“獲得國家91項專利,碳纖維回收利用比美國提前兩年時間做到,全國第一條碳纖維熱塑性復合材料生產線……”或許你很難將這些成就與一家成立不到4年的公司聯系起來。
但就是這樣一家“新”企業,憑借著自身的堅持,成為了碳纖維熱塑性復合材料領域的“黑馬”。
成立于2016年12月的安徽旭升新材料有限公司(以下簡稱:旭升新材)是一家專業從事新能源汽車用超能復合材料研發與生產的高新技術企業。其研發生產的碳纖維PA熱塑性復合材料是碳纖維復合材料加工新技術,在國內少有。
過去的倒視鏡在480G左右,用碳纖維PA復合材料制作的倒視鏡只有200G左右,重量減輕58%。
“碳纖維熱塑性復合材料應用領域很廣泛,將來在新能源汽車領域肯定會大有作為。以我們生產的倒視鏡為例,應用在新能源汽車上,能減輕重量,增強強度。耐刮擦性也有提高,倒視鏡移動性更輕便、靈活,耗電少。”旭升新材創始人蔡福泉近期在接受《大國之材》采訪時表示。
失敗千次迎來全國NO.1
如果所有人都說你錯了,有可能這才是你離正確最接近的時候。蔡福泉和他的團隊在碳纖維熱塑性復合材料上的堅持,看起來證明了這個道理。
碳纖維復合材料可分為熱固性與熱塑性,熱塑性具有可注塑成型,能夠滿足大量的高速生產的節奏,以及可回收等優勢。高分子材料畢業的蔡福泉和他的同學一起組建了這家公司,攻克這一材料。
從一個新課題開始,到找出理想的基體材料,他們用了近5年時間。項目在不斷失敗、不斷總結、不斷提高中緩慢推進。
“這里頭我們走了很多彎路,失敗不亞于1000次。”提到研發之初的艱辛,蔡福泉記憶猶新。“因為一開始不知道哪個基體好,也沒有資料和文獻可查,我們就找了很多基體去試,但老是不成功,試了很多次后才想出相似相熔理論。”
排除了上千種不可能后,成功在慢慢靠近。在理論層面,尼龍材料對碳纖維的浸漬與尼龍材料的熔融指數息息相關,熔融指數大,分子量小。而分子量小又影響復合材料的綜合性能,因此要盡量選擇熔融指數高,分子量分布窄、流動性好的尼龍材料需要大量的試驗。
但碳纖維和尼龍6不完全相似,需要對尼龍材料進行改性,使得尼龍材料能夠和碳纖維充分的浸漬以提高材料的綜合性能。同時對碳纖維進行表面處理,以增加與基體的反應活性。“我們加了很多助劑改性兩種材料,改性后出來的材料復合要求了。可以說,這里頭的技術難點就在這里,創新點也在這。”蔡福泉說。
材料開發出來了,如何產業化令蔡福泉撓頭不已。
“國內沒有設備,更沒有這樣的產線。一開始我們講要買設備的時候,國內一些知名廠家聽到都很感興趣,都想來投標。但聽到我們是生產碳纖維熱塑性復合材料后,他們都退縮了,并勸我也別做了,肯定做不成的。”蔡福泉告訴《大國之材》,幾乎所有先前感興趣的廠家都用專業知識和真實案例勸他不要涉險。
對方認為,制造熱塑性的復合材料的過程中因為碳纖維質量輕,會在空氣中飄起來,此外它具有導電性,會損毀設備。
在備受備“打擊”后,蔡福泉團隊與中國化工科學研究院開始合作。“他們一開始也說沒有完全的把握,但愿意試一試。”
正是這一試,試出了全國較早的碳纖維熱塑性復合材料生產線。
“雖然生產線里面有三個關鍵設備是從德國進口的,但其余部分的設備都是化工研究院研發出來的,這比我們一開始設想的全部進口成本要低多了。如果設備全部進口,報價是1000萬歐元左右,而現在,整條產線的成本是1000萬人民幣左右。”蔡福泉介紹。
2018年,旭升新材在國內較早建成了碳纖維熱塑性復合材料生產線,2019年,該產線投產。目前,該產線的年產量為1500噸。
“雖然現在產線還不是很完善,存在這樣那樣的問題,但總算是有了,我們也在邊用邊完善。”蔡福泉透露,今年上半年,旭升新材準備開第二條產線。“有了第一條,第二條就是復制了,會非常快。如果不是因為疫情耽誤,第二條產線已經起來了。”
應用:從“天上”到“地面”
過去,碳纖維熱塑性復合材料主要應用于航天航空領域,如用于直升機的地板、機身結構、固定機翼、尾翼、前襟翼以及垂尾根部的整流罩等部位。隨著許多高端領域對高性能復合材料的要求越來越高,熱塑性碳纖維復合材料開始逐步展現出自身的特殊優勢,為越來越多的產業提供零部件服務。
蔡福泉介紹稱,隨著碳纖維熱塑性復合材料行業的發展,其應用也逐步從“天上”落到“地面”,從高高在上的航空領域到家喻戶曉的汽車、電子等領域。
在我國汽車產業飛速發展的同時,能源安全、節能減排已成為汽車產業可持續發展所面臨的 重要問題。國家出臺了一系列的政策法規,對汽車的能耗和排放指標均進行了嚴格的限制,而汽車輕量化正是解決上述問題的重要手段。
碳纖維復合材料以其優異的機械性能、抗疲勞性能以及遠低于金屬的密度條件,成為了汽車輕量化的首選材料。但是,目前90%以上的汽車用碳纖維復合材料均采用熱固性樹脂體系,這類材料存在回收困難、固化周期長等問題。
由于具有易加工成型、邊角廢料可回收利用、不污染環境、成型周期短、生產成本低等特點,碳纖維熱塑性復合材料就成為解決這一問題的有效手段。
“碳纖維熱塑性復合材料易注塑成型,生產效率高,而且制品可重復加工,跟汽車產業可以配套。”蔡福泉表示。
據蔡福泉介紹,由于碳纖維增強聚合物基復合材料有足夠的強度和剛度,是制造汽車車身和底盤等主要結構件的較輕材料。“預計碳纖維復合材料的應用可使汽車車身和底盤減輕質量40%-60%,相當于鋼結構質量的1/3-1/6。”
而最接地氣的領域當屬運動領域。“比如用在高檔跑鞋上,主要保護運動員的腳腕,但目前成本還很高,一雙鞋好幾萬。”
目前,旭升新材涉及的應用包括:汽車、無人機螺旋槳材料、筆記本電腦外殼等。
以碳纖維增強熱塑性復合材料筆記本電腦外殼為例,這種筆記本電腦外殼以PMMA為基體,基體強度高,與碳纖維融合性好,整體性都能得到了提高。相對于傳統的碳纖維熱固性復合材料,這種筆記本電腦外殼外殼厚度減薄10%,重量減少10%。同時,在延展性能上表現更好,更具韌性,不易損壞。
“另外,相對熱固性符合材料,熱塑性復合材料具有可回收的特點。比如,我們做實驗的時候要先打個件,有時候打不成功,但是一點也不會浪費,我們會把這個廢件粉碎,然后按照一定的比例重新放到生產線上回爐,對整個系統沒有任何影響。”蔡福泉說。
成為最強大那個
讓旭升新材成為國內熱塑性復合材料領域的最強最大企業并爭取兩年內上市是蔡福泉的心愿。為此,他也做出了具體的規劃:“最近批下來的60畝的土地將是我們的新廠房,還要建一座新的研發大樓,名字我們起好了,就叫‘碳材料研發中心’。我們會聘請三個院士,將業務定位在民用的新能源汽車。”
“我去參加行業會議或展覽了解到現在在研究試驗階段的碳纖維熱塑性復合材料國內也有幾家了,但是真正規模化生產的只有我們一家。”蔡福泉表示,這也意味著與該領域發達的其他國家相比,國內還存在差距。
而造成這種差距的主要原因是國內進入該領域較晚,應用領域的拓展方面落后、人才缺乏、關鍵設備無法自主生產、沒有專業生產的助劑等。“我們還沒有數據庫,這就影響市場銷售,也影響人才隊伍。這一塊單靠汽車廠家、材料廠家是搞不起來的,必須由國家部門牽頭來搞。”
碳纖維熱塑性復合材料的產業化,旭升新材已邁出了重要一步,這也是國內在此領域中重要的一步。
“我們公司已經取得高新技術企業,材料已經應用筆記本電腦外殼,無人機,新能源汽車上了。出口到意大利產品也符合國際標準要求。由于受疫情影響出口受阻,正在開發國內市場,訂單已經接到年底了。”
去年年底,在合肥召開的亞洲新能源聯盟會議上,旭升新材的項目獲得了科技創新獎。“現場的專家和汽車廠家的老總們都很看好我們這個項目。”
也是在同一場會議上,與會專家提出,建立該行業的國家數據庫。“這個數據庫意味著什么呢?有了數據庫,設計人員就敢用我們設計的汽車倒視鏡了,因為在里面一查,對汽車影響等等,所有的參數都能一目了然,他們就心中有數了。”蔡福泉告訴《大國之材》。
蔡福泉透露,目前汽車廠家在該方面已有所行動,而東華大學、北航也已建立相關實驗室。“應該很快了,一旦有了數據路,這個應用就很普遍了。”
【人物介紹】
蔡福泉,教授級高工,1982年畢業于四川大學高分子材料系,從事高分子材料研發應用40多年。獲得國家專利78項。榮獲國家、省、市區科技進步獎7項,公開發表論文17篇。
【企業介紹】
安徽旭升新材料有限公司創建于2016年, 是一家專業從事碳材料研發與生產的科技型中小企業, 2019年榮獲高新技術企業稱號。公司現有聚合物、 碳纖維熱塑性復合材料、 PC光擴散材料等系列產品, 可廣泛應用于汽車、 電子、 電器、 通訊、 機械、 航空等領域。長期與新能源汽車合作, 并與大專院校開展產學研合作, 對CF+PA6、 CF+PA66、 CF+PC、CF+PEEK進行重點開發研究。
-
碳纖維
+關注
關注
0文章
86瀏覽量
11905
原文標題:成立4年歷上千次失敗 這家企業的碳纖維終擺脫加工難困局
文章出處:【微信號:xincailiaozaixian,微信公眾號:新材料在線】歡迎添加關注!文章轉載請注明出處。
發布評論請先 登錄
相關推薦
復合材料的機械性能測試詳解
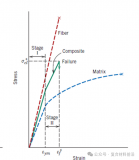
一文看懂PEEK、PEKK、PAEK等熱塑性復材及相關成型工藝進展
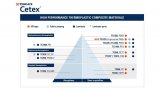
復合材料的測試及分析指南
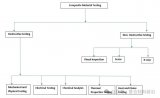
C/C復合材料連接技術研究進展
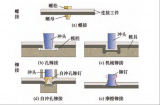
粉末涂料在復合材料部件上的應用
石墨烯化學鍍銅對放電等離子燒結石墨烯增強鋁基復合材料組織和性能的影響
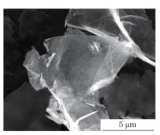
PEEK與其他熱塑性材料的比較
碳/碳復合材料的優點有哪些
ATA-2021B高壓放大器在碳纖維復合層板損傷定位研究中的應用
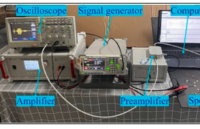
碳纖維阻抗和玻璃纖維阻抗的區別
用量占比超90%,碳纖維復合材料成打造eVTOL首選
基于隱形飛機噴氣式發動機雙S彎噴管的纖維纏繞工藝
單向碳纖維強化的柔性壓電納米復合材料的原理、結構設計及應用
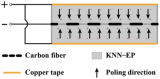
評論