃比傳感器周圍的流道形狀專門進行了設計。尤其是在WGV 打開時,該設計僅將來自WGV 的廢氣導向空燃比傳感器。使未受渦輪攪動的氣體與傳感器接觸,實現各缸空燃比的精確檢測。為防止水造成傳感器的損壞,對傳感器和流道表面的位置也進行了確定(圖7和圖8)。
3 全負荷性能
小型化渦輪增壓發動機的優勢之一是能夠獲得較大的低速扭矩,這有助于改善車輛的燃油經濟性,因為在與傳統發動機相同功率條件下變速箱可以置于較高檔位,使發動機運行在較低轉速工況下。此外,采用手動變速箱,在發動機和車輛的低速工況時可以獲得充足的扭矩。可以通過減少換檔頻率,而且避免了發動機轉速不必要的增長。因此,駕駛員可以獲得理想的動力性能和較好的燃油經濟性,關鍵在于確保充足的低速扭矩,各家公司采用了各種方法降低最大扭矩對應的發動機轉速。
通常,為了提高增壓壓力,需要增加進入渦輪的排氣能量(即增加排氣流量和排氣溫度)。但是,發動機在低速時較少的氣量很難滿足高增壓壓力的需求。可行的應對措施是改變氣門正時,將進氣門關閉正時設置到接近下止點(BDC),防止進氣倒流,確保足夠的進氣流量。然而,這會導致在上止點(TDC)附近有較大的進排氣重疊角。以直列4缸發動機為例,相鄰氣缸的排氣倒流增加了這個氣缸中的殘余廢氣。最后,進入氣缸內的空氣量不會增加。此外,高溫殘余廢氣增加,壓縮行程缸內溫度升高導致敲缸現象(圖9~10)。圖9中,ηvb定義為修正到環境溫度和壓力條件下的容積效率。該值對應于節流閥全開無增壓的容積效率。
為避免此種現象,豐田汽車公司在8AR-FTS發動機上采用了雙渦道渦輪增壓器,降低了進排氣門重疊期間相鄰氣缸的排氣倒流。然而,因封裝和生產限制,當前的8NR-FTS發動機采用單渦道渦輪增壓器。通過減小排氣凸輪作用持續角,從而減小進排氣重疊角度和倒流脈沖(圖11)。圖12為改變排氣持續角前后,基于模擬和發動機實際運行的容積效率ηv 和ηvb的驗證結果。結果顯示,排氣持續角減小時,殘余廢氣量減少,進氣量增加。
發動機燃油對機油的稀釋可能導致低速早燃(LSPI)。為減小燃油稀釋量,在各個進氣和壓縮行程進行3次噴油(圖13)。對噴油正時進行了調整,避免了燃油與進氣門和氣缸內壁接觸和附壁。這項措施有效地消除了早燃,將其發生的頻率降低到對活塞和活塞環無損壞的程度。
相比之下,在發動機高速下提高增壓壓力具有折中效果。較大背壓和大量的殘余廢氣導致敲缸現象,從而使點火正時延遲,排氣溫度較高。因此,基于渦輪進口燃氣的溫度限制,需減少燃油噴射量來降低排氣溫度。與傳統催化器相比,將催化劑載體的孔間壁厚減小1/3,以降低背壓。此外,催化劑載體的強度提升,形成了六邊形催化器。這些措施確保了排放物的轉化性能。
采取的其他措施包括集成排氣歧管的缸蓋(圖14)、排氣冷卻、降低背壓、減少殘余廢氣,以及擴展過量空氣系數(λ)=1燃燒區域等。集成排氣歧管的氣缸結構緊湊,確保了每個氣道的均勻冷卻,并消除了倒流的影響。冷卻主要集中在弧形的排氣歧管,提高了排氣冷卻效率。同樣設計了較長的單獨排氣道,最大程度地提高渦輪增壓器效率。集成排氣歧管的冷卻設計得以優化,降低了發動機在高負荷工況的廢氣高溫。另一方面,發動機低速時排氣溫度相對較低,排氣和冷卻液之間的溫差變小,冷卻液流量減少。
圖15為全負荷特性。在轉速為1500r/min時就達到了低速最大扭矩185N·m,發動機最大功率85kW 時,λ=0.89。
4 燃油消耗
4.1 發動機測功機上的燃油消耗
燃油經濟性差的主要原因之一是發動機在低負荷工況的泵氣損失。為降低8AR-FTS發動機的泵氣損失,豐田汽車公司采用了帶有中間鎖止裝置的VVT-iW 系統,推遲進氣門關閉正時的阿特金森循環。
為提高發動機低負荷區域的燃油經濟性,8NRFTS發動機也采用了VVT-iW 系統。然而,受負重疊期的影響,僅進氣側的配氣相位移動,泵氣損失降幅不明顯。在負重疊期,泵氣損失或壓縮損失反而增高。可行對策也是推遲排氣門正時,加大重疊角。然而,為實現發動機低速大扭矩特性,發動機排氣持續角小,如果重疊角加大,排氣門開啟正時推遲遠離下止點,這增加了泵氣損失,惡化了燃油經濟性。
圖17示出了不同氣門正時和重疊角的燃油消耗變化。
圖17的等高線示出燃油經濟性的惡化過程(以百分比表示),最佳燃油經濟性對應的排氣持續角為240°CA。排氣門開啟角(EVO)置于30~35°CABBDC時,進排氣重疊角的作用以及膨脹比增大,使得燃油消耗得以改善(A線)。在A線和B線之間,僅進排氣重疊角提高了燃油經濟性。然而,為延長重疊期,將EVO置于BDC后(B線)時,壓縮行程泵氣損失增大,燃油經濟性惡化。因此,阿特金森循環對改善燃油經濟性效果并未完全實現。
在中等負荷下,背壓隨增壓壓力的增大而增加。換言之,增壓壓力提高會導致較高的泵氣損失。因此,為提高該運行區域的燃油經濟性,需將增壓壓力降低到最小,充足氣量的需求也要優化。通過調節進氣正時及盡可能靠近BDC關閉進氣門得以實現。基于以上原因及全負荷工況的持續性,發動機僅限于在極低負荷下應用阿特金森循環(圖18)。隨著負荷增加,進氣門關閉正時從晚關調整為早關,因此在整個工況范圍內達到了良好燃油經濟平衡性。由于VVT的設定值隨著容積效率波動必須有大的調整變化,采用VVT-iW系統可提高相位移動的速度。
通過燃燒方法也可提高燃油經濟性。在低、中和高負荷各區域,優化每一循環的噴油次數和噴油正時。為預防阿特金森循環低溫壓縮氣體條件下燃燒惡化,提高發動機低速或高負荷下的燃燒速度,將燃油調整到在壓縮行程進行噴射,在火花塞附近形成弱分層混合氣。在中等負荷下,由于下止點時的進氣流速減小,燃油靠近下止點處進行噴射,以提高缸內渦流并加速燃燒速度(圖19)。噴油正時的調節在熱機和冷機運行期間進行。尤其是在冷態工況下,通過增大弱分層混合氣區域改善燃燒(圖20)。
機械摩擦損失也大幅降低。采用偏置曲軸降低了活塞的摩擦損失,提高了有效熱效率。在進排氣門周圍采用了較細的搖臂、較小的氣門彈簧座、蜂窩形氣門彈簧和中空充鈉排氣門,減小了慣性質量和氣門彈簧的負荷。其他的減摩措施包括采用防滑正時鏈條、低摩擦材料的鏈條導輪、活塞裙部精細表面重整技術和低摩擦曲軸油封,優化發動機各部分的潤滑油分配、采用高效率的泵齒形線。采用新研發的高強度連桿材料,可以減小往復慣性質量,從而可以采用輕量化曲軸。
圖21示出發動機整個工況范圍內的燃油消耗率和λ。最小燃油消耗率為236g/(kW·h)(有效熱效率:36.2%)。集成排氣歧管的缸蓋的部分作用是使λ=1的燃燒區域擴展到190km/h(最大速度195km/h),幾乎整個發動機運行區域的燃燒都處于化學計量比的燃燒。
4.2 起停控制策略
在車輛停止時為使發動機停車后重起,開發了基于第一壓縮氣缸的分層噴射和燃燒的重起控制策略。該控制策略已經用于8AR-FTS發動機。與傳統的氣道噴射發動機重起控制相比,該系統旨在更快重起發動機,并通過限制發動機轉速沖擊實現平穩重起。
與傳統氣道噴射控制方式相同,為增加缸內進氣量,發動機停機前立即打開節氣門。利用缸內壓縮氣體壓力的回彈作用將活塞控制在BTDC90°CA附近停止。重起時,起動機驅動曲軸轉動,在壓縮行程上止點前進行噴射。火花塞周圍形成易燃混合氣,點火時刻推遲。如圖22所示,采用這種噴射控制,發動機重起時間比傳統氣道噴射方式快大約200ms。
大幅推遲點火時刻同樣可以控制扭矩的升高率,從而限制發動機轉速沖擊。因此,需要較低的制動保持壓力,實現無沖擊平順重起。
4.3 熱管理
為提高暖機過程的燃油經濟性,通過CAE優化了發動機、CVT和車內加熱器(空調)的冷卻液流量。在暖機期間,為確保車內的舒適性,并通過降低發動機摩擦損失提高燃油經濟性,熱量分布優先考慮發動機和空調。此外,發動機機體內部的結構可以使機油和冷卻液之間進行熱交換。暖機期間,熱量從冷卻液傳遞到機油,會提高每個摩擦副的溫度。相反,在高溫和高負荷工況下,熱量從機油傳遞到冷卻液,具有冷卻機油的效果,免除了安裝機油冷卻器的需求。
新開發的8NR-FTS發動機也采用了一些8ARFTS發動機所采用的技術。在冷機條件下,溫控系統通過減小機體冷卻液流量促進機體溫度上升,并通過系統暫停活塞冷卻噴嘴工作,中斷活塞冷卻機油供給,根據駕駛工況調整機油流量,防止對活塞和活塞環的過度冷卻,減小活塞及活塞環與缸套的滑動摩擦。集成排氣歧管的氣缸蓋也回收排氣熱量,加快冷卻液溫度的上升,提高氣缸及其他部件的溫度。這些技術措施有助于改善燃油經濟性(圖23)。
與先前的自然吸氣1.8L發動機相比,基于發動機的燃油經濟性改善、改進的起停控制、熱管理系統,通過提高低速扭矩實現的發動機轉速下降,以及交流電機和電池優化的充電/放電控制,在新歐洲行駛循環(NEDC)工況下的車輛燃油經濟性提高約25%。
5 冷起動燃燒特性的改善
該發動機不使用氣道噴射,在極其寒冷的溫度下,燃油霧化和油氣混合氣便成為一大問題。通過使用類似于改善發動機燃油經濟性的多次噴射策略,解決了這個問題。圖24為極寒溫度下發動機起動時多次噴射的示意圖。進氣行程每一噴射使燃燒室內形成稀混合氣,壓縮行程進行噴射在火花塞周圍形成可燃混合氣。進氣行程分次噴射限制了噴霧長度,減小了氣缸壁上的燃油附壁量。因此,與傳統氣道噴射發動機相比,該發動機在極低溫條件下的起動時間更短。
6 車輛動態特性
6.1 低速響應
為改善車輛的動態特性,在提高發動機全負荷特性的同時,減小渦輪增壓器遲滯期也是重要的。
8NR-FTS的開發目標是實現快速的瞬態響應特性,最小化包括中冷器在內的進氣系統的體積,并降低進氣壓力損失。穩壓腔的容積減小到1.1L,單位排量穩壓腔容積是豐田汽車中最小的。中冷系統為水冷設計,最小化了渦輪增壓后的進氣系統容積。中冷器采用了獨立于發動機冷卻系統的低溫冷卻回路,而且采用1個電動水泵。冷卻回路控制冷卻液流量,根據發動機運行工況保持最佳冷卻效果,最小化了水泵的功耗。中冷器采用獨立于發動機冷卻系統的低溫冷卻回路。為提高冷卻效率,改進了中冷器的內部結構,在水路側增加了翅片,并優化了增壓氣體側的翅片和通道形狀(圖25)。
通過這些控制同樣可以提高動態性能。除WGV控制外,還進行了掃氣控制,暫時將氣門重疊角增大超過常規設置,以提高增壓壓力,使其大于背壓。進入渦輪的氣體增加,保證了增壓壓力。如圖26所示,掃氣控制縮短了渦輪遲滯期。
6.2 發動機與CVT匹配開發
該渦輪增壓發動機的主要特征之一是能夠與CVT進行匹配。首先,研究了最佳CVT換檔控制及其與渦輪增壓發動機的匹配開發。圖27示出節氣門全開(WOT)時從30km/h開始加速的條件下,2種換檔控制的車輛縱向加速度曲線(G)。曲線A為發動機轉速快速提高的加速度數據。曲線B為控制發動機轉速提高的加速度數據。曲線C為同樣條件下加裝手動變速器的車輛加速度數據。曲線A中,加速度初始保持穩定,然后減小,之后突然增大。曲線B中,加速度實現了與手動變速器車輛相同的線性提升。
圖28示出在圖27中的數據條件下,每循環的容積效率隨發動機轉速的變化。曲線A,進氣流量突然增加前,轉速達到約4000r/min,容積效率實際并無提升。這是因為如果發動機轉速與自然吸氣發動機以同樣的方式快速提高,增壓提升率與進氣量升高率相抵。因此,每燃燒循環的容積效率并不增加。此外,隨換檔慣性損失增加,開始出現降速。相比之下,曲線B示出增壓壓力線性響應提升,通過CVT極其靈活的換檔控制性能控制發動機轉速提升量和提升率。此外,控制發動機轉速提高率也最小化了換檔慣性損失,實現了加速度的線性增加,有助于降低CVT所謂的加速滯后感。因此,該渦輪增壓發動機與CVT的匹配使CVT換檔控制優化了增壓壓力響應和驅動力響應。
圖29示出采用CVT和手動變速器從40km/h開始的加速度曲線。盡管換檔期間慣性損失量使采用CVT時的加速提升稍有延遲,但車輛的加速感覺與駕駛員的意圖相一致,這也是CVT的主要特點之一。在逐步加速工況下,隨駕駛員的操作(油門下壓量和速度)優化換檔控制(即換檔量和速度),CVT實現了與手動變速器相同的線性加速度,在快速加速下達到了加速度的線性和最大值響應。平穩加速,駕駛員不會感到渦輪增壓器遲滯。
圖30示出裝配雙離合器變速器(DCT)或CVT車輛從停止開始加速的車輛縱向加速度G 曲線。DCT總傳動比小10%。離合器嚙合導致DCT起動響應延遲,而CVT因變矩器具有扭矩的放大功能,擁有更好的初始起動性能。此外,盡管變矩器損失使中間區域的加速度稍低于DCT,但其扭矩放大作用使CVT幾乎與總傳動比較小的DCT具有同樣的峰值加速度。鑒于綜合加速特性,采用CVT能實現平穩的線性感受。
除常規運行模式外,CVT還配有運動模式。如上所述,常規模式下,CVT憑借其高的低速扭矩實現線性加速。運動模式下,通過換檔控制改變發動機扭矩改善加速響應,實現非常快速的加速響應(圖31),如此快速的加速響應也通過提高增壓壓力實現。這是通過提高鎖止期間的發動機轉速、增加給定油門位置的發動機扭矩需求實現。此外,為改善增壓壓力響應而提高發動機轉速,換檔控制較常規模式執行更快,進一步增強了加速響應。通過這些措施,運動模式實現了更為直接的加速感受,使車輛駕駛更具樂趣。
7 結語
本文描述了豐田新型1.2L小型化渦輪增壓ESTECD-4T(8NR-FTS)發動機的硬件和軟件特性。該發動機的主要特征總結如下:
(1)通過增強進氣流動和缸內渦流,采用每循環多次噴油策略,在無氣道噴射的情況下發動機實現了快速燃燒。
(2)采用單渦道渦輪增壓器、較小的排氣持續角和掃氣控制,發動機從1500r/min開始就達到了最大扭矩。
(3)通過冷卻集成排氣歧管氣缸蓋內的廢氣,λ=1區域得以擴展。
(4)通過在壓縮行程缸內直噴使發動機立即平順重起的起停控制、改善發動機燃燒特性,以及采用高速比的換檔控制等,實現了頂級車輛的燃油經濟性。
(5)總之,該渦輪增壓發動機與最佳CVT換檔控制相結合,最小化了加速滯后感,實現了新的令人興奮的動態性能和出色的燃油經濟性。
-
機械
+關注
關注
8文章
1593瀏覽量
40647 -
汽油機
+關注
關注
0文章
58瀏覽量
11557 -
渦輪增壓器
+關注
關注
3文章
90瀏覽量
11709
發布評論請先 登錄
相關推薦
揭秘豐田最高熱效率的汽油機
關于4缸兩級渦輪增壓直噴式柴油機性能介紹
關于3缸1.0L增壓燃油分層噴射汽油機性能分析
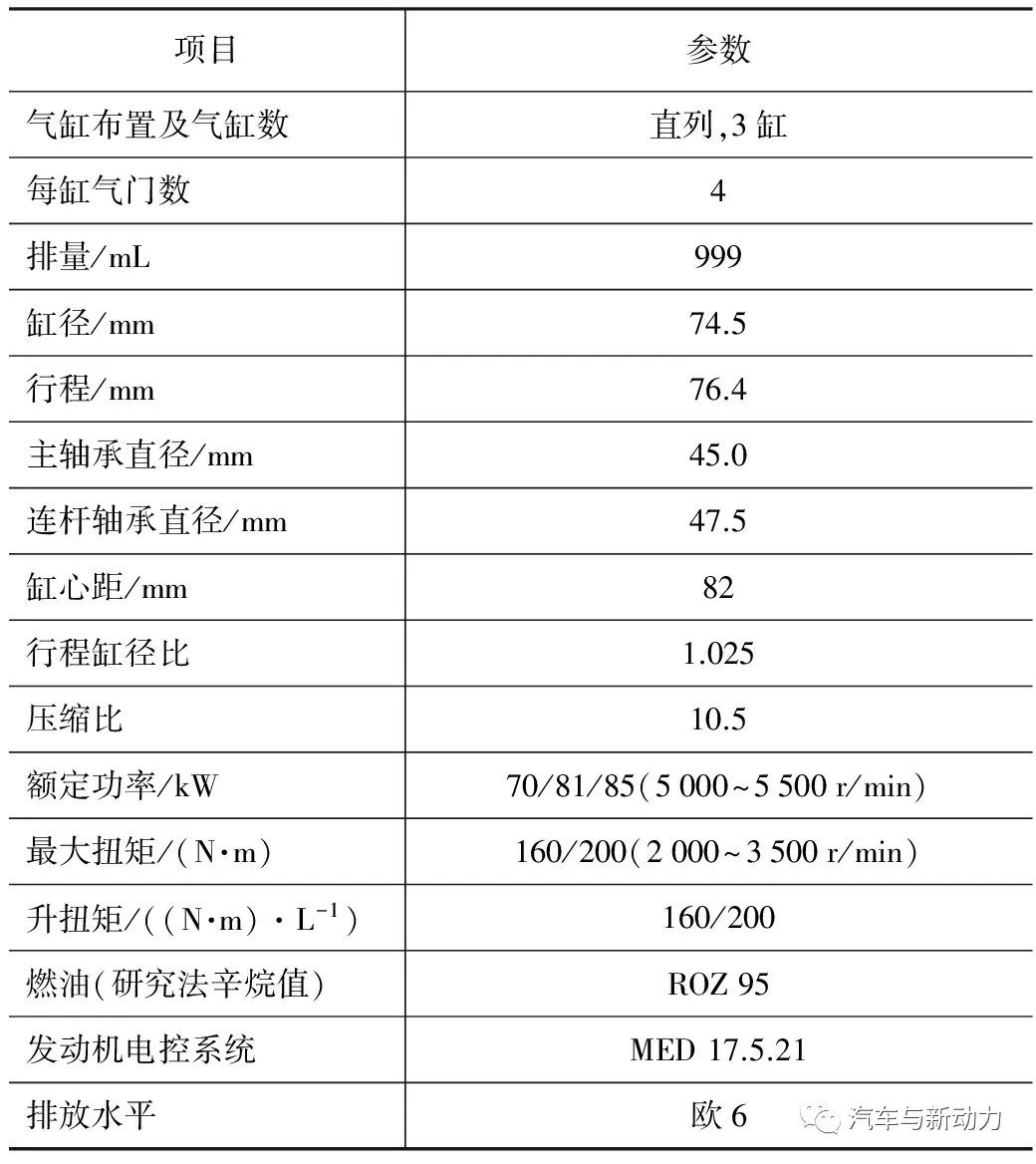
關于Volkswagen新型4缸1.5 L-TSI增壓直噴式汽油機性能分析
關于直列6缸直噴式汽油機性能分析
關于Mercedes-Benz1.8L渦輪增壓汽油機性能分析
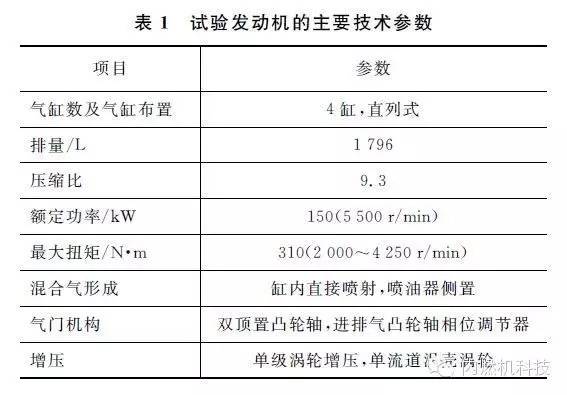
關于歐6直噴汽油機性能分析和可行性解決方案評價
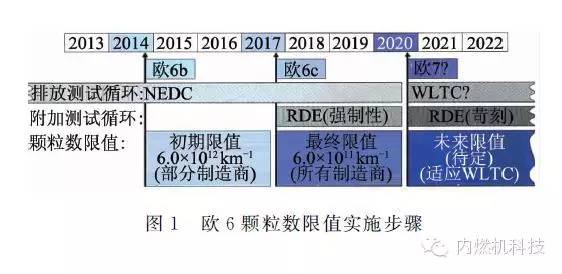
關于Volkswagen3缸1.0 L-TSI汽油機性能分析
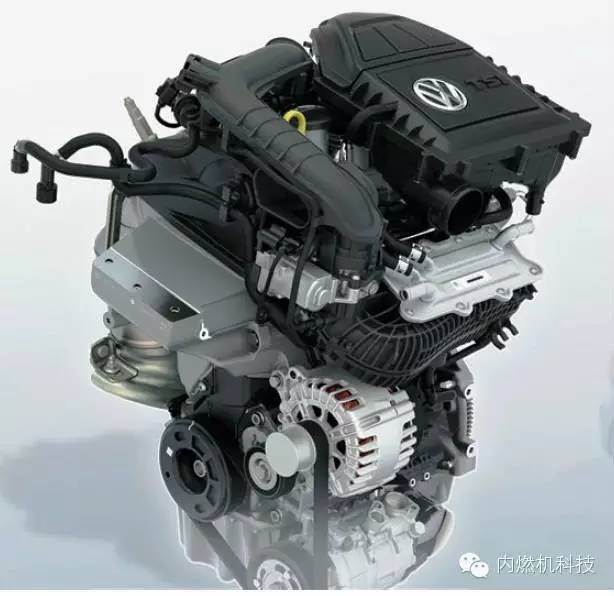
評論