隨著國內制造企業實力的提升,很多工廠開始大舉購買更好的設備進行生產。然而,有些工廠使用這些設備后的效能并不太理想,有的甚至在短期內設備就開始出現故障。
一位設備操作技工如是抱怨,“我們工廠那些設備,天天壞,壞了就報修,維修真沒少花錢,老板也不想想怎么維護保養!”
正因為我們的生產現場管理對于設備的嚴重疏漏,設備才會經常出現“癥狀”!一流的工廠時時維護設備,三流的工廠天天維修設備,一字之差,效能卻相差數倍。
差在哪里?
差在對現代管理的理解,差在管理制度的落實,差在用落后的觀念去使用最先進的設備。
現代班組的生產,越來越離不開各種加工、輔助設備,沒有穩定運行的設備,就不會有班組正常的生存基礎。
反觀我們的身邊,設備卻在頻頻違背我們的心愿,故障頻發,能源中斷,油路泄漏,備件不良,功能喪失等等這些設備導致的問題,時時干擾著正常工作進行,生產現場組織活動因此總處于中斷狀態。久而久之,班組長從組織生產的“戰斗精英”,變成了組織搶修,匯報的“救火精英”。
同樣,面對設備故障頻發,設備管理部門和專業維修人員疲于應付,工作東奔西殺,到處救火,可依然擺脫不了被一線人員抱怨的厄運,最終,導致一線班長和設備維修人員同時心力交瘁,無可奈何。
如何實現零故障?
有人可能要問,按照零故障觀點,設備豈不可以永久地使用下去了嗎,這里我們要區分兩個不同的概念就是自然老化和強制惡化。
所謂自然老化就是雖然使用方法正確,但隨著時間的推移,設備發生了物理和化學的變化,初期的性能逐漸下降。
而所謂的強制惡化是指未按應有的方法作業,人為地促使了惡化。比如,應加油處未加油,或雖加油卻量過少或周期過長。還有未進行應有的設備清掃等等,即該做的事沒做,都會促使設備惡化。
這樣,設備的使用壽命就低于其應有壽命,大大短于自然老化的壽命。因此零故障觀點的意義在于指導我們正確認識故障,做該做的事以避免強制惡化,延緩自然老化。
目前為止,之所以還存在很多故障,往往是沒有抓住故障的真正原因。在故障發生前,通常都存在一些微小的、隱含的缺陷。如果在故障發生前,對這種不引人注目的、最終導致故障的潛在缺陷加以重視,并及時改善,就可以消除故障。由此可見,潛在缺陷的明顯化處理是“無故障”的原則。
為了實際推進這項工作,我們針對可能產生故障的原因,導出實現零故障的五大對策:
1、具備基本條件
所謂具備基本條件,就是指清掃、加油、緊固等。故障是由設備的劣化引起的,但大多數劣化是由于不具備基本條件3要素引起的。
2、嚴守使用條件
機器設備在設計時就確定了使用條件。嚴格按照使用條件使用,設備就很少產生故障。比如電壓、轉速、溫度及安裝條件等,都是根據設備的特點而決定的。
3、使設備恢復正常
一臺設備,即使具備了基本條件,保證使用條件,由于很難做到十全十美,因此設備還是會發生劣化,產生故障。所以使隱含的劣化明顯化并使之恢復到正常狀態。這意味著我們應經常地對設備進行正確的檢查和預防修理。
4、改進設計上的不足
有些故障即使采取了上述三種對策后仍無法消除,它們往往是由于設備在設計、制造、安裝過程中的不足或差錯所造成。對這類故障應認真分析并對這些缺陷加以改善。
5、提高人的素質
所有的對策都要由人來實施,在實現零故障的過程中人是最根本的。首先,每個人都要有認真的態度,敬業的精神,其次,對故障有一個正確的認識,最后就是要提高操作和維修人員的專業技能。
總的來說,我們在日常工作中要做好下面這幾方面的工作:防止劣化的活動:正確操作、準備、調整,清掃、加油、緊固等;測定劣化的活動:檢查使用條件,對設備作日常、定期檢查以早日發現故障隱患;復原劣化的活動:及時消除隱患和劣化,使設備恢復到正常狀態。
用步進方式來開展自主保養
大家都希望設備有高的效率。就設備而言,其效率的高低涉及兩方面的人,一是生產使用人員,二是保養維修人員。如果兩方面的人員都把自己看作各自孤立的一方,我們是生產者只管使用,你們是維修保養者,設備的好壞由你們負責,這樣當然不會產生什么好的結果。
應該看到,生產使用和維修保養是一個整體的兩個方面,這就好比自行車的兩個輪子,只有二者齊備互相配合,才能充分發揮出設備的效能。生產使用部門并不只管生產和使用就夠了,它也應承擔起設備保養的基礎工作,即“防止劣化的活動”。只有生產使用部門搞好了“防止劣化的活動”,維修保養部門才能發揮出其所承擔的專職保養手段的真正威力,才能使設備得到真正有效的保養。
我們把生產使用部門進行的以“防止設備劣化”為中心的保養活動叫做“全員參加的自主保養活動”,通常就稱為自主保養。在自主保養活動中。為了充分地發揮設備的能力,必須實行“自己的設備由自己管理”,做一個能駕馭設備的人。因此,操作人員除應具備制造產品的能力外,還須具備以下四個方面的能力:
1、能發現異常的能力
能發現設備異常的“異常發現能力”,并不單純是已產生了故障或產生不良時才發現異常,而是當似乎要發生故障,似乎要產生不良時,能對這些故障原因之類的異常一目了然,只有這樣,才能稱作為真正的“異常發現能力”。
2、能正確地、迅速地處理異常的能力(處理復原能力)
對于已發現的異常現像,只有使之恢復至原來的正確狀態,才能發揮設備本來的功能,而且還應能根據異常的程度來決定是否向上級及維修保養部門報告,該怎樣處理。
3、條件設定能力
發現異常的能力常常取決于各人的水平和經驗,由于水平和經驗的不一,就可能影響對異常的發現。為了防止這種現像,就應該決定一個確定的量,以判斷設備是否正常。判斷基準應定量,以溫度為例,其定量應確定為“應在XX度以下”,而不能模糊地描述為“不得有異常的發熱”。這里要強調的是,與其重視判斷基準的正確度而延遲了執行,還不如先定一臨時基準,再多次修正,以定出更為合適的基準,這種方法更具現實意義。
4、維持管理能力
設備發生了故障再維修總沒有預防在先的好,為此,就必須確實地遵守既定標準,比如“清掃、加油標準”、“自主檢查標準”等。
能力是如何形成的,它主要靠工作中的不斷學習和積累,因此工作本身就是一種學習,由于能力的不斷提高它又可取得更多的工作成果,它們三者之間是一種相互依存、相互促進的關系。
要培養出能駕馭設備的操作人員,要形成自主保養的體制,一方面要注重人才的培養,另一方面要根據其實際能力對工作有切實的提高,以實現真正的效果,也即這個效果是能得到維持的。在開展自主保養時,不可寄希望于一下子解決許多問題,為此將目標和內容整理為7步,這就是“步進式自主保養”。理想的方法是,徹底地做到每一步,待達到一定程度,再進入下一步。
7步完成自主保養
第一步:初期清掃
初期清掃就是以設備為中心徹底清掃灰塵、垃圾等。我們要將清掃變檢查,檢查能發現問題,發現設備的潛在缺陷,并及時加以處理。同時通過清掃可有助於操作人員對設備產生愛護之心。
第二步:發生源、困難部位對策
為了保持和提高第一階段初期清掃的成果,就要杜絕灰塵、污染等的根源(發生源),為此可采取消除或加蓋、密封等對策。對難于維護保養的部位,如加油、清掃、除污等,也應采取有效對策,提高設備的可維護保養性。
第三步:編寫清掃、加油基準
根據第一、第二步活動所取得的體會,編寫一個臨時基準,以保養自己分管的設備,如清掃、加油,緊固等基本條件。
第四步:綜合檢查
為了充分發揮設備的固有功能,要學習設備結構、功能及判斷基準,檢查設備各主要部分的外觀,發現設備的缺陷并使之復原,同時使自己掌握必要的檢查技能。再者,對以前編寫的基準可考慮不斷完善,以利檢查。
第五步:自主檢查
在第三步編寫的清掃基準,加油基準,檢查基準的基礎上,加上第四步學到的內容,并完全遵照執行,這就是自主檢查基準。在學習和執行的過程中,還要不斷學習和熟悉設備的操作和動作,質量和設備等等的關聯性,具有正確操作設備和早期發現異常情況的能力。
第六步:整理、整頓
從現有的以設備為中心的活動向外圍設備、整個車間擴大活動范圍,在掌握了上述5步的能力的基礎上,發展為實現并維持整個車間應有的形象。本步所說的整理是指明了車間內的工夾具、半成品、不良品等,并制定出管理基準,應徹底減少物、事等管理對像,盡量簡化。所謂應徹整頓就是要遵守(維持)即定基準并逐步完善,以便作業人員易于遵守。車間實行目視管理和管理實行標準化。
第七步:自主管理的徹底化
通過以前6步的活動,已獲得了不少的成果,人員也得到了很大的鍛煉,所以這第七步就要建立起不斷改善的意識,不斷地進行PDCA循環,結合公司的方針、目標,制定出適合自己的新的小組活動目標,做到自主管理的徹底化。
-
設備
+關注
關注
2文章
4503瀏覽量
70610
原文標題:工廠設備天天壞!如何實現零故障?
文章出處:【微信號:AMTBBS,微信公眾號:世界先進制造技術論壇】歡迎添加關注!文章轉載請注明出處。
發布評論請先 登錄
相關推薦
零碳節能工廠是什么?有什么功能?如何實現? ?
TüV萊茵為天合光能頒發零廢工廠認證及零碳工廠核查聲明
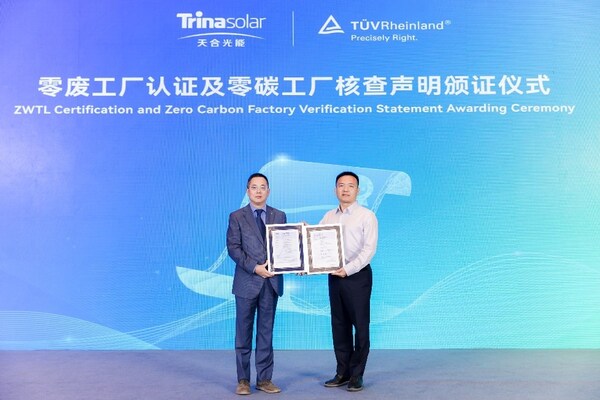
CNC智能工廠如何實現
工廠配電設備運行監控系統解決方案
如何解決工廠中相同IP設備沖突故障問題
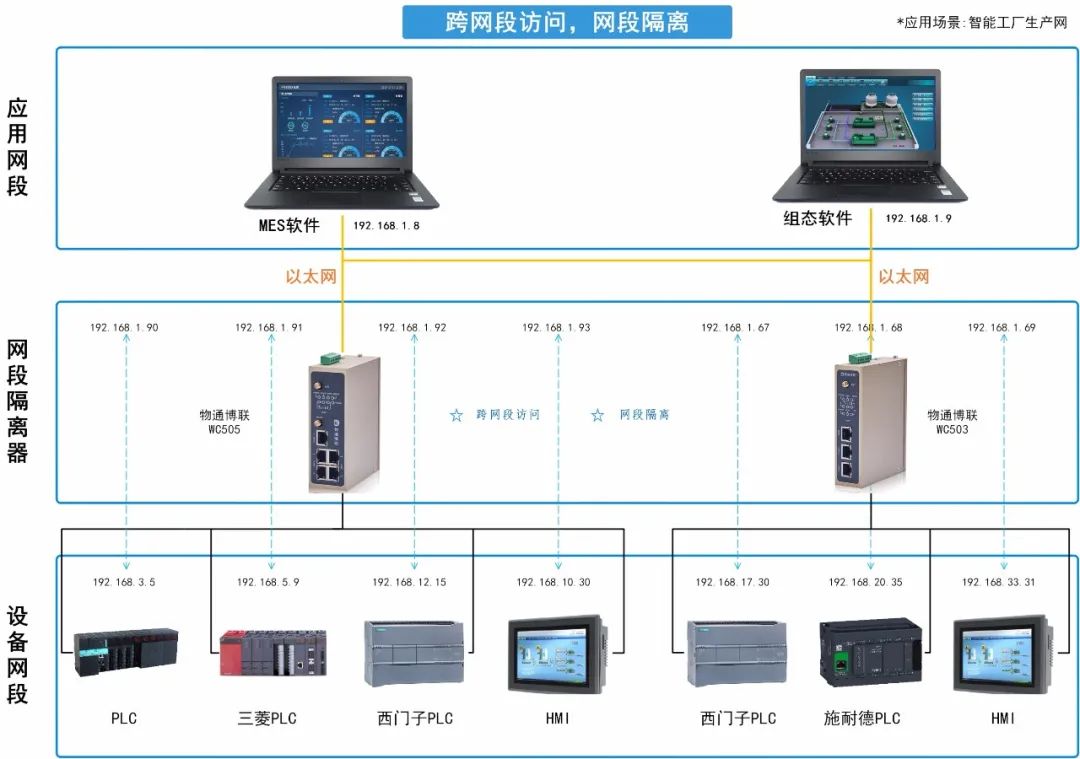
工廠設備遠程監控系統是什么?工廠設備遠程監控系統的功能特點
工業物聯網賦能智能工廠,助力企業實現設備智能運維管理
智能工廠解決方案(工業物聯網平臺有什么功能)
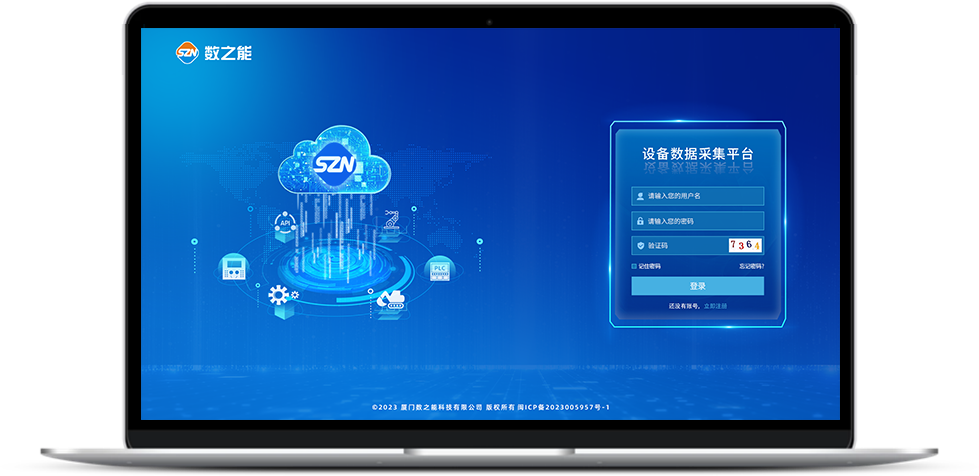
評論