編者按
采用自主研制的固相摩擦擠壓增材制造設備,針對6061-T651鋁合金進行摩擦擠壓增材制造(Friction Extrusion Additive Manufacturing,FEAM)工藝試驗,探討固相摩擦擠壓增材工藝可行性、工藝參數與沉積層成形及缺陷相互影響,分析討論6061鋁合金單道多層FEAM試樣增材沉積成形、界面連接機制及力學性能變化規律,為在鋁合金結構制造領域實現FEAM技術的工業化應用提供了重要試驗依據。
1 序言
高強鋁合金具有密度低、強度高、耐腐蝕及優異斷裂韌性與塑性成形性等特點,是僅次于鋼鐵材料的在工業制造領域廣泛應用的結構材料之一。傳統的鋁合金結構采用鑄造、鍛造、焊接及粉末冶金等整體工藝加工制造,由于工藝流程長、需要大型加工設備及復雜工裝模具等,因此會增加制造成本與時間,很難適應先進制造工業的發展趨勢。
金屬增材制造技術的發展為實現輕量化鋁合金復雜結構自由設計及快速制造提供了新途徑。然而,由于鋁合金具有熔點低、熱裂敏感及容易氧化等固有冶金局限性,針對目前在工業領域已廣泛應用的2000、6000或7000系列的鍛造鋁合金,采用激光及熔絲電弧增材制造很難獲得無孔隙、裂紋及夾雜等冶金缺陷的鋁合金增材構件,因此限制了熔焊增材制造技術在輕量化鋁合金結構制造領域的廣泛應用[1,2] 。
與熔焊工藝比較,固相摩擦焊是材料加工領域具有特色的先進加工技術,其關鍵優勢是:金屬材料不存在熔化現象、避免了熔化結晶凝固過程中各種冶金缺陷,所獲得的焊縫組織致密、晶粒細小、強度與韌性明顯較高,尤其是能實現熔焊性差的高強鋁合金焊接;為開發一種獲得高性能鋁合金增材構件的固相摩擦擠壓增材制造技術提供了重要基礎。
目前,國外研究者已將逐層沉積原理與固相摩擦焊工藝結合起來,對可能實現的固相摩擦擠壓增材制造工藝進行了許多探索試驗研究,如摩擦沉積(Friction Deposition,FD)[3] 、摩擦堆焊(Friction Surfacing,FS)[4] 、復合金屬擠壓與連接增材(Hybrid Metal Extrusion & Bonding,HYB)[5] 、攪拌摩擦增材(Friction Stir Additive Manufacturing,FSAM)[6,7] 及增材摩擦攪拌沉積(Additive FrictionStir Deposition,AFSD)工藝等 [8]。
其中,由美國Aeroprobe公司研制開發的AFSD具有顯著優勢,是目前唯一可實現增材路徑自由成形的固相摩擦擠壓增材工藝方法。2018年該公司開發了基于AFSD的商業化3D打印設備,并采用新術語“MELD”表征這種變革工藝,同時成立專門MELD設備公司進行工業化推廣應用。
試驗表明,MELD工藝可成功實現各種鋁合金(1xxx系、2xxx系、5xxx系、6xxx系及7xxx系)、鎂合金(AZ31、AZ91及WE43等)、銅合金(Cu110及Cu185)、不銹鋼(316L)、鎳基合金(Inconel625、718等)、鈦合金(Ti-6Al-4V)與金屬基復合材料(Al-SiC、Al-W及Al-Mo)等材料的增材制造,增材沉積速率高(鋁合金增材沉積速率>1000cm3/h)、增材內部殘余應力明顯低于熔焊增材工藝[9] 。
MELD不僅能用于同種及異種金屬增材制造與焊接過程,還可應用于金屬表面涂層加工、金屬結構修復強化、功能梯度材料及金屬基復合材料制備等,在鋁合金結構增材制造及修復強化領域顯示出巨大應用潛力。由于缺乏設備,故在國內很少見到有關MELD工藝研究的公開報道。
本文對固相摩擦擠壓增材制造工藝原理進行分析討論,通過自主設計研制基于MELD工藝的固相摩擦擠壓增材制造設備,對6061鋁合金的固相摩擦擠壓增材制造工藝、沉積成形及力學性能進行試驗探討,為在國內推廣應用這種特色金屬固相增材制造技術提供參考依據。
2 固相摩擦擠壓增材制造工藝原理
固相摩擦擠壓增材制造工藝原理如圖1所示。在中空的非消耗軸肩內部有填充棒料,軸肩與基板表面保持給定空間,軸肩帶動填充棒料以相同角速度高速旋轉,在軸向壓力作用下填充棒料持續摩擦擠壓基板表面,從而產生強烈摩擦熱和剪切塑性變形,導致材料軟化產生塑性流動,從而填充軸肩與基板表面之間的間隙;隨著軸肩沿基板表面橫向移動,被軟化材料與基板產生冶金連接,并沉積在基板表面形成增材層;沿給定加工路徑重復上述操作即可形成單道多層增材構件。基于上述工藝原理,我們自主設計研制成功實現填充材料的固相摩擦擠壓增材設備及試驗平臺,為進行增材工藝試驗提供基礎。
圖1 固相摩擦擠壓增材制造工藝原理
由于固相摩擦擠壓增材制造采用消耗填充棒料自身“摩擦擠壓”基板,所以填充棒料既產生摩擦熱源又是被加工材料,通過摩擦擠壓使得填充棒料軟化后直接沉積到基板上形成增材,在沉積過程中消耗棒料將受到強烈摩擦擠壓剪切塑性應變作用,由此可見“摩擦與擠壓”是該工藝的關鍵特征。因此,為有效反映摩擦擠壓塑性成形的強烈熱-力耦合冶金加工特征,本文采用術語“固相摩擦擠壓增材制造(Friction Extrusion Additive Manufacturing,FEAM )”表征這種特色固相增材制造技術[10]。
3 試驗材料及方法
試驗采用6061-T6鋁合金作為基板,尺寸為300mm×100mm×5mm,填充棒料為6061-T651鋁合金,其直徑為20mm、長度為200mm。6061屬于可熱處理強化鋁合金,具有高比強、高模量、高延展性及塑性成形特性等,在航空航天、汽車工業及機械工程領域等具有廣泛應用。全部增材工藝試驗在天津大學固相摩擦焊研究室研制的FEAM設備上完成。在大量探索工藝試驗基礎上,選擇的FEAM試驗工藝參數見表1。
為評估FEAM工藝過程及增材試樣組織特征,采用TOPRIE TP9000多路數據記錄儀及鎳鉻K型熱電偶對增材試樣沉積層間熱循環曲線進行測試,探討工藝過程熱循環曲線變化規律。為進行增材試樣組織及力學性能分析,分別定義增材試樣長度、寬度和厚度方向為X、Y、Z(見圖1)。試驗結束后沿Z方向切割金相試樣,進行機械拋光及腐蝕處理;分別使用超景深立式顯微鏡和Olympus GX 51光學顯微鏡進行宏觀形貌和顯微組織觀察;使用JEOL 7800熱場電子掃描顯微鏡(SEM)在背散射模式下進行增材結晶相觀察;采用Tecnai G2 F30透射電子顯微鏡(TEM)對增材試樣第二相種類、尺寸及密度進行觀察表征。為探討增材層組織均勻性及性能各向異性,采用HVS-1000顯微硬度計對單道多層增材試樣的不同位置進行顯微硬度檢測,檢測位置如圖2所示。
圖2 硬度檢測位置
硬度測試載荷為100g,加載時間為15s,相鄰測試點間隔1mm。對增材試樣分別沿X、Y、Z方向不同位置線切割加工制備微小拉伸試樣,取樣位置和尺寸如圖3所示。
圖3 拉伸試樣取樣位置及尺寸
分別應用電子萬能拉伸試驗機(CSS-44100)和Instron2710-004微小力學測試系統進行拉伸試驗,拉伸速率分別為1mm/min和0.3mm/min。最后采用掃描電鏡(SU1510)對不同增材試樣、不同方向的拉伸試樣斷口進行組織觀察和EDS分析,并探討增材試樣斷裂模式。
4 結果分析與討論
FEAM主要工藝參數包括軸向壓力F、軸肩工具轉速ω、移動速度v和增材層厚d。其中F和ω是決定摩擦熱量的關鍵因素,F太小時,即使增加ω也無法形成有效的摩擦熱量;當F超過一定值后,隨著ω增加,摩擦熱量將不斷增加、送料速度也將不斷增加。v及d決定著增材沉積效率高低,v越大則沉積效率越高,但必須與ω及F相匹配,否則將形成不連續沉積寬度,導致工藝過程不穩定;而d是由預先設置的軸肩與基板之間的空間控制,增加d同樣提高沉積效率,但d過大時,將影響沉積層界面之間的結合強度。因此,只有上述工藝參數在優化范圍內變化時,才能實現有效的增材沉積過程。
在FEAM過程中,填充棒料承受轉矩的變化規律如圖4所示,對應沉積工藝參數ω=600r/min、v=300mm/min、F=10kN、d=4mm。從圖4可看出,FEAM工藝過程可劃分為沉積前預熱、摩擦擠壓沉積過程和快速冷卻三個階段。首先,填充棒料與基板表面開始接觸摩擦導致轉矩T快速上升達到峰值;然后,棒料軟化產生強烈剪切塑性擠壓變形,連續填充軸肩工具與基板表面之間空間,使得轉矩迅速降低到平衡點以下近似穩定值,填充棒料進入穩定摩擦擠壓沉積階段;最后,沉積結束停止旋轉,轉矩迅速降為零。沉積過程工藝穩定階段的摩擦熱功率(Tω)近似為恒定值。
圖4 FEAM過程中填充棒料承受轉矩的變化規律
FEAM過程中沉積層底部不同位置熱循環曲線變化規律如圖5所示。其中,所測試的峰值溫度為430~464℃;其峰值溫度近似為鋁合金熔點(580~650℃)的72%~80%,其加熱和冷卻速率分別為33~50℃/s和3.6~5℃/s(從最高溫度降至100℃時的近似冷卻速率)。這表明FEAM為完全固相增材沉積過程并具有較高冷卻速率。
圖5 FEAM過程中沉積層底部不同位置熱循環曲線變化規律
FEAM過程中產生的宏觀與微觀缺陷分別如圖6、圖7所示。填充棒料塑性流動與沉積缺陷形成直接相關,由于工藝參數不當,所以會產生飛邊、不連續、未連接、弱連接及孔洞等缺陷。當軸向壓力過大、移動速度較慢時,填充材料軟化嚴重,被擠出軸肩邊緣形成飛邊,造成材料沉積效率降低;而當軸向壓力較小、移動速度過快時,填充材料沉積不連續增加。
軸向壓力過大導致送料速度明顯增加,有可能導致填充材料堵塞軸肩內孔,使沉積工藝失敗。沉積工藝參數匹配不合適,還會導致沉積層界面產生弱連接或未連接缺陷,明顯降低沉積層界面結合強度。這將對FEAM力學性能產生嚴重不利影響。
圖6 FEAM宏觀缺陷
圖7 FEAM微觀缺陷 圖8所示為FEAM的增材層厚d及軸肩表面特征對沉積層及界面結合狀態的影響。增加d時,將減小軸肩對沉積層界面的摩擦加熱作用,使沉積層界面產生弱連接缺陷,降低界面結合強度;減小d時,有利于提高沉積層界面結合強度,但降低增材沉積效率。當采用帶凸臺的軸肩工具時,由于凸臺對沉積層的強烈摩擦擠壓攪拌作用,使沉積層及界面附近產生明顯的塑性流動宏觀變形特征,這將更好地促進沉積層界面上下材料的混合,從而獲得更高界面結合強度(見圖8a)。
而采用平面軸肩時沉積層界面基本為平直狀態,界面附近材料塑性變形流動特征并不顯著(見圖8b)。帶凸臺的軸肩工具有利于沉積界面的冶金結合,但會增加軸肩工具承受的轉矩,從而影響沉積工藝過程穩定性。
圖8 不同增材層厚下FEAM沉積層截面形貌
不同轉速下單道雙層及單道九層增材試樣截面宏觀形貌分別如圖9、圖10所示。從圖9、圖10可看出,除兩側部分區域可能存在不良結合外,沉積層內部區域均為完全致密組織,這說明FEAM屬于近凈成形增材制造工藝,最終增材還需要加工去除兩側結合不良區域。
但增材內部宏觀組織均勻,不存在孔隙、裂紋及夾雜等冶金缺陷,由于采用平面軸肩工具,沉積層界面塑性變形小,基本為平直狀態,多層沉積的熱循環作用沒有對增材宏觀成形產生顯著影響。因此,采用軸肩轉速400r/min、600r/min和800r/min與移動速度300mm/min工藝可成功獲得每層增材厚度約為4mm的致密無缺陷的FEAM增材試樣。
圖9 單道雙層增材試樣截面宏觀形貌
圖10 單道九層增材試樣截面宏觀形貌 同轉速下單道雙層增材不同位置的微觀組織如圖11所示。從圖11可看出,由于連續摩擦擠壓熱-力耦合作用,沉積層及界面附近產生連續動態再結晶并實現擴散冶金連接,因此多層增材均呈現均勻細小等軸晶組織特征,平均晶粒尺寸不超過(8.84±1.76)μm。
沉積層界面由于直接承受剪切塑性應變作用,所以其晶粒稍微細小(7.68±1.73)μm;與原始填充棒料母材晶粒平均尺寸(24.21±5.3)μm比較,增材微觀組織產生顯著細化現象。雖然不同沉積層受到軸肩轉速變化及多層熱循環累積作用,但不同位置晶粒細化趨勢及尺寸并沒有明顯差異,這說明在FEAM中細小等軸晶組織具有良好的分布均勻性及穩定性。
圖11 單道九層增材微觀組織
600r/min轉速下單道雙層增材試樣顯微硬度分布如圖12所示。試驗結果表明,一層底部、中間、頂部及界面的平均硬度分別達到填充棒料母材的60.7%、61.5%、59.4%、56.9%;二層底部、中間及頂部的平均硬度分別達到填充棒料母材的60.5%、64.2%和68.0%。
雖然產生明顯軟化現象,但具有較好的均勻性,說明雙層增材的各向異性差異較低。單道九層增材硬度分布云圖如圖13所示。隨著沉積層數增加,增材頂部硬度值可達到70HV0.1以上;但由于多層熱循環作用,所以其余大部分區域硬度有所降低,600r/min與400r/min兩種轉速下的平均硬度值分別為55.1HV0.1 、57.1HV0.1,具有相對均勻硬度分布特征,說明多層增材的硬度仍具有相對低的各向異性差異。
圖12 單道雙層增材試樣不同位置顯微硬度分布
圖13 單道九層增材硬度云圖
600r/min下單道九層增材試樣組織的TEM圖像如圖14所示。由于6061為熱處理強化鋁合金,所以其析出相轉變為:過飽和固溶體→Mg、Si原子團簇→β‘’相→β‘相+Q’相→β相+Q相,其中各種析出相是其主要強化機制。
而FEAM中熱循環峰值溫度(見圖5)已超出β‘’相、Q‘相和β’相的溶解溫度,并具有較高冷卻速率;加之劇烈熱-力耦合作用,使頂層增材β‘’相大部分溶解,β‘相則發生明顯粗化,Q’相也部分溶解到基體中;而在界面附近析出相全部溶解,僅剩球狀的結晶相,析出強化明顯降低。試樣底部經歷多次熱循環,使β‘’相溶解更為充分、β‘相更加粗化。因此,多層沉積態增材內部不可避免地會產生硬度降低/軟化現象。
圖14 單道九層增材試樣TEM圖像
400r/min下單道九層增材試樣X及Z方向拉伸性能比較如圖15所示。沿X方向多層增材頂部抗拉強度可達到231MPa;但隨著遠離試樣頂部,增材試樣內部所受熱循環次數逐漸增加,從頂部到底部抗拉強度呈現先減小后趨于穩定的特征,除頂層區外,增材大部分區域平均抗拉強度為186MPa,中部與底部拉伸曲線基本類似;達到填充棒料母材的55%;但平均斷后伸長率可達45.1%。
沉積層塑性變形能力因沉積區晶粒細化而明顯優于母材。沿Z向增材試樣中間區域的抗拉強度最高為173MPa,平均抗拉強度為165MPa,可達到X向強度的88.9%,但只有填充棒料母材的47%;而增材試樣前進側(AS)及后退側(RS)的抗拉強度與中部基本類似,但伸長率有所降低,這說明沿增材不同方向的抗拉強度既存在明顯軟化現象,還存在較大各向異性特征。
對于單道多層增材試樣,由于中部和底部沉積層經歷多次熱循環作用,這不僅使增材層內的強度降低,也使界面的結合強度降低。而沿Z向即垂直于沉積層界面的拉伸性能,是評估界面冶金結合強度的關鍵指標,它受到工藝參數、增材厚度及軸肩表面形狀的顯著影響,對此還需要進行大量的FEAM工藝優化試驗和深入研究。
圖15 單道九層增材X向與Z向拉伸性能比較 5 結束語
本文基于自主研制的固相摩擦擠壓增材制造設備,對6061-T651鋁合金FEAM工藝可行性,以及工藝參數對增材成形、界面連接機制及力學性能進行初步試驗探索,獲得以下主要結論。
1)在軸肩轉速400r/min、600r/min和800r/min與移動速度300mm/min工藝下,成功實現6061鋁合金FEAM工藝過程,獲得每層增材厚度和寬度分別約為4mm和32mm的單道雙層及九層增材試樣,沉積層內部完全致密,不存在孔隙及裂紋冶金缺陷,沉積層界面可實現良好的冶金連接。
2)FEAM工藝參數選擇不當時,有可能產生飛邊、不連續、未連接、弱連接及孔洞等成形缺陷。其中,軸向壓力、軸肩轉速、移動速度、增材厚度及軸肩表面形狀是影響沉積層成形和界面結合強度的關鍵因素。
3)FEAM具有均勻細小等軸晶組織特征,多層增材平均晶粒尺寸不超過7.62μm。由于析出強化相的溶解與粗化,因此多層增材內部產生顯著軟化現象,但硬度分布具有較好均勻性,其平均硬度不超過填充棒料母材的50.4%。
4)FEAM多層增材試樣X向抗拉強度可達到填充棒料母材的55%,而垂直沉積層界面Z向抗拉強度僅為母材的47%,增材不同方向拉伸性能存在較大各向異性,對此還需要進行大量的FEAM工藝優化試驗和深入研究。
審核編輯 :李倩
-
焊接
+關注
關注
38文章
3150瀏覽量
59851 -
增材制造
+關注
關注
0文章
256瀏覽量
12802
原文標題:高強鋁合金固相摩擦擠壓增材制造工藝全解析
文章出處:【微信號:xincailiaozaixian,微信公眾號:新材料在線】歡迎添加關注!文章轉載請注明出處。
發布評論請先 登錄
相關推薦
增材制造原材料有哪些種類
增材制造的特點是,因此適于進行什么加工
增材制造技術有哪些類型和特點
增材制造技術的常見工藝方法有哪些
增材制造技術原理及應用有哪些
增材制造技術是干什么的 增材制造技術有哪些類型
3分鐘帶你讀懂綠展科技增材制造
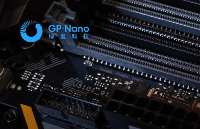
評論