5G時代到來,汽車生產制造也在改變。2019年,奇瑞捷豹路虎和中國聯通共同宣布,雙方在5G技術包括網絡技術研究、應用研究和通信服務與企業信息化等方面將展開合作,這標志著奇瑞捷豹路虎的“智能制造”將進一步升級。
在5G網絡的加持下,奇瑞捷豹路虎將打通能源管理系統NB-IOT等領域技術融合的網絡解決方案,實現實時掌控企業能源使用情況及計算單車能耗;在基礎數據服務中,發揮5G網絡高帶寬、低延時以及上下行高速率等方面的優勢,并將其應用到虛擬裝配項目中,結合MR混合現實技術實現3D裝配模擬場景。這句話比較難理解,簡單來說就是,5G提升了奇瑞捷豹路虎生產制造的控制能力,而且可以對奇瑞捷豹路虎未來的精細化管理提供非常大的支持。
放眼長遠,你才能更好地理解為什么說5G就是奇瑞捷豹路虎實現“智能+”的催化劑。從行業角度來看,與其他制造業不同,汽車的生產是一套復雜的系統工程,數以萬計的細小零件需要經過多條生產線組裝成整車出廠。如果是基于傳統制造業技術,能夠對整條生產線施加影響的手段還比較匱乏。
從工廠角度來看,基于互聯網技術的支持,汽車制造是以智能工廠為載體,以關鍵制造環節的智能化為核心,以端到端數據流為基礎,以通信網絡為基礎支撐。通過自組織的柔性制造系統,奇瑞捷豹路虎已經可以實現高效的個性化生產的目標。而在互聯網技術中更先進的5G,一旦介入必然會給造車帶來更高的支持。
現階段的準備是否充足,直接決定了未來能否在這條賽道取得桿位和速度優勢。面對5G這一藍海,有洞察的車企早已進入“預備”動作,而作為首家中英合資的車企,奇瑞捷豹路虎在公司成立之初便做出前瞻性布局,通過SAP、MES、LES三大核心系統的建設,打造了研發——生產——物流的信息聯通和覆蓋的高度智能化造車體系。
奇瑞捷豹路虎的二期工廠,更是集合最先進的技術,讓其成為全球最先進的汽車制造工廠之一,奇瑞捷豹路虎在智能制造方面的前瞻性布局使其持續引領行業發展,為5G時代的繼續領先中積蘊了能量。這一點,在常熟二期工廠得到了充分體現。
二期工廠有什么特色呢?它不僅延續了一期工廠的品質智造能力,同時又將工業互聯網充分融入到全生產周期中。通過打通物聯網,實現了在云端建立大腦來控制和協調制造過程。在2017年,趁著二期工廠建設,奇瑞捷豹路虎對整個生產制造體系進行了升級,其圍繞全價值鏈業務流程整合、ABC-AI/Big data/Cloud為基礎的數字化智能工廠、智能供應鏈、3D/AR技術為核心的虛擬化工廠四個部分進行數字化轉型,為中國汽車工業在智能制造領域輸入了全新概念。
這些概念比較難以理解,實際一點來說,就是提升了裝配效率和產品品質。汽車的質量是由部件質量和整體質量兩個關鍵指標組成,傳統制造業技術,很難實現對部件質量問題的逆向追溯。因此,掌握生產自動化、質量控制體系以及安全生產的技術就掌握了汽車制造業的核心技術。目前國內汽車制造業,研發、生產、測試等環節,信息的填報仍主要依賴于技師的經驗和技術,工作效率低,生產過程中收集的數據并不精確,造成質量隱患和安全隱患。而智能制造則能填補這些缺陷。那么,奇瑞捷豹路虎是如何運用“智能手段”來提升產品品質,實現產品可靠性的提升呢?
作為捷豹路虎首個英國本土以外的整車制造工廠。奇瑞捷豹路虎常熟工廠在建設初期就確立了要建設成為中國最先進的制造廠,工廠采用世界一流的設計理念,建成全球領先的沖壓、焊裝、涂裝、總裝車間、發動機工廠、研發中心以及質量中心。不僅采用與捷豹路虎全球一致的操作系統和質量評價標準,也引入了與捷豹路虎全球統一的采購和供應商管理標準,包括采用一致供應商體系標準,一致的高品質供應商篩選系統和一致的供應商質量標準平臺。
因為建立時間相對晚,因此也更具互聯網時代的特性。比如,工廠的高度自動化特點:焊裝擴建車間自動化率達到100%,全鋁車身車間鉚接自動化率達到100%。在具體設備方面,總裝二車間新增了電池模塊AGV自動運輸合裝設備,總裝車間采用了全自動天窗安裝機器人,安裝用時不超過3分鐘。可以說,奇瑞捷豹路虎常熟工廠是目前中國生產自動化率最高的工廠之一。
再比如,常熟工廠的柔性化生產:作為一家共線生產兩個豪華品牌的企業,奇瑞捷豹路虎以模塊化設計為基礎進行柔性制造,可以處理30萬種個性化選裝配置的汽車。當然,作為柔性化生產的支持,物料準備系統也非常智能。工廠對物料標識、物流信息采集、貨物實時監控等智能倉儲流程,以及物料智能分揀系統、配送路徑規劃、配送狀態跟蹤等都進行了智能化改造。比如第二總裝車間的物流區域中,已經全面使用車載或手持終端進行輔助物料拉動,并采用語音揀選系統,確保物料出庫準確率。它還可以實時掌握包括運輸船位置、船上貨物、到岸時間、報關清關進度等在內的信息,及時有效地拉動整個供應鏈。
另外,奇瑞捷豹路虎常熟工廠也實現了高度物數字化,設備普遍“連接”。常熟工廠的整車自動化設備連接率達到86%,發動機工廠達到100%。如上文所講,常熟工廠大面積使用物聯網系統,在焊裝、涂裝、總裝工藝、發動機工廠以及物流等流程中,均利用超高頻無線射頻識別系統RFID及讀寫設備,實現全流程生產過程控制及追蹤,并上傳追蹤數據,建起了覆蓋全產品生命周期和制造全業務活動的工業大數據平臺。在物料配送上,也都是系統自動分配,并采用AGV小車自動拉動。在造車過程中,工作人員可以精確追溯每一臺車的生產制造數據,并實現對售后數據的持續跟蹤與分析,做到對每一款產品負責。總而言之,就是每一個環節都可以追溯和在線監控,并可以通過遠端收集數據和遠程控制。
高度智能化的造車技術固然能提升裝配效率和產品品質,但卓越的品控管理才能帶來絕對保障。在生產過程中,奇瑞捷豹路虎對每個環節都嚴格把關,將智能科技與工人經驗相結合,形成了一套完備的制造體系。在沖壓、焊裝、涂裝和總裝這汽車制造的四大生產工藝流程中,奇瑞捷豹路虎都有線上和線下兩種檢測方式同時交叉檢測,確保產品的品質,保證生產的一致性。在大面積生產中,一致性是衡量產品品質的關鍵指標。要做到這個,奇瑞捷豹路虎使用了很多高科技武器。
線上的檢測就分多種方式,我們以焊裝車間為例。奇瑞捷豹路虎的焊裝車間采用100%線上檢測和密集的線下檢測來保證焊接的質量。焊裝車間的線上檢測運用世界級激光定位設備和攝像技術,該工藝精確到0.2毫米。除了激光在線檢測,焊裝車間還使用了Calipri非接觸間隙面差測量,這可以完整精確地測量任何縫隙輪廓和物體輪廓,測量精度達到0.05mm,每個測點的總測量時間小于5秒,快速高效。
線下檢測則更為多樣,包括采用DEA BRAVO懸臂三坐標測量機、Leica激光跟蹤儀、Romer關節臂、Gap-Gun 、GOM藍光掃描設備、激光雷達等計量設備。三坐標儀檢測是奇瑞捷豹路虎質檢中的特色,通過每天會進行對產品的抽檢,利用鉸接式探針探測到各個有角的位置,進行光學測量或直接使用計算機輔助設計數據輸入到計算機系統中進行測量,確保所有部件尺寸精確和完美匹配。
另外,車間還會在每天對每班次生產的白車身各大總成抽檢一輛份進行測量及監控,檢測范圍為每臺車身的4000多個焊點。其中,激光雷達自動測量是航空航天工業測量技術手段,奇瑞捷豹路虎也是國內首家主機廠應用這個技術。而高頻次線下檢測和100%的線上檢測使得車輛在焊接上做到萬無一失,保證車身的結構穩定性。為了確保所有的產品電氣的可靠性,奇瑞捷豹路虎升級了整車VCATS電檢系統,可以有效覆蓋所有的電氣功能檢測項目,從電氣電路檢查到實車操控檢驗。
由于工業互聯網的使用,在奇瑞捷豹路虎生產過程中,小到每個電器模塊的零件號都會在生產過程中受到監控。通過標準零件號(以數據形式存儲在云端)進行對比,檢查模塊是否裝錯,并反復確認其精度和品質。在總裝車間下線后,車輛還會進行全面質量檢測,包括油漆、鈑金、內外飾、功能、淋雨、路試等,確保產品品質。
在質量中心奇瑞捷豹路虎有一套“全質全能”的系統。這包括20分鐘的靜態淋雨測試;模擬各種環境的振動臺加環境倉,可以測試從零下30攝氏度到80攝氏度環境測試和振動程序以模擬世界上最嚴酷的道路狀況,并測評來自車輛本身的聲音和異響。在模擬倉中,產品的冷卻系統、報警系統、臺架自動調節系統、路譜數采儀等設備單元都被全面檢測一遍。
智能制造的最重要的目標是通過基于物聯網的信息技術,來規范和控制整個制造流程。而奇瑞捷豹路虎在5G戰略合作的支持下,必然能進一步深化“智能制造”的高質量發展方式,引領中國高端汽車制造業的前進方向。
-
智能化
+關注
關注
15文章
4897瀏覽量
55447 -
智能制造
+關注
關注
48文章
5570瀏覽量
76372 -
5G網絡
+關注
關注
8文章
1741瀏覽量
42390
發布評論請先 登錄
相關推薦
捷豹路虎斥資5億英鎊助力Halewood工廠轉型純電動車生產
英特爾將進一步分離芯片制造和設計業務
捷豹路虎加大投資應對電動汽車轉型放緩
西門子與微軟進一步擴展戰略合作關系
進一步解讀英偉達 Blackwell 架構、NVlink及GB200 超級芯片
卓馭科技與高通合作宣布進一步推動汽車行業智能駕駛技術的發展
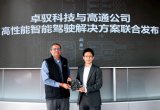
路虎攬勝純電版在北極圈測試,展示無偽裝制造質量
Cognizant 將延續與 Pon IT 的合作,旨在進一步管理和優化云服務
Arbe在中國上海設立分公司,進一步增強企業影響力
英飛凌重組銷售與營銷組織,進一步提升以客戶為中心的服務及領先的應用支持能力
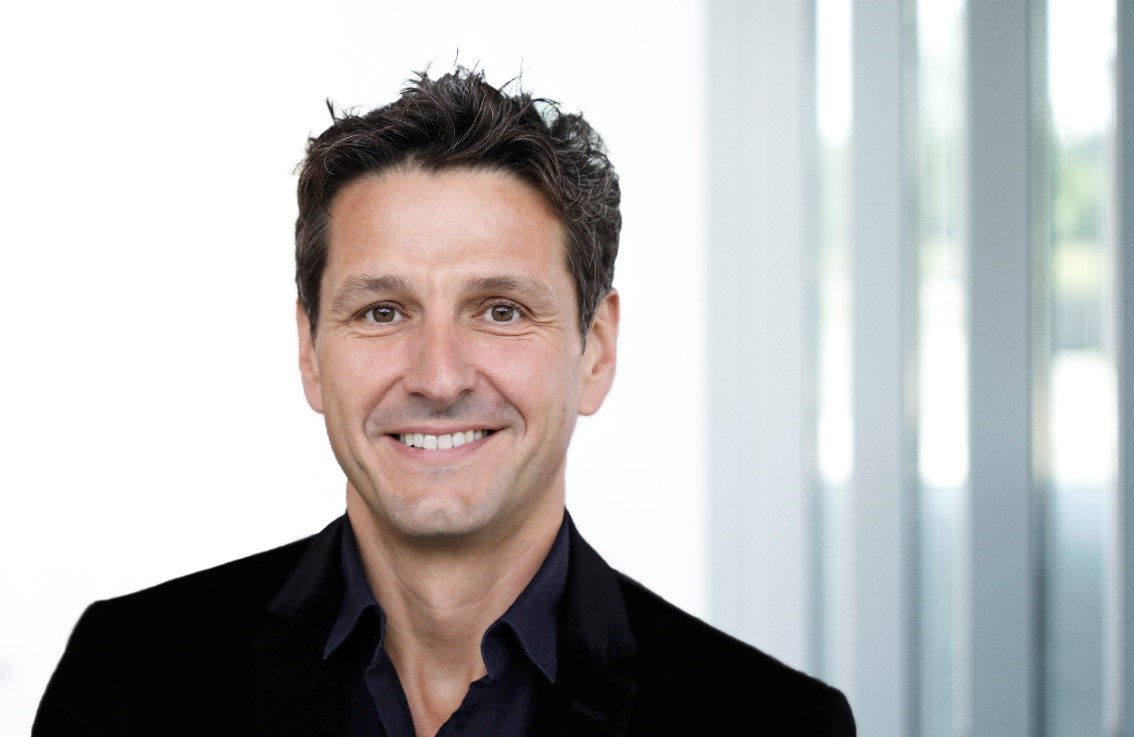
評論