(文章來源:汽車總站)
鋰離子電池發生的起火燃燒事故,主要是電動汽車不合理的使用,造成電池化學能量瞬間轉換成熱能,造成電池內部熱失控和熱失控擴散,使電解液的有機溶劑在大量熱的作用下分解并蒸發,可形成易燃性混合物,遇火源引起整車燃燒爆炸。
熱失控(Thermal runaway)是指由于鋰離子液態電池在外部高溫、內部短路,電池包進水或者電池在大電流充放電各種外部和內部誘因的作用下,導致電池內部的正、負極自身發熱,或者直接短路,觸發“熱引發”,熱量無法擴散,溫度逐步上升,電池中負極表面的SEI(Solid Electrolyte Interface)膜、電解液、正負極等在高溫下發生一系列熱失控反應(熱分解)。直到某一溫度點,溫度和內部壓力急劇增加,電池的能量在瞬間轉換成熱能,形成單個電池燃燒或爆炸。
引起單個電池熱失控的因數很多、很復雜,但電流過大或溫度過高導致的熱失控占多數,下面重點介紹這種熱失控的機理。以鋰離子電池為例,溫度達到90℃時,負極表面SEI膜開始分解。溫度再次升高后,正負極之間的隔膜(PP或PE)遇高溫收縮分解,正、負極直接接觸,短路引起大量的熱量和火花,導致溫度進一步升高。
熱失控時,230℃~250℃的高溫導致電解液幾乎完全蒸發、分解了。它含有大量易燃、易爆的有機溶劑,逐步受到熱失控的影響,最終分解發生燃燒,是熱失控的重要原因。電解液在燃燒同時,產生一氧化碳等有毒氣體,也是重大的安全隱患。電解液如果泄漏,在外部空氣中形成比重較大的蒸汽,容易在較低位置大范圍擴散,這種擴散范圍極易遇火源引起安全事故。
在正常的充、放電過程中,正極脫出微量的游離氧與碳負極反應也會生成少量的易燃氣體CO,在正常溫度時它們不會助燃。正極氧化物由于短路造成的高溫下會發生分解反應,會產生游離狀態氧。這一些游離氧和CO在高溫下會與電解液蒸汽一起發生燃燒,形成惡性循環。
清華大學的研究顯示:正極中含鎳越多則熱穩定性越差,碳素材料的負極在壽命的前期較穩定,但是壽命衰減后變差。這從側面說明三元鋰電池的高鎳比例,雖然容量更大,但會導致更大的熱失控風險。
熱失控擴散指的是在電池包內部,個別電池熱失控后,熱量通過熱傳導和對流、輻射的方式迅速向周圍電池擴散,此時散熱裝置無法排除熱量,熱失控擴展到周圍電池,引起連鎖反應,電池表面溫度達到650~1 000℃,使電池包進一步燃燒。此時電池包卸壓閥門打開,火焰和濃煙擴展到電池包外部,此時在車外可能看到濃煙,進一步引燃車輛上電池周圍的可燃物,最終導致整車起火燃燒的現象。
從上述分析可以看出,電池內部就具備燃燒3要素,即可燃物、氧氣和火源。發生燃燒時,通常可采用噴水滅火,也可以采用干粉滅火器、二氧化碳滅火器滅火,砂土也是安全的滅火工具,最實用的滅火劑還是大量的水,它可以快速給電池包降溫。
車輛使用過程中,因各種原因,電池包可能發生電解液泄漏,泄漏前期不一定有熱失控發生,不易覺察。電解液容易揮發,還有腐蝕性,與空氣混合后生成有毒、刺激性氣體,對空氣和水造成嚴重污染,對人體器官會造成傷害,長期接觸易引起頭痛、頭暈、身體虛弱、惡心等。
目前,鋰電池廠商商和相關研究機構正在設法從鋰電池內部找出消除上述各種風險的措施,研發高穩定的電池材料,從根本上防止熱失控發生。這些研究內容包括電解液改進、正極材料改進、隔膜改進、表面包覆、泄壓閥及熱敏電阻(PTC)和加工工藝改進。
電極形狀改進的重要技術措施是疊片工藝,這一工藝技術對降低熱失控具有一定的作用。目前電池正極以整體卷繞工藝為主,電極極片在卷繞拐角處有內應力,在使用一段時間之后內應力會誘導極片產生破裂,容易誘發熱失控。而疊片工藝由于生產工藝效率低下,遠不及卷繞工藝應用廣泛,但極片一片片的疊加,它沒有拐角處應力問題,熱失控的誘因降低了。
智能隔膜技術對于控制鋰電池內部溫度具有一定的意義。采用美國Celgard公司的3層智能復合膜,在溫度120℃時,上、下層PE膜里面的微孔閉合,減緩鋰離子通過,電流減少溫度就會下降。溫度135℃時,中間層PP膜里面的微孔閉合,鋰離子不能通過隔膜,沒有電流通過,隔膜溫度就會下降。
電池蓋安全技術狀態對于防止燃燒是關鍵。在電池蓋的表面增加刻痕,當內部熱失控氣體壓力達到一定程度時,氣體在刻痕處沖破電池蓋,從此處排放出去。市場新出現的電池包CTP(Cell To Pack)技術,它取消了電池組框架,結構更加簡化,但是對于電池的一致性要求更高。另外,電池生產現場的雜質也會進入電池內部,引起短路,隨時可能誘發熱失控,為此必須做好生產現場的清潔工作。
當發生熱失控及擴展時,盡量降低事故的嚴重性,除BMS安全管理以外,還有電池包安全結構技術,以及主動安全技術。結構安全設計包含電池內部結構優化、熱傳播阻斷設計(阻燃復合材料的使用),排放閥的排泄通道設計(目前國內市場上主要是EPV(Explosion Proof Valve)防爆閥,不能完全隔離水汽進入電池包)、PTC及熔斷器設計等。
電池包內部布置時,必須進行電氣布局優化設計,減少插接件的數量和不合理的線束走向,讓整體的布局更加緊湊。電氣設計時要對最小電氣間隙及爬電距離進行優化,采用分布式電池外短路保護設計,多維模組熱擴展結構防護透氣防爆裝置。常用的熱傳播阻斷技術有模組間的隔熱設計,在模組之間增加隔熱零件,目前特斯拉汽車采用電池組之間增加云母片進行隔火。
增加電路熔斷保護設計。為防止主回路過載發熱和短路危險,在產品設計中采用了在主回路中安置主熔斷器、主繼電器、模組過流保護、電池過流保護和過流分級防護技術。為防止因電池包浸水和采集回路(對每一個單體電池或電池組的電壓進行檢測的低壓電路)導線及連接器失效,造成的短路對電壓采集回路有傷害,在電壓采集線電源端設置采集線路過流防護熔斷器,對系統內所有電壓采集回路進行保護[17]。
目前電池廠商多數通過監控電壓來判定電池熱失控,有的廠商也通過溫度來判斷。但目前多數廠商趨向于在電池包內安裝專用的壓力傳感器模塊,單個或多個電池向外熱失控時向外排放氣體后,電池包內壓力達到設定值時BMS系統綜合判定后開始報警。壓力傳感器模塊可以在停車后一段時間內處于待機狀態,繼續檢測壓力,如果壓力超標就會通知BMS系統啟動,開始監測工作。
采用主動安全技術的防爆設計。若電池發生機械碰撞及過充電的濫用情況(后面對7大類濫用原因有詳細介紹),電池內部發生熱失控時,大量高壓氣體封閉在電池內部,電池布局時設法讓電池向指定的安全方向排放氣體,杜絕了危險的進一步擴大。
采用主動安全技術的主動滅火裝置。火災探測裝置決定滅火裝置能否適時啟動、及時滅火、主動噴射惰性氣體或制冷劑來冷卻電池,目前主要在大型客車及公交車上推廣,在小型電動乘用車上還沒有應用。熱管理控制技術,可以防止預防熱失控的發生,在熱失控初期減緩它,抑制熱失控擴展。
熱管理控制技術屬于BMS功能的一部分,它可以通過對每一單體電池組實施監控,若發現單體電池溫度過高,則實時反饋,并及時切斷該電池的外部電路、啟動電池組冷卻系統和滅火系統。熱管理技術可以盡量使各電池組在最佳的溫度范圍內工作,防止熱失控發生和擴展、及時發出電壓和溫度監測報警等。
BMS在充電過程中,根據每臺車輛上電池狀態的變化情況自動給出最佳的充電方案,并將信息反饋給充電樁,實施最佳的充電方案。雖然在電池廠商在組裝時,會對電池按照差異最小化的原則進行電池分組,但隨著車輛使用時間增長個體電池的性能會逐漸出現差異,BMS的充電策略對于實施個體電池精確的控制越來越困難,可能會造成電池過充。
從BMS角度來看,熱失控發生之后,它無法消除這個風險,但要求它至少能提前5 min發出警報,給乘客的逃生贏得時間。優良的BMS在熱失控的前面階段把內部短路風險識別出來,至少提前15 min報警,給乘員發出報警并全車自動斷電,讓乘員安全離開。
(責任編輯:fqj)
-
鋰電池
+關注
關注
260文章
8145瀏覽量
170765 -
電池技術
+關注
關注
12文章
906瀏覽量
49335
發布評論請先 登錄
相關推薦
朗凱威鋰電池定制深度解析深藍 L07 新能源汽車鋰電池/電動汽車鋰電池
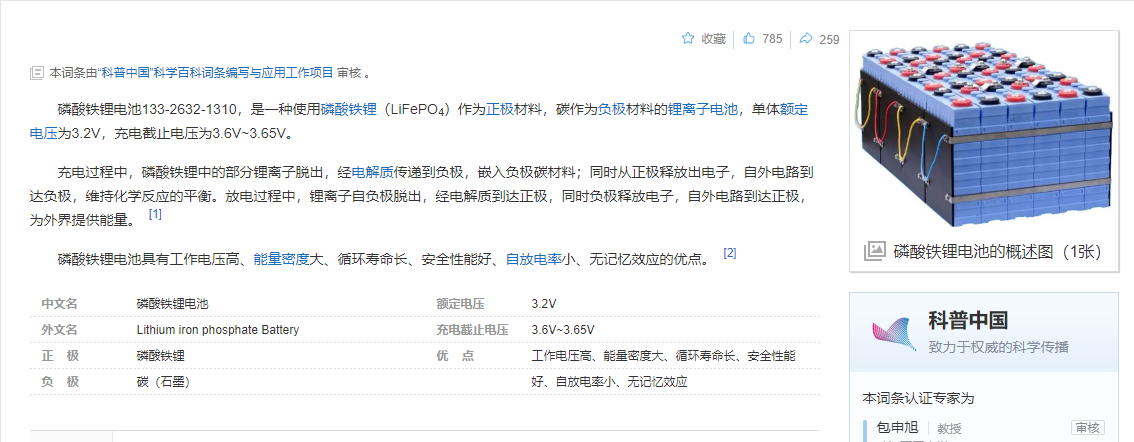
朗凱威鋰電池隔膜10強介紹鋰電池隔膜:小部件,大作用!
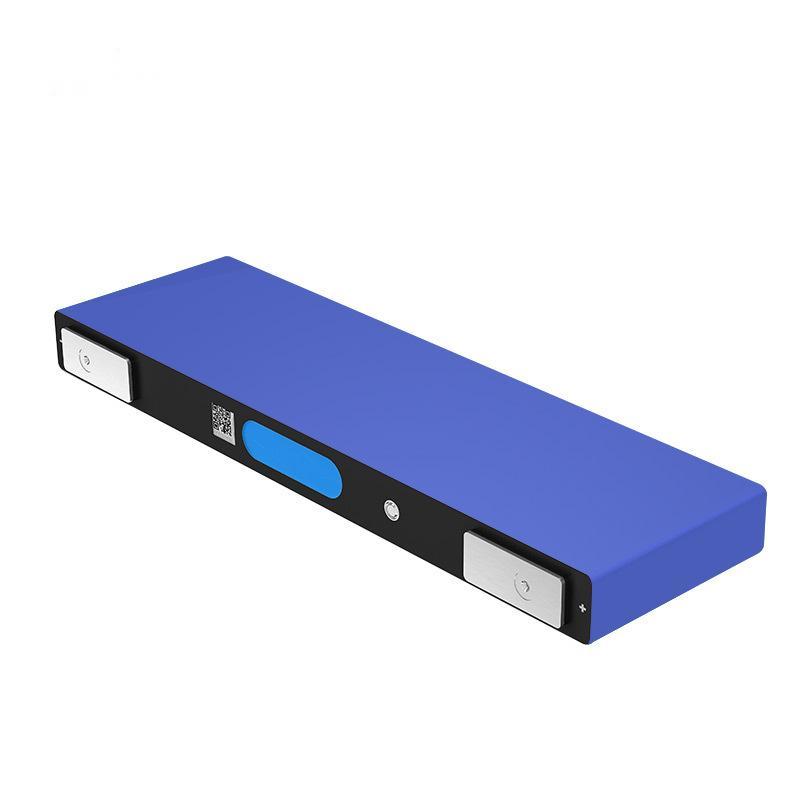
如何設計鋰電池相關電路避免鋰電池邊充邊放?
為什么鋰電池需要BMS?
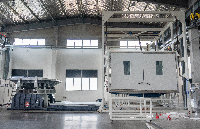
鋰電池CE認證要準備哪些資料?
PL7072C鋰電池保護電路:高精度過充過放解決方案
英集芯IP2341:適用于音箱電源解決方案的多節串聯鋰電池異步升壓充電芯片
鋰電池防爆試驗箱是什么?
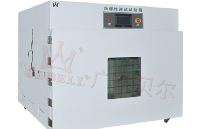
評論