最近,熱評估已成為電源管理系統中的熱門話題。隨著許多應用對功率要求的提高,應考慮熱管理以避免過熱。尤其是在芯片中集成了功率MOSFET的DC-DC轉換器產品,其功耗面臨著封裝尺寸和PCB布局面積有限的挑戰。因此,熱評估應包含在項目預覽中。Flotherm 是一款專業的熱模擬工具,用于模擬熱系統的真實情況,有助于減少不必要的試錯過程成本。在本應用筆記中,將討論電源管理系統熱模型的建模和驗證。
1. IC 熱模型建模
根據不同的應用和要求,有多種 IC 封裝。封裝尺寸、結構、材料、裸片尺寸和功耗曲線等幾個參數都會影響 IC 的熱阻。一般這些參數可以由IC產品工程師(PE)提供,根據上述參數開發熱模型。以下是一些適用于 DC-DC 降壓轉換器和 PMIC 的常見 IC 封裝。
1. 不同類型的 IC 封裝
圖2. 熱模型構建示例
圖 2 是安裝在 PCB 上的芯片的熱模型構建示例。IC 的熱模型由 die、die attach、lead-frame die pad 和焊膏組成,它們各自具有不同的熱導率,這取決于它們的材料。一般管芯的材料是硅,其電導率為117.5 W/(K·m)。其他材料特性例如可以參考下表1。導熱系數可能會隨著不同的材料而變化。請注意,物體的(絕對)熱阻(以 K/W 為單位)取決于熱導率、熱路徑的長度和橫截面:
其中 θ 是絕對熱阻,Δl 是熱路徑的長度, A 是熱路徑的橫截面積,k 是材料的熱導率。
表 1. IC 熱模型的熱導率
2. 電感熱模型建模
除 IC 外,電感可以看作是開關電源變換器系統中的第二大熱源。因此,電感熱模型的開發是必不可少的。與 IC 的模型類似,建立準確的電感器熱模型需要一些信息。首先,我們可以在數據表中找到電感的外形尺寸,包括長度、寬度和高度(見圖 3)。其次,由于外部障礙,內部結構是不可見的。有兩種方法可以獲取所需的參數。一種是拆掉電感,測量內部布線配置,如線材粗細、匝數等。另一種更溫和的方法是向電感器制造商詢問信息。然后您可以按照信息建立電感器的熱模型,如圖 4 和圖 5。
圖3. 電感器外形尺寸
圖 4. 制造商提供的電感器內部結構
圖5. Flotherm 開發的電感器熱模型
電感材料的導熱系數如表 2 所示。需要注意的是,大部分熱量會通過銅線傳遞到外部電源走線。這是因為銅的熱導率高于鐵氧體,所以大部分熱量會通過熱導率最高的路徑流動。
表2. 電感熱模型的熱導率
3. PCB熱模型建模
在對主要熱發生器(IC 和電感器)進行建模后,下一步是開發散熱器。在大多數使用 SMD 組件的電源轉換器中,PCB 對功耗起著重要作用。傳熱有三種方式:傳導、對流和輻射。當產生溫差時,熱量將開始從高溫區向低溫區流動。大多數熱量將選擇熱阻最小的路徑,即通過焊料到銅的 PCB 傳導。圖 6 顯示了安裝在 PCB 上的 IC 的熱阻網絡示例。
圖6. 熱阻網絡示例
花一些時間在 PCB 布局安排上是至關重要的。一般來說,PCB走 線越寬越厚,熱阻越小。但是,如果 IC 封裝尺寸較小,PCB 走線寬度也會受到限制。在傳熱和布局規則之間會有一個權衡。例如,開關節點的 PCB 走線應始終足夠大以維持電流,但也應足夠小以減少噪聲耦合。在具有多層設計的 PCB 中添加熱通孔是改善熱傳遞的一種解決方案。在 Flotherm 仿真工具中,建議將圓形 Vias 轉換為矩形 Vias,以減少收斂周期。使用公式(1)和(2)來完成轉換很簡單。圖 7 演示了轉換示意圖。
圖7. 圓形過孔到矩形過孔的轉換
4. 電源管理系統熱模型驗證
建立每個組件的熱模型后,就可以進行臺架測試以驗證熱模型的準確性。驗證分為兩個步驟。第一步是一次只用一個熱源檢查每個組件的準確性。第二步是使用熱模型檢查整個電源管理系統的準確性。
圖 8 給出了 RT6228 的 IC 熱模型。RT6228 是一款 HV 單 Buck 轉換器,封裝類型為 UQFN-12HL 3x3-56B (FC)。倒裝芯片的設計可以降低引線鍵合阻抗以提高效率,同時也會降低芯片到IC引腳的熱阻。需要注意的是,IC 熱模型的發熱區域將位于內部功率 MOSFET 的區域。在這種情況下,發熱區域位于芯片的下半部分。如果一個芯片中有多個導軌,比如 PMIC,就會有多個熱源。在這種情況下,應根據每個導軌的位置將加熱區域分開。
圖8. RT6228 的 IC 熱模型
RT6228 EVB 的熱模型如圖 9 所示。熱模型的布局是根據實際 EVB 完成的(圖 9 左側)。它是 1oz 四層設計,EVB 尺寸為 100mm x 72mm。許多熱通孔放置在 IC GND 和 VIN 平面中,以改善向其他層的熱傳遞。由于電源層和接地層是影響熱傳遞的主要因素,因此可以在 PCB 熱模型中簡化其他控制回路走線。
圖9. PCB 的熱模型
由于IC在沒有外部元件的情況下無法工作,因此芯片上產生的熱源是一個問題。另一種方法是通過內部功率 MOSFET 的體二極管注入恒定電流。為了確認不同功耗下熱模型的準確性,有三種不同級別的注入電流來加熱芯片。表 3 顯示了 IC 熱模型的驗證結果,以及仿真和實驗的外殼溫度比較。本實驗中,電流注入高邊MOSFET的體二極管產生功率耗散,環境溫度約為25°C。結果表明,仿真與實驗之間只有2%的溫度偏差。
表3. IC 熱模型驗證
電感器熱測量如下所示。與IC熱模型驗證類似,電感放置在PCB上,發熱源為電感銅線。功率耗散是由電感繞組的 DCR 通過將電流注入導線而產生的。電感器的功率損耗可以通過將電感器兩側的差分電壓乘以注入電流來計算。最后驗證結果如表4所示,測量與仿真的溫度偏差在3%左右。
表4. 電感熱模型驗證
此外,以下是使用熱像儀 (Fluke Ti450) 測量電感器外殼溫度時需要注意的一些技巧。由于電感封裝的反射系數高于IC封裝,因此IR測量會不準確。為了降低電感的反射系數,在電感表面貼一塊黑色電工膠帶,有助于提高發射率。圖 10 是電感溫度測量的示例。EVB放置在密封箱內,用于靜止空氣狀態,熱耦合器用于監測箱內環境溫度。使用熱像儀進行測量時,正確調整焦距對精度至關重要。此外,在每個測試條件下等待熱平衡至少 15 分鐘。
圖10. 電感溫度測量的實驗設置
在前面的步驟中,驗證了每個組件的熱模型精度。在下一步中,所有這些組件將被組合起來,以確認完整的電源管理系統。通過調整輸出反饋電阻,RT6228 可支持 0.6V 至 5V 的輸出電壓。為了驗證不同功耗的熱模型,有兩個實驗案例來驗證熱模型。詳細的仿真和實驗參數列于表 5 和表 6。在每個測試條件下,功耗被分為三個分量:IC 的功耗、電感的功耗和 PCB 走線的功耗。因此,仿真設置將取決于功耗的分布。此外,所有情況都是在 25°C 的環境溫度下完成的。仿真和實驗結果如圖 11 和圖 12 所示。對于案例 1,輸出電壓為 3.3V,負載條件為 6A。IC的功率損耗,PD_IC為 1.73W,電感器的功率損耗 P D_L為 0.93W,PCB 的功率損耗 P D_PCB為 0.3W。電感的功率損耗包括銅損和磁芯損耗,其中銅損通過I L 2 xDCR 計算,磁芯損耗可以在電感制造商的數據表中找到。在這種情況下,電感器 DCR 為3.3m W,鐵損約為 0.81W。PCB的功率損耗通過I PCB 2 xR PCB計算,其中PCB走線電阻可分為兩部分:一是輸入電容到VIN管腳的走線電阻,約為4m W, 另一個是 SW 腳到輸出電容的走線電阻,大約8m W。然后根據 (P D_IC = P D_TOTAL – P D_L – P D_PCB )計算 IC 功率損耗。仿真結果與實測實驗結果對比,IC外殼溫度幾乎相同,電感溫度偏差小于5%。對于案例 2,輸出電壓為 1V,負載條件為 6A。IC 的功率損耗 P D_IC為 1.53W,電感器的功率損耗 P D_L為 0.286W,PCB 的功率損耗 P D_PCB為 0.3W。在這種情況下,電感器 DCR 為 3.3m W鐵損約為0.167W。PCB 走線電阻與案例 1 中的相同。仿真結果與實驗結果對比,IC外殼溫度偏差僅為2%,電感溫度偏差小于5%。
表5 案例一的仿真和實驗參數
圖11. 案例 1 的仿真和實驗結果
表6 案例 2 的仿真和實驗參數
圖12 案例 2 的仿真和實驗結果
五、總結
在本應用筆記中,對電源管理系統熱模型的建模和驗證進行了說明。報告中描述了 IC、電感器和 PCB 熱模型的開發。驗證結果顯示仿真和測量之間的偏差很小。最后,通過精確的熱模型仿真,可以預測應用的熱行為,防止過熱等熱問題。這將有利于縮短開發時間并避免因反復試驗而產生的額外成本。
-
建模
+關注
關注
1文章
316瀏覽量
61481 -
電源管理系統
+關注
關注
0文章
60瀏覽量
16595
發布評論請先 登錄
IGBT模塊及散熱系統的等效熱路模型
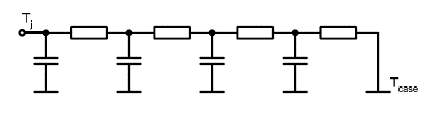
關于功能驗證、時序驗證、形式驗證、時序建模的論文
Saber軟件功率MOSFET自建模與仿真驗證
基于CFD建模進行PCB熱設計
基于CFD建模方法進行PCB熱設計應用
如何構建UVM寄存器模型并將寄存器模型集成到驗證環境中
AHB片上系統總線的建模與驗證
如何使用Soatherm進行MOSFET熱模型的設計
熱管理系統建模案例:模型工具、熱管理系統
基于RC熱阻SPICE模型的GaNPX?和PDFN封裝的熱特性建模
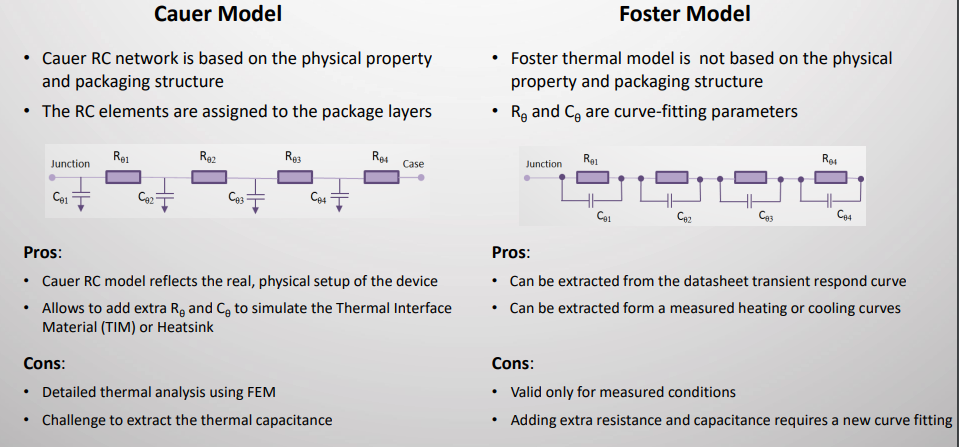
評論