1.印制電路板的制作
印制電路板的制作過程分為:底圖膠片制版、圖形轉移、腐刻、印制電路板的機械加工與質量檢驗等。
(1)底圖膠片制版
1)CAD光繪法
這種方法是應用CAD軟件對印制電路板進行布線后,使用獲得的數據文件來驅動光學繪圖機,使感光膠片曝光,經過暗室操作制成原版底圖膠片。
2)照相制版法
照相制版法是先進行黑白底圖的繪制,再將繪制好的印制電路板黑白底圖,通過照相進行制版的方法。
(2)圖形轉移
把相版上的印制電路圖形轉移到覆銅板上,稱為圖形轉移。
具體方法有絲網漏印、光化學法。
1)絲網漏印法
絲網漏印法是指:將所需要的印制電路圖形制在絲網上,然后用油墨通過絲網模版將印制電路圖形漏印在銅箔板上,形成耐腐蝕的保護層,經烘干、修版后,實現圖形轉移。
2)光化學法
目前,在大批量的印制板生產中,大多采用光化學法即直接乳劑制板法制作圖形。如圖10所示。
圖10光化學法工藝流程
(3)腐蝕技術(腐刻)
腐蝕是指利用化學或電化學方法,對涂有抗蝕劑并經感光顯影后的印制電路板上未感光的部分,進行腐蝕去除銅箔,在印制板上留下精確的線路圖形的過程。
腐蝕方法有搖槽法、浸蝕法和噴蝕法三種。
搖槽法最簡單,所用的設備是一只放腐蝕劑的槽,裝于不斷搖動的臺面上。
浸蝕法是將工件浸沒在盛有能保溫的大槽中蝕刻。
噴蝕法生產速度較快,用泵將腐蝕劑噴于印制板表面進行腐蝕加工。
2.工業制板
實際生產中,制造印制板要經過幾十道工序。主要有:
(1)繪制照相底圖
照相底圖是用來制作照相原版或生產底板的。大多數的底圖是由設計者繪制的,早期的印制電路板生產是手工布線貼圖,效率低、精度低、周期長。隨著計算機及其應用軟件的發展,目前,工程技術人員可以利用CAD/CAM軟件來輔助設計、輔助生產印制電路板。大大提高了生產效率和制板質量。
(2)照相制版
照相制版就是得到原版底片。用繪制好的制板底圖照相制版,版面尺寸應與PCB尺寸一致。制板過程與普通照相大體相同,可分為軟片剪裁→曝光→顯影→定影→水洗→干燥→修版。
制版時,先按一定的比例將原圖放大,然后再運用縮微照相技術將放大的原圖通過光學系統縮小到原來的尺寸,成像在銀鹽感光材料上。再經過顯影等一系列加工處理,就得到了“原版”,或稱為“母版”。一般母版為“負像”。
(3)圖形轉移
把相版上的印制電路圖形轉移到覆銅板上,稱圖形轉移,它是PCB制作過程中很重要的一道工序。根據圖形轉移后所得到的電路圖形與所需要的電路圖形是否一致,可分為“正像”和“負像”。
圖形轉移的方法很多,常用的有絲網漏印法和光化學法等。
1)絲網漏印
絲網漏印(簡稱絲印)是一種古老的印制工藝,與油印機類似。絲網漏印就是在絲網(真絲、滌綸絲等)上通過貼感光膜(制膜、曝光、顯影、去膜)等感光化學處理,將圖形轉移到絲網上,或在絲網上黏附一層漆膜或膠膜,然后按技術要求將印制電路圖制成鏤空圖形。然后通過刮板將印料漏印到覆銅板上,于是在覆銅板上便得到所需的電路圖形。這些印料經紫外光(或加熱)固化后,便具有各種不同用途的良好抗蝕性能。
絲印時所使用的“印料”常稱為“抗蝕油墨”,種類很多,常用的有抗蝕印料、耐電鍍印料、阻焊印料、字符印料和防護層印料等。
絲網漏印可以通過手動、半自動或自動絲印機實現。圖11是最簡單的絲網漏印裝置,工作時只需將覆銅板在底板上定位,將印制材料放到固定絲網的框內,用橡皮板刮壓印料,使絲網與覆銅板直接接觸,即可在覆銅板上形成由印料組成的圖形,然后烘干、修版。
圖11絲網漏印
2)光化學法
光化學法有直接感光法和光敏干膜法兩種。
①直接感光法。其工藝過程為覆銅板表面處理→涂感光膠→曝光→顯影→固膜→修版。修版是蝕刻前必須要做的工作,可以對毛刺、斷線、砂眼等進行修補。
②光敏干膜法。工藝過程與直接感光法相同,只是不是涂感光膠,而是用一種由感光性齊聚物(或共聚物)、粘合劑、光引發劑、增塑劑、穩定劑、著色劑及溶劑等成分組成薄膜作為感光材料。這種薄膜由聚酯薄膜、感光膠膜、聚乙烯薄膜三層材料組成,感光膠膜夾在中間,使用時揭掉外層的保護膜,使用貼膜機把感光膠膜貼在覆銅板上。
(4)蝕刻
蝕刻也稱爛板。是生產過程的一個重要環節,它的成敗關系到印制電路板的后續工序。它是利用化學方法除去板上不需要的銅箔,留下組成圖形的焊盤、印制導線及符號等。蝕刻劑有許多種類,常用的蝕刻溶液有酸性氯化銅、堿性氯化銅、三氯化鐵等。
三氯化鐵(FeCl3)在電子學、印制電路、照相制版、金屬精飾等加工和生產中,被廣泛用作銅、銅合金、Ni-Fe合金及鋼的蝕刻劑。它適用于絲網漏印油墨、液體光致抗蝕劑和鍍金印制電路版電路圖形的蝕刻。用三氯化鐵為蝕刻劑的蝕刻工藝流程如下:
預蝕刻檢查→蝕刻→水洗→浸酸處理→水洗→干燥→去抗蝕層→熱水洗→水沖洗→(刷洗)→干燥→檢驗。
氯化銅(CuCl2·2H2O)作蝕刻劑,具有配方簡單、蝕刻速度快、溶銅量高、穩定性好、產品質量可以得到保障、能機械化連續生產、溶液再生和銅的回收容易、對環境的污染可以得到有效的控制等突出優點,在印制電路板生產中得到了迅速地推廣,目前生產中已作為首選蝕刻劑,取代了三氯化鐵蝕刻劑。
氯化銅蝕刻劑根據印制板的制作方法不同,又分為酸性和堿性兩種,酸性氯化銅蝕刻劑適用于絲網漏印及多層板內層電路的制作工藝。堿性氯化銅蝕刻劑適合于鍍焊料(錫-鉛)保護層的單面、雙面及多層印制外層電路的制作工藝。
(5)金屬化孔
金屬化孔工藝為下一步的電鍍加厚銅層打下基礎,實現良好的電氣互連,金屬化孔不好就會造成孔內無銅或是有很薄的銅層,一經通斷試驗就造成開路。
金屬化孔是連接多層或雙面板兩面導電圖形的可靠方法,是印制電路板制造技術中最為重要的工序之一。雙面印制電路板兩面的導線或焊盤要連通時,必須通過金屬化孔實現。它關系到多層板內在質量的好壞,其主要工作是在多層板上鉆出所需的孔、把孔內的鉆污去除、在孔壁上沉積上一層導電金屬銅,使原來非金屬的孔壁金屬化,也稱沉銅。在雙面和多層PCB中,這是一道必不可少的工序。
金屬化孔的質量對雙面PCB是至關重要的,金屬化孔要求金屬層均勻,完整,與銅箔連接可靠,電性能和機械性能符合標準。在表面安裝高密度板中這種金屬化孔采用盲孔方法(即沉銅充滿整個孔)以減小過孔所占面積,提高密度。
目前的金屬化孔主要有三類:埋孔、盲孔和過孔,埋孔是無法從基板外部看到,孔存在于基板內層,為先鉆并鍍覆孔后,再壓合加工完成。盲孔是可以從基板的一個外表面看到,是先壓合再鉆孔的沒有貫穿基材的孔。過孔是可以從基板的兩個表面都能看到,是先壓合再鉆孔的貫穿基材的孔。如圖12所示。
圖12多層撓性線路中的過孔、埋孔和盲孔
所謂沉銅就是化學鍍銅。它是一種自催化氧化還原反應,在化學鍍銅過程中Cu2+得到電子還原為金屬銅,還原劑放出電子,本身被氧化。其反應實質和電解過程是相同的,只是得失電子的過程是在短路狀態下進行的,在外部看不到電流的流通。因此化學鍍是一種非常節能高效的電解過程,它沒有外接電源,電解時沒有電阻壓降損耗。化學鍍銅時可以一次浸入到化學鍍銅液中進行鍍銅,而用電鍍法是無法做到的。化學鍍銅可以在任何非導電的基體上進行沉積,利用這一特點在印制板制造中得到了廣泛的應用。應用最多的是進行孔金屬化。
金屬化孔的工藝流程如下:
鉆孔板→去毛刺→去鉆污→清潔調整處理→水洗→粗化→水洗→預浸→活化處理→水洗→加速處理→水洗→化學鍍銅→二級逆流漂洗→水洗→浸酸→電鍍銅加厚→水洗→干燥。
由于化學鍍銅溶液中的甲醛對生態環境有危害,并且有致癌的潛在危險,同時化學鍍銅溶液中的絡合劑(如EDTA等)不易進行生物降解,廢水處理困難。因而直接電鍍技術近年來得到了迅速的發展和應用。
(6)金屬涂覆
金屬涂覆就是采用化學鍍和電鍍的方法,在PCB的銅箔上進行表面涂覆,以提高印制電路的可焊性、導電性、耐磨性、裝飾性及延長PCB的使用壽命,提高電氣可靠性。涂覆工藝主要應用在表面貼裝雙面、多層印制電路板上。常用的涂覆層材料有金、銀、銅和鉛錫合金等。
1)鍍銅
鍍銅是PCB制造的基礎技術之一,鍍銅分為全板電鍍(化學鍍銅后加厚銅)和圖形電鍍,其中全板鍍銅是緊跟在化學鍍銅之后進行,而圖形電鍍是在圖相轉移之后進行的。
①全板電鍍方法可用于制造寬度和間距要求不太嚴格的印制電路板。全板電鍍的工藝流程如下:
化學鍍銅→活化→電鍍銅→防氧化處理→水沖洗→干燥→刷板→印制負相抗蝕圖象→修版→電鍍抗蝕金屬→水沖洗→去除抗蝕劑→水沖→蝕刻。
②圖形電鍍是對導電圖像進行選擇性的電鍍。一般有兩種情況:一種方法是先用化學鍍提供0.5~1.0μm的導電銅層,然后全板電鍍銅,使其鍍層厚度達到5μm左右。
圖形電鍍銅是在圖像轉移后進行的,一般是作為鉛錫或錫鍍層的底層,也可作為低應力鎳層的底層。在自動線生產中,圖形電鍍銅與電鍍錫鉛合金(或錫)連在一條生產線上。其工藝過程如下:
圖像轉移后印制板→修板/或不修→清潔處理→噴淋/水洗→粗化處理→噴淋/水洗→活化→圖形電鍍銅→噴淋/水洗→活化→電鍍錫鉛合金
└→鍍低應力鎳→鍍金
2)鍍鎳/金
為了提高耐磨性(插拔時),減低接觸電阻,防止氧化(銅)和提高連接可靠性。通常在PCB插頭(俗稱“金手指”)和某些特殊部位鍍耐磨的Au-Co或Au-Ni。插頭電鍍鎳與金一般由自動生產線來完成。其工藝流程如下:
上板→清洗→微蝕→刷洗→活化→漂洗→電鍍→低應力鎳→漂洗→活化→漂洗→電鍍金→金回收(用)→漂洗→烘干→下板。
還可以用浸鍍和化學鍍的方法進行鍍鎳和金。
3)電鍍錫/鉛合金
電鍍錫/鉛合金大多是在與電鍍銅組成的自動生產線上來進行的。錫/鉛合金層除了作耐堿抗蝕劑外,還用作可焊層(經熱油熱熔或紅外熱熔后)。由于經過熱油和紅外熱熔的Sn/Pb合金層厚度較厚,易形成龜背現象,因而不適用于表面安裝技術,目前電鍍錫/鉛合金層主要是用來作耐堿抗蝕劑。
4)化學鍍錫
為達到良好的焊接性能,適應環保的需要,消除錫鉛合金中鉛的含量,通常單獨使用化學鍍錫的工藝。
錫具有良好的導電性和釬焊性。在銅基體上化學浸錫,就是使表面銅層與錫液中錫離子發生置換反應。當錫層形成后,反應立即停止。
(7)涂助焊劑與阻焊劑
PCB經過圖形轉移、蝕刻、去膜和表面金屬涂覆后,在裝配元器件之前,應根據不同需要進行助焊或阻焊處理。涂助焊劑可提高可焊性;而在高密度鉛錫合金板上,為使板面得到保護,確保焊接的準確性,可在板面上加阻焊劑,使焊盤裸露,其他部位均在阻焊層下。
助焊劑在焊接過程中,能與基金屬表面及焊料表面的各種化合物發生化學反應,生成可溶(熔)性的化合物。在這一過程中,助焊劑起到了凈化基金屬與焊料表面并防止空氣再次對金屬表面氧化的作用。
阻焊是指將焊盤和焊接部分以外的其余部分(包括圖形導線和基片)全部都涂一層阻焊保護印料。這層保護印料在裝配好的印制電路板進行“波峰焊’’時,可防止導線間發生“橋連”現象,能有效地提高焊接質量,降低廢品率。同時又可節省焊料,減輕印制電路板的重量,降低成本。阻焊印料是永久性的涂料,焊接后不需去除,對印制電路起到永久性的保護作用。
阻焊涂料按固化條件分熱固化型和光固化型兩種,色澤為深綠或淺綠色。PCB上還有表示各元器件的位置、名稱等的文字及符號,一般是采用絲網漏印的方法印上去的,常見的為白色。
(8)熱熔鉛錫
印制電路板電鍍錫鉛后,鍍層和銅箔結合并不牢固,電路圖形外面的Sn-Pb合金鍍層為薄片狀和顆粒狀,為多孔狀結構,外觀呈暗灰色。它在加工過程及以后的焊接工藝中,易氧化變色,而影響其可焊性。為此,它必須進行熱處理。把它加熱到Sn-Pb合金鍍層的熔點以上,使這一鍍層的合金再熔化,促進熔融狀態的合金與基體金屬合金化,同時使鍍層變為致密、光亮、無針孔的結構。這一過程通常稱為“熱熔”。
印制電路板熱熔的方法有紅外熱熔、熱油熱熔、蒸汽冷凝熱熔、熱空氣熱熔四種。目前生產上廣泛采用的是紅外熱熔和熱油熱熔。通過紅外線或甘油浴使鉛錫合金在190℃~220℃溫度下熔化,充分潤濕銅箔而形成牢固結合層后再冷卻。
(9)熱風整平
熱風整平技術近年來發展很快,它實際上是將浸焊和熱風整平二者結合起來了,熱風整平時,先把清潔好的印制電路板浸上助焊劑,隨后浸在熔融的焊料里浸涂焊料,然后使印制電路板從兩個風刀之間通過,用風刀的熱壓縮空氣使錫鉛合金熔化,并把印制電路板上的多余焊料吹掉。同時排除金屬化孔里的多余焊料,使印制導線表面上沒有焊料堆積,也不堵孔,從而得到一個光亮、平整、均勻的的焊料涂覆層。
(10)清洗
印制電路板在制造及裝焊過程中,由于各種污染因素的存在,導致印制導線和元器件引線的腐蝕、造成短路等現象,嚴重影響印制電路的可靠性。因此,必須對各種印制電路及印制電路組件(PCA)進行嚴格的清洗,以除掉助焊劑殘渣、防氧化油、焊料污染物和其他各種污染物,特別是助焊劑殘渣等。一般來說,印制電路板清洗后其清潔程度應滿足MIL-P-28809標準。
常用的洗滌劑是氟碳清洗劑,主要工藝方法是:氣洗-噴洗-氣洗-干燥。
由于氟碳溶劑對臭氧層的危害,目前各國正考慮用新材料和新技術來替代氟碳溶劑的清洗。同時免清洗技術也逐步推廣開來。實現免清洗工藝可采用兩種方法:一種是采用低固態焊劑,另一種是在惰性氣體中焊接。
3.印制電路板質量檢測
在完成機械加工后,應對印制電路板進行質量檢驗。檢驗的主要項目包括:目視檢驗、連通性試驗、絕緣電阻的檢測、可焊性檢測等。
(1)目視檢驗
目視檢驗是指用肉眼檢驗所能見到的一些情況。通常目檢能發現一些包括導線是否完整、焊盤的大小是否合適、焊孔是否在焊盤中間等明顯的表面缺陷。
(2)連通性試驗
對多層電路板要進行連通性試驗,以查明印制電路圖形是否是連通的。這種試驗可借助于萬用表來進行。
(3)絕緣電阻的檢測
測量印制電路板絕緣部件對外加直流電壓所呈現出的電阻即為絕緣電阻。
在印制板電路中,此試驗既可以在同一層上的各條導線之間來進行,也可以在兩個不同層之間來進行。
(4)可焊性檢測
可焊性檢測是用來測量元器件連接到印制板上時,焊錫對印制圖形的附作能力。一般用附作、半附作、不附作來表示其可焊性。
責任編輯人:CC
-
印制電路板
+關注
關注
14文章
963瀏覽量
41512 -
電路板
+關注
關注
140文章
5086瀏覽量
101424
發布評論請先 登錄
印制電路板設計規范
印制電路板的設計基礎
印制電路板故障排除方法(光繪底片制作)
印制電路板基礎知識點匯總_印制電路板制作過程
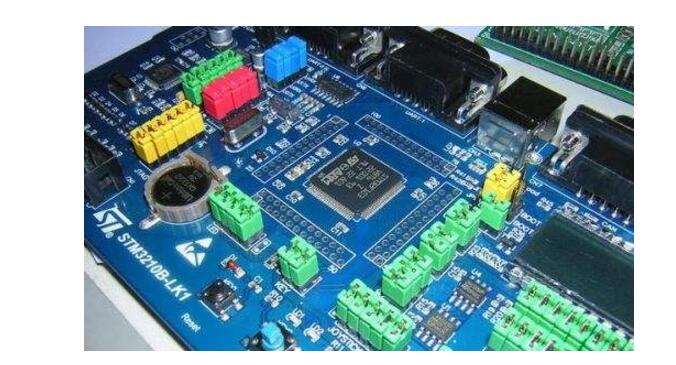
印制電路板的質量要求_印制電路板的原理
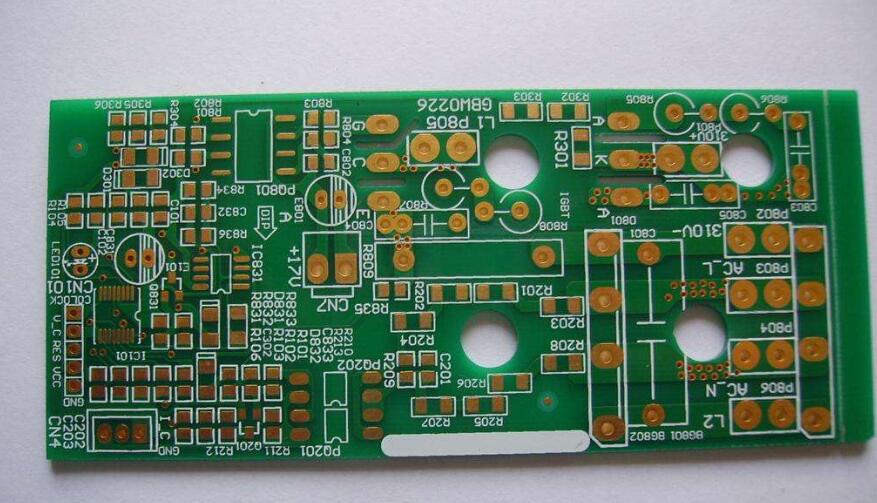
為什么叫印制電路板?印制電路板來由介紹
印制電路板設計心得體會_設計印制電路板的五個技巧
簡單DIY印制電路板設計制作過程
印制電路板的一般布局原則_印制電路板前景
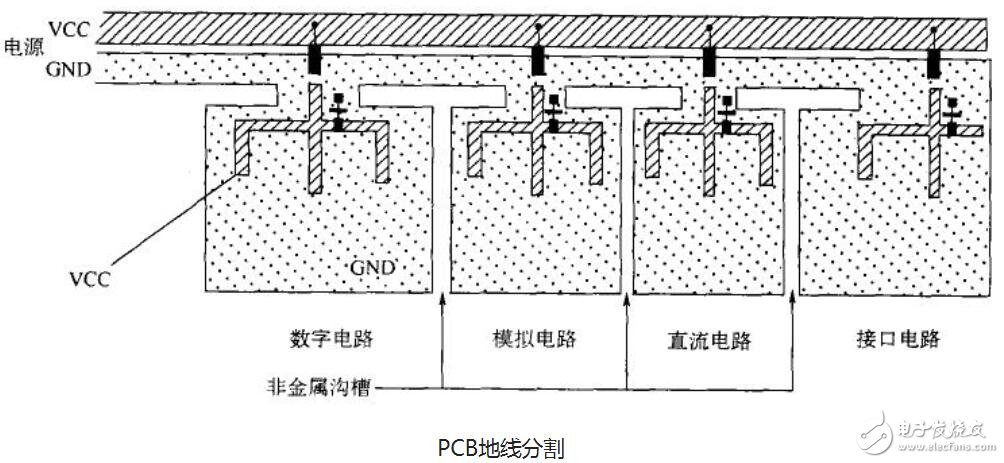
評論