摘要
薄晶片已成為各種新型微電子產(chǎn)品的基本需求。更薄的模具需要裝進更薄的包裝中。與標準的機械背磨相比,在背面使用最終的濕法蝕刻工藝而變薄的晶片的應力更小。硅的各向同性濕式蝕刻通常是用硝酸和氫氟酸的混合物進行的,并添加化學物質,以調整單個晶圓旋轉加工的粘度和表面潤濕性。 隨著硅被蝕刻并加入到蝕刻溶液中,蝕刻速率將隨時間而減小。這種變化已經(jīng)被建模了。本文的重點是比較過程控制技術,以保持一致的蝕刻率作為時間和晶片處理的函數(shù)。這些模型允許延長時間,補充化學品或這些物質的組合。
硅蝕刻:
硅的各向同性濕法蝕刻最常用的化學方法是硝酸和氫氟酸的結合物。它通常被稱為HNA系統(tǒng)(HF:一基氮:醋酸與醋酸) ,作為濕式工作臺應用程序的緩沖區(qū)添加。硝酸作為一種氧化劑,將其表面轉化為二氧化硅,然后用高頻蝕刻(溶解)該氧化物。
Si + 4HNO3 SiO2 + 4NO2 + 2H2O SiO2 + 6HF H2SiF6 + 2H2O
單個晶圓旋轉處理器提供了蝕刻晶圓一側的能力,同時保護另一側。對于單一晶圓旋轉處理器,需要添加具有更高粘度的化學物質,以在晶片表面提供更均勻的蝕刻。上述溶液中的醋酸被磷酸和硫酸的組合所取代。這些厚粘性酸不通過化學方式參與蝕刻反應,因此不會改變化學動力學,但會增加 由于粘度的增加而產(chǎn)生的傳質阻力。有文獻報道,在相同的去除率下,在高頻和一硝酸的混合物中加入少量粘性酸會更有效地降低晶片的粗糙度。此外,HF和一氮的比值會影響蝕刻率和表面粗糙度。在高高頻和低氮濃度下,該過程非常依賴于溫度,反應速率控制,導致不穩(wěn)定的硅表面。在低高頻和高硝酸含量下,由于擴散限制反應,表面光滑拋光。化學反應的速率與sp有關。
實驗:
實驗結果在SSEC 3300系列單晶圓自旋處理器系統(tǒng)上進行。所采用的化學成分是氫氟酸、一硝酸、硫酸酸和磷酸酸的混合物,比例為1:6:1:2。使用SSEC的收集環(huán)技術進行了化學反應的再循環(huán)。在蝕刻過程中有許多工藝參數(shù)可以變化,從以往的工作中選擇了一個優(yōu)化工藝。
隨著硅晶片被蝕刻的時間不變,我們可以看到蝕刻的深度逐漸減少(蝕刻率降低)。下面的圖表顯示了一個擴展的尺度,以便仔細查看數(shù)據(jù)和一個趨勢線。這種經(jīng)過加工的晶片的蝕刻深度(蝕刻率)的變化對于制造工藝是不可接受的。
圖1:恒定蝕刻時間下的硅蝕刻深度。
時間vs化學品
圖3:每4小時增加蝕刻時間1秒。
在從蝕刻到?jīng)_洗的轉換過程中,我們關閉收集杯并停止收集化學物質,以避免在化學物質中加入水。在此過程中損失的化學物質的量 短暫的時間(小于一秒)在我們所使用的流量下大約是30毫升。因此,在處理了400個晶片后,我們將消耗12升的化學供應,它將需要重新填充。此外,在某個時候,溶液中硅的含量將達到最大值,其化學性質將需要被取代。
另一種保持恒定蝕刻速率的方法是在化學混合物中加入活性成分(HF),或者不斷地去除和補充化學溶液或這些溶液的某種組合。
下圖顯示了在每個晶圓片后加入30毫升化學物質的結果,其中加入的化學物質是5毫升HF和25毫升1:6:1:2混合物的混合物。
圖4:添加化學品以保持恒定的蝕刻速率。
繼續(xù)添加400片化學物質,我們看到了保持蝕刻率的能力。
圖5:增加時間或添加化學品的比較。
總結
隨著硅晶片的蝕刻,可以觀察到蝕刻速率的下降。HF峰值提供了一種補充活性成分的方法。與此同時,硅正以六氟硅酸的形式在溶液中積累起來。去除硅的唯一方法是在每個晶片上去掉一些溶液。晶圓尺寸將確定尖峰、去除和新鮮補充量,以達到穩(wěn)定的平衡。就化學成本和系統(tǒng)停機時間而言,這是最低的擁有成本,并將導致隨時間不變的蝕刻率。
審核編輯:湯梓紅
-
工藝
+關注
關注
4文章
666瀏覽量
29232 -
蝕刻
+關注
關注
10文章
424瀏覽量
15926 -
硅晶片
+關注
關注
0文章
74瀏覽量
15384
發(fā)布評論請先 登錄
KOH硅濕法蝕刻工藝設計研究
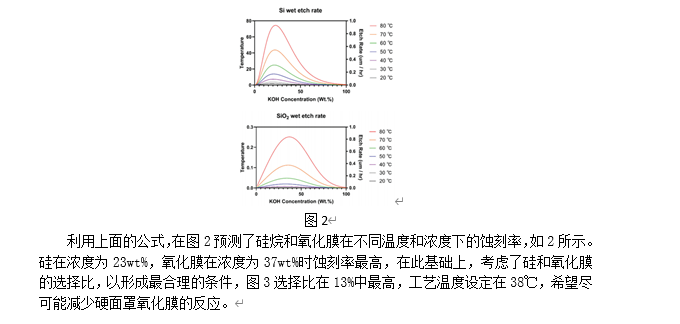
使用n型GaSb襯底優(yōu)化干法和濕法蝕刻工藝
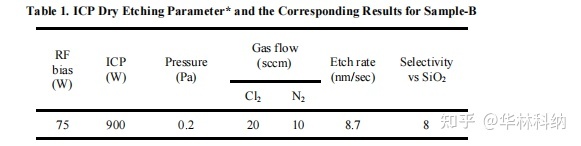
濕法蝕刻工藝的原理
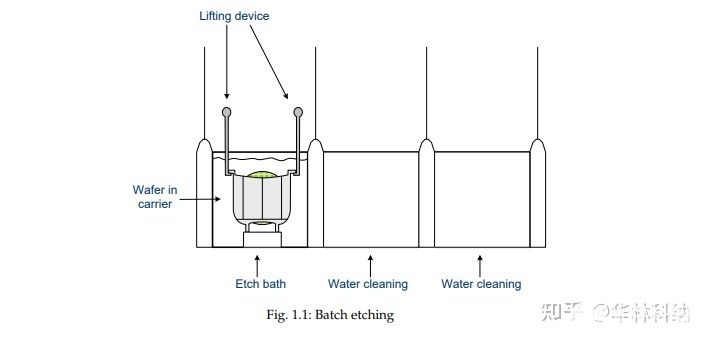
硅片減薄技術研究
PCB外層電路的蝕刻工藝
濕法蝕刻工藝
《炬豐科技-半導體工藝》GaN 納米線制造和單光子發(fā)射器器件應用的蝕刻工藝
PCB蝕刻工藝原理_pcb蝕刻工藝流程詳解
關于濕法蝕刻工藝對銅及其合金蝕刻劑的評述
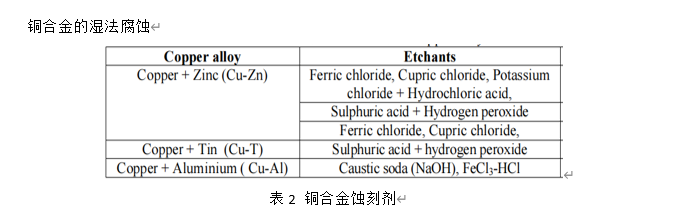
微機械結構硅片的機械減薄研究
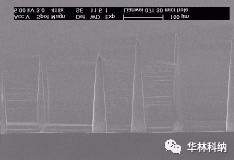
用于硅片減薄的濕法蝕刻工藝控制
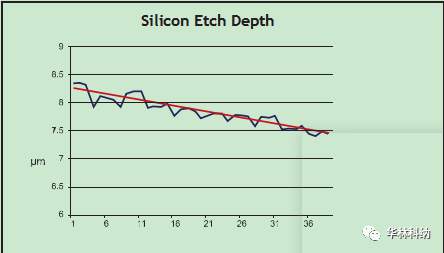
評論