半導體制造是一個復雜的行業,這個過程中任何地方的小改進都會對底線產生重大影響。本文討論了通過引入智能制造解決方案為半導體行業不斷優化制造的好處。
日益復雜的市場需求正推動著半導體晶圓廠(無論是集成設備制造商(如英特爾或三星)還是無晶圓廠/代工廠模式)尋求提高生產靈活性,上市時間和盈利能力的方法。引入新產品的步伐正在加快,開發,制造和部署產品到市場的復雜性也在增加。為了滿足這些需求,公司將產品設計和測試與制造聯系起來,以在閉環反饋周期內優化產品和過程。
數字化可以滿足減少周期時間,降低成本和提高產量同時增強創造力和創新的業務需求。數字化正在幫助解決跨組織和價值鏈擴展和協調的局限性。同樣,工程領域和垂直專業領域之間的界限也越來越模糊,因為公司充分利用了大數據的能力,并且在以前孤立的領域中水平地進行了分析。
但是,晶圓廠完全數字化和“智能化”意味著什么?智能制造與當今大多數半導體公司有何不同?每個晶圓廠將有自己的需求,并由量化的業務目標驅動不同的數字轉換切入點。智能制造已全面數字化,不僅在晶圓廠內部,而且在從設計到分銷的所有參與者之間,都提供了越來越多和更可靠的信息流。半導體中的智能制造不僅僅是晶圓廠中的連接設備。它涉及從概念和設計到制造和服務的流程優化。
智能工廠的各個方面
實現智能晶圓廠的周期時間,良率和成本效益意味著數字化連接整個制造過程生命周期。這遠遠超出了最現代的半導體制造執行系統(MES)及其跟蹤功能。盡管跟蹤和跟蹤的改進已基本到位,但在客戶為受管制設備(汽車,醫療,航空航天和國防,安全和生物識別技術)制造IC的推動下,將設計與制造相連接的技術才剛剛成為重要的資源。晶圓廠利用歷史和高級預測分析來提高晶圓廠性能。
智能化工廠概念化的一種方法是作為一個統一的協作平臺,該平臺包括產品,生產和性能的數字孿生子,而不僅僅是靜態模型。
數字孿生的這一概念已廣泛用于航空航天,國防和汽車等行業,以描述設計的產品。制造商可以基于數字雙胞胎的概念,以結構化,集成的方式將產品信息,決策和歷史聯系在一起,從而在整個產品生命周期中捕獲產品創新和知識。這被稱為數字線程,它使創新生命周期內的可追溯性成為可能。它還使在下游流程中重用設計變得更加容易,這不僅節省了時間,而且由于每個人都在使用單一的事實來源,因此提高了質量。最初,智能制造應該更專注于生產和績效的數字化線程,
一個智能半導體晶圓廠具有與MES集成的調度功能,可以創建一個環境,以便不斷更新資源受限的每個工作站下一步的操作視圖。當今的高級MES可以對復雜的流程建模,但它們還需要在可重復使用的工作流程中管理規格,方劑,掩膜和工具。
智能工廠的所有組件都需要進行自定義,以適應任何給定組織的特定需求。低代碼和無代碼應用程序開發平臺是關鍵組件。這些平臺使您能夠通過自定義軟件應用程序推動業務轉型。
如今,任何經驗水平的設計師都可以創建適合他們需求的應用程序。這將建立內部人員開發人員網絡,通過連接新舊系統,自動化流程并促進提供可操作情報的數據分析,來獲取洞察力并加快數字化進程。
封閉設計,構建和測試的循環
作為智能制造實現的一部分,有機會使用設計數據來提高產量和其他裕量因素。晶圓廠已經將產品設計與制造聯系起來,以通過制造設計(DFM)技術實現產品優化。制造測試結果中的數據還提供了降低成本,提高質量和產量所需的寶貴見解。
通過新一代的端到端軟件自動化,可以加速設計與制造之間的聯系。設計自動化軟件也許是智能晶圓廠中最不明顯的組件,但是為了創建更高效的IC制造,控制成本并為電子功能的持續改進創造空間,它變得越來越重要。在一個示例中,IC設計在生成掩模之前要經過物理驗證。使用機器學習算法分析該過程中的數據,并將其反饋給鑄造廠以優化設計流程。
設計與制造之間的聯系的另一個例子,也有助于建立一個開放的現代生態系統,來自IC測試分析。半導體技術和過程控制要求在數千種不同產品設計中具有可重現的原子級性能。在所有產品上始終如一的高產能力令人望而生畏。過去,良率由制程能力,使用測試芯片進行良率學習以及在晶圓廠進行制程監控來控制。如今,通過先進的機器學習算法對來自失敗的IC測試的數據進行了分析,以找出過去可能無法發現的良率限制因素。
捕獲良率限制器的概念也可以在上游擴展到實際制造設計(DFM)流程中,尤其是在光刻過程中,這是制造過程中的關鍵步驟。到晶圓廠發現嚴重的與光刻相關的問題時,為進行簡單的布局更改而在設計過程中為時已晚。為了避免或減少設計延遲,設計人員可以使用光刻模擬來檢測布局中的薄弱點,并分析光刻對設計的電氣性能的影響。
然后,工程師可以在設計流程的早期進行任何所需的調整。為此,必須有一種機制使設計人員能夠將光刻工藝知識納入其現有設計流程中。實際上,以光刻友好設計(LFD)套件的形式存在。LFD套件使IC設計人員可以評估布局對給定工藝的響應,然后糾正那些在制造過程中最有可能失敗的配置。這里利用機器學習算法來預測具有高檢測精度和覆蓋率的產量限制,同時減少總體運行時間。
收集,分析和使用這些數據是創建以智能制造為中心的全面數字孿生的一部分。它還需要基于信任和經過驗證的數據安全性的緊密合作伙伴生態系統。
設計公司需要了解其特定于設計的制造/產量挑戰的方法,而鑄造廠則需要設計數據以有效解決產品/過程的相互作用。制造測試數據與設計數據相結合可以提供強大的工具來解決一些最具挑戰性的原子級問題。沒有這些信息共享,生態系統將無法真正發展成為在全球半導體市場中競爭所需要的智能制造愿景。
現在開始智能半導體制造
半導體晶圓廠在實現智能制造方面處于領先地位,但是功能多種多樣,并且發展迅速。面對競爭壓力,半導體晶圓廠需要催化劑來實現并加速其數字化轉型。障礙依然存在,但是生態系統正在積極開發智能工廠所有組件的解決方案,從不但利用工廠中的物聯網,而且利用寶貴的設計數據的完整數字孿生子,到靈活的平臺和統一的生態系統,從而為買家,開發人員,設計師,生產單位,分包商,供應商等等。與經驗豐富的專業行業合作伙伴合作,將最佳地定位智能晶圓廠,以實現利潤和創新。
晶圓廠應尋求具有現成解決方案的供應商進行產品開發和制造,以加速實現真正的智能晶圓廠。例如,西門子的Xcelerator產品組合集成了軟件,服務和應用程序開發平臺,以幫助制造商全面數字化其運營以實現智能工廠的目標。邁向完全智能工廠的下一步將需要一定的機構意愿,投資,并需要與生態系統合作伙伴建立合作伙伴關系,而生態系統合作伙伴對于產品開發和制造擁有豐富的數字軟件產品組合。
責任編輯:tzh
-
半導體
+關注
關注
334文章
27516瀏覽量
219833 -
晶圓
+關注
關注
52文章
4931瀏覽量
128108 -
智能制造
+關注
關注
48文章
5576瀏覽量
76399 -
智能工廠
+關注
關注
3文章
1003瀏覽量
42448
發布評論請先 登錄
相關推薦
【「大話芯片制造」閱讀體驗】+ 半導體工廠建設要求
【「大話芯片制造」閱讀體驗】+跟著本書”參觀“半導體工廠
半導體制造行業MES系統解決方案
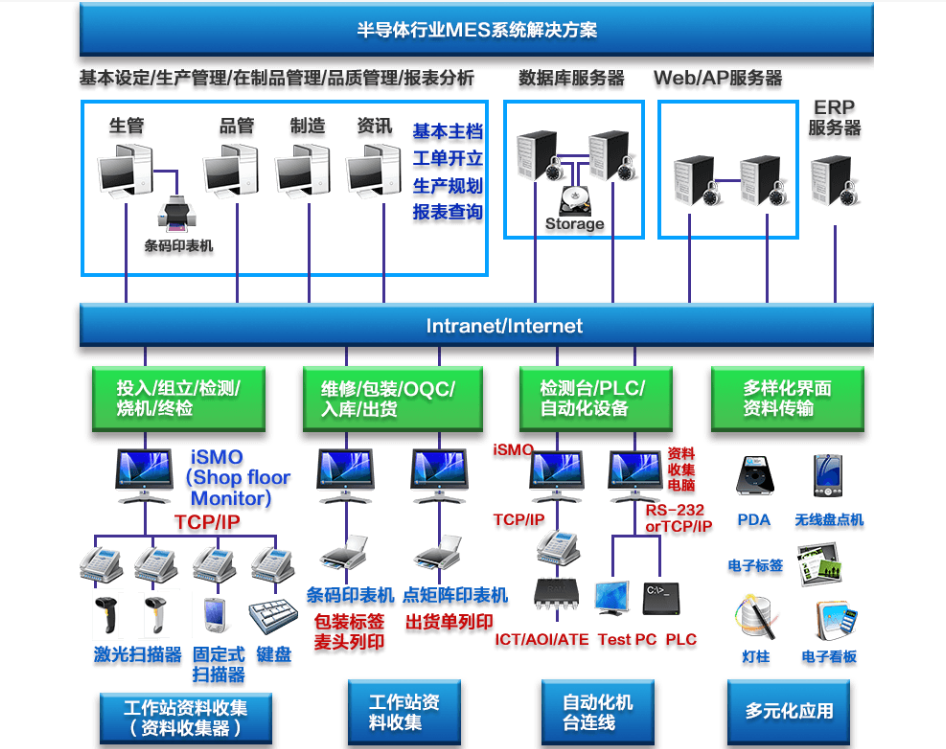
半導體的能帶理論
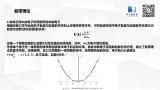
評論