前段時間去了一趟青島參加TMC的車規(guī)級SiC功率模塊的論壇。如之前所述,在這個領(lǐng)域,隨著400V往800V總線轉(zhuǎn)換,SiC產(chǎn)業(yè)已經(jīng)成為十分朝陽行業(yè),在中國也占據(jù)了一個非常重要的位置。
如何從車企和SiC企業(yè)之間建立這個溝通渠道,本次TMC論壇做了一次非常好的嘗試,我這里做一些梳理和記錄。
Part 1
1.
目前碳化硅的價(jià)格是IGBT的大概三到五倍,甚至最近碳化硅的供應(yīng)商們把價(jià)格進(jìn)一步提高了(由于缺芯)。明年,將有70%以上的汽車企業(yè)至少有一款碳化硅會試運(yùn)行或者測試,預(yù)計(jì)到2027-2030年碳化硅將成為主流。
目前為止大量的封裝材料依賴進(jìn)口(尤其是耐高溫的材料),包括絕緣的封裝材料等,目標(biāo)是到2025年,自主碳化硅芯片加上自主的封裝能夠上車。
2.
碳化硅的市場需求(市值而不是數(shù)量)未來幾年會有一個非常快速的增長,碳化硅貴很多,硅基器件不會那么快退出市場。碳化硅和800V是比較好的組合,但并不是一對一的關(guān)系,早期800V的系統(tǒng)碳化硅的器件并沒有那么成熟,用的還是硅基IGBT。目前碳化硅大部分還是采用了現(xiàn)有硅基的技術(shù),實(shí)際上都是用現(xiàn)有的封裝技術(shù),這一方面可以規(guī)避SiC市場的不確定性,并且保證技術(shù)成熟度,努力讓碳化硅模塊先跑起來,再進(jìn)行優(yōu)化。
真正想發(fā)揮碳化硅的優(yōu)勢,可以做下面的工作:
●冷卻:目前主流的是單面的直接水冷技術(shù),但碳化硅更適合雙面的水冷技術(shù),碳化硅目前大部分還是平臺性器件,發(fā)熱的范圍很窄,產(chǎn)生的熱量其實(shí)很高,這樣對冷卻提出了更高的要求。
●銀燒結(jié)技術(shù)封裝的溫度比較高,可以克服封裝可靠性的問題,底端的連接和不同位置都可以采用銀燒結(jié)技術(shù)。銅燒結(jié)可能實(shí)現(xiàn)一個全銅的模塊。
●鍵合技術(shù):碳化硅在比較高頻的情況下運(yùn)行,需要一個非常低的低電感技術(shù)。可以采用柔性(像電路板的鍵合方式),像雙面的鍵合把整個包覆的板作為像引線一樣,直接焊接到這個表面,這都是比較新穎的鍵合技術(shù)。
●高溫的塑封材料:運(yùn)行溫度可能會比較高,需要一些新的材料去適應(yīng)它的體系。
●基板:從CTE的熱膨脹技術(shù)差異上來看,氮化鋁和氮化硅都是一個比較好的材料,相對來說跟碳化硅的熱膨脹技術(shù)都是比較接近。但是氮化鋁的韌性不足很容易就碎掉,比較希望采用富銅的氮化鋁材料。
碳化硅很特殊的地方在于材料多,很多都是創(chuàng)新公司在做,傳統(tǒng)功率半導(dǎo)體企業(yè)通過收購的方式去做垂直的整合在未來也是非常重要的趨勢。因?yàn)椴牧咸厥庑裕?IDM是比較有優(yōu)勢的,使用的碳化硅和硅整個成本的比例是為2.5:1左右,未來幾年它可能逐漸降低到2左右。
3.
上汽全系800V,包括一個800V的快充電池,前驅(qū)是一個A軸,后驅(qū)是一個C軸,包括高壓的PDC。電驅(qū)動系統(tǒng)的重量增加了4%,重量功率密度可以提升60%。碳化硅器件成本很貴導(dǎo)致電驅(qū)的成本上升大概30%左右。400V的C軸和800V的C軸效率對比,高效區(qū)明顯變大了,90%的效率擴(kuò)大6.6%,95%的效率區(qū)間擴(kuò)大7%。碳化硅更適合CLTC的工況,平均效率提高了3%-5%。
電驅(qū)控制集成了MCU+VCU+BMS部分功能,采用Aurix TC389主控芯片,配備SBC3584實(shí)現(xiàn)功能安全,部分車端BMS的功能加進(jìn)去了。
中速、低速、高速不同的工況情況下,碳化硅系統(tǒng)的應(yīng)用中會有一個比較優(yōu)的最佳效率點(diǎn)。在10K頻率下也可以控制在2.1萬轉(zhuǎn)的高速情況,從10K提到12K的時候,這個波動明顯降低了很多。碳化硅應(yīng)用之后電機(jī)控制可以達(dá)到2.5萬轉(zhuǎn)這樣一個情況,碳化硅的開關(guān)頻率提升20%、30%,轉(zhuǎn)速也可以進(jìn)一步地再提升。基于碳化硅功率器件把頻率做高,13K以下測到的噪音,15K、16K、17K,可以看到很明顯的優(yōu)化。碳化硅高速開關(guān)特性對驅(qū)動芯片的要求比較高,需要精益性的設(shè)計(jì),更高開關(guān)造成的EMI方面的影響也很大。軸電壓的根源是PWM開關(guān)導(dǎo)致的電容感應(yīng)電壓,通過源頭、路徑包括軸承本身的一些綜合優(yōu)化。
4.
碳化硅器件要:
●突破高溫限制,達(dá)到200度穩(wěn)定運(yùn)行
●解決高速開關(guān)易受干擾,實(shí)現(xiàn)高速門級驅(qū)動
●散熱過于集中,需要采用高效散熱方法
Part 2
5.
碳化硅功率第一代接近批產(chǎn)的是邊框+灌膠型的碳化硅功率模塊。同時已經(jīng)著手嵌入PCB管的碳化硅模塊,直接將碳化硅器件嵌入到電路板還是可行的,在五六年之后能實(shí)現(xiàn)投產(chǎn)的一代產(chǎn)品。
WLTP工況下的開關(guān)頻率,找電機(jī)損耗最低值,不同的轉(zhuǎn)速和不同的扭矩情況下找出來最優(yōu)化的開關(guān)頻率,單純使用碳化硅逆變器能夠降低4.5瓦時/公里的功率消耗。如果我們用優(yōu)化過后的開關(guān)頻率,從逆變器端功率損耗升高,但從電機(jī)的角度是進(jìn)一步降低了0.55瓦時/公里,電機(jī)和逆變器綜合起來優(yōu)化0.4瓦時/公里的功率損耗降低,加上碳化硅逆變器的開關(guān)損耗和導(dǎo)通損耗的降低,共有4.9瓦時的損耗降低。
6.
Viper設(shè)計(jì)初衷是避免鍵合線的失效點(diǎn),提高導(dǎo)熱系數(shù),封裝層面也考慮到整個封裝的簡化,縮減整個設(shè)計(jì)制造成本,從而提高可行性。
Viper的主要應(yīng)用場景主要是通過對于電流密度以及結(jié)溫進(jìn)行改善,雙面水冷的封裝設(shè)計(jì)是為了優(yōu)化散熱設(shè)計(jì),同時減少對于所謂成本較高的晶圓的應(yīng)用,從而最終優(yōu)化整個系統(tǒng)的成本。
雙面水冷,熱導(dǎo)系數(shù)偏低,結(jié)溫也會控制得比較低。
尺寸和用量來說,用到的晶圓會更少一些,這樣的話整個成本會更低。
基于可靠性考慮,設(shè)計(jì)中取消了鍵合線的設(shè)計(jì),通過焊接或者灌封等方式,最終模塊能量密度會更高一些。
7.
講充電機(jī),我就不在這里摘錄了。
8.
傳統(tǒng)平面型的是第一代,也是目前正在使用的碳化硅結(jié)構(gòu)(比較主流的)。博世雙溝槽型的碳化硅是縱向的延伸,可以有效地縮小尺寸間距。雙溝槽的技術(shù)也有利于電流密度的提升,尺寸間隙的減小。在相對同樣的室溫下,溝槽型的碳化硅產(chǎn)品在同樣的面積下比傳統(tǒng)平面型的碳化硅要小很多。針對于可靠性的優(yōu)化也有利保證了碳化硅產(chǎn)品更高的性能。
博世第一代的碳化硅產(chǎn)品1200V、750V已經(jīng)量產(chǎn)了。第二代產(chǎn)品的開發(fā)已經(jīng)在進(jìn)行中,第二代750V已經(jīng)有試樣,到2023年計(jì)劃量產(chǎn)。第二代碳化硅產(chǎn)品改良:
●溫度系數(shù)可以減少10%。
●集成二極管,整個碳化硅開關(guān)控制過程中它會產(chǎn)生比較高的壓降,二極管的壓降只有第一代的一半,能夠減少50%,可以支持更快的開關(guān)速度。
審核編輯:劉清
-
IGBT
+關(guān)注
關(guān)注
1277文章
4022瀏覽量
253291 -
TMC
+關(guān)注
關(guān)注
0文章
36瀏覽量
17491 -
SiC功率模塊
+關(guān)注
關(guān)注
0文章
11瀏覽量
10304
原文標(biāo)題:TMC車規(guī)級SiC功率模塊論壇小結(jié)(上)
文章出處:【微信號:QCDZSJ,微信公眾號:汽車電子設(shè)計(jì)】歡迎添加關(guān)注!文章轉(zhuǎn)載請注明出處。
發(fā)布評論請先 登錄
揚(yáng)杰科技SiC車規(guī)級功率半導(dǎo)體模塊封裝項(xiàng)目盛大開工
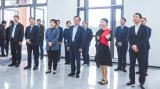
會展動態(tài)|TMC2025車規(guī)級功率半導(dǎo)體論壇「初步日程+展覽」首發(fā)
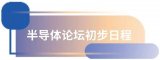
比亞迪全新1500V車規(guī)級SiC功率芯片解讀
會展動態(tài) | SiC“隱形心臟”引爆技術(shù)革命!TMC2025功率半導(dǎo)體論壇:以點(diǎn)帶面構(gòu)建全產(chǎn)業(yè)鏈協(xié)同創(chuàng)新
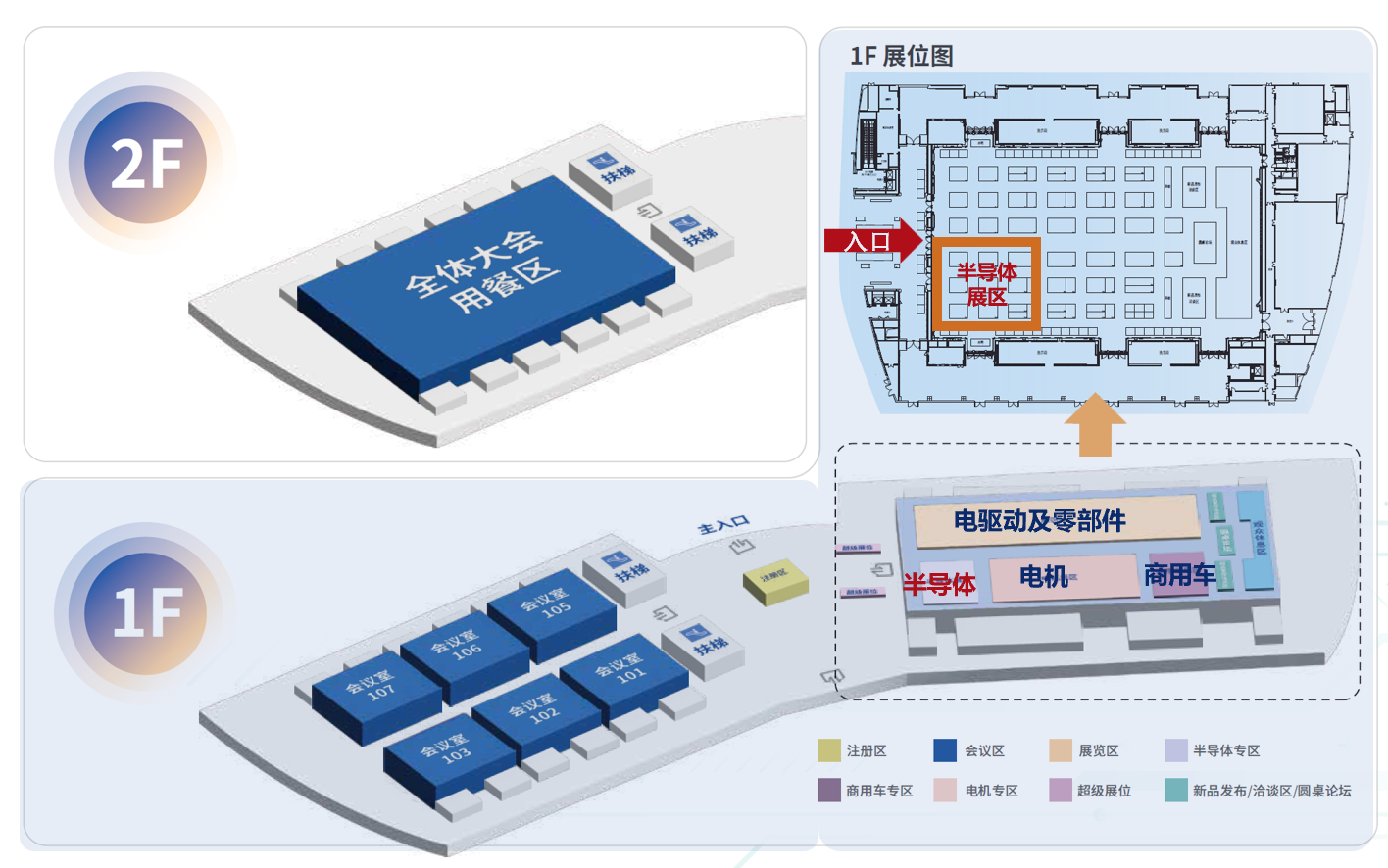
CAB450M12XM3工業(yè)級SiC半橋功率模塊CREE
功率器件熱設(shè)計(jì)基礎(chǔ)知識
博世自研PM6 SiC功率模塊產(chǎn)品介紹
深入剖析車規(guī)級IGBT模組的成本要素
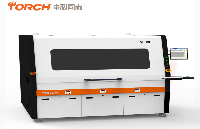
如何辨別符合車規(guī)級標(biāo)準(zhǔn)的電子元器件?
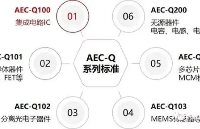
車規(guī)級IGBT模組:成本背后的復(fù)雜系統(tǒng)解析
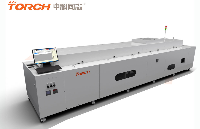
車規(guī)級芯片車身空調(diào)控制方案Demo
TMC2024丨車規(guī)級功率半導(dǎo)體論壇劇透二丨全球技術(shù)趨勢與主驅(qū)功率半導(dǎo)體應(yīng)用創(chuàng)新
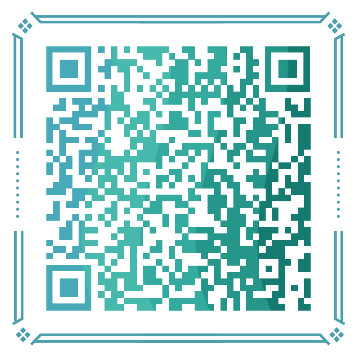
瞻芯電子第三代1200V 13.5mΩ SiC MOSFET通過車規(guī)級可靠性測試認(rèn)證
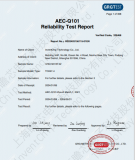
TMC2024丨車規(guī)級功率半導(dǎo)體論壇劇透一丨SiC模塊特色封裝與半導(dǎo)體制造技術(shù)創(chuàng)新
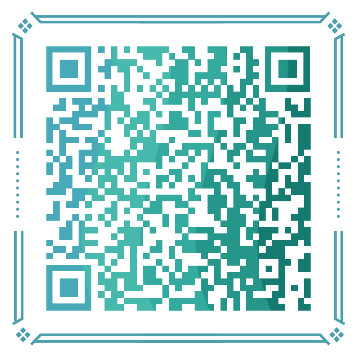
評論