從工業物聯網 (IIoT) 到網絡基礎設施設備,下一代電子系統正在注入新的智能,在不斷縮小的空間中需要更多的功率,而不會影響熱預算。因此,傳統的解決方案并不適合。然而,考慮到上市時間壓力,設計人員沒有大量時間來設計電源,他們必須在有限的空間內努力散熱,同時滿足沖擊、振動和 EMI 要求。
在不過熱的情況下可靠地為縮小的設備和傳感器供電的最佳方法是什么?并快速創建這些電源設計?
傳感器歷來包括一個傳感元件和一些將傳感數據傳輸到可編程邏輯控制器 (PLC) 的方法。數據將是單向的并以模擬格式傳輸。然而,模擬數據通信容易產生噪聲,控制器無法直接診斷、重新配置或重新校準傳感器。隨著時間的推移,技術不斷進步,傳感器制造商開始將更多功能集成到這些設備中,同時通過二進制傳感器降低噪聲敏感性。在二進制傳感器中,數據仍僅限于單向通信,工廠車間仍需要技術人員來處理手動校準等任務。
IO-Link 的出現通過允許傳感器和控制器之間的雙向通信將智能帶到了工廠車間的邊緣(圖 2)。借助此功能,系統可以實時調整、配置和診斷傳感器——這正是滿足工業 4.0 和智能工廠的需求所需要的。
與為單一產品建造和優化的傳統工廠不同,智能工廠旨在快速適應市場需求的變化。實時診斷功能有助于預測性維護,并可以延長工廠正常運行時間。
圖 2. 帶有 IO-Link 傳感器的 PLC
智能傳感器的智能特性增加了這些傳感器的功耗。與此同時,工業設備制造商也有向小型化方向發展的趨勢。這意味著為智能傳感器供電需要解決熱量和尺寸方面的挑戰。為了說明這些挑戰,讓我們考慮一個帶有 IO-Link 的智能接近傳感器(圖 3)。在此應用中,微控制器從傳感元件收集數據,對其進行線性化和校準,然后將其發送到 IO-Link 收發器。從這里,數據被發送到系統 PLC。IO-Link 連接器還提供 24V 為傳感器供電。
圖 3. 帶有 IO-Link 的智能接近傳感器示例
傳感器電路的傳統電源解決方案將涉及低壓差線性穩壓器 (LDO)。讓我們看看傳感器電路、電源和整個設備的功耗。老式模擬傳感器電路通常消耗大約 15mA。24V 工業電源軌最高可達 30VDC。功耗如下:
I O = 15mA,Vi = 30V(最大值)
P Sensor = VoxIo = 75mW
P SUP = P LDO = (Vi – Vo) xIo = 375mW
P Device = P Sensor + P LDO = 450mW
在本例中,只有 75mW 用于實際工作(為傳感器電路供電),而 LDO 由于效率低下而損失了 375mW。我們的設備必須消耗 450mW 的總功率。為傳感器添加更多智能功能將需要更多電流,這對于設備的功耗來說不是好消息。使用上面的計算,如果我們將傳感器電路電流增加到 30mA,則:I O = 30mA,P Sensor = 150mW,P SUP = 750mW,P Device = 900mW。900mW 超過了大多數小型接近傳感器的功耗限制。所以,散熱是個大問題。
傳統 LDO 電源解決方案的替代方案是使用小型 DC-DC 電源模塊。如圖 4 所示,在 15mA 傳感器電流和保守的 75% 效率下,DC-DC 電源模塊的功率損耗僅為 25mW。這有助于將總器件功耗從 450mW 降至 100mW,功耗降低 4.5 倍。
圖 4. 電源耗散 - LDO 與 DC/DC 轉換器解決方案
由于 DC-DC 電源模塊的高效率,傳感器可以支持更多的電路和功能,因為熱量最小化并支持更多的傳感器電流。Maxim 的 Himalaya uSLIC 系列提供了一些非常適合微型傳感器的電源模塊示例:MAXM17532是一款 100mA 超緊湊型寬輸入電壓 uSLIC 器件,以及MAXM17552可在高達 60V 的輸入電壓下工作。這些緊湊型模塊可節省空間、減少熱量并有助于簡化電源設計。
隨著工業 4.0 繼續推動對智能傳感器的需求,借助高度集成的 DC-DC 電源模塊,解決為這些傳感器供電的挑戰現在變得更加容易。
審核編輯:郭婷
-
傳感器
+關注
關注
2550文章
51038瀏覽量
753086 -
控制器
+關注
關注
112文章
16334瀏覽量
177813 -
plc
+關注
關注
5010文章
13274瀏覽量
463073
原文標題:【會員風采】科通芯城2020年業績:凈利潤1.87億同比增長29.2%,芯片和智能硬件成亮點
文章出處:【微信號:qidianxiehui,微信公眾號:深圳市汽車電子行業協會】歡迎添加關注!文章轉載請注明出處。
發布評論請先 登錄
相關推薦
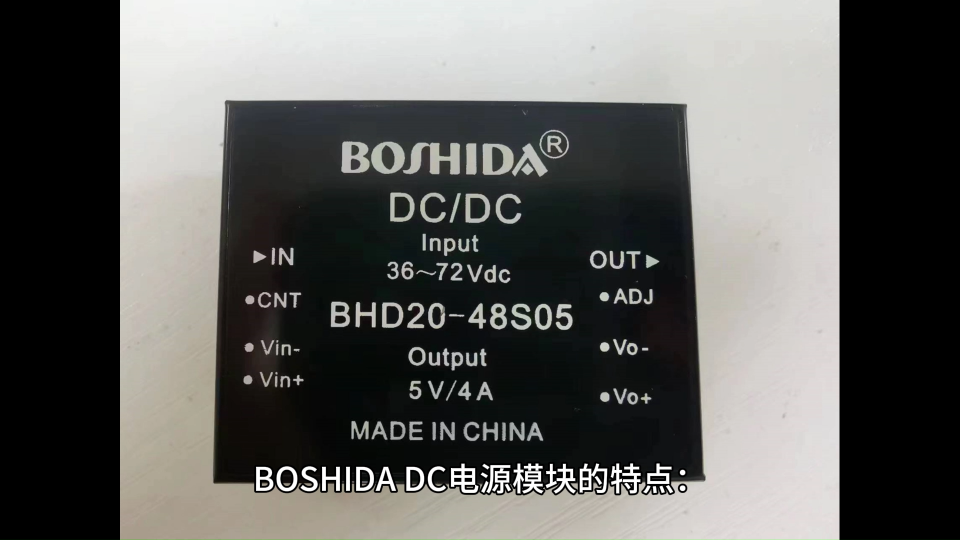
低功耗DC-DC電源模塊的精細化PCB設計
低功耗DC-DC電源模塊的精細化PCB設計
牛!低功耗DC-DC電源模塊的精細化PCB設計
牛!低功耗DC-DC電源模塊的精細化PCB設計
DC電源模塊的使用范圍是什么?

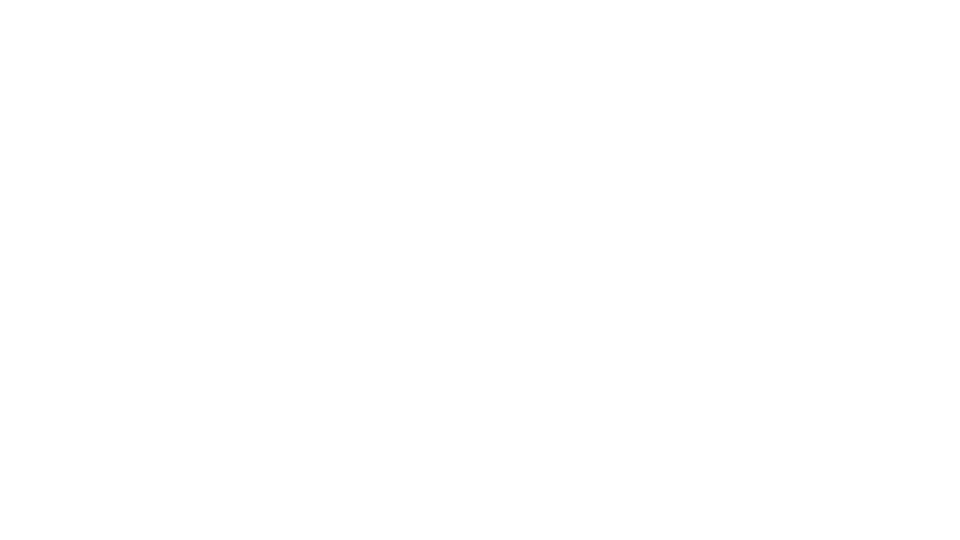
評論