看完Battery Day的內容,特別是涉及到電池設計到底盤設計的融合,我覺得這個方向上面是存在很大的距離,想要完成所謂的CTC Cell to Chassis的設計是需要有幾個先決條件的:
1)由車企來主導整個Giga Factory,從電芯生產到純電動整車生產,并且按照一定的數量,比如50萬臺產能配合單臺80kwh左右的量(40GWh)這樣的最小單元去布置
2)這種設計,一定是圍繞爆款來設計的,其實從MEB、BEV3、E-TGNA,重點還是各個傳統車企并不清楚什么樣的車才能達成爆款,所以要在平臺上用不同的電量、不同的車身結構和不同的細分市場去實驗
3)足夠的穩定性:由于整體的設計迭代,既要符合上面的從電芯到車輛的規格爆款,里面的技術迭代就不能快,不能投了那么多的設備和資金,從電芯的材料體系到尺寸輕易動。
因此從CTC這種思考,更多的是一種自然演進的過程,而不是你想要降本或者多塞電池的手段,特斯拉能做因為這款采用CTC的電動皮卡的熱情給帶起來了,而且在一個新工廠,新電芯新需求,還有個老板愿意去嘗試.。
第一部分 CTC帶來的收益
從直觀來說,在傳統的底盤設計中加入革命性的因素,核心的價值還是在皮卡需要更多的電池,我們從BEV3的皮卡800V+200kwh的設計中能看到這方面的訴求。在純電動皮卡的細分領域,Rivian、福特、通用還有后續Canoo這樣的公司都在嘗試全新的設計。
圖1 在單層結構上層疊2層實現的200kwh的皮卡電池
圖2 Canoo的電芯和底盤集成
所以這個設計思路,就是從車身結構、底盤和電芯布置上,整體性的進行大的跳躍,看下面這個圖,一改之前的大模組的結構,所有的電芯按照矩陣式排列放在下面的托盤上。
圖3新型電芯搭配的整塊設計
從這里可以看到,其實最大的變化,就是里面電芯布置結構的約束變少了,先給你所有的空間用來布置電芯,然后從整體去考慮碰撞、底部保護等,優先是在同等的空間下塞入足夠的電芯和足夠的能量。在這里空間上的變化最大,中間的梁、兩邊的梁還有上蓋的空間都節約出來了,給你裝入足夠多的電池。
圖4 電芯式直接整塊整合
第二部分:為什么短期內CTC很難讓人踐行
我覺得集成方式的結構,最直接的影響就是生產方式:
1)標準化模組:不管是之前的390模組還是目前大家看到的590模組和各個其他車企定義的模組尺寸,電芯生產和車輛的工廠是可以分離,產能的匹配在各個地區是可以調節的。
2)CTP設計:從CTP設計的第一階段,16-24個電芯做出來的大模組,這個模組的生產方式就已經改變了原有的分工,由于模組的重量還有電壓,其實并不特別適合遠距離的運輸,所以它把Pack生產也隱含在了里面。隨著CTP的減重深入,這個趨勢特別明下。
3)如果到了CTC階段:特斯拉整個圓柱電芯都需要在一個底部支撐部件上進行,所有的做完以后直接把這個東西和車體進行整合,來解決結構固定和密封問題,使用車身下地板作為上蓋密封,整個電池包也變成了不容易運輸的部件,從制造角度,那真的是必須持續有訂單,電芯=》底盤直接生產。
而在設計開發里面,我們能看到的好處,就是減重,得到了更多的空間,失去的最大的問題還是靈活性,需要圍繞一個車型來布置和優化。這直接帶來車企內部組織架構的變化,分工的變化,這方面特斯拉這樣隨時能調整的企業還是有開先河的資本的。
小結
我覺得這個事情在乘用車的滲透,可能會比想象的更慢,說到底還是賭爆款車型,CTC技術更像是一種順勢而為的結果而不是用來出爆款車型的手段。
責任編輯:YYX
-
電動
+關注
關注
2文章
273瀏覽量
26430 -
特斯拉
+關注
關注
66文章
6311瀏覽量
126548 -
電芯
+關注
關注
14文章
723瀏覽量
25853
原文標題:【聚創新能源?總工札記】CTC技術的應用場景
文章出處:【微信號:weixin-gg-lb,微信公眾號:高工鋰電】歡迎添加關注!文章轉載請注明出處。
發布評論請先 登錄
相關推薦
DAC348X EVM的I路輸出電路,畫圈的那一部分有什么作用?0L電感L40有什么作用?
恩智浦助力打造靈活可擴展的電動汽車充電樁
特斯拉在墨西哥交付Cybertruck電動皮卡
特斯拉對電動皮卡Cybertruck推出增程電池服務
多口適配器-現代生活中的不可或缺的一部分
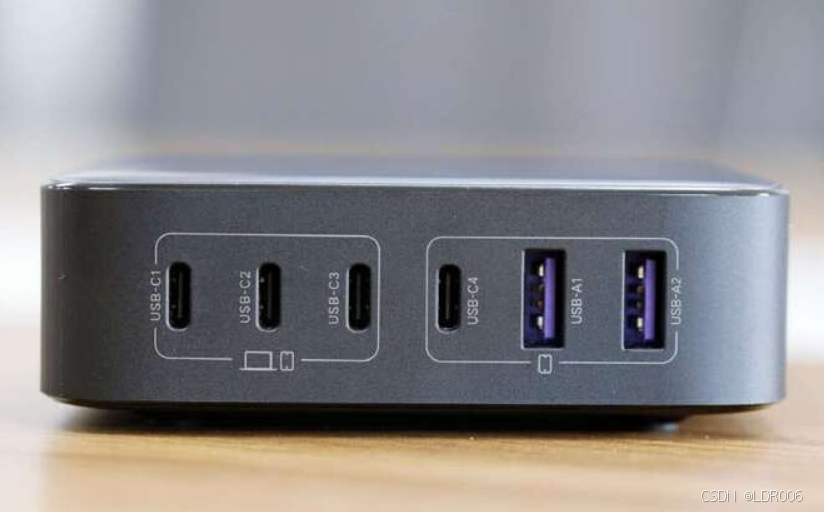
評論