智能化和電動化的大浪潮已然拉開序幕,擁抱變革才能不錯過這一生機勃勃的時代。就在2021年開年,圍繞“1000公里續航”話題的爭議就已火藥味十足。但無論理想與現實之前有多遠的距離,向著1000公里“進發”看來已是必然之路。而電池的“萬丈雄心”需要電池管理系統(BMS)來加以成全,BMS如何隨需而變?又將催生哪些新的技術?隨著BMS的“權重”凸顯,產業鏈條又將發生怎樣的更迭?
一切都在變化中,能否在變局中開新局?
BMS的變局
BMS之所以如此重要,是因電池本身在成本和性能上已成為整車廠致勝的關鍵點,而電池的續航里程、快充、成本等均與BMS的優化息息相關。恩智浦半導體副總裁兼驅動和能源系統產品線總經理李曉鶴提及,如在一定程度上提高充電狀態以及電池健康的估算準確值,就可在不增加成本的情況下提高快充速度或單次續航里程。
如TI中國區嵌入式與數字光處理應用技術總監師英所言,BMS常見的訴求在于:一是如何保證電池系統的安全性。二是如何讓電池系統在最大的效率下運行,即最大化續航里程。三是提升可靠性。四是進一步降低成本。
正因為BMS所締造的高價值譜系,因而盡管從占比來看,李曉鶴的估計是BMS在電池總成本中占比較小,約在10%-20%之間,但BMS仍大有可為。
對于延長續航里程、縮短充電時間這一持續的“命題”,李曉鶴指出了相應的挑戰,即延長里程要提高比能量,縮短充電時間則要增加比功率,產生的風險諸如過壓、過充、熱失控等,這都需要BMS有更高的安全等級、更快的診斷速度和更精確的測量等。
而BMS經過十多年的發展,關注點亦逐漸轉向,需要全盤考量。李曉鶴表示,最初幾年是關注其可靠性的優化。而在過去的幾年,關注點已轉移到系統成本的優化。到現在,一方面整體系統成本的優化會一直繼續,未來整體電池成本控制將會有一個質的提升,目前成本約130美元/千瓦時,十年之內或將成本壓縮至一半。另一方面,隨著車廠產量從幾萬輛、幾十萬輛車進入百萬級別,如何能以相對成熟的方式,做到成本更優化、安全性更高、可靠性更高等一致性將是持續的考驗。
作為汽車業老牌勁旅,恩智浦的BMS整體方案除著力滿足上述需求之外,還有一大優勢是其可兼顧14V、48V、400V、800V以及各種不同模式,可擴展性和復用性可助力客戶輕松進行軟硬件開發,并且只需關注應用層軟件的差異化設計即可,從而降低驗證時間并加快上市。
在業界期盼的快充層面,亦如同一把雙刃劍,畢竟快充會降低電池的壽命,比慢充更耗損電池。對此,李曉鶴表示,一方面可從電化學設計角度來改善,這是材料本身要解決的問題。二是BMS通過提高精度、優化測量方式以及確保更好的電流電壓同步性來支持快充,并從中保證安全。
供應鏈的“變遷”
無論是已成全球趨勢的汽車芯片短缺以及巨大的不確定性,還是智能汽車的模塊化演進,都在催化供應鏈的自主可控和重塑,傳統線性產業鏈模式已然“生變”。
在傳統線性的模式中,汽車零部件廠如博世、大陸等以及電池供應商可作為Tier1,而汽車半導體公司一般可作為Tier2,供應鏈條一般是Tier2至Tier1再至整車廠。
“BMS是一個多元化市場,因電池本身是新能源汽車廠商的戰略重點,整車廠、電池廠、Tier1都想抓住機會?!崩顣扎Q分析說,“目前是多種現象共存,有的是以整車廠為主導,車廠本身擁有電池的集成能力,就像大眾等;有的是像寧德時代這樣有很強實力的電池制造商為主導,完成整個系統的設計和集成工作,為整車廠提供電池包,而這樣整車廠的溢價權、決策權就會相對低一些;還有一種傳統情況是恩智浦將方案提供給Tier1,Tier1再供給整車廠,中間還有一家電池企業?!?/p>
受國際形勢不確定性和缺貨日趨嚴重的影響,構建安全可控的汽車芯片供應體系,已經成為了產業發展的“當務之急”。眾多車企紛紛走向自研或者聯合芯片公司研發的道路,Tier1和整車廠商的驗證速度明顯提升。在這一過程中,半導體廠商更需應時而動。
“對于半導體廠商來說,因整車廠和電池廠在競爭中有更多的主動權,整車廠是甲方,電池廠則擁有最核心的材料、機械以及電池設計資源。因此半導體廠商服務的客戶是非常多元化的,不只是和Tier1接觸,與整車廠、電池廠都要建立更強的互動?!?李曉鶴直言道。
無線BMS的“進階”
盡管有線BMS縱橫江湖多年,但一個微妙的現實是,BMS從有線走向無線的趨勢已在“顯性化”。
這主要還是因為有線BMS的弊病所致。據TI中國區嵌入式與數字光處理應用技術總監師英介紹,在有線BMS系統中,每一節電池包都有模組,模組中的每個電池都必須通過一個通信電纜連接到一個調節電量、做電池電芯監控和平衡的監控芯片。為使通信電纜的連接可靠,一般會采用菊花鏈連接,而且線纜需要重型銅線,這造成非常龐雜的電纜布置,不僅會增加重量,而電纜和連接器故障亦是導致電池包出現故障的主要原因。而一旦電纜或者連接器出現問題可能需要更換整個電池包,費用也會十分昂貴。
因而,無線BMS成為解決這一痼疾的動向之一。師英指出,一方面,采用無線的方式則可不采用重型銅線,從而將更多空間留給電芯,這可提高整個電池包的體積能量密度,從而提高新能源汽車的續航能力。另一方面,它不僅可以減低制造工藝的難度,還可以降低后續維護的成本。
值得一提的是,為避免干擾和相關挑戰,TI專門為了無線BMS設計的一個無線通訊協議棧。師英強調,這一協議網絡可用性可以達到99.999%,錯誤故障率極低,就算萬一有99.999%之外的故障也有快速診斷和恢復機制,從而讓網絡恢復到安全通信的狀態。同時,這套系統提供多個跨平臺進行可靠系統設計的自由,提供可擴展性和高靈活性。據師英介紹,TI無線BMS已經通過了符合汽車安全完整性等級ASIL D認證,以及更高水準的國際標準化組織(ISO)26262認證。
雖然無線BMS看似“美好”,但畢竟是一新生事物,想要“開辟一片新天地”仍面臨著諸多挑戰。
對此,德州儀器 (TI) 電池管理系統工程經理吳萬邦認為,無線BMS除在技術上保證可靠性、安全性、價值化之外,成本的進一步降低將更便于市場接受,但這還需要一段時間。此外,相關工程師如何將新的無線方案融入其整體的開發,亦是無線BMS方案實現商用化的挑戰。而為了進一步助力無線BMS方案的落地,TI著力提供從軟硬件到參考設計全流程解決方案,以加速產品的上市時間。
瓦爾登湖有一句話:有些人步伐與眾不同,那是因為他們聽見了遠方的鼓聲。
責任編輯:tzh
-
半導體
+關注
關注
334文章
27297瀏覽量
218114 -
無線
+關注
關注
31文章
5451瀏覽量
173246 -
bms
+關注
關注
107文章
996瀏覽量
65951 -
電池
+關注
關注
84文章
10563瀏覽量
129484
發布評論請先 登錄
相關推薦
MOS管在電池管理系統(BMS)中應用的解析
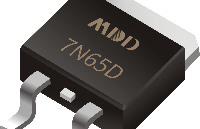
精準監測電池單體狀態,CMU在BMS中的兩種發展趨勢
什么是電池BMS系統(高精度電流檢測傳感器在BMS中的作用)
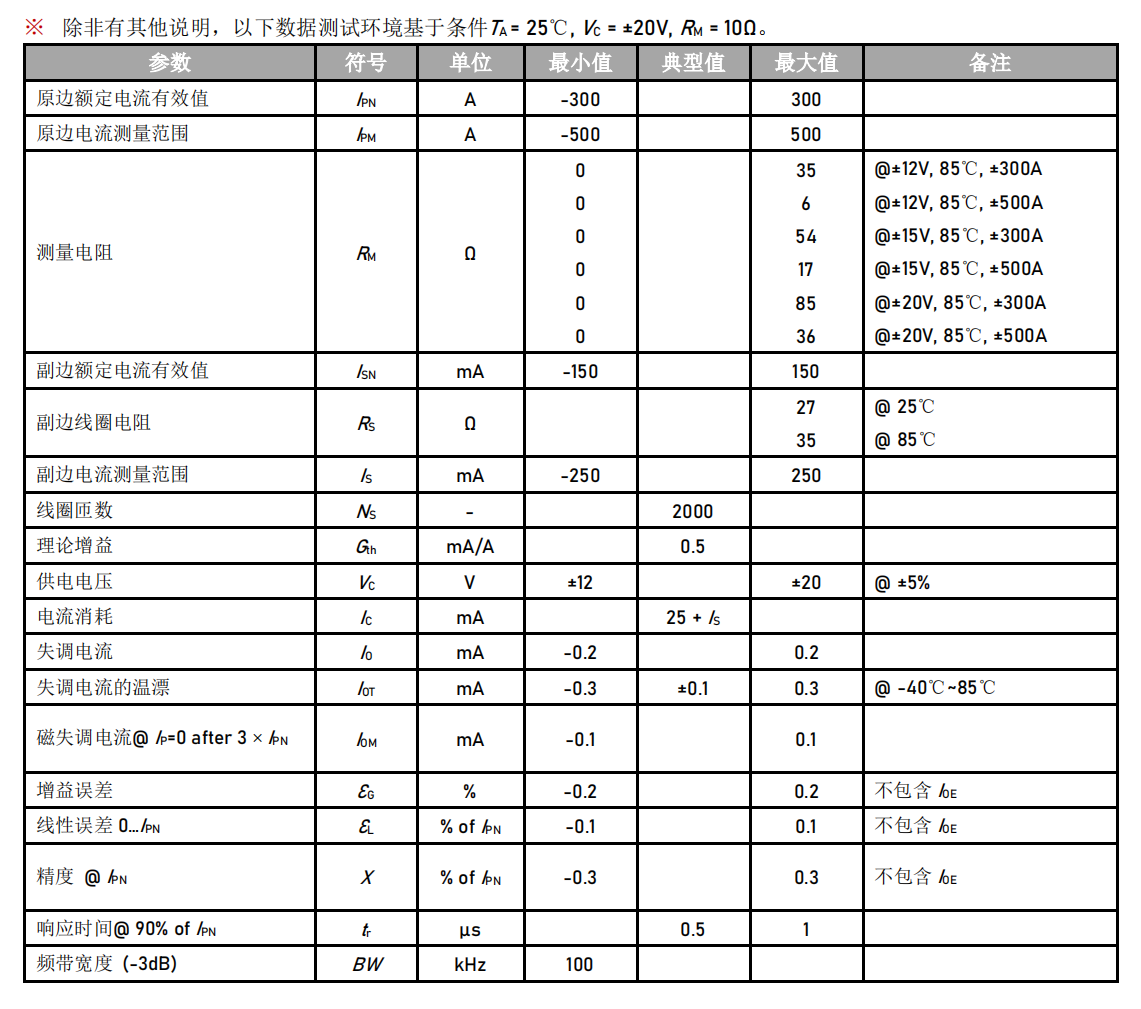
儲能bms和動力bms哪個好
BMS電池管理系統的作用有什么?如何設計電池管理系統 (BMS)
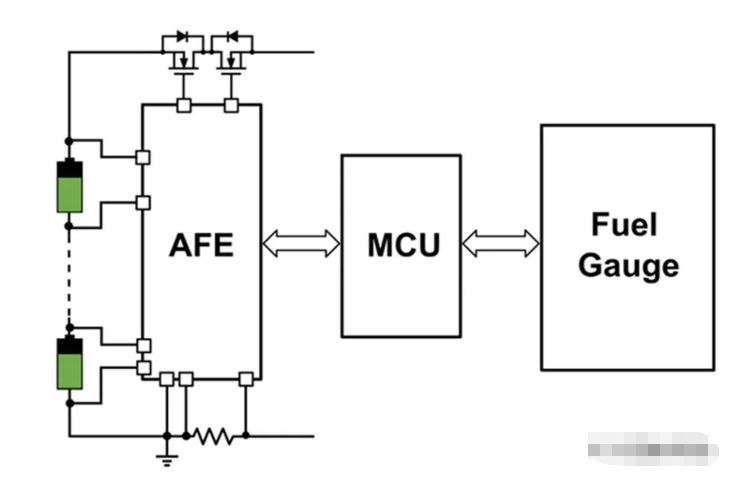
評論