摘要:提出一種家具板件幾何尺寸測量機器視覺系統,采用兩級成像排除板件的顏色、紋理、圖案、標識和表面缺陷等對圖像質量的影響,并利用線性聚焦光源、線掃描相機和編碼器獲取高對比度、輪廓清晰的板件圖像。在此基礎上,設計圖像處理軟件、提取出板件的幾何要素,進而計算出板件的長度、寬度、對角線等15個尺寸參數。工廠應用測試結果表明,檢測系統的速度和重復精度均高于人工測量,在測量誤差±0.5 mm范圍內,系統測量值與人工測量值的平均吻合度達到95%以上。
目前我國家具制造行業已經進入個性化定制和大規模集成化生產的新階段。各大型家具公司普遍采用自動化流水線加工各類家具板件,但是其尺寸測量還主要采用人工使用游標卡尺和卷尺抽查方法,主觀因素影響大、精度低、速度慢,已經成為家具行業生產自動化的瓶頸問題。
近年來,隨著CMOS成像技術和數據傳輸技術的飛速發展,計算機獲取和處理圖像的能力從每秒幾十幅提高到上萬幅。機器視覺將人工智能與CMOS成像技術、數據傳輸技術和計算機技術等結合起來,以非接觸的方式每秒獲取和處理數千萬個圖像數據,并在成像識別、缺陷檢測和尺寸測量中獲得了巨大的成功。Ergün B等[1]將數字近景攝影測量系統應用于工業大尺寸板件的測量,精度達到0.001 mm,但是操作復雜、計算量大、速度慢,難以滿足大尺寸板件快速測量的要求。瑞士Baumer公司研制了基于激光三角測量傳感器的板件尺寸檢測系統,但結構復雜、功能有限、造價太高,難以在國內家具行業推廣使用[2]。
隨著全球加工制造業向中國的轉移,國內加緊了板件尺寸檢測機器視覺系統的研制。2017年公開了一種基于面陣相機的板件尺寸檢測機器視覺系統[3],相機在板件上方移動并對準檢測中心后靜止拍攝圖像,用計算機處理圖像并計算各幾何要素的尺寸,其主要不足是尺寸檢測的精度只有±1 mm,速度慢,且大尺寸板件檢測困難。2018年武昌首義學院開發了一種基于機器視覺的通用平面尺寸檢測軟件系統[4],實現多個尺寸同時測量,但是需要人工提取感興趣區域,難以實現在線高速的自動化檢測。還有一種基于機器視覺的機加工件尺寸測量系統,通過多個圖像傳感器耦合,對機械零件進行圖像采集、處理并將測量結果實時反饋到控制端,實現機械零件的尺寸測量[5],但該系統速度慢,亦難以實現在線高速檢測。2019年在“基于機器視覺的大尺寸工件自動測量系統”[6]一文中提出了基于改進隨機抽樣一致性的亞像素直線/圓弧檢測算法,但是該系統只能獲取和處理板件的局部圖像信息。文獻調研表明,迄今為止,國內外在板件視覺測量的成像方法和圖像處理等方面取得了一定進展,但是尚沒有研制出應用到生產實際的機器視覺系統。
筆者研制了一種基于機器視覺的非接觸式家具板件尺寸在線測量系統,能以60 m/min的速度在線測量長度240~2 600 mm、寬度140~800 mm、10種典型顏色與紋理的家具板件,其重復檢測標準差小于0.05 mm,與人工使用游標卡尺測量結果的吻合度達到95%以上,為家具板件尺寸的機器視覺檢測探索新徑。
1 機器視覺測量系統簡介
機器視覺測量系統的結構與工作原理如圖1所示。
本機器視覺系統由預檢成像系統和二次成像系統兩部分組成。預檢成像系統由一臺近距離拍攝的MGS036-H面陣相機和LED平面陣列光源組成,獲取待檢測板件的640像素×480像素局部圖像。預檢系統通過支持向量機識別局部圖像的顏色和紋理,判斷板件的型號并向成像系統發送成像曝光參數,同時為圖像處理設定最佳的二值化閾值。
成像系統由高精度線掃描相機、LED線性聚焦光源和光柵編碼器構成。光柵編碼器實時監測待測量家具板件的傳輸速度,并向線掃描相機發送采樣脈沖。線掃描相機以每行16 000像素、每0.05 mm掃描1行的速度連續獲取板件的全局圖像。
對應于寬800 mm、運行速度60 m/min的機器視覺傳送帶,縱向每0.1 mm有2個像素點;橫向每行采樣16 000個像素點,即橫向每0.1 mm有2個像素點。成像系統的精度保證了系統測量的精度。
控制設備選用Intel i7芯片,8G內存,Nvidia GTX1080顯卡。工控機實時控制預檢系統和成像系統,連續處理圖像并計算出板件的幾何尺寸,然后顯示、輸出檢測數據。
2 軟件與圖像處理算法設計
測量系統的算法流程如圖2。
圖2 算法流程框圖Fig.2 Algorithm flow chart
家具板件傳輸到二次成像系統時,線掃描相機按照預檢系統給出的曝光參數獲取家具板件的高精度圖像。工控機對圖像做腐蝕、膨脹、邊緣增強、銳化等預處理,以排除圖像噪聲的干擾,并按照預檢系統給出的二值化閾值對圖像二值化,在此基礎上再提取板件的幾何要素特征,最后計算板件的長、寬和對角線等幾何尺寸。
2.1 預檢算法
高速拍攝的板件圖像只包含板件的局部顏色、紋理等信息,本系統采用支持向量機的非線性映射算法將低維空間線性不可分的樣本轉化為高維特征空間,使其具有線性可分性。
維向量的目標函數為:
(1)
其中為核函數。
分類決策函數為:
(2)
通過多次迭代獲得分類器,然后用分類器識別板件的顏色、紋理和型號,最后確定檢測板件的成像參數和二值化閾值。
2.2 板件邊沿提取
家具板件的邊沿有1~2 mm的圓弧過度封邊帶。如圖3所示,對應的圖像邊沿呈現過渡帶區間灰度值變異點。這些變異點對圖像邊沿的識別帶來干擾,影響長度和寬度的測量精度。本系統的邊沿算法如下:
圖3 家具板件圖像邊沿的灰度過度帶
一個點到直線的距離用
表示。所謂直線擬合,即找到一條直線,使得各點到這一直線的距離之和最小,即目標函數
最小。
(3)
其中:—直線擬合的距離函數,
—擬合點數。本系統采用基于Huber損失函數的邊沿直線擬合算法以增強函數對干擾點的魯棒性,
可表示為:
常量值能改變干擾點對距離函數的權重,確定經驗值常量
。
2.3 尺寸標定
本系統在橫向方向和縱向方向采用不同的轉換方式將像素轉換成尺寸,輸出尺寸最小單位為0.1 mm。根據三角投影關系,圖像橫向的像素所對應的實際尺寸與其光程位置相關。因此,需要利用分段函數得到橫向各特征像素點對應尺寸:
(5)
式中:—待測量的橫向像素位置,
—原始點的橫向像素位置,
—橫向區間分段函數。
假設為第
段,則
表示:
(6)
一般當為足夠大時,
為一次函數。
縱向尺寸標定時,傳送帶的線速度用編碼器的脈沖數精確計量,相機的掃描速度由編碼器的脈沖激發控制。設為單位長度內編碼器的脈沖數,
的數值隨傳送帶的速度波動而變化。設板件的縱向尺寸為
:
(7)
其中:—待測量的板件的縱向像素距離;
—對應家具板件封邊帶尺寸。
3 工廠應用試驗結果與分析
試驗環境為某大型家具工廠柜身生產車間,機器系統經受車間溫度、濕度、粉塵和噪聲的環境考驗。實驗樣本為顏色、紋理特征不一的10種常見型號的家具板件,包含刨花板家具和實木板家具兩種類型的家具板件共1 022塊,長度240 ~1 500 mm,寬度200~650 mm不等。每塊板由3個質檢員用2級精度的游標卡尺分別測量板件的平均長度、平均寬度、孔徑、孔心的X和Y坐標、槽寬、槽長、槽中心相對于基準邊的縱向和橫向尺寸;兩條對角線長度、板件上、下底寬度和左、右邊的長度等15個尺寸參數。求出3人測量的平均值和重復性標準差,并統計得出測量一塊板的平均人工耗時量。同時,用機器視覺系統在線測量上述15個尺寸參數3次,求出每塊板15個參數的尺寸平均值、重復性標準差和耗時量。
以長度和寬度測量為例,人、機測量結果比較見表1。設為系統測量值與人工測量值相減的差值落在某一誤差范圍的次數,
為測量的總次數,則人機測量結果吻合度
的計算公式為:
表1:10種板件的人機測量結果
注: 測量誤差范圍±0.5 mm。
(8)
設每一塊板重復測量的次數為,單次測量的尺寸為
,
次測量的尺寸平均值為
。重復檢測標準差
為:
(9)
從表1可以看出,在測量誤差設定為 ± 0.5 mm范圍內,人機測量長度值的吻合度平均為97.3%,寬度值的吻合度平均為99.9%,表明了機器視覺測量值和人工測量值具有高度的一致性,機器視覺可以取代人工測量。而且,機器視覺系統測量的重復性標準差的平均值為0.041 mm,而人工檢測的重復性標準差為0.14 mm,二者的比值為1∶3.4,系統測量的重復精度遠高于人工測量。
此外,測量計時表明,人工檢測15個尺寸參數的平均速度為每塊板8 min,系統測量的平均速度為每塊板6 s,即本系統的測量速度是人工測量速度的80倍。
4 結語
筆者基于機器視覺開發了一種家具板件尺寸測量系統。工廠應用試驗表明,該系統能以速度60 m/min、精度±0.5 mm自動在線測量板件的長度、寬度等15個尺寸參數。
本研究為板件尺寸手工抽查方式轉變為非接觸高速在線測量方式探索了新路。下一步的研究重點是提高板件的長度測量精度,進一步降低機器視覺系統的傳輸隨機誤差和傳送帶的累積誤差。在此基礎上,研發與機器視覺檢測相適應的板件自動分揀系統和板件質量全生命周期跟蹤系統。
審核編輯 :李倩
-
測量系統
+關注
關注
2文章
539瀏覽量
41429 -
機器視覺
+關注
關注
162文章
4388瀏覽量
120437 -
人工智能
+關注
關注
1792文章
47424瀏覽量
238947
原文標題:基于機器視覺的家具板件尺寸在線測量
文章出處:【微信號:vision263com,微信公眾號:新機器視覺】歡迎添加關注!文章轉載請注明出處。
發布評論請先 登錄
相關推薦
愛普生開發了一種烤箱控制的晶體振蕩器,其功耗比傳統OCXOs1低56%
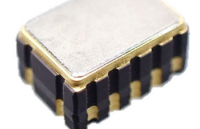
評論