汽車產(chǎn)業(yè)作為制造業(yè)中的明珠,具有制造工藝復雜、裝配線柔性大、作業(yè)手法精密、生產(chǎn)節(jié)拍緊張等特點[1]。以總裝車間為例,生產(chǎn)一臺車需要經(jīng)過400~500 個崗位,500~600 名員工的作業(yè),汽車制造流水線每50~90 s 就有一臺車下線,整個制造過程十分依賴人工[2],提高人員效率,降低生產(chǎn)成本是汽車企業(yè)的重要方向,最終就體現(xiàn)在自動化程度的提升上[3]。
工業(yè)中的視覺檢測技術,通俗的說就是用設備代替人工完成測量、檢查、引導、識別等一系列操作[4],設備相比于人來說,不會疲累,不受環(huán)境影響,工作效率高,檢測更穩(wěn)定[5],不僅能提升汽車生產(chǎn)的人員效率,而且能獲得更高的汽車品質(zhì)[6]。
2 視覺檢測技術與某車企總裝車間介紹
2.1 視覺檢測技術的發(fā)展歷程
視覺檢測技術的主要組成部分包括光源、視覺相機、圖像處理器、計算機處理系統(tǒng)、執(zhí)行機構(gòu)等[7],視覺檢測技術作為工業(yè)技術中的一個細分領域,涉及到圖像處理、數(shù)字圖像轉(zhuǎn)換、機械工程、自動化檢測、光源設計、圖像傳感器技術、模擬電子信號、數(shù)字信號處理技術、人機協(xié)同技術等,每一項技術的發(fā)展都會影響到視覺技術的進步[8]。
從視覺技術的發(fā)展歷史來看,視覺技術自20世紀50 年代提出,經(jīng)歷了CCD 技術出現(xiàn)、計算機運算能力躍升、LED 任意光場設計、OCR 識別技術等多次技術突破才逐漸成為可以應用在工業(yè)生產(chǎn)中的成熟技術[9]。
2.2 某車企總裝車間介紹
某主機廠現(xiàn)為國內(nèi)主流汽車公司,單條生產(chǎn)線的整車制造能力達到24 萬臺/年。總裝車間作為整車制造四大工序的最后一個流程,具有人員多、工藝復雜、節(jié)拍緊張、品質(zhì)要求高的特點,某車企總裝車間的生產(chǎn)節(jié)拍達到70 JPH(臺/每小時),平均51 s 下線一臺整車,緊張的生產(chǎn)節(jié)奏需要大量的崗位和員工。
某車企的總裝車間近年來自動化程度不斷提高,已經(jīng)導入了輪胎自動化安裝設備、前后擋風玻璃自動安裝設備、發(fā)動機自動質(zhì)檢設備、車門自動涂膠設備、車身加強劑自動底涂設備等,大大優(yōu)化了人員效率。其中多數(shù)自動化設備都運用到視覺技術,在自動化程度不斷提高的過程中與多個視覺檢測技術廠家如ABB、安川首鋼、基恩士、康耐視、SRT 等都有密切合作。
3 某車企總裝車間視覺技術應用
人工質(zhì)檢的缺點是人員疲憊后的穩(wěn)定性和可靠性降低,易受到環(huán)境干擾,質(zhì)量研究表明,人工作業(yè)的出錯概率為3‰,而正常工作的機器出錯的概率可以降低到0,視覺檢測技術的品質(zhì)保證能力大大強于人工質(zhì)檢。視覺檢測技術在某車企總裝車間的應用實踐主要包括發(fā)動機質(zhì)檢、加強劑涂布質(zhì)量檢查、玻璃膠型檢查、手持終端檢查等。
3.1 發(fā)動機質(zhì)檢
在某主機廠已經(jīng)實現(xiàn)的汽車發(fā)動機視覺質(zhì)檢包括檢查螺栓緊固是否疏漏、零件有無漏裝及安裝不良、卡箍安裝位置是否正確、條碼標簽是否準確等。因此利用視覺檢測技術需要克服質(zhì)檢點分布廣、類別多、判斷基準各不相同的難點。
發(fā)動機視覺質(zhì)檢的解決方案是采用4 臺機器人攜帶200 萬像素的工業(yè)相機,分布在發(fā)動機的左前、左后、右前、右后位置,如圖1 所示。質(zhì)檢結(jié)果形成數(shù)據(jù)庫用于追溯和查詢。機器人運動半徑為712 mm,可完全覆蓋發(fā)動機所有質(zhì)檢點。在45 s節(jié)拍內(nèi)檢查項目34 項,共47 點,包括條形碼核對、紅油標識、卡箍安裝狀態(tài)、密封圈安裝狀態(tài)等。
發(fā)動機視覺質(zhì)檢的工作流程,如圖2 所示。
圖2 發(fā)動機視覺質(zhì)檢流程
視覺檢測技術的原理是首先獲取被檢查點圖像,通過曝光、灰度、邊緣銳化等處理,提取檢測點的明顯特征,并同檢測基準對比,輸出檢查結(jié)果。例如,螺栓點油視覺質(zhì)檢的實現(xiàn)原理是利用具有紅油標識的螺栓經(jīng)過視覺軟件的處理后,顯示為白色,如圖3 所示,沒有紅油標識的螺栓顯示為黑色,依此為依據(jù)可以進行點油標識的明顯判斷。
當視覺檢測出現(xiàn)異常情況時,設備會自動觸發(fā)報警并提示異常原因,通知生產(chǎn)管理人員處理,異常處理完畢后自動記錄結(jié)果及處理人信息,便于后續(xù)品質(zhì)追溯。
視覺檢測技術在發(fā)動機質(zhì)檢上的應用,實現(xiàn)了紅油螺栓的識別、卡箍安裝位置的測量、標識碼的掃碼功能,相較于人工質(zhì)檢異常檢出率達到100%,質(zhì)檢工時下降20 s/臺,單臺產(chǎn)品車成本下降1.26元。并增加了品質(zhì)追溯能力,為過往異常的查詢和確認提供了依據(jù)。視覺檢測軟件具備二次開發(fā)功能,可以根據(jù)后續(xù)新車型需求進行功能開發(fā)。
3.2 加強劑涂布視覺檢查
安裝汽車前后擋風玻璃、側(cè)窗玻璃時,都需要在車身位置涂布一層加強劑,加強劑主要作用是增強玻璃與車身之間的粘合力,防止玻璃膠老化。加強劑的涂布要求達到均勻飽滿、完全覆蓋設定軌跡等標準,若不符合要求會影響到玻璃安裝品質(zhì),因此需要檢查確認,使用視覺檢測技術進行隨行檢查可以實現(xiàn)穩(wěn)定可靠的檢測,并形成追溯管理。
加強劑涂布的視覺檢查主要由機器人、高速視覺相機、工控機組成,如圖4 所示,機器人攜帶高速視覺相機隨行涂布,每秒9 090 幀的高速視覺相機完成實時檢查。視覺相機跟隨涂布膠槍運動,運動速度350 mm/s,在高速涂膠的過程中,高速拍照獲取加強劑涂布照片,保證能夠滿足45 s 的設備節(jié)拍。
圖4 機器人攜帶視覺相機進行涂布檢查
加強劑涂布視覺檢查的工作流程,如圖5所示。
圖5 加強劑涂布視覺檢查流程
采用顏色傳感器與超聲波傳感器結(jié)合,加強劑涂布后通過打光顯示為黑色,車身顯示為白色,黑白分布變得明顯,再以20 mm×40 mm 的標準行程段進行加強劑涂布的超聲波檢測。如圖6 所示,若搜索出涂布面積符合要求,則一直跟隨拍照檢測直到整個車身的涂布軌跡完成,若搜索不到加強劑涂布(涂布中斷),則軟件提示報警,由生產(chǎn)管理人員進行處理。
圖6 加強劑涂布的視覺檢查
視覺檢測技術在加強劑涂布上的應用,實現(xiàn)了全自動涂布與檢測,相較于人工涂布檢查的方式異常檢出率可達到100%,徹底杜絕涂布不良流出。涂布檢測工時下降8 s/臺,削減有害工位2 個,單臺產(chǎn)品車成本下降9.01 元。
3.3 玻璃密封膠膠型視覺檢查
玻璃密封膠是涂布在玻璃邊緣上,在給汽車安裝玻璃時,用以粘合玻璃和車身使之密封,玻璃密封膠的膠型對涂布質(zhì)量有較大影響,因此需要控制玻璃膠的膠型,主要體現(xiàn)在玻璃膠的形狀是否滿足膠寬8 mm(可略微浮動),高度12~13 mm,涂布是否均勻,是否存在斷膠等,及時檢測出涂布不良可有效減少不良品的流出。
由于玻璃密封膠的膠型特點體現(xiàn)在立體結(jié)構(gòu)上,一般的2D 拍照無法檢測出3D 特征,因此使用3D 激光三角法視覺檢測解決此課題,如圖7 所示。檢測流程如圖8 所示。
圖7 玻璃膠膠型3D檢查的原理示意
由涂膠機器人攜帶高速視覺相機及激光傳感器組成膠型檢查系統(tǒng),如圖9 所示。借助高速視覺相機,實現(xiàn)隨行高速拍照檢查,借助激光掃描膠型,為視覺處理圖片創(chuàng)造了光場條件,借助視覺測量技術獲得膠型照片中膠型的寬度信息,通過計算激光反射時間,獲得膠型高度信息,寬度和高度信息整合后與標準膠型數(shù)據(jù)對比,即可實現(xiàn)實時檢查,如圖10 所示。
圖8 玻璃密封膠膠型視覺檢查流程
視覺檢測技術在玻璃密封膠涂布膠型的檢查相較于人工檢查,膠型異常檢出率提高到100%,膠型的寬度及高度信息依靠視覺檢測能夠?qū)?shù)據(jù)精確到0.1 mm,明顯提升品質(zhì)控制能力,膠型檢測工時下降6 s/臺,同時單臺產(chǎn)品車成本下降2.58元。
4 視覺技術的發(fā)展方向與應用淺析
4.1 3D測量與多點檢測
在汽車制造行業(yè)或其他制造業(yè),機器視覺用于產(chǎn)品質(zhì)量檢查已經(jīng)得到了廣泛的應用[10],3D 視覺系統(tǒng)可以大量識別隨機放置內(nèi)飾件、外飾件等,3D 成像更接近真實物體的形狀,可用來測量工件凹槽的深度等,如圖11 所示。
圖11 3D測量與多點檢測
總裝車間內(nèi),整車車身的總裝工程包括電裝、內(nèi)裝、底盤、外裝四大類,每類都涉及到大量的裝配,零件數(shù)量多,裝配要求不同,若將3D 檢查和多點測量應用至整車車身的質(zhì)檢,可以檢查零件的規(guī)格是否正確、裝配的基準是否符合要求、防盜標簽的字符是否準確、螺栓的緊固是否標識等項目。依據(jù)現(xiàn)有的視覺檢查技術,由機器人攜帶視覺相機,4 臺機器人分布在車體四周,對各種類型和不同位置的檢測點進行拍照,并由高速計算機快速比對檢查基準,以基準進行判斷,如圖12 所示。同時可保存檢測圖形,用于查詢和追溯,在發(fā)動機視覺質(zhì)檢的案例中可以看到未來整車質(zhì)檢的身影。
4.2 穩(wěn)健視覺算法與深度學習神經(jīng)網(wǎng)絡
現(xiàn)今的視覺算法還存在較大的進步空間,在復雜的工業(yè)應用現(xiàn)場,視覺算法的效率不足,同時受到環(huán)境影響,準確性和魯棒性下降[11],抗環(huán)境光干擾的能力不足。除硬件的進步之外,開發(fā)出穩(wěn)健的視覺算法同樣是一個重要方向。同時5G 數(shù)據(jù)網(wǎng)絡的到來為云計算提供了強大的視覺計算能力,良好的通訊基礎為在云中處理大量機器視覺數(shù)據(jù)提供了可能。車間每年生產(chǎn)24 萬臺汽車,大量的生產(chǎn)案例,借用5G 網(wǎng)絡云計算訓練,視覺檢查的準確性將大大提高,完全可以適應生產(chǎn)現(xiàn)場的個性化需求,年產(chǎn)量巨大的汽車制造工廠,就是深度學習模型中鮮活的數(shù)據(jù)庫。
例如汽車輪胎上具有多種信息,一般通過凸顯字符的形式標識,包括輪胎的品牌、規(guī)格、尺寸、標識等,以此判斷輪胎組裝時的完成度。當輪胎上的點油標識缺失或規(guī)格錯誤時,會造成品質(zhì)不良,同時輪胎的安裝和檢測都不易發(fā)現(xiàn)品質(zhì)不良點,若采用視覺檢測技術對輪胎來件品質(zhì)進行檢查,以此杜絕裝配的品質(zhì)隱患。如圖13 所示。如果視覺檢測技術配合深度學習,大量的生產(chǎn)實例將為深度學習提供源源不斷的數(shù)據(jù)來源,機器將會以更高的效率和準確性進行處理,不僅工時會下降,檢測算法也會趨向最優(yōu)化。
圖13 輪胎的視覺質(zhì)檢
5 結(jié)束語
視覺檢測技術在某車企的總裝車間得到了大量的應用,發(fā)動機視覺質(zhì)檢、加強劑涂布檢查、玻璃密封膠膠型檢查等,實現(xiàn)了檢查的自動化,提高了人員效率,改善了作業(yè)環(huán)境,同樣隨著視覺技術的進步,未來在總裝車間會引進更多的視覺技術,擴大視覺技術在汽車行業(yè)的應用。
在未來,可以預想到工智能的深度學習能夠使視覺檢查越來越準確,視覺檢測技術的價格會更加親民,通訊和計算能力的躍升幫助檢查的速度提升。汽車生產(chǎn)行業(yè)提出越來越多的需求,而視覺檢測技術的進步,也一定能夠滿足這些需求。
原文標題:某車企總裝車間視覺檢測技術的應用
文章出處:【微信公眾號:新機器視覺】歡迎添加關注!文章轉(zhuǎn)載請注明出處。
責任編輯:haq
-
計算機
+關注
關注
19文章
7508瀏覽量
88074 -
機器視覺
+關注
關注
162文章
4378瀏覽量
120394
原文標題:某車企總裝車間視覺檢測技術的應用
文章出處:【微信號:vision263com,微信公眾號:新機器視覺】歡迎添加關注!文章轉(zhuǎn)載請注明出處。
發(fā)布評論請先 登錄
相關推薦
3D 視覺定位技術:汽車零部件制造的智能變革引擎
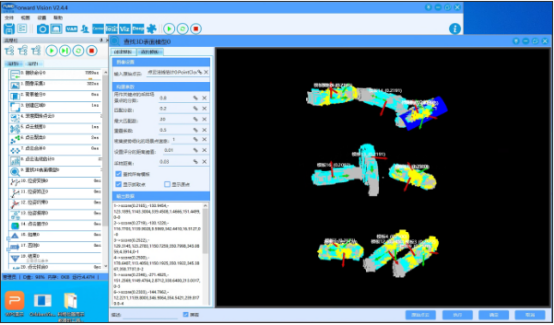
視覺檢測的優(yōu)勢有哪些?為什么傳統(tǒng)生產(chǎn)線要做視覺檢測?
機器視覺和人工智能在數(shù)字化制造領域的深度應用分析
視覺檢測是什么意思?機器視覺檢測的適用行業(yè)及場景有哪些?
機器視覺在焊接質(zhì)量檢測中的應用
人臉識別技術將應用在哪些領域
機器視覺檢測技術在工業(yè)自動化中的應用
機器視覺尺寸檢測技術全解析!
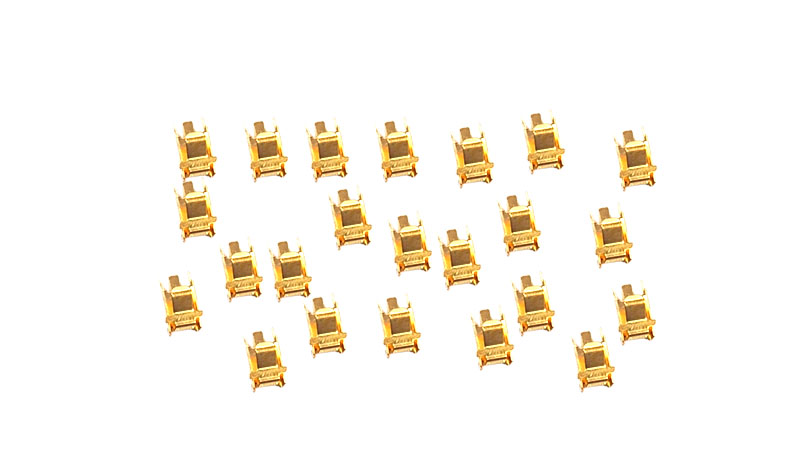
Profinet轉(zhuǎn)Ethernet IP網(wǎng)關在汽車配件生產(chǎn)中的應用
確保零失誤!最先進的生產(chǎn)視覺系統(tǒng)!
視覺檢測技術沖破人工界限
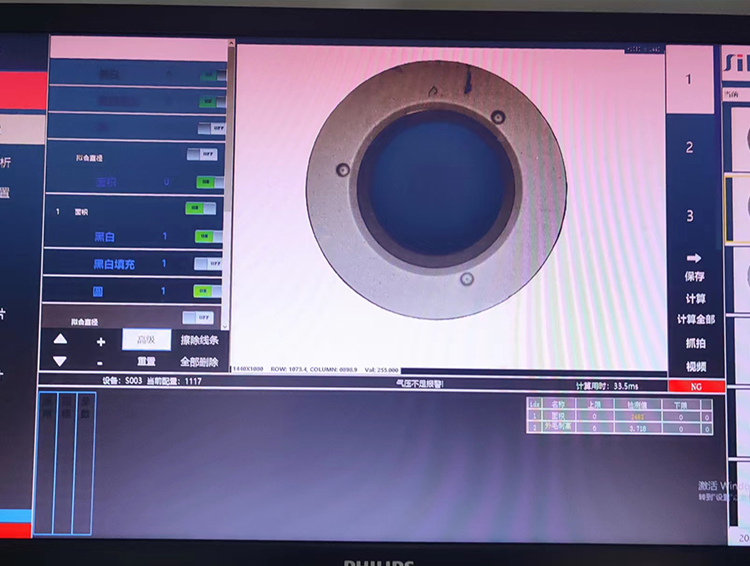
電動汽車電池電極制造的AI技術與機器視覺能力
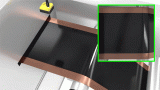
法拉電容如此優(yōu)良,是否可以應用在汽車行業(yè)?
焊接視覺檢測系統(tǒng)的原理和應用
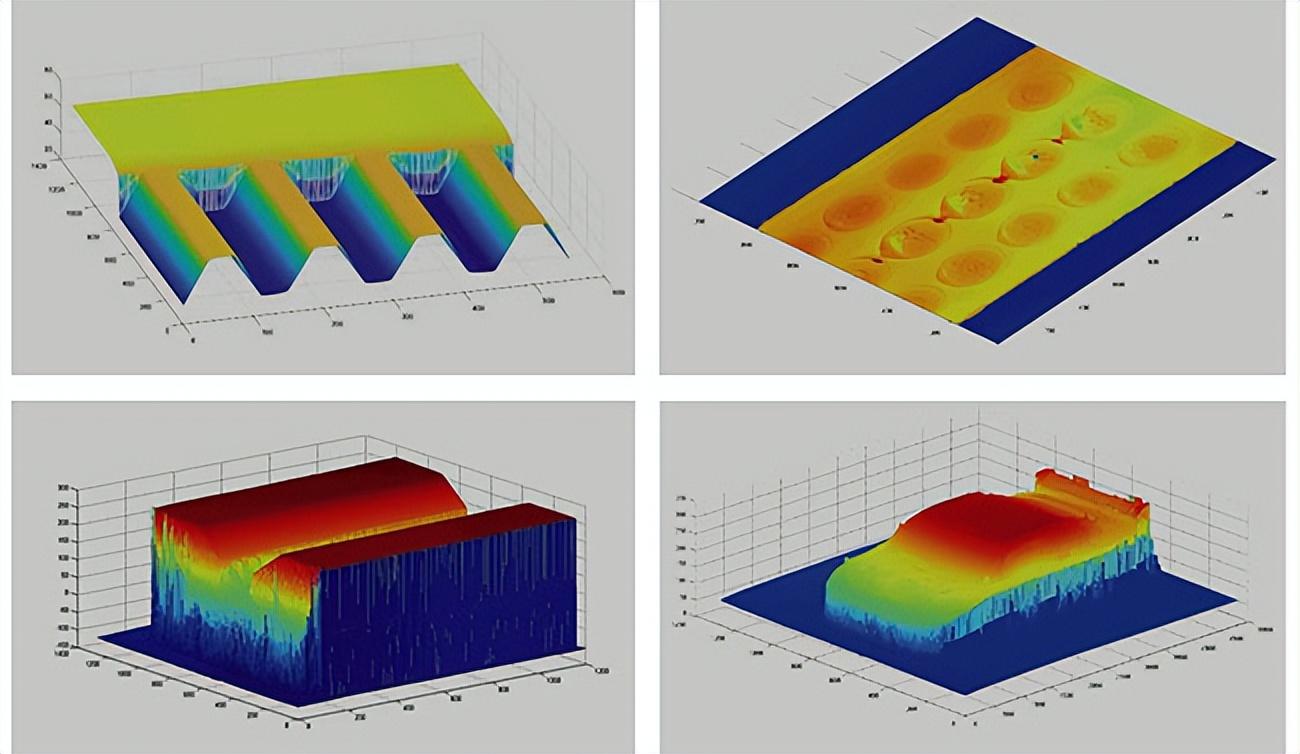
評論