碳化硅和氮化鎵是寬帶隙(WBG)半導體,也是被認為要求更高功率和更高溫度的電力電子應用最佳材料。由于這些WBG半導體具有優異的性能,如寬禁帶(>3eV)、高臨界電場(>3 MV/cm)和高飽和速度(>2x10cm/s),SiC和在功率轉換效率方面,GaN可以克服基于硅的器件所達到的終極性能。
此外,WBG半導體器件的工作溫度(>250℃)比基于硅的器件(<150℃)如圖1/2/3所示,這意味著可以從功率轉換系統中去除龐大、復雜和沉重的冷卻系統。逆變器和轉換器汽車部件可以通過在高溫環境中的簡單散熱設計變得更小。通常,功率模塊的結構具有半導體芯片和散熱/絕緣板的多層結構,所有層都有不同的材料特性,例如熱膨脹系數(CTE),這會在重復操作過程中引起熱機械應力。
另外為了承受更高的功率和更高的熱密度,如何絕緣和散熱是WBG功率轉換系統的關鍵問題之一。因此,出現了一些問題,例如如何將這些多層互連以在高溫下實現并具有熱穩定可靠性。此外,電力電子陶瓷基板在散熱以防止電力電子模塊故障方面起著重要作用。功率半導體器件與散熱器之間存在直接鍵合銅DBC和直接鍵合鋁DBA的散熱/絕緣陶瓷基板。熱量從功率半導體器件的表面傳遞到散熱器,DBC和DBA在陶瓷板的兩側金屬化,以提高陶瓷基板的導熱性并形成電路,由于其優異的導熱性、低熱阻和絕緣電壓高。
然而,DBC和DBA基板的夾層結構會由于CTE不匹配而引起熱機械應力。據報道,陶瓷基板的耐熱性取決于陶瓷和金屬的類型。在-50℃至250℃的溫度范圍內進行了苛刻的熱沖擊循環測試期間,在各種陶瓷應用的活性金屬釬焊(AMB)DBC陶瓷基板與鍍鎳層的熱機械穩定性。DBC襯底與氮化硅陶瓷中間層在1000次熱沖擊循環內沒有嚴重損壞,而氮化鋁和氧化鋁在相同循環后由于銅層嚴重分層。
結果表明,這些失效可能表明氮化鋁和氧化鋁具有比氮化硅更高的CTE值和更低的韌性的關鍵缺點。由于以前的研發只是觀察了DBC陶瓷基板本身,因此故障必須是由Cu和陶瓷之間的不匹配引起的,這意味著應力來自DBC。這種熱循環僅在陶瓷基板樣品中產生均勻的溫度變化如圖4所示。然而,陶瓷基板中的實際熱分布必須具有較大的溫度梯度,才能將產生的熱量從器件芯片表面傳遞到冷卻系統如圖4所示,在從芯片到冷卻系統的熱傳導過程中,由CTE失配引起的應力比單個DBC陶瓷基板更復雜,因此在設計功率模塊時迫切需要評估這種實際的溫度分布。在這種情況下,功率循環測試是一種非常有用的評估方法,用于評估在類似于實際操作條件下使用的器件封裝的可靠性。
在這個過程中,這種陶瓷基板的傳熱性能主要取決于所采用的陶瓷材料的熱性能,例如氧化鋁、氮化鋁和氮化硅,這些在功率模塊需要導電銅和絕緣陶瓷的全面組合,包括層厚和電路圖案,以同時實現熱管理和最小的功率損耗。通常要在功率循環測試后測量器件的熱阻,需要一個功率循環系統設備和一個T3ster系統,即熱瞬態測試儀系統。它是一種監測通過設備的熱傳輸技術。然而,動力循環系統和T3ster系統非常昂貴,需要占用大量空間。實際上需要一個簡單、快速和小型化的熱測量系統。
在碳化硅微加熱器芯片中,并用于與各種類型的DBC陶瓷基板如氮化鋁和氧化鋁以及氮化硅鍵合。Ag燒結連接被用作連接材料的模具,因為它可以承受高溫應用,并且在許多先前的研究中都有講到,測量了不同類型DBC的SiC微加熱器芯片到冷卻系統的穩態熱阻。此外,還進行了功率循環測試,以研究每種類型DBC陶瓷基板上的SiC微加熱器芯片貼片結構的高溫可靠性。通過微焦點3D計算機斷層掃描(CT) X射線系統分析電源循環后的故障。這種方法可以顯著區別于傳統的熱循環測試,因為可以在重復的熱環境中考慮材料的熱性能。
-
功率模塊
+關注
關注
10文章
468瀏覽量
45118 -
碳化硅
+關注
關注
25文章
2770瀏覽量
49088 -
陶瓷基板
+關注
關注
5文章
213瀏覽量
11433
發布評論請先 登錄
相關推薦
在IGBT模塊中氮化鋁陶瓷基板的應用如何?
陶瓷封裝基板——電子封裝的未來導向
為什么要選擇陶瓷基板作為封裝材料?
斯利通淺談陶瓷基板的種類及應用
如何有效解決路由器散熱和穩定性的問題
DBC陶瓷基板市場現狀及未來發展趨勢
DBC陶瓷基板是干什么用的?
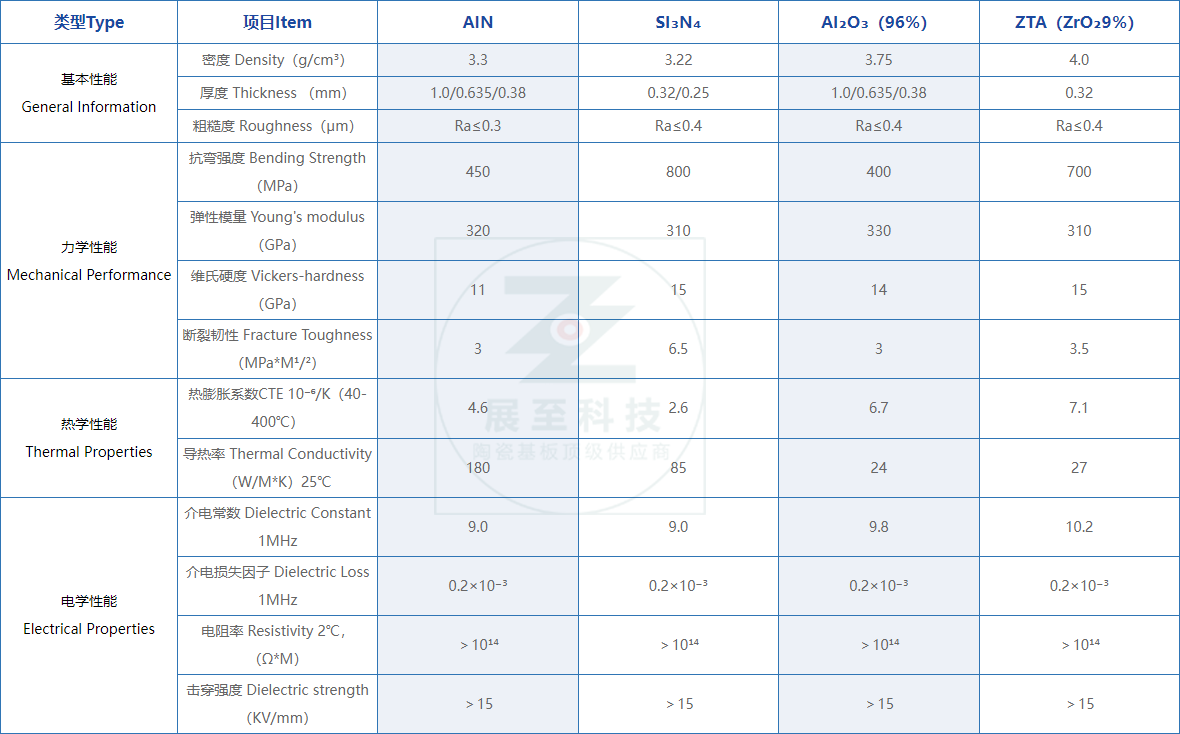
陶瓷基板的種類及其特點
什么是熱電偶穩定性?影響熱電偶穩定性的主要因素
陶瓷基板技術PK:DBC vs DPC,你站哪一邊?
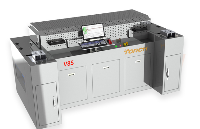
電阻器的熱穩定性分析
熱重分析儀如何測材料的熱穩定性和成分
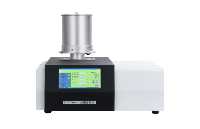
評論