翻譯自——semiengineering
傳感器的大規模應用和機器學習的發展讓集中測試在一些影響力較大的領域成為了可能。
機器學習和集成電路制造設備中結合了更多的傳感器,這為晶圓廠和封測代工廠對于針對性測試和更快吞吐量創造了新的可能性。
這種做法的目的是為了提高質量,降低制造復雜芯片的成本。在最先進的節點上,制造復雜芯片所需的時間正在增加。隨著晶體管數量的增加,更多的芯片被添加到電路板或封裝中,這導致了需要更多的時間去測試這些器件,也增加了總體成本,如果測試時間保持不變,就會降低被測設備在其生命周期內的可靠性。
所以,我們有必要區分哪些設備確實需要徹底測試,哪些設備已經在硅材料中得到了充分的驗證。這相當于對一個測試套件進行修剪,但是這個需要收集足夠有用的數據來進行調用。在過去這很難做到,但是隨著更多傳感器的參與,生成了更多的數據,我們就可以更細致的查看數據并從中進行有效識別模式。
PDF solutions公司表征解決方案副總裁DennisCiplickas說:“如果能建立一個準確率達到99.99%的模型來預測芯片何時會老化,那么你就可以跳過芯片老化的過程,從而節省成本。”
不管你設定的比例是多少,20%、30%或50%的跳躍率都可以,這將節省老化成本。而且數據越多,預測就越準確。
困難在于如何連接正確的數據來實現這一點。所以如果你所有的數據都在封測代工廠上運行,從晶圓排序、組裝,到最后的測試都在那里,你就可以整合所有的數據并從中做出預測。但如果你在不同的地方進行的這些工序,那就必須從多個地點合并數據,這就需要一個系統來做到這一點。”
老化測試用于檢測芯片中各種元件的早期故障。在過去,這類數據是通過數據交換共享的,雖然有用,但還不足以消除測試。
Ciplickas說:“最初,數據交換網絡背后的初衷是建立一個數據庫,這樣你就可以看到你的供應鏈。”“機器學習現在可以讓你把許多不同的功能放在一起,來做一些新的事情,比如預測。”所以通過從傳感器獲得的數據,就可以控制老化成本。下一個步驟是使數據能夠以連貫、連接的方式一起流經不同的站點,通過這些來進行預測。”
實際上,這就是一種將全流程的各種組件描述的更加精細,并精確地消除不必要的測試。
OptimalPlus副總裁兼總經理Doug Elder表示:“現在,你可以在進行晶圓排序和最終測試的豎井中連接所有數據源,以確定故障來自何處。你可以減少你的測試集和疑似老化的區域,你也可以運行機器學習算法來修復測試和改進你的方法。”
在過去,在現場實施之后,可能需要幾個月或幾年的時間才能顯現出生產問題。其中一些問題可以通過軟件來解決,比如智能手機的天線問題,在技術被取代之前,這些問題一直運行良好。但隨著越來越多的芯片被用于工業和汽車應用上,這種方法已經不再適用。
Elder表示:“如果你能在檢查中或老化階段發現這些問題,那么你就能將老化測試時間減少10%到20%。”“這對制造商來說是個很大的數字。
在實時情況下,通過查看自適應測試時間的減少量,估測哪些測試沒有失敗。這樣就可以減少測試時間,并且你可以通過一個閉環系統將其添加回測試循環中,該系統可以包含從晶圓排序到最終測試的所有內容。此外,重新測試也會增加我們的額外成本。但在損壞之前,你能重新測試多少次呢?其中一個案例:一個設備被重新測試了17次,直到最終通過測試。”可以看出,這對正在測試的設備來說并不是好事,既昂貴又耗時。在晶圓廠,每分每秒都有成本。
更好的數據,更好的結果
“好的”數據在不同的市場可能意味著不同的東西,甚至常常在同一個市場中也是如此。數據之所以有用,是因為它對特定的操作、過程或設備都有效。但需要大量的專業領域知識來做此決定。
yieldHUB首席執行官John O’Donnell表示:“我們發現一些較小的公司并不是在每個領域都有專長。”“尤其是在汽車領域,有些公司可能在設計方面很強大,但在測試方面就沒那么精通。”這就給復雜的芯片設計帶來了一個問題,久而久之,對芯片來說,問題將變得更加關鍵。但它也突顯了貫穿整個設計到制造鏈的一個挑戰,即確保參與其中的人都能理解其他工序的工作。
“有人可能會問,‘我們真的需要把時間花在這塊嗎?重要的是團隊中的每個人都必須看清這一點,”Donnell解釋到:“你可能是某個芯片特定部分的專家,而不是另一個部分的專家,所以你就需要合作和分析,還要在知識庫中進行維護。這使得你對特定領域有了足夠的信心,你可以將你的知識添加到系統分析中,以此減少測試數量所需的成本。
確保數據質量的另一種方法是對數據進行連續饋送。因此,與所有外部數據不同,其中一些數據可以在設備運行時進行測量。
proteanTecs的首席執行官Shai Cohen說:“有了在線數據,你就能不斷提高性能,做出正確的決定。”“在工序和內存中你都可以權衡參數缺陷。這提供了很高的覆蓋率,但是你需要添加多維代理,這些代理可以通過機器學習進行測量和處理。現在你可以為特定的設計配備代理,重建數據,以便更好地了解正在發生的事情。”
空空如也,垃圾滿天飛
傳感器不夠精確,不要緊。以波音737 MAX為例,故障傳感器可能是兩起墜機和一系列恐慌背后的罪魁禍首。其中一個問題是,數據需要更廣泛地共享,才能識別錯誤,而系統供應商往往將這些數據作為競爭優勢加以保護。
"在測試方面,我們一般遵循標準化的測試去設計芯片,但原始設備制造商對此缺乏足夠的信任。“National Instruments運輸部門首席解決方案經理Doug Farrell表示。“他們不愿意分享數據,這種情況必須改變,因為你不可能在一家公司里擁有一切。在自動駕駛方面尤其如此,一級汽車制造商和原始設備制造商正在進行激烈的競爭。”
所以我們只有不斷的測試傳感器,以確保數據的質量。
Farrell說:“對于操作車隊的人來說,他們可以在換班結束時對傳感器進行診斷,并對其進行校準。”“好多公司跳過了中間步驟,直接從純粹的模擬轉向將傳感器安裝在汽車上,因此診斷是必不可少的。”
為防止將來出現問題,數據本身也要存儲。
PDF的Ciplickas說:“我們試圖避免的是無聲數據的破壞。”“當這種事發生的時候,你無法預測。”
對于安全關鍵型應用程序,結果可能比這糟糕得多。現在,這些設備的功能帶來了責任,而數據是確定哪里出了問題以及原因的最佳方法。
OptimalPlus電子部門總經理Uzi Baruch表示:“汽車行業與半導體行業的根本區別在于,測試只是汽車行業的一個載體。”“這比你通常在半導體行業看到的要多,不僅限于電子產品,這是一條完整的裝配線,有多個接觸點。”
設計檢查
檢查在高級節點和某些類型的高級封裝中變得越來越困難。因此,人們要在更多的地方安裝更多的傳感器——無論是在設備中還是在封裝中——并要使這些傳感器更小、更快、功耗更低。
CyberOptics首席執行官Subodh Kulkarni表示:“目前晶圓廠和封測代工廠已經在進行抽樣檢測。”“現在我們正在對封裝進行功能檢查。問題是在我們進行100%的檢查之前會有多少放射性塵埃。但由于封裝太貴了,有必要對其進行合理的成本檢查。”
隨著新材料的引入和新結構的加入,這種檢查會變得更加困難。此外,由于漫射光不同于其他物質,所以不同的材料需要不同的檢查技術。Kulkarni指出,這兩種方法都需要重新校準光學攝像機等檢查設備。
他說:“這讓先進的封裝檢驗和模塊檢驗變得越來越困難,尤其像HBM。”“在過去,2D檢查就足夠了。現在你需要對存儲模塊進行3D光學檢查。”
這將花費更多的時間,生成更多需要分析的數據。
結論
在制造業中,將傳感器數據和機器學習結合使用的方法剛剛興起,但是提高質量和減少測試時間的機會是巨大的。這也有助于減少冗余的設計,這在部件、功率和重量方面都是難能可貴的。
proteanTecs首席商務官RaananGewirtzman表示:“我們的目標是終止增長的冗余。”對于ISO 26262規定尤其重要,因為它需要一定程度的冗余。但我們可以通過增加更好的測量代理來解決。”
這需要用一種完全不同的方式來看待和使用數據,但是以更少的成本提供更好的覆蓋范圍的前景得到了多方的關注,最大的問題是這種方法能擴展到什么程度。
審核編輯 黃昊宇
-
傳感器
+關注
關注
2551文章
51177瀏覽量
754294 -
ML
+關注
關注
0文章
149瀏覽量
34667
發布評論請先 登錄
相關推薦
測試壓阻式壓力傳感器性能的方法
壓力傳感器怎么測試好壞
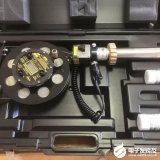
傳感器的響應時間對測量結果有何影響?
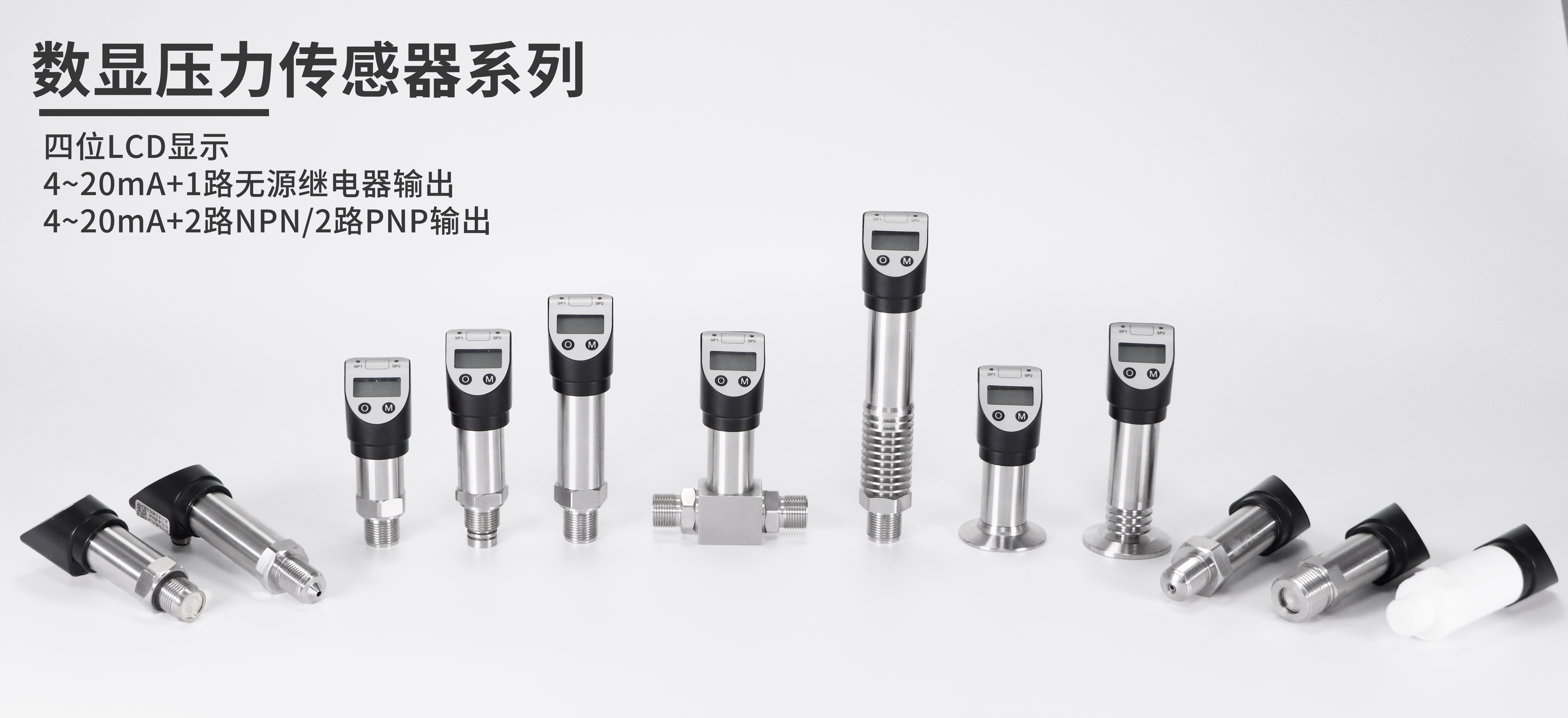
溫度傳感器的響應時間影響因素
工業溫度傳感器的優缺點 溫度傳感器在智能家居中的應用
CMOS與傳統傳感器的成本比較
Sensirion 推出迄今極具成本效益的溫度傳感器
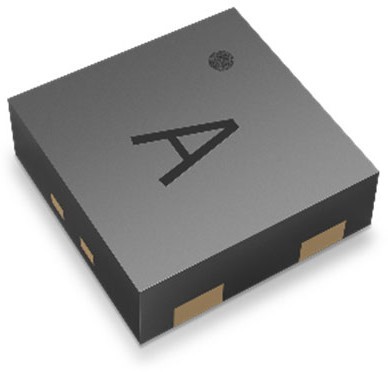
評論