引 言
油井的抽油機數(shù)據(jù)采集傳輸管理是油田生產關鍵環(huán)節(jié)之一,生產計劃的決策依賴于大量現(xiàn)場數(shù)據(jù)的及時正確的采集。由于資金的制約和傳統(tǒng)管理方式等因素,我國石油企業(yè)在生產作業(yè)上自動化的應用程度還很低。例如抽油機的井口回壓、出油溫度、套壓、油壓等資料均靠人工巡井獲得。我國的油田大部分油井分布較分散,這就造成數(shù)據(jù)采集工作量大,采用傳統(tǒng)的人工巡檢方法對油井生產數(shù)據(jù)采集錄入,效率是非常低下,精確度不高受天氣影響大的特點,對油井的生產動態(tài)數(shù)據(jù)掌握不及時,不能做到在線管理。各項數(shù)據(jù)靠人員匯總錄入分析,也不適應現(xiàn)代化管理的要求。為了準確且迅速地掌握并利用采油現(xiàn)場數(shù)據(jù)信息,對生產狀況進行有效地統(tǒng)籌平衡管理,優(yōu)化資源配置,提高企業(yè)的經濟效益,打造數(shù)字化油田,應著手建立一套抽油機生產數(shù)據(jù)采集DCS自控系統(tǒng)。
1 DCS系統(tǒng)概述與系統(tǒng)原理
1.1 DCS簡介
DCS(Total Distributed Control System)是以微處理器為基礎的集中分散型控制系統(tǒng)。自20世紀70年代中期首次推出后,就一直占主導地位的控制系統(tǒng)框架。它的主要特征是集中管理和分散控制相結合,與模擬電動儀表較,具有連接方便、數(shù)據(jù)存儲量大等優(yōu)點;與計算機集中控制系統(tǒng)比較,它具有操作監(jiān)督方便、危險分散、功能分散等優(yōu)點,但其信號傳送一般采用4~20 mA的電流信號形式,一個變送器或執(zhí)行機構需要一對傳輸線來單向傳送一個模擬信號。抽油機工作看似簡單,實際由于油井分布的面積大分散性等特點,對于油田企業(yè)來講,對其采油生產過程進行自動檢測、順序控制就是一個很龐大的工作。應用自動數(shù)據(jù)采集控制系統(tǒng),可以對單井抽油機的工作狀態(tài)進行實時監(jiān)測,對生產設備進行自我保護與自我控制,可以大大提高其運行效率。
1.2 結合DCS模型設計數(shù)據(jù)采集系統(tǒng)的三層結構原理
1.2.1 抽油機數(shù)據(jù)采集的三層功能概述
傳統(tǒng)的DCS分三層網絡結構:生產管理級,監(jiān)控級和過程控制級等。在油井數(shù)據(jù)采集系統(tǒng)中,過程控制級是整個采集系統(tǒng)的關鍵部分。其性能影響著油井抽油機各種參數(shù)信息的實時性、抽油機狀態(tài)的運行判斷以及管理決策的正確性。該系統(tǒng)中的過程控制級完成抽油機的運行參數(shù)的檢測任務。監(jiān)控級則通過協(xié)調過程控制設備,實現(xiàn)抽油機工作過程的動態(tài)管理及停開操作。生產管理級完成制定生產計劃和工藝流程。DCS使用相對集中的控制站,完成生產過程中各個局部的控制作用,實現(xiàn)分散、數(shù)字化的控制過程。
1.2.2 采集數(shù)據(jù)信息的分類
根據(jù)控制理論可知,控制系統(tǒng)的數(shù)據(jù)信息可以劃分為設定量、擾動量、反饋量及輸出量。在抽油機生產數(shù)據(jù)采集系統(tǒng)中,也可以分為這四類相對應的因素:設定量是依據(jù)當前抽油機的各項標準參數(shù)如井口回壓、出油溫度、套壓等;擾動量是外界人為因素和各項干擾影響因素,即各種設備的誤差及其后對現(xiàn)場環(huán)境的影響等要素;輸出量是經過測量的各項生產技術指標量;反饋量是對輸出量進行信息采集處理后,將參與和設定量比較的量。同樣將油田抽油機的數(shù)據(jù)采集系統(tǒng)應用同樣的工作原理,設定量輸入系統(tǒng)并受擾動量作用后,經系統(tǒng)功能轉換產生目標近似輸出量,然后對輸出量進行信息采集處理并反饋到設定量,從而形成新的設定量,同時進一步修改并精確設定當前抽油機效率最優(yōu)參數(shù)標準值,從而達到控制原油開采的目的。當抽油機發(fā)生器械故障導致停井時,工作人員可以第一時間發(fā)現(xiàn),并且根據(jù)系統(tǒng)采集數(shù)據(jù)分析故障原因,迅速派出維修人員抵達現(xiàn)場,進行設備的維修,最大限度降低了因抽油機故障造成的原有生產損失。
2 抽油機數(shù)據(jù)采集系統(tǒng)功能的實現(xiàn)
油井數(shù)據(jù)采集管控系統(tǒng),是集抽油機生產控制、數(shù)據(jù)監(jiān)測和管理于一體的生產過程自動化控制體系。該系統(tǒng)以油田作業(yè)的抽油機運行管理為對象,以智能測控儀器儀表為窗口,通過計算機網絡通信將計算機網絡延伸到油井的井口,形成了油井數(shù)據(jù)采集自控系統(tǒng),實現(xiàn)油井信息的快速獲取、信息集中處理、分析、診斷和反饋控制。具體實現(xiàn)項目的系統(tǒng)功能,是由系統(tǒng)主機、過程機和直接數(shù)字控制分別完成統(tǒng)一組成的。在計劃系統(tǒng)里,各種傳感器和智能儀表為測量控制級,以控制器或PLC為核心的下位機系統(tǒng)構成了整個油田的生產系統(tǒng)的操作級,用具有網絡功能的控制主機為上位機構成了數(shù)據(jù)采集控制系統(tǒng)的監(jiān)控級。各子系統(tǒng)之間具有自己獨立的網絡系統(tǒng)和布線系統(tǒng),并通過網絡與公司其他生產單元監(jiān)控操作站相連,同時監(jiān)控操作站又與企業(yè)信息網相連,將生產數(shù)據(jù)發(fā)送到公司管理部門。
2.1 系統(tǒng)的設計與實現(xiàn)功能
油井生產管理自動化控制系統(tǒng)采用分層控制結構。形成以多臺計算機為基礎的分散型控制系統(tǒng)。采用過程裝置控制設備和多個控制卡及I/O子系統(tǒng)模板組成過程裝置控制級,通過通信網絡將過程信息傳送到上、下級。抽油機數(shù)據(jù)采集的功能分層是根據(jù)集散控制系統(tǒng)的體系特征而設計,它充分反映集散控制系統(tǒng)的分散控制、集中管理的特點。抽油機運行信息自下向上到管理層逐漸集中,同時,它又自管理層向下至生產一線逐漸分散。其簡單系統(tǒng)框圖如圖1所示。
2.1.1 生產管理級功能介紹
系統(tǒng)生產管理級(中心控制室)主要用于完成對整個系統(tǒng)各子功能的控制及調度。流程圖顯示功能模塊完成各個工作區(qū)域的流程圖和相應參數(shù)變化情況的顯示。歷史趨勢及棒形圖顯示模塊:實現(xiàn)歷史生產狀況的趨勢再現(xiàn)和與之對應時間點的棒形圖及數(shù)據(jù)表格顯示。控制主機系統(tǒng)軟件的主要功能是通過通信網絡實現(xiàn)上位機與下位機間的數(shù)據(jù)傳輸,以及將下位機實時采集的數(shù)據(jù)進行處理,包括存入數(shù)據(jù)庫、進行流圖顯示,還有數(shù)據(jù)表的顯示及各種要求的報表打印輸出。控制主機LED顯示大屏幕可以顯示油井分布圖并且定義多個測控畫面,每個測控畫面上可以顯示多個測控參數(shù),比如可以實時顯示電流、電壓、溫度、油壓等參數(shù)。通過控制主機實現(xiàn)抽油機的停開機的網絡控制;油井故障實時顯示報警,包括故障發(fā)生時間和故障原因;基本實現(xiàn)數(shù)據(jù)在線分析診斷,具有計算流壓、系統(tǒng)效率、抽油桿、抽油泵、抽油機分析,功圖量油比較,智能診斷等功能。
2.1.2 監(jiān)控級是功能介紹
系統(tǒng)的控監(jiān)控級(油井工作站)主要完成系統(tǒng)內部通信鏈路的建立及數(shù)據(jù)信息流的傳輸。油井工作站既是中心控制室與智能測控終端的中間站,又可獨立運行。數(shù)據(jù)采集及系統(tǒng)內部通信是該系統(tǒng)的核心。可以完成功能包括:初始化系統(tǒng)參數(shù)、運行參數(shù)設置、修改及對所有智能測控終端進行各類參數(shù)范圍和功能的設置;對所有智能測控終端定時校對;定檢、自動巡檢(自動校對、通信、測量等);故障處理(日志、實時響應);功圖管理(比較、備份、分析);對終端檢測的抽油井故障進行報警和顯示。
油井工作站直接與生產區(qū)的智能儀表接口,將各種生產數(shù)據(jù)信息采集并處理后按一定格式存放;它還有另一個重要的任務是不斷監(jiān)聽通信線路是否有上位機傳來的數(shù)據(jù)傳輸請求,將所采集信息準確快速地傳往中心控制室主工作站。并且要保證所采集數(shù)據(jù)的正確、完整性和及時性。最大的特點是該系統(tǒng)是一個連續(xù)不間斷的運行系統(tǒng),一旦開機運行即不需要任何人工干預。這就決定了油井工作站不僅要從硬件上保證安全可靠,而且在軟件開發(fā)上也要從高可靠性、安全性方面出發(fā),保證其正常連續(xù)運行。在最惡劣的情況下,如系統(tǒng)掉電、系統(tǒng)“飛程序”等,還應使油井工作站具有一定的故障自診斷和自動恢復功能。
2.1.3 控制級實現(xiàn)的功能介紹
系統(tǒng)過程控制級的各種數(shù)據(jù)采集儀器儀表是系統(tǒng)最底層部分,可完成的功能包括:示功圖、電流圖等的測量及儲存;電機的電流監(jiān)測及抽油桿斷脫、抽油桿卡死保護;井口控制箱門的狀態(tài)監(jiān)視;回壓、油壓、套壓、井口溫度的監(jiān)測;電網電壓的監(jiān)測及電壓高、低、斷相保護。控制系統(tǒng)具體實施時,根據(jù)油田的實際情況,可以采取適當?shù)呐渲谩嫿ㄏ到y(tǒng)應考慮預留通信接口,以便將來對系統(tǒng)進行后續(xù)擴建。該部分系統(tǒng)軟件中設計了以下主要功能模塊:系統(tǒng)初始設定模塊;系統(tǒng)故障自診斷恢復模塊;通信服務模塊;數(shù)據(jù)采集模塊;數(shù)據(jù)存儲模塊。
3 數(shù)據(jù)采集系統(tǒng)的網絡通信
3.1 自動化網絡與企業(yè)辦公網絡通信
油氣田自動化網絡相對于企業(yè)辦公網絡是一個相對封閉獨立的自動化工控網絡,要實現(xiàn)自動化控制網與企業(yè)辦公網的數(shù)據(jù)交換通暢,需要設計合理的網絡拓撲結構。所以油田自動化控制網絡根據(jù)自動化系統(tǒng)需求,采用內部IP地址,通過路由方式與企業(yè)辦公局域網建立連接,并以NAT網絡技術實現(xiàn)工控網絡內部IP地址與企業(yè)辦公網絡IP地址間的“邏輯”鏈路連接。所以自動化系統(tǒng)采用的網絡拓撲結構必須滿足自動化控制網絡系統(tǒng)安全及與企業(yè)網絡數(shù)據(jù)交換通暢的要求。
3.2 自動化網絡內部數(shù)據(jù)通信
為了保證通信的完整性,大部分DCS廠家都能提供冗余數(shù)據(jù)公路。為了系統(tǒng)的安全性,使用復雜的通信歸約和檢錯技術。所謂通信歸約就是一組規(guī)則,用來保證所傳輸?shù)臄?shù)據(jù)被接收,并且被理解使它與發(fā)送的數(shù)據(jù)一樣。整個數(shù)據(jù)傳輸系統(tǒng)由總部中心控制室的主工作站和下級各分工程師站的子站構成通信網絡,主工作站同時可以掛在網絡上,允許其他有協(xié)議的網絡計算機共享數(shù)據(jù)資源。具體工作方式采用主從式,即主站巡回呼叫各個子站,同時下傳數(shù)據(jù)。相應地被呼叫的子站接收數(shù)據(jù)并按要求上傳數(shù)據(jù)。收集到的數(shù)據(jù)由組態(tài)軟件管理在主機上實時顯示,同時寫入數(shù)據(jù)庫供第三方使用。實際的系統(tǒng)組態(tài)根據(jù)具體的管理層設置了兩層管理權限,即公司級管理員、現(xiàn)場操作級管理員。根據(jù)用戶名和密碼權限,公司級管理員能夠進入系統(tǒng)所有頁面并進行操作,現(xiàn)場級管理員則只能進入相應的管理區(qū)域頁面進行監(jiān)管操作。采用網絡版的工控組態(tài)軟件,該軟件不但可以提供逼真的系統(tǒng)工藝圖,同時實時動態(tài)顯示控制現(xiàn)場參數(shù)和該系統(tǒng)設備工作狀態(tài)。
對于管理而言,系統(tǒng)采用基于工藝流程顯示、控制的組態(tài)軟件,它的人機界面好,管理功能強,同時支持網絡數(shù)據(jù)庫,能夠做到數(shù)據(jù)有效管理和共享。
4 系統(tǒng)可靠性的對策
4.1 對系統(tǒng)可靠性的一般理解
系統(tǒng)的可靠性是指產品在規(guī)定的條件下和規(guī)定的時間內完成規(guī)定功能的能力。作為產品的一個特性指標,可靠性具有綜合性、時間性和統(tǒng)計性的特點。所謂“綜合性”是指它不是從某一個側面來衡量產品的優(yōu)劣,而是從整體上評價系統(tǒng)能否完成預定的功能來評價一個產品的優(yōu)劣。所謂“時間性”是指系統(tǒng)在整個使用周期內,隨著時間的推移,在各種現(xiàn)場環(huán)境條件和不同的使用條件下,保持與該系統(tǒng)出廠驗收所達到的一切功能的能力。所謂“統(tǒng)計性”是指一套DCS可靠性的高低是不能用儀器在一個短時間內測量出來的,而是需要通過大量統(tǒng)計數(shù)據(jù)的積累,按照一定的統(tǒng)計規(guī)律才能求出。前端自動化測控儀表等設備長期工作在強腐蝕高溫高壓狀態(tài)下,對設備的硬件耐用性要求非常高。設計中利用雙重化冗余技術來達到高的可靠性,減少依賴于人工智能、無程序可循的工程業(yè)務和維修作業(yè)。系統(tǒng)可靠性的保證更為復雜,在這里筆者列舉系統(tǒng)初始數(shù)據(jù)采集的前端進行數(shù)字信號隔離,可以使得系統(tǒng)的可靠性大大提高。
4.2 提高單個設備使用從而提升系統(tǒng)整體安全
要提高設備的性能安全性,首先要了解該系統(tǒng)自動化儀表測量的實際指標,包括壓力、溫度、流量等。這些被測量值是會被傳感器等采集設備輸出作為電信號被讀取的。由此該系統(tǒng)控制環(huán)節(jié)所要測量的基本指標為:
壓力測量一般采用應變式壓力傳感器,精度高達(0.2%~0.3%),輸出為0~5 V;溫度的測量一般采用美國AD公司生產的半導體集成溫度傳感器AD59KH,可以輸出標準化的線性電流,綜合了多種測量元件的優(yōu)點;對于流量測量可以利用流量計,取其輸出的脈沖信號,同樣可以轉化為數(shù)字信號輸入該系統(tǒng)的檢測單元。
因此,可以通過減少非正常電信號對設備的沖擊,延長單個設備使用壽命。檢測并將信號送到AI模塊前,因電流轉換輸送單元與強電直接連接,高低壓之間無隔離,強電容易竄入AI模塊。輕者損壞模塊的某個通道,重者引起DCS中AI模塊的損壞,進而導致整塊AI模塊故障,使控制級主站的很多工藝參數(shù)不能顯示。所以加入數(shù)字I/O隔離模塊。被測的模擬信號經過三個環(huán)節(jié)變換成數(shù)字信號,輸入到計算機CPU處理單元,A/D轉換為12位精度地轉換模塊,其他兩個環(huán)節(jié)的精度和匹配是測量的關鍵。做如上信號處理后,可以最大限度的保護系統(tǒng)后環(huán)節(jié)的電子設備及模塊,從而提高整個系統(tǒng)的安全可靠性。原理圖如圖2所示。
5 結 語
該系統(tǒng)建成后可實時掌握抽油機的工作狀態(tài),可以提高抽油機采油的工作效率。在設備出現(xiàn)故障時及早發(fā)現(xiàn),避免不必要的經濟損失,縮短診斷故障的時間,有效地提高開井率。通過有線或無線網絡通信與主站計算機相接,可以使公司管理層直接了解各油井抽油機的工作狀態(tài),縮短生產數(shù)據(jù)的傳遞周期,提高資料錄入存取的準確性。公司管理與生產決策人員可以通過中央控制室計算機直接了解各油井的示功圖變化,及時進行分析、診斷,從而達到優(yōu)化系統(tǒng),組織生產的目的。抽油機數(shù)據(jù)采集系統(tǒng)的建成可以實現(xiàn)數(shù)據(jù)自動提交、報表自動生成。從而降低勞動強度,可以同時為工程、地質人員提供準確及時的數(shù)據(jù),實現(xiàn)了及時掌握油井生產動態(tài)和油田生產狀況。利用該系統(tǒng)可及時了解全油田的生產動態(tài),通過多個實時及歷史數(shù)據(jù)的全面展示可以對某一生產分系統(tǒng)(如集輸系統(tǒng))進行全面分析與監(jiān)測,為系統(tǒng)優(yōu)化運行提供參考依據(jù)。通過全部油井的逐一計量,可快速實現(xiàn)對全油田生產動態(tài)的及時掌握,為油田的技術措施提供數(shù)據(jù)支持。自動化實時數(shù)據(jù)向關系數(shù)據(jù)的轉化,實現(xiàn)了自動化數(shù)據(jù)與ERP等管理軟件的無縫接入,使自動化數(shù)據(jù)直接用于原油的生產運輸與管理,服務于企業(yè)的生產。
責任編輯:gt
-
控制系統(tǒng)
+關注
關注
41文章
6752瀏覽量
111764 -
數(shù)據(jù)采集
+關注
關注
40文章
6924瀏覽量
115631 -
微處理器
+關注
關注
11文章
2369瀏覽量
83814
發(fā)布評論請先 登錄
DCS數(shù)據(jù)采集系統(tǒng)有什么功能
數(shù)據(jù)采集與控制系統(tǒng)應用說明
DCS控制系統(tǒng)的配置與實施流程
如何選擇合適的DCS控制系統(tǒng)
DCS控制系統(tǒng)在工業(yè)自動化中的應用
DCS控制系統(tǒng)的工作原理
DCS數(shù)據(jù)采集與實時監(jiān)控
DCS數(shù)據(jù)采集IOT平臺有什么功能
DCS數(shù)據(jù)采集物聯(lián)網網關是什么
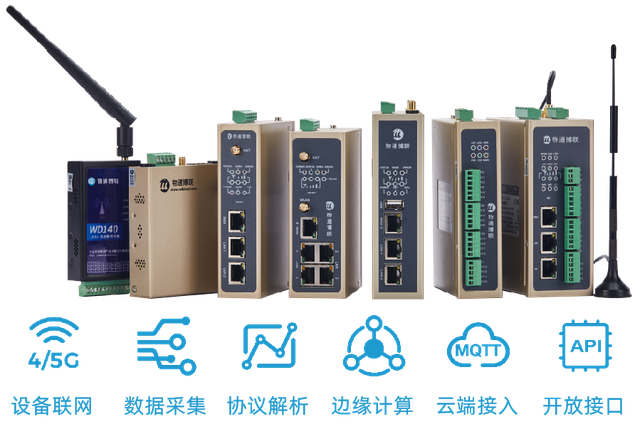
制藥廠DCS數(shù)據(jù)采集遠程監(jiān)控解決方案
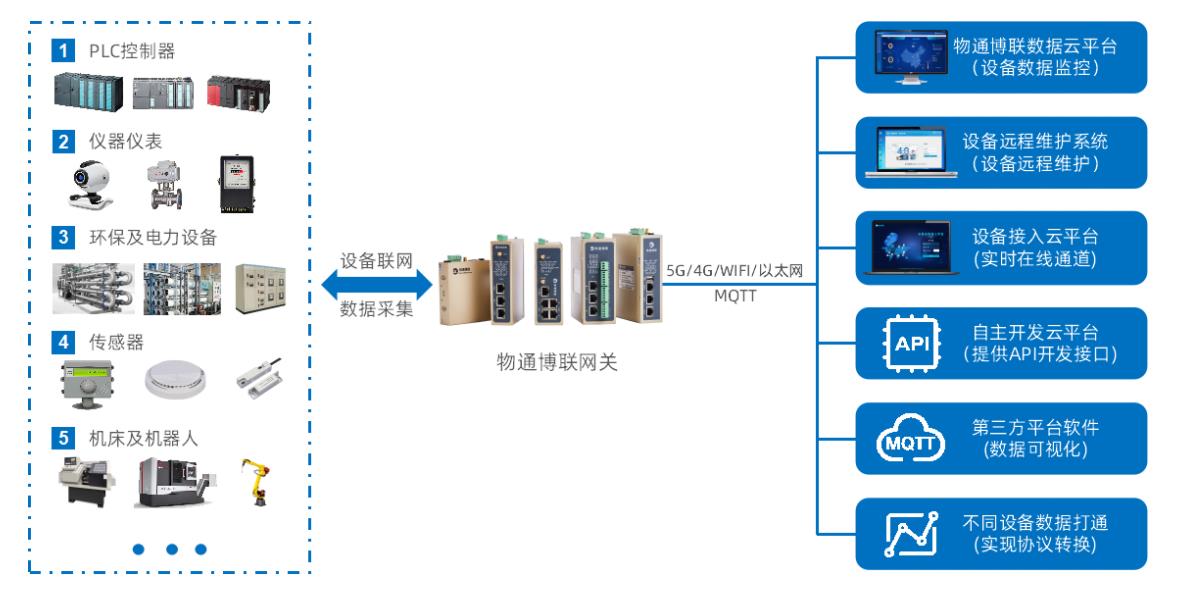
DCS數(shù)據(jù)采集平臺的功能和作用
工控系統(tǒng)PLC、DCS、SCADA數(shù)據(jù)采集如何實現(xiàn)
DCS控制系統(tǒng)什么意思?施耐德電氣打造Foxboro DCS解決方案助推工業(yè)數(shù)字化
DCS數(shù)據(jù)采集系統(tǒng)的功能與應用場景
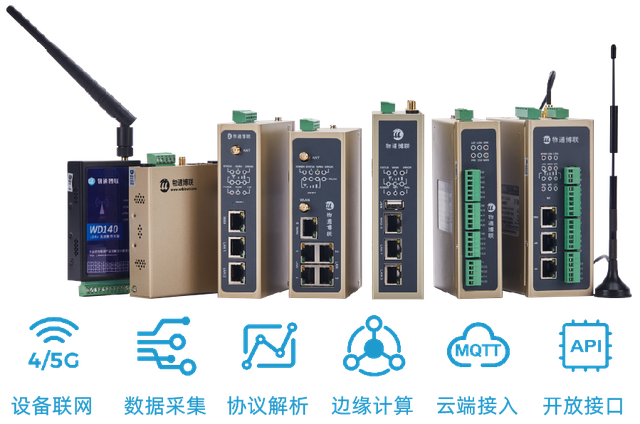
評論