Hi 小伙伴們,上一篇我們講了關于散熱的一些應用基材,這一篇我們將重點介紹在光通信行業被廣泛應用的ALN陶瓷,從器件基板,薄膜電路,散熱基板,到陶瓷封裝等等,我們都能隨處可見。
此文我們將通過以下幾方面全面了解ALN的特點及制作工藝:
(1)ALN的性能特點
(2)ALN的材料制備
(3)ALN的金屬化工藝
(4)ALN的應用
ALN的性能特點
氮化鋁陶瓷有很高的熱導率,在陶瓷材料中僅次于SiC和BeO,目前國內平均水平為150W/m·K,國外為180 ~ 250/m·K,是氧化鋁陶瓷熱導率的7 ~ 8 倍;其機械強度和介電強度都優于氧化鋁陶瓷,膨脹系數、介電性能分別與Si和氧化鋁陶瓷相近。因而人們希望用高熱導率的氮化鋁陶瓷替代氧化鈹或氧化鋁陶瓷用于高密度、高性能電子封裝的陶瓷基板材料。
ALN陶瓷基板材料制備
陶瓷基板的成型主要有壓模、干壓和流延成型3種方法。
流延成型類似于攤雞蛋餅,控制刮刀與基帶的間隙就能控制厚度,可以薄至10um以下,厚至1mm以上我們的陶瓷電路基板都是采用的這種方法;
干壓法類似于金屬粉末冶金放入模具中壓鑄成型,適合大塊件;
壓模法就是注塑,可以做成形狀稍復雜的一些結構,如陶瓷插芯采用注塑成型。
下面介紹一些氮化鋁粉末常用的提取方法
現在使用較多的制備氮化鋁粉末的方法有鋁粉直接氮化法、氧化鋁碳熱還原法、溶膠法、自蔓燃法、等離子合成法、化學氣相沉積法、等等。
1)鋁粉直接氮化法
ALN+N2→2ALN將鋁粉放入通有氮氣與氨氣的反應的反應爐中加熱到600℃開始反應。我們就能合成大量純度較高的ALN粉,目前有這種方式的大規模生產。但是這種方法一般難以得到顆粒微細、粒度均勻的氮化鋁粉末,通常需要后處理。還有AL顆粒表面氮化后形成ALN層會阻礙氮氣向顆粒的中心的擴散,因此采用這種方法轉化率是一個重要的問題。
2)氧化鋁的碳熱還原法
Al203+3C+N2→2AlN+3CO這種方法目前運用在工業生產中運用最為廣泛,對其研究進行的比較深入。
在該法中制備氮化鋁粉體中常加入氧化鈣、氟化鈣、氧化釔等作為催化劑,其中加氟化鈣更有效的降低活化能,提高反應速率。這種制備的氮化鋁粉末純度高,成形和燒結性能好,但合成溫度高反應時間長,粉末粒度較大。
這邊需要說明下,如果有懂得金絲鍵合工藝的小伙伴就比較清楚,表面較為粗糙的有顆粒狀明顯的氮化鋁,如果使用這類的氮化鋁濺射薄膜金屬,打線時是不太容易鍵合上的,特別是球焊工藝,很容易出現脫焊狀況。
ALN的金屬化工藝
為了器件封裝結構,元器件搭載及輸入、輸出端的連接等目的,氮化鋁陶瓷基板表面常常作金屬化處理。ALN的陶瓷基片金屬化方法很多,分為以下幾種
厚膜金屬化、薄膜金屬化、直接鍵合銅金屬化、化學鍍金屬化等。
在半導體器件行業,最常見應用陶瓷電路基板電極采用是薄膜工藝和厚膜工藝。這兩種工藝方式是完全不一樣的,薄膜工藝指真空蒸鍍、和離子濺射這類能夠精確控制膜的形狀和厚度的成膜工藝,如我們光通信器件貼片載體Ti/Pt/Au或者Ti/Ni/Au電極和AuSn焊料都是采用薄膜工藝制備;
而厚膜工藝指絲網印刷,這類比較粗略簡便的成膜工藝,如泵浦源大功率激光器需要快速散熱都是使用的厚膜渡銅工藝氮化鋁。
大家知道我們光通信器件貼片載體常常采用AuSn共晶焊料,但焊料可不是直接蒸鍍在氮化鋁上的,而是底下有一層電極,采用Ti/Pt/Au或者Ti/Ni/Au這幾種金屬組合而成的薄膜電極,而且這幾種金屬都是有蒸鍍先后順序的,這是為什么呢?Ti/Pt/Au跟Ti/Ni/Au的差異性在哪里?
氮化鋁是六方晶纖鋅礦結構,密堆間隙中的Al離子半徑小,價態高,具有較強的極化作用,使氮化鋁清潔表面的不飽和氮具有較高的化學活性。通常氮因電負性大,電離勢高而有很強的共價傾向,即使與低電負性金屬反應,也會因負離子負電荷高,離子半徑較大而水解。故一般狀況下,氮不易與金屬反應。Ti,Ta,W等金屬因能與氮形成高晶格能化合物,使其在氮化鋁表面附著性能很好。
鈦具有良好的耐蝕性,較高的比強度和較小的質量密度,然而鈦表面的耐磨性差,易氧化,接觸電阻高,釬焊性差,在某些介質或高溫下鈦的耐蝕性也變差,使其應用受到一定的限制,在鈦上鍍鉑或鍍鎳可以克服以上缺點,鉑鎳鍍層硬度高,電阻小,可釬焊。
最后一層就是我們所熟悉的鍍金層,金子可是個好東西,在空氣中不易氧化,耐腐蝕,導電性能極佳,散熱性能好,還能與其他金屬如錫、銅做成焊料等等,
另外激光器的P面或N面常常都有鍍金處理,與我們的半導體芯片為了形成較好的附著力,跟我們的金絲鍵合能夠有效融合,所以氮化鋁的電極最后一層都需要用鍍金處理,鍍金厚度一般控制在0.5~1um左右,太薄了不行,金絲鍵合的強度難以保證,厚了當然是好事,那成本當然也上去啦。
氮化鋁電極鍍層及設計參數
一般廠家做電極鍍層時都會建議金屬化不能完全到邊,會預留0.05mm的白邊,因為一整片氮化鋁切割小片的時候會導致卷金問題;
Ti的厚度完全取決于氮化鋁拋光的表面粗糙度,目前我們國內也能做成鏡面氮化鋁,粗糙度能夠達到<0.05um,所以Ti厚度一般控制在0.1~0.2um;金錫焊料的厚度最小5um以上,我曾做過相應的貼片壓入厚度試驗,一般我們的貼片設備吸嘴壓力參數范圍3~500g左右,共晶焊15g的力道已經很大了,貼完片后將芯片推掉在電鏡掃描下測得芯片陷入厚度為2~3um;
下面我們再來解釋下,電極鍍層Ti/Pt/Au跟Ti/Ni/Au的性能差異
鉑金屬的抗腐蝕性極強,在高溫下非常穩定,電性能亦很穩定,它在任何溫度下都不會氧化。
鎳金屬亦有較好的抗腐蝕性,綜合性能比鉑金屬略遜色,導熱系數比鉑金屬稍高,鎳導熱系數90W,鉑金屬70W,但是鎳的成本要比鉑低個幾百倍,所以有很多廠家鍍層工藝都是選用的鈦鎳金;
如果要使用鈦鎳金鍍層氮化鋁的小伙伴們需要注意了,我曾經在這個工藝上栽過很大的跟頭。
我曾經負責過一大功率半導體封裝工藝,在做樣品時沒太過多關注氮化鋁的鍍層工藝參數,只是注意點都集中在選用高導熱系數的ALN選用的200W,實驗結果散熱性能也是通過要求,但是這個時候出現了一些問題,有個別樣品半導體芯片出現了“漏電”現象,這里所謂的“漏電”并不是真的漏電,而是芯片N級與P級之間的阻值發生了變化,原本是有一定幾十到一百Ω阻值的,可是“漏電”的芯片阻值只有幾個Ω或是0,也就是芯片的有源層直接導通了。當時對這個問題沒有太過細想,以為是芯片切割解理時導致芯片有源層損傷導致。
后來在小批量生產時,大規模的爆發了這種“漏電”不良品,不良率有40%~50%,這下問題就嚴重了,矛頭仍然指向芯片端工藝,絲毫沒有注意到氮化鋁,大伙都知道,我們在做芯片失效分析時,如果找不到直接原因,那只有人機料法環一一排除了,最后排查到氮化鋁這塊,以為是鍍層參數有問題,又更改了相應的鈦鎳金參數,還是不行,領導這時也發話三天內給出解決方案,大伙有體驗過這種手足無措,毫無頭緒的失效分析解決么,多少偉大的攻城師死在城墻門口,一旦城墻被攻破,那種成就感真是比娶了媳婦還美。
沒轍兒,只能不停的各種實驗,最后選用金屬鈦鉑金作為蒸鍍鍍層,實驗結果忽然讓人柳暗花明,撥云見日,“漏電”現象消失得無影無蹤;最后對比兩種熱沉發現,竟然是鎳層搗的鬼;
分析得知,鎳鍍層有很多直徑約1um圓錐狀山峰,類似于金屬的批鋒毛刺,雖然被外面的金層有所覆蓋,但是一但經過高溫回流或者高溫共晶焊時,這些晶須很容易攀附到半導體的有源層,再加上大功率半導體的有源層離氮化鋁鍍金面只有十幾個um的高度,很容易形成短路;
所以我這邊給小伙伴的建議是,如果半導體的有源層是在芯片的側面或者有源層高度很低時,如EML、DFB、大功率激光器,建議使用鈦鉑金工藝氮化鋁;
如果應用的場合是信號線過渡、垂直發光腔芯片如Vcsel,還有PD、電容等可以使用價格廉價點的鈦鎳金氮化鋁;
ALN的應用
(1)載體熱沉
(2)陶瓷封裝
(3)陶瓷電路
針對熱沉COC類、BOX類器件封裝工藝,目前天孚通信可做專業代工生產,推出高速率BOX有源器件封裝等系列解決方案。TFC擁有高精度貼合,金絲鍵合技術能力,自動化貼片設備精度可達±0.5um,亦可提供穩定AWG/TFF光學器件方案;同時擁有高精度精密加工和Recptacle設計裝配能力,TFC還擁有各種類型自由空間隔離器設計和隔離器芯片與插芯貼合以及擁有光學模擬分析能力,可以根據客戶要求定制設計和加工各類型的組件帶透鏡產品。如有合作意向的小伙伴們也可找我們洽談。
-
陶瓷
+關注
關注
0文章
139瀏覽量
20719 -
器件封裝
+關注
關注
0文章
7瀏覽量
5482
發布評論請先 登錄
相關推薦
華清電子擬在重慶建設半導體封裝材料和集成電路先進陶瓷生產基地
氧化鋁隔斷粉在氧化鋁陶瓷基板的應用
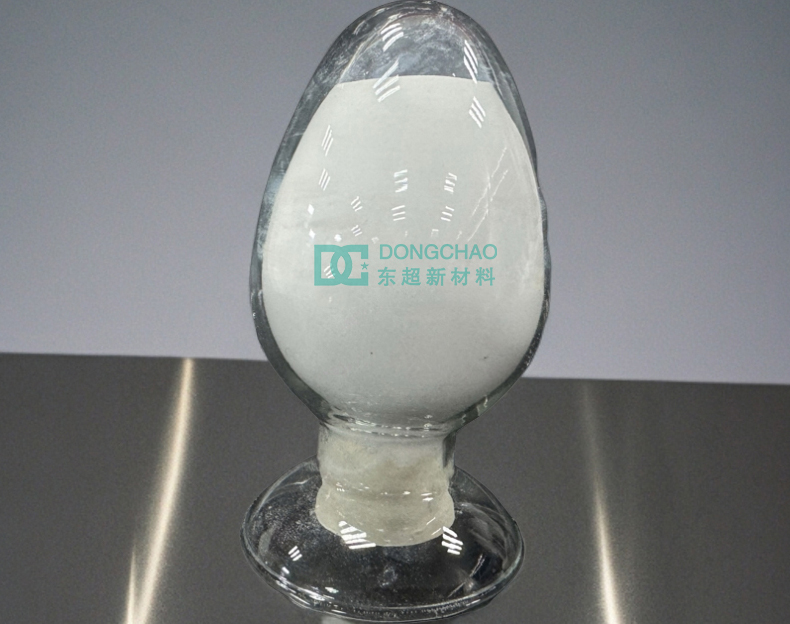
如何通過創新封裝技術提升功率器件性能
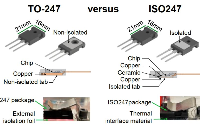
氮化鋁封裝材料:讓電子設備更穩定、更可靠
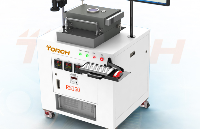
氮化鋁AlN電阻器-厚膜AlN電阻
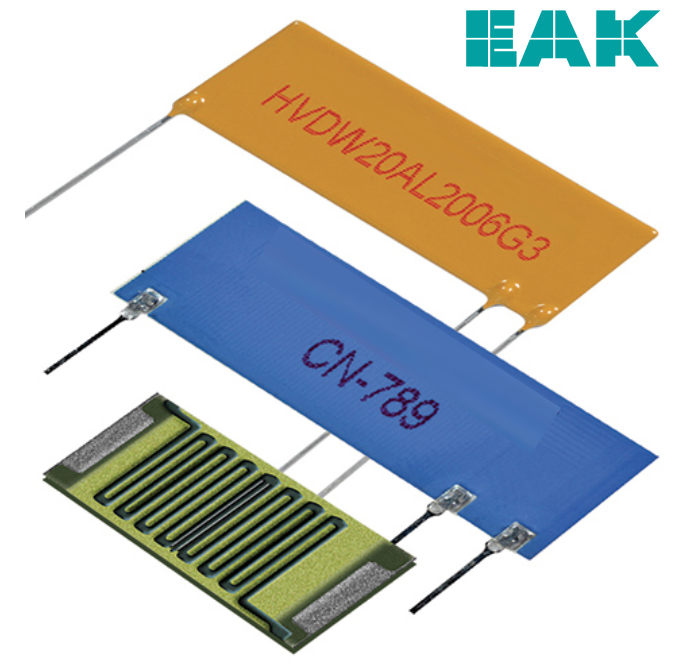
用于射頻功率應用的氮化鋁電阻元件

氮化鋁與氧化鈹用于大功率電阻器產品
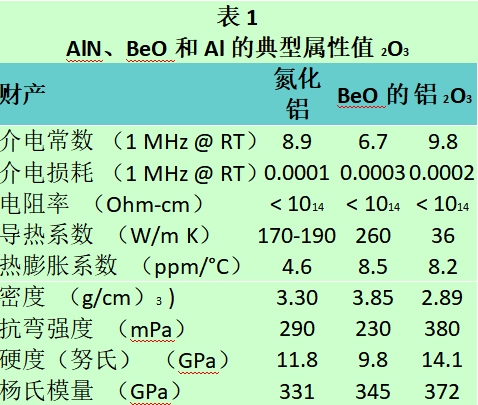
氮化鋁上的厚膜高功率片式電阻器
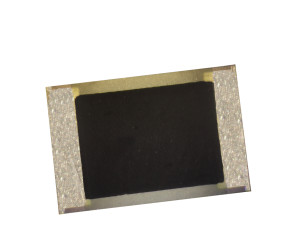
日本旭化成氮化鋁基板技術突破:邁向更大面積與實用化
Transphorm攜手偉詮電子推出兩款新型系統級封裝氮化鎵器件
導熱氧化鋁陶瓷基板:推動5G技術發展的關鍵材料
功率半導體器件陶瓷基板用氮化鋁粉體專利解析及DOH新工藝材料介紹
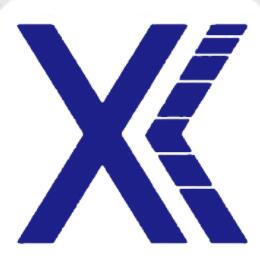
基于高溫退火非極性面氮化鋁單晶薄膜實現高性能聲學諧振器開發
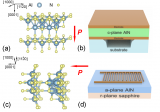
評論