軸承套圈的金屬流線
目前,生產中小型軸承套圈主要有冷擠壓、鋼管車削、熱鍛和冷輾擴4種方法,而使用常規的金相檢測手段根本無法區分這4種方法生產的軸承套圈。通過研究發現,這4種工藝生產的軸承套圈的流線存在一定的區別,可以通過觀察流線來區分軸承套圈的生產途徑。
1觀察軸承套圈流線的方法
觀察軸承套圈的流線需要在縱向試樣上進行,將套圈縱切面經拋光后用5%的苦味酸酒精溶液進行浸蝕,用放大倍數為10~20倍的顯微鏡對切面進行直接觀察,可以很清晰地看到其流線。
2各加工工藝制造的軸承套圈的流線
流線是金屬中的低熔點成分和帶狀組織偏析在軋制或擠壓時伸展而形成的[1]。流線形成后,用一般的熱處理方法不能消除。以下介紹這4種不同生產方式加工的軸承套圈的金屬流線。
2.1冷擠壓
冷擠壓,又稱冷鍛,是把金屬毛坯放在冷擠壓模腔中,在室溫下,通過壓力機上固定的凸模向毛坯施加壓力,使金屬毛坯產生塑性變形而制得零件的加工方法。其特點為:
(1)比切削加工和其他鍛壓生產節約材料。
(2)可以高效率地加工形狀復雜的零件。
(3)冷擠壓件的尺寸和形狀精度高,表面質量好,且提高了力學性能。
軸承套圈毛坯冷擠壓一般采用套料單圈復合擠壓工藝,其生產流程如圖1所示。外圈采用復合擠壓原理生產,內圈用單圈反擠壓原理生產,所以外圈和內圈的流線也不相同。復合擠壓時坯料上的一部分金屬順著凸模運動方向流動,而另一部分的流動方向則相反,外圈毛坯經車削后的流線如圖2所示。單圈反擠壓使金屬的流動方向與凸模的運動方向相反,內圈毛坯經車削后的流線見圖3。
2.2鋼管車削軸承套圈的流線
由于軸承鋼管內、外徑精度較高,總脫碳層深度淺,有利于少切削或微切削工藝制造軸承套圈,也有利于精密輾擴軸承套圈[2]。鋼管本身的流線是沿拔制方向延伸,經車削后溝道部分的流線被切斷。鋼管車削軸承套圈的流線見圖4。
2.3鋼管冷輾擴軸承套圈的流線
冷輾擴可使套圈毛坯的形狀極大限度地接近成品的形狀,從而顯著地提高材料利用率和零件的精度,節省部分車加工、磨加工工序,提高磨削效率。同時由于采用了無切削輾擴加工工藝,使零件內部金屬流線得到改善,大大提高了軸承的使用壽命,因此軸承套圈冷輾擴技術作為一種無切削加工工藝越來越受到軸承制造業的重視[3]。鋼管經過冷輾擴加工后,其內部的流線按工件表面形狀延伸。經冷輾擴后軸承套圈的流線見圖5。
2.4熱鍛→車削軸承套圈的流線
熱鍛是生產軸承套圈毛坯的傳統工藝。國內目前普遍采用中頻感應對坯料進行加熱,再經截料,墩壓,沖孔,擴孔等工序生產軸承套圈。中頻感應加熱用于熱鍛主要有省電節能;安裝、操作方便;快速透熱,減少表面氧化,節省材料;可避免表面脫碳,提高鍛件質量;提高模具壽命;極大地改善工作環境;生產成本低等優點,因此近幾年得到了迅速發展。熱鍛件經車削后流線見圖6。
2.5熱鍛→車削→冷輾擴軸承套圈的流線
熱鍛件經車削后再進行冷輾擴也是生產軸承套圈的途徑之一。熱鍛件經車削再進行冷輾擴后的軸承套圈的流線如圖7所示。
-
結束語
實踐證明,采用觀察流線的方法可以有效地分辨出各種不同的套圈成形方法,有利于進行產品的失效模式分析,且簡便可靠。
(運轉世界大國龍騰 龍出東方 騰達天下 龍騰三類調心滾子軸承 劉興邦CA CC E MB MA)
熱處理工藝對軸承尺寸穩定性的影響
軸承是一種精密的機械基礎件,內圈及外圈尺寸的精度直接影響著安裝質量、軸承的各種性能.因存儲條件引起的尺寸變化,會造成軸承在使用時,出現早期失效[1]。為此,筆者通過改變軸承熱處理工藝路線的方法,對影響軸承尺寸穩定性的因素,做了下列研究。
1試驗方法
1.1試驗工藝方案
以車加工后的6204、6209軸承內圈為例,各取40件樣品進行試驗.改變熱處理工藝路線的淬、回火工藝參數,分4組進行試驗,每1組10件,工藝方案見表1。使用的設備為:振底式淬回火自動生產線。
1.2熱處理質量
四種試驗工藝方案經熱處理后,其硬度平均值均在62~63HRC,硬度值和淬火、回火組織均符合JB/T1255標準規定,測量結果見表2。
2試驗結果及分析
2.1試驗結果
兩種軸承內圈,分別按照四種試驗工藝方案,經過磨削加工之后(其中第4種工藝方案,經過附加回火處理)存放四個月。軸承內孔尺寸,每月測量一次,為了減小測量誤差,每次測量均使用同一臺儀器和標準件,且測量前標準件和被測工件一起恒溫4h。實際測量的內孔尺寸數據整理后,與存放之前的初始尺寸之差的平均值如表3,變化曲線如圖1所示。
2.2試驗結果分析
(1)從表3和圖1、圖2可以看出,隨著存放時間的增加,兩種軸承的內孔尺寸總的變化趨勢是增大。這說明,盡管熱處理后的硬度及金相組織合格,但是,軸承鋼在低溫回火過程中殘余奧氏體不可能完全轉變,在奧氏體化溫度為840℃,工件冷卻至室溫時,殘余奧氏體含量可達12%,這些殘余奧氏體隨著時效逐漸轉變為馬氏體,從而引起工件尺寸漲大。
(2)第2種工藝方案,其尺寸變化量最大。這是由于淬火油溫較高,使軸承鋼淬火過程中組織不能充分轉變,因而殘余奧氏體含量較高.而延長回火時間對薄壁零件的組織轉變沒有明顯的影響。所以造成回火后工件尺寸變化比較大。
(3)第3種工藝方案的尺寸穩定性效果非常明顯,這說明軸承鋼在淬火后、回火前經過充分冷卻能起到減少殘余奧氏體的作用。
(4)工件的直徑和橫截面積的大小同樣影響殘余奧氏體的含量,直徑和橫截面積越大,殘余奧氏體含量也越大,造成工件尺寸膨脹越大。
(5)第4種工藝方案的工件粗磨之后進行附加回火處理,尺寸穩定性很明顯,這是因為附加回火能夠消除部分磨削應力,能夠起到進一步穩定組織的作用。
4種工藝方案中,工件隨存放時間的變化是跳躍式的,這說明工件在淬回火后馬氏體和奧氏體的組織轉變都是不充分的,而是隨著時效逐漸轉變。當殘余奧氏體轉變占主導地位時,工件尺寸就變大;而馬氏體回火轉變占主導地位時,工件尺寸就收縮。
3結語
(1)回火前的清洗冷卻工序,要根據不同的工件類型,制定相應的清洗時間和溫度,特別是夏天淬火、回火自動生產線上的循環清洗系統應增加冷卻裝置。
(2)工件粗磨之后,應進行附加回火處理,能夠起到穩定尺寸的作用。
(3)對于尺寸穩定性要求較高的精密軸承和中大型薄壁軸承必須采用附加回火或冷處理工藝。
審核編輯:符乾江
-
軸承
+關注
關注
4文章
2110瀏覽量
31156 -
金屬
+關注
關注
1文章
592瀏覽量
24305
發布評論請先 登錄
相關推薦
軸承結構生產工藝流程柴油機軸承的結構與安裝
鳳凰動力舵輪驅動輪的穩定性如何影響AGV的運行效率和穩定性
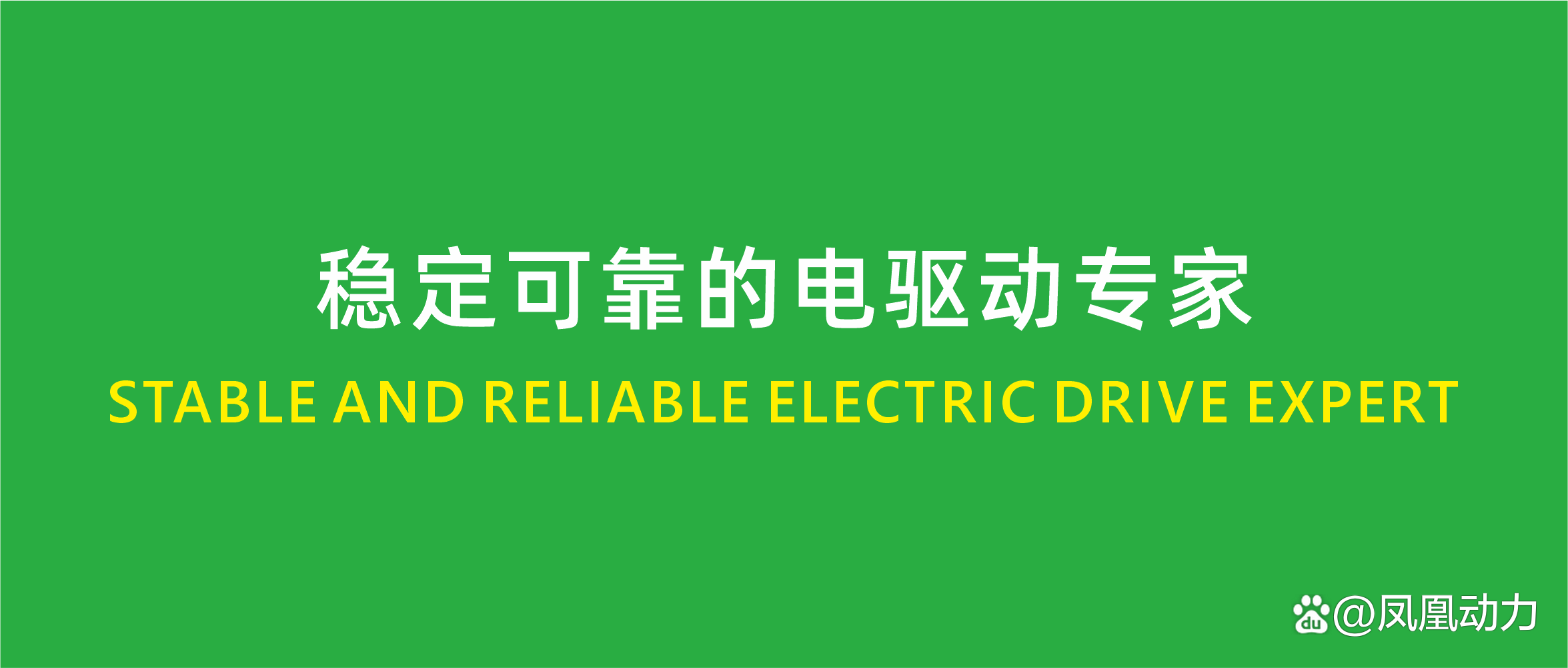
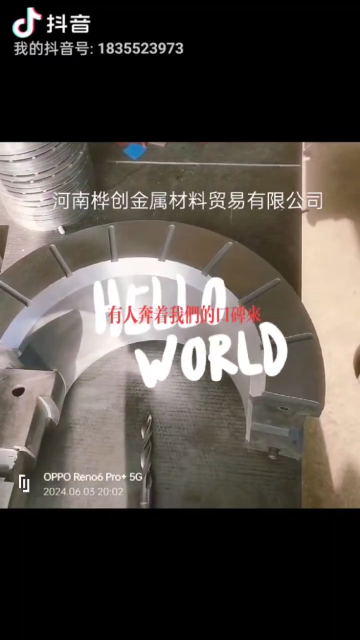
評論