Volvo汽車公司將一種可全球使用的全新4缸發動機系列及結構型式投放市場。該系列中的汽油機和柴油機具有相同的缸心距、缸徑和行程,它們的共同特點是明顯的小型化、進一步的模塊化、高升功率和低燃油耗。以往,Volvo公司采用4缸、5缸、6缸和8缸發動機,現在4缸以上機型已基本被取消。
1 高功率和低燃油耗
2013年秋季,Volvo汽車公司推出新型發動機系列,該系列以名為“Volvo發動機結構(VEA)”的新型結構型式為基礎,主要特點是高升功率和低燃油耗。此外,持續改進的模塊化結構和緊湊的動力總成外形為Volvo汽車公司的技術提供了新的自由度,該公司在底盤開發、前置發動機車型方案和被動安全等方面一直占據領先地位。VEA系列有8種機型,其中3種已于2013年秋季上市。
Volvo汽車公司的VEA系列機型以新穎的方式利用模塊化組合部件的原理。所有的汽油機和柴油機都具有相同的缸心距、缸徑和行程,排量均為2.0 L(圖1)。這些發動機在瑞典舍夫德的Volvo發動機工廠同一條流水線上生產。嚴格的模塊化原理使結構配置高柔性地適應不同發動機各自的市場需求,并使中等規模的汽車制造商能夠經濟合理地組織生產,降低生產成本。
圖1 Volvo汽車公司的汽油機平臺和柴油機平臺(圖中的模糊圖像表示發動機尚未投放市場)
VEA系列動力總成僅涉及4缸機型,因而只需較小的安裝空間,對前置發動機車型的裝配具有眾多有利效果。由于發動機機艙相對較小,為較昂貴的前艙懸置解決方案取得了空間。此外,還允許采用較短的前懸掛,簡化汽車碰撞時的安全管理。
由于對增壓系統、燃燒系統和噴油系統進行了深入開發,VEA系列的頂級機型達到或超過傳統5缸和6缸機的功率水平。圖2所示新型T6汽油機以高升功率挑戰當今最高等級的動力驅動裝置(圖3),并且十分重視降低燃油耗。通過降低摩擦功率和流動損失,以及應用高效增壓、高熱效率和高效的熱管理技術,使發動機在冷起動后快速預熱,同時,配備有效的排氣后處理系統,最終達到了上述目標。
VEA系列中的首批3種機型已于2013年秋季上市,分別是T5汽油機、T6汽油機和D4柴油機,其他功率機型也將逐步投放市場.
圖2 新型T6直接噴射汽油機
圖3 T6、T5汽油機和D4柴油機與競爭機型的升功率比較
2 基礎發動機的模塊化
VEA系列機型具有統一的基本結構,這是持續不斷模塊化的基礎,所有汽油機和柴油機都具有相同的排量,并被分成2組功率等級。第1組功率等級包括高功率機型和中等功率機型,而柴油機強勁的最高燃燒壓力則決定了發動機的外形尺寸。
第2組功率等級包括功率較小而燃油效率較高的機型,功率較小的柴油機最高燃燒壓力降低到14 MPa,接近汽油機的水平。汽油機和柴油機的許多零部件均相同,例如曲軸、主軸承蓋框架底座、機油泵、油底殼、輔助設備傳動、發電機和空調壓縮機等,其余零部件則具有高度的共通性,例如氣缸體曲軸箱和平衡軸模塊。
3 輕型結構方案
無論是柴油機,還是汽油機,都具有壓鑄鋁氣缸體曲軸箱和主軸承蓋框架底座(圖4)。主軸承蓋加強鑲鑄件采用球墨鑄鐵件,氣缸套采用灰鑄鐵制成。柴油機除具有較高的結構高度和尺寸加強的氣缸套外,其氣缸體曲軸箱基本與汽油機的相同。鑲鑄氣缸套的外表面噴涂共晶鋁涂層,能夠與壓鑄鋁氣缸體曲軸箱良好結合,相比通常采用表面粗糙工藝的鑲鑄件更為牢固,可改善氣缸的圓度,減小活塞環的預張緊力。這種氣缸體曲軸箱的設計及其鑄造工藝在質量或強度方面都能獲得良好的效果。
圖4 氣缸體曲軸箱和主軸承蓋框架底座(氣缸套和主軸承蓋的鋁涂層具有與鋁鑄件良好結合的特性)
主軸承蓋框架底座采用2種不同設計,唯一差別在于主軸承直徑。主軸承蓋完全被鋁包圍,在高功率機型上,在鑲鑄前,其表面也要噴涂共晶鋁涂層。
4 低摩擦的曲柄連桿機構
為了縮小軸承尺寸,所有機型的曲軸都是模鍛件。高功率機型組與燃油耗優化機型組的主軸承直徑不同,以盡可能減少摩擦。主軸承蓋框架底座與氣缸體曲軸箱之間采用具有專利權的定位銷,可獲得更好的定位精確度,同時改善軸承的軸向同心度。
強勁的D5、D4柴油機使用相同的活塞,并帶有由機油冷卻的第1道活塞環槽鑲圈。采用高強度襯套縮小活塞銷直徑。由于D3、D2柴油機的最高燃燒壓力較低,允許使用具有較小壓縮高度的輕型活塞和較長的輕型連桿,以及較小的連桿小頭襯套直徑。輕型活塞能使慣性質量減輕20%,因而可取消平衡軸。汽油機機型具有相似的活塞,只因壓縮比不同而使活塞頂設計有所不同,活塞銷也較短。此外,汽油機和柴油機的活塞銷都涂覆類金剛石碳(DLC)涂層。
采用最先進的工藝技術,明顯降低活塞摩擦,其中涉及新的珩磨工藝規范,以及第1道活塞環采用基于真空的物理汽相沉積涂層,有助于降低約50%切向力。所有汽油機均具有統一的活塞環設計。油環由兩部分組成,其特點是減小環高度,并具有較小的環岸寬度(即刮油唇高度),以及圓周表面涂覆DLC涂層。柴油機的活塞環組也是統一的。
5 氣缸蓋和氣門機構
新型氣缸蓋的結構設計在很大程度上以Volvo汽車公司久經考驗的5缸機和6缸發動機為基礎,最重要的變化包括降低摩擦、提高升功率,以及開發通用件及用于汽油機和柴油機的共用接口。
由于汽油機的升功率較高,氣缸蓋必須能承受極大的熱負荷,因此選用AlSi7鋁合金材料,并對其進行T7熱處理。橫向流動冷卻方案提供了突出的恒定冷卻效果,這種冷卻方式也被用于柴油機機型。汽油機采用直接作用式氣門機構和具有DLC涂層的免維修機械式挺柱。進、排氣凸輪軸是可調的,其皮帶輪采用摩擦較小的滾動軸承。凸輪軸由灰鑄鐵制成,因為這種材料適用于與氣門挺柱之間的滑動接觸。
對柴油機的氣缸蓋結構及冷卻水套進行精心設計,可以承受19 MPa的最高燃燒壓力和較高的升功率。為了提高材料的強度和耐高溫極限,開發了一種鑄造過程中的熱處理新工藝,如采用冷的壓縮空氣有針對性地淬火,明顯改善材料的組織結構,使其樹枝狀晶體間距小于17 μm,這種材料規格被稱為“A317 T7”。柴油機采用滾輪搖臂、液力挺柱,以及質量輕且材料硬度高的裝配式鋼凸輪軸。凸輪軸軸承定位套處的定位銷確保加工和裝配時的精確定位,能進一步降低運轉時的摩擦。
6 采用可調式機油泵的潤滑系統
VEA系列機型采用相同的潤滑系統。機油泵可全調節工作,通過電磁閥,以轉速、負荷和機油溫度為參數調節機油壓力,確保在所有運行工況下都有足夠的機油供應。在低負荷運行工況下,活塞頂停止噴機油冷卻,以減少摩擦損失,降低燃油耗和有害物排放。必要時,機油泵提高機油壓力,并打開活塞機油冷卻噴嘴。機油濾清器對微小顆粒具有極高的過濾能力。即使在低負荷下,機油溫度也相對較高,因此降低了摩擦損失,并改善了曲軸箱的通風效果。
Volvo汽車公司為VEA系列發動機開發了一種易流動的0W20級潤滑機油,能明顯降低摩擦。由于這種機油中的灰分較少,因此有助于排氣后處理系統獲得緊湊的外形。
7 冷卻系統和溫度利用
汽油機與柴油機的冷卻系統有所不同。柴油機的散熱在全負荷時較多,而在部分負荷和暖機運轉時則較少。汽油機使用功率為400 W的電動水泵,減少了摩擦損失,并能改變冷卻液流量,使冷起動后的發動機能迅速達到正常運行溫度。
Volvo汽車公司在柴油機上應用機械式冷卻水泵,由氣動調節閥控制發動機快速預熱所需的冷卻液流量。為了確保在發動機暖機期間車廂內的采暖,由1個功率為15 W的小型電動水泵提供來自氣缸蓋冷卻循環回路的熱水。廢氣再循環(EGR)的冷卻水循環回路中同樣有1個功率為15 W的小型電動水泵,它經過冷卻器后的閥輸送冷卻液。為了使再循環廢氣達到較低的溫度,從而降低氮氧化物排放,按低溫水平設計EGR循環回路。
8 用于不同功率機型的模塊化增壓系統
由于氣缸排量是統一的,因而對于VEA系列機型的功率等級差異而言,增壓系統起決定性作用。由于對升功率的要求較高,因而按照最新的技術狀況(包括兩級增壓在內)來開發增壓系統,并分別應用于汽油機和柴油機(圖5)。新增壓系統最重要的特點是模塊化結構,所有功率等級的柴油機和汽油機增壓系統的安裝位置及發動機側接口都是相同的。這種設計方案使發動機配裝汽車時有統一的標準。
圖5 模塊化增壓系統是拓展功率等級的關鍵因素
為T5汽油機開發了一種帶廢氣渦輪增壓器的整體式鋼制排氣歧管,與鑄造排氣歧管相比,它具有較輕的質量和較小的熱慣性。T6汽油機的增壓系統采用機械驅動的羅茨壓氣機,向大尺寸的廢氣渦輪增壓器輸送增壓空氣。在低轉速時,羅茨壓氣機自動工作,從而獲得較大的扭矩,轉速隨增壓壓力的建立而提高后,廢氣渦輪增壓器開始工作,羅茨壓氣機則脫開停止工作。
D4柴油機匹配串聯式兩級廢氣渦輪增壓系統,Volvo汽車公司為此進一步開發了增壓技術,并于2008年首次用于2.4 L柴油機。這種優化的增壓系統與改進的燃燒過程協調配合,將升功率從66 kW提高到71 kW。2個渦輪增壓器中較小的增壓器能在低轉速時自發地建立增壓壓力。
9 燃燒室中央汽油直接噴射
汽油機的火花塞和噴油器被布置在燃燒室中央,其新穎的噴霧形成能產生非常均質的燃空混合氣。這種燃燒室中央汽油直接噴射方式能在發動機起動時形成分層充量,并實現最有效的催化轉化器預熱。采用這種噴油方式的VEA系列機型不僅性能超過進氣道噴射發動機,而且比噴油器側置的直接噴射汽油機更好,其優點是燃油耗低,并能滿足美國準零排放車(PZEV)的廢氣排放標準要求。
進氣道設計能在進氣行程的氣缸中形成空氣和燃油的滾流運動,而在壓縮行程,則由滾流運動產生充量擾動,提高燃燒速度,使燃燒更穩定,從而應用高EGR率降低泵吸損失和燃油耗。為了確保無爆震燃燒,在冷卻水套、進氣道、噴油嘴方向和燃燒室幾何形狀等方面進行全面優化。最終,T5汽油機采用10.8的高壓縮比,T6汽油機采用10.3的高壓縮比。
10 應用250 MPa噴油壓力和噴油量閉環控制技術的柴油機燃燒系統
VEA系列的柴油機采用全球最新的共軌噴油系統,將250 MPa最大噴油壓力與所謂“智能精度修正技術”的噴油量閉環控制技術相結合。該技術基于每次噴油過程在燃油系統中產生的壓力波,從該壓力波獲得精確的噴油時刻和噴油量信息。在每個噴油器中都有1個壓力傳感器和1個用于數據傳輸及存儲的芯片,發動機電控單元用這些數據計算實時噴油量,并進行相應調節。這一精確可靠的系統能使發動機獲得高升功率、低排放、低燃燒噪聲和高熱效率的性能,而且還能自動補償噴油器老化和磨損,從而使發動機在整個使用壽命期內穩定、可靠地運行。
圖6示出燃油壓力傳感器在噴油器中的位置,緊湊的電磁執行器被直接置于噴油嘴短針閥附近,它與壓電噴油器相似,能快速開啟或關閉噴油嘴針閥。該電磁閥能以極少的泄漏控制3/2伺服閥,因而能降低燃油泵消耗的功率和燃油耗。
圖6 帶燃油壓力傳感器和最高噴油壓力250 MPa的噴油器
同時,重新設計了發動機的進排氣道和燃燒室,以便與汽油機結構相匹配,并獲得模塊化接口。由于這種進排氣道具有優良的流動特性,因而排氣道相對較小,同時較大的進氣道又能利用較大的空間。活塞頂燃燒室凹坑被設計得寬而淺,以改善進氣效率,減少活塞熱損失,降低活塞熱負荷。出于升功率和升扭矩方面的高要求,最高氣缸壓力被提高到19 MPa,壓縮比被降低到15.8。
11 模塊化排氣后處理系統
按歐6b、美國超低排放車(ULEV)及PZEV廢氣排放標準設計的排氣后處理系統遵循汽油機和柴油機的模塊化原理。在所有機型上,渦輪出口和排氣后處理系統部件的進口都位于相同位置。氧化催化轉化器被設計得非常緊湊,第1個載體芯子位于廢氣渦輪增壓器出口后,第2個載體芯子則旋轉90°布置(圖7),2個芯子之間無需管道。這種專利布置型式具有極低的流動損失,而且在第2個芯子中能獲得均勻的流動分布。總之,這種氧化催化轉化器能確保響應時間短,以及有害物的高效凈化。
圖7 模塊化的排氣后處理系統具有較低的壓力損失和均勻的流動過程
用于汽油機的三效氧化催化轉化器第1個芯子體積為1.5 L,而體積為1.0 L的第2個芯子僅用于美國排放標準方案。與ULEV排放標準相比,PZEV排放標準方案的涂層必須具有較高的貴金屬含量。在柴油機上,則采用1.5 L的存儲式氮氧化物催化轉化器與2.5 L柴油機顆粒捕集器相組合的方案。
12 運行性能、功率和扭矩
VEA系列首批3種機型的功率和扭矩特性曲線示于圖8,為了進行比較,圖中還示出傳統5缸增壓發動機的特性曲線。T6汽油機在低轉速時具有極大的扭矩,在整個轉速范圍內,其扭矩特性曲線全面超越5缸2.5 L I5P增壓汽油機,考慮到其排量減小25%,T6汽油機已進入市場上的頂級機型領域。T5汽油機在1 500 r/min低轉速時也能提供大扭矩,其扭矩特性曲線與5缸發動機的極為接近。
圖8 新型T6、T5汽油機及D4柴油機與傳統5缸2.5 I5P及2.0 L I5D發動機的功率和扭矩比較
與傳統單級渦輪增壓5缸發動機相比,新型D4柴油機在低轉速時的扭矩和功率特性曲線相似,D4柴油機的扭矩建立更快,但最大扭矩要在略高轉速下才能達到。較大的差別是在高轉速區域,從發動機轉速3 000 r/min起,新型4缸機的低壓渦輪就承擔起建立增壓壓力的任務,因而能夠提供大扭矩和高功率。
13 低燃油耗
在VEA系列機型的整個開發過程中,十分注重降低燃油耗。為此,除發動機小型化外,主要將精力集中于改進整機結構。圖9示出發動機摩擦特性。D4柴油機摩擦特性處于FEV分布帶的下端,而帶有小軸承和低摩擦活塞的較小功率機型摩擦甚至更低。T6、T5汽油機和D4柴油機配裝于S60轎車后,其CO2排放量示于圖10,其中,與競爭機型的比較是按汽車整備質量考慮的。
圖9 新型T6、T5汽油機和D4柴油機的摩擦與FEV分布帶的比較(Stripp法、無燃燒)
圖10 Volvo汽車公司S60轎車(汽車整備質量)的新歐洲行駛循環CO2排放量
14 結語
Volvo汽車公司成功開發了一種具有模塊化結構的新型發動機系列,該發動機平臺由2種功率組的4缸2.0 L發動機組成,通過增壓技術實現了寬廣的功率跨度,包括帶廢氣放氣閥的渦輪增壓器和先進的兩級增壓系統。針對汽油機和柴油機的燃燒過程,按各自的功率水平進行精確調整,降低了燃油耗和廢氣排放。作為新發動機系列的首批機型,T6、T5汽油機和D4柴油機已投放市場。T6高功率汽油機的升功率達到同類機型的頂級水平。由于摩擦較低,以及新開發的熱力學性能,所有機型的燃油耗都達到競爭機型中的最佳水平。新發動機系列的緊湊外形和標準安裝位置為汽車在安全性、底盤開發和前置發動機車型設計等方面開辟了新的空間。
-
發動機
+關注
關注
33文章
2495瀏覽量
69533 -
功率
+關注
關注
14文章
2071瀏覽量
69970 -
模塊化
+關注
關注
0文章
332瀏覽量
21404 -
柴油機
+關注
關注
1文章
173瀏覽量
26307
發布評論請先 登錄
相關推薦
第五屆中國汽車發動機現代技術論壇(11月,上海)
發動機停缸控制及其標定
電噴發動機轉速傳感器信號波形試驗
CA1261汽車發動機懸置系統隔振的研究
【Embedded Pi申請】汽車發動機電子模塊開發
汽車發動機升級產品解決汽車發動機燃燒問題。
發動機的振動檢測
TJ7101型轎車1L排量的新型發動機的組成部分
發動機總成包含哪些部件_發動機總成包括什么_發動機總成圖解
汽車發動機構造是怎么樣的?汽車發動機如何維修20個詳細案例分析
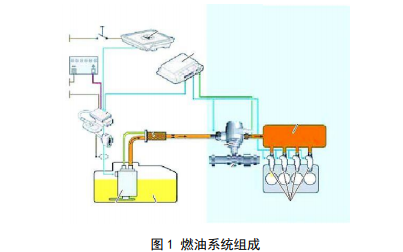
評論