(文章來源:中關村在線)
粉末床選區激光熔化(SLM)3D打印技術為構建具有自由形狀和復雜特征的零件提供了極大的自由度,但面對這種與傳統技術截然不同的增材制造方式,如何既滿足用戶對零件設計優化與機械性能的要求,又能夠合理控制增材制造成本,是開展面向增材制造的設計時所需要考慮的因素,也是一個需要在應用實踐中探索與積累的過程。
3D科學谷將分享一個3D打印除塵通道零件的設計案例,設計團隊通過仿真驅動設計、打印參數優化等方式實現了零件優化設計的既定目標,并合理控制了增材制造成本。
工程服務企業埃特博朗( Etteplan )為客戶重新設計了一種除塵通道零件,該零件的原始零件是用傳統方式制造的,存在的問題是成本高,并且因體積偏大而給設備裝配帶來困難。因此,客戶希望對現有的除塵通道進行設計優化。經過評估,埃特博朗采用金屬3D打印技術對此部件進行再制造,增材制造工藝釋放了除塵通道的設計空間,優化后的部件比原始方案重量輕、成本低,并且氣流特性得到改善。
埃特博朗為除塵通道項目組建了團隊,成員包括增材制造設計、增材制造生產和打印過程仿真方面的專家。在整個設計過程中,使用了增材制造生產成本估算工具和增材制造過程仿真軟件。
除塵通道零件的第一代增材制造設計去除了多余的材料,并獲得平滑的內部空氣通道。在這一點上,設計團隊使用了過程仿真軟件進行除塵通道零件擺放方向優化,從而分析出擺放方向對構建時間、支撐量以及所需的后處理工作量和預測的變形/變形水平的影響。
設計團隊確定了兩種比較優選的擺放方式。雖然按照這些擺放方式,單獨計算一個組件的打印時間長,但能夠充分利用打印構建板的空間,這意味著能夠在打印構建板中擺放的組件數量達到最多,即能夠在一次打印中同時制造的組件數量最多,從而使得每個組件的打印時間少于其他擺放方案。
接下來,設計團隊對第一代增材制造設計方案進行了修改,從而提高在首選方向上的可打印性,并減少對支撐結構的需求。為了確定在哪里需要使用支撐結構,設計團隊對選定擺放方向的組件進行了打印過程仿真,這將確保打印過程中不會發生因變形引起的零件與刮刀的碰撞,并確保最終變形水平在合理范圍。
在此階段,設計團隊還使用了增材制造成本估算工具,估算和比較各種設計方案與原始傳統制造零件的成本。估算結果表明,僅制造單個3D打印零件所需的材料和時間成本昂貴,但是如果一次打印同時制造11個零件,則3D打印成本與傳統制造成本基本持平。
設計團隊對除塵通道零件做了進一步的設計優化,將4層零件堆疊擺放在同一個打印構建板中,使用這種方式能夠在一次打印中制造出120個零件。打印過程仿真再次被用于估算零件所需的支撐結構,以及對打印過程進行了仿真模擬。優化除塵通道設計,最大化單次打印中可打印的零件數量等設計優化工作,使得單件3D打印除塵通道零件的成本比傳統零件制造成本低 40%。同時,由于通過增材制造技術建立了更為靈活的供應鏈,客戶能夠實現除塵通道的小批量按需生產。
以上部分展示了面向增材制造的零件設計迭代過程,設計團隊最終找到了實現更低制造成本的設計方案。但是實現更低的制造成本、更靈活的供應鏈,僅是除塵管道零件3D打印應用的部分價值,根據3D科學谷的了解,3D打印及面向增材制造的設計還帶來了附加價值,包括:重量減輕50%以上;顯著提升的氣流特性;比原始零件更易于組裝的連接設計。
由于除塵通道不是屬于關鍵的承重結構,因此最終產品并不要求達到具有完全致密材料的最佳機械性能。設計團隊對3D打印工藝參數做了一定優化,零件的機械性能只要足夠滿足應用需求即可,這樣使得打印時間得以縮短。
設計團隊與粉末床金屬3D打印設備制造商SLM Solutions 公司合作優化了工藝參數,提高部分不可見區域的打印速度,同時在其余部分使用標準的高質量工藝參數。此外,對支撐結構進行了優化,最大程度地減少材料的使用,并且使得打印后的粉末清除更加容易。這些優化使得打印時間減少了25%。
(責任編輯:fqj)
-
零件
+關注
關注
1文章
113瀏覽量
14950 -
3D打印
+關注
關注
26文章
3553瀏覽量
109246
發布評論請先 登錄
相關推薦
? SLA立體光固化成型:一項實現3D打印領域高精度數字模型實體化的先鋒技術
3D打印技術,推動手板打樣從概念到成品的高效轉化
自動零件分析儀的原理和應用
3D打印汽車零部件模型定制服務,多種材料、快速打印-CASAIM

應用在3D打印機的BD系列金屬連接器
工業零部件三維掃描形位公差檢測3d偏差比對-CASAIM
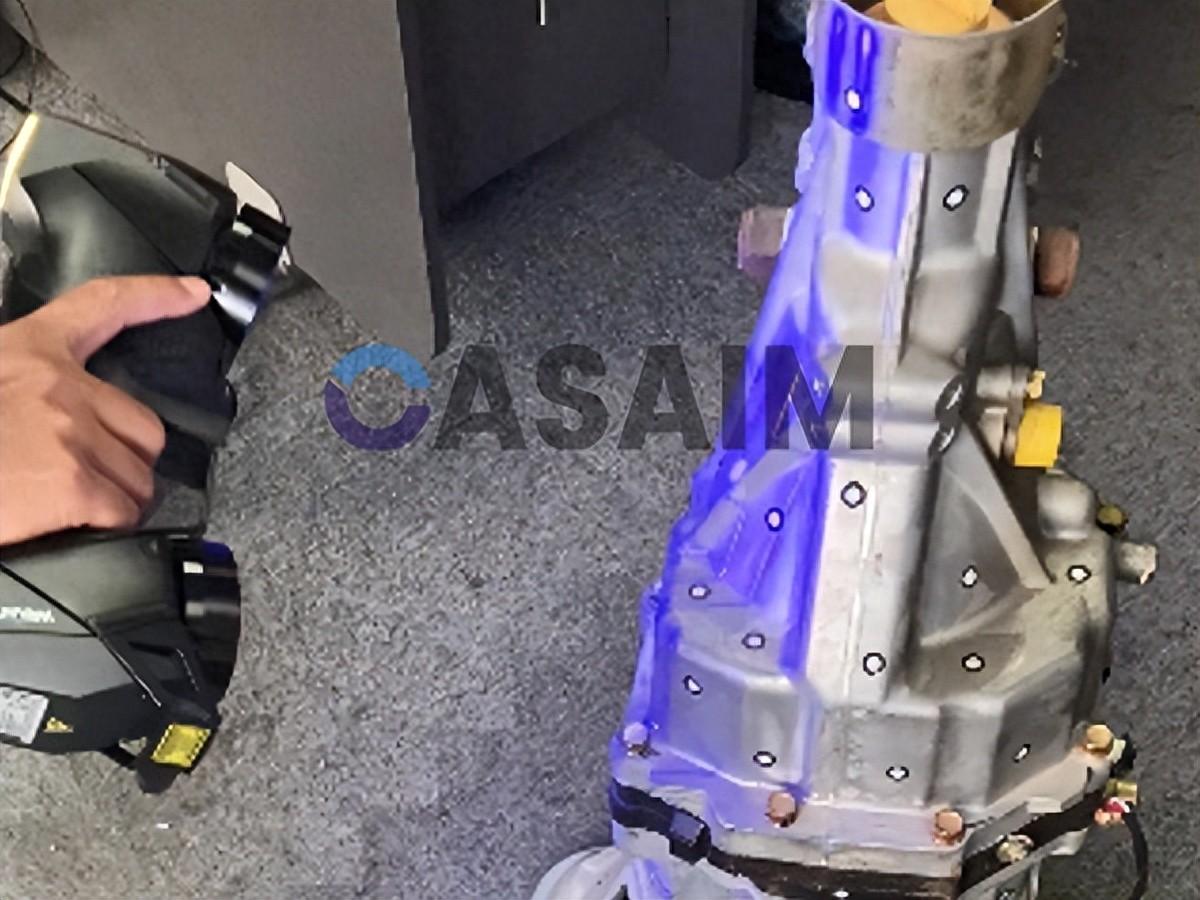
安寶特產品 安寶特3D Evolution:增材制造零件查找器
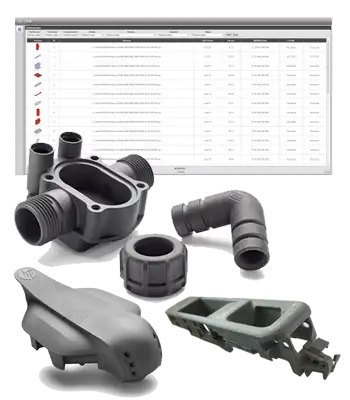
3D打印航空航天零部件模型3D打印定制設計服務CASAIM
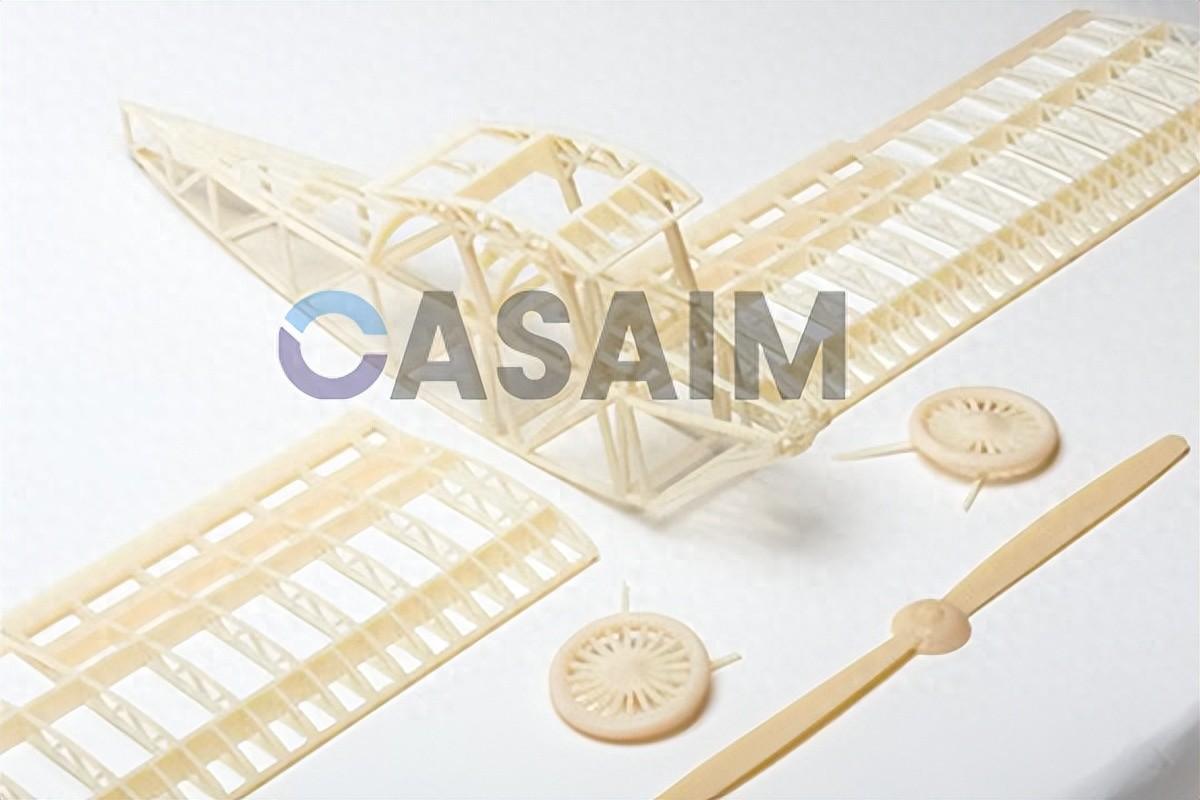
3D打印汽車零部件建模設計3D打印服務
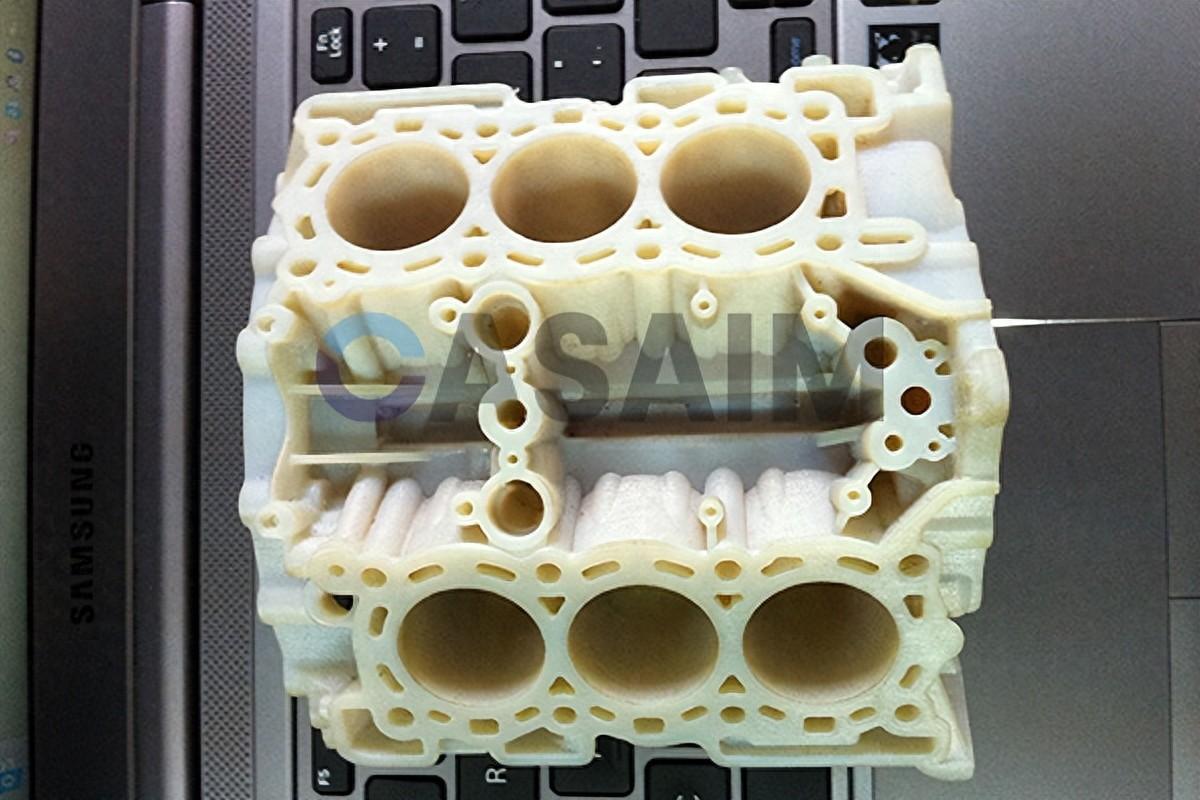
【開源作品】自制一個3D打印的移動終端——T3rminal
3D打印成就未來新產業
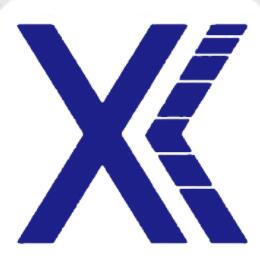
評論