■800V 平臺可有效解決電動(dòng)車?yán)锍探箲]、快充速度問題,車企紛紛布局:續(xù)航能力和充電時(shí)長是影響電動(dòng)車普及程度的重要因素,現(xiàn)階段新能源車的續(xù)航里程大約為 500-600km,無法滿足城際間長里程駕駛需求;另外由于新能源車補(bǔ)能效率較低, 燃油車的加油時(shí)間僅為 5 分鐘左右,而新能源車充電通常需要 60 分鐘,提升電壓平臺可提升整車運(yùn)行效率及充電速度。以保時(shí)捷為例,保時(shí)捷將電壓平臺從 400V 提高至800V 后,實(shí)現(xiàn) 300kW 充電功率,可以在 22.5 分鐘內(nèi)把 Taycan Turbo S容量 93.4kWh 的動(dòng)力電池從 5%充至 80%, 提供 300 公里的續(xù)航能力,高壓線束的截面積僅為 400V 架構(gòu)下的二分之一,線束減重 4kg。吉利極氪、小鵬汽車、廣汽埃安、比亞迪、理想汽車、北汽極狐、嵐圖等車企也相繼投資 800V 電壓架構(gòu)產(chǎn)品,并逐步計(jì)劃量產(chǎn)。
■采用碳化硅器件并未提高整車成本:目前單個(gè)碳化硅功率器件的價(jià)值量約為硅基IGBT的3倍,但主機(jī)廠通常從整車成本考慮,采用碳化硅能帶動(dòng)整車系統(tǒng)效率提升,從而降低系統(tǒng)其他部分成本。根據(jù)產(chǎn)業(yè)調(diào)研,在中高端車型中使用硅基IGBT的總體成本約為3000元左右,碳化硅器件成本約為硅基IGBT的3倍,在相同性能的產(chǎn)品中,使用碳化硅器件可使汽車?yán)m(xù)航能力提升5-10%,以5%的性能提升計(jì)算,對應(yīng)電池端即可節(jié)省4000-5000元,碳化硅耐高壓和耐高溫特性可使得電纜、散熱系統(tǒng)等成本降低,僅散熱系統(tǒng)即可節(jié)省1000元左右,綜合成本可抵消器件本身成本的增加。使用碳化硅并不會增加整車成本,這為行業(yè)發(fā)展帶來長久動(dòng)力。
■碳化硅成本下降空間大,800V架構(gòu)車型有望向經(jīng)濟(jì)型下沉:目前碳化硅襯底制作難,長晶速度慢導(dǎo)致成本過高,是影響碳化硅器件滲透率的主要因素,現(xiàn)階段采用碳化硅器件的多為中高端車型。未來隨著碳化硅襯底工藝提升、尺寸擴(kuò)大及行業(yè)產(chǎn)能增加,勢必帶來產(chǎn)品成本降低,經(jīng)濟(jì)型電動(dòng)車也將有望搭載高壓方案。目前6寸導(dǎo)電型襯底片的市場零售價(jià)約1000美元/片,據(jù)產(chǎn)業(yè)調(diào)研,到2025年價(jià)格有望下降至500美元以下,硅基和SiC基的成本差距會在2倍內(nèi),屆時(shí)碳化硅器件更據(jù)優(yōu)勢,滲透率將有望持續(xù)提升。
■目前問題:新能源汽車發(fā)展不及預(yù)期;800V架構(gòu)產(chǎn)品量產(chǎn)不及預(yù)期;SiC技術(shù)難度大,產(chǎn)品研發(fā)、量產(chǎn)不及預(yù)期;SiC滲透率不及預(yù)期。
01 新能源汽車向 800V 高電壓平臺演變, 對功率器件要求持續(xù)提高
1.1. 電壓平臺演變歷史:從量變到質(zhì)變
在燃油車時(shí)代,通過升高電壓的方式實(shí)現(xiàn)電能的大功率傳輸,滿足汽車供電需求。1918年,汽車引入蓄電池,其電壓僅為6V;隨著汽車電器如車燈、照明、ISG等用電器件的增加,6V低電壓系統(tǒng)無法滿足車用電器功率要求,加之電氣化部件的大量集成,1950年汽車電壓平臺升級為12V;二十世紀(jì)九十年代,出現(xiàn)42V汽車電壓平臺,但是由于零部件升級電壓規(guī)格成本高而未能實(shí)現(xiàn);2010年前后,在信息娛樂、混動(dòng)的需求背景下,歐洲發(fā)起48V電壓系統(tǒng)升級,Audi, BMW, Daimler, Porsche, Volkswagen 聯(lián)合推出48V系統(tǒng),與12V電壓平臺共存;2020年,各國節(jié)能法規(guī)的頒布推動(dòng)48V低電壓平臺發(fā)展。
隨著車載電器數(shù)量的增多,以及自動(dòng)駕駛、節(jié)油減耗等要求的提出,電動(dòng)汽車的電壓平臺將逐漸由 400V 升高至 800V,以分擔(dān)蓄電池的工作壓力。純電動(dòng)汽車中成百上千個(gè)電池串并聯(lián)形成超百伏的電池包, 其高壓系統(tǒng)主要包括動(dòng)力電池、配電盒、OBC、DCDC、電驅(qū)、PTC、空調(diào)、充電口等。
目前,電動(dòng)車根據(jù)帶電量不同選擇不同的電壓等級。一般小型代步車的電壓為48V、60V和72V;乘用車的電壓范圍大約為250-450V;大巴車、公交車等由于帶電量高,其基本電壓為450-700V。在未來,隨著對續(xù)航里程、充電速度要求的提高,電動(dòng)車電壓有望升至800V-1000V。
國內(nèi)外車企紛紛布局800V高電壓平臺。2019年4月保時(shí)捷Taycon Turbo S 全球首發(fā),業(yè)內(nèi)最先量產(chǎn)800V高電壓平臺的汽車,將最大充電功率提升到350kW,可以在22.5分鐘內(nèi)把Taycon Turbo S容量93.4kWh的動(dòng)力電池從5%充至80%,提供300公里的續(xù)航能力。2020 年12月,現(xiàn)代汽車集團(tuán)推出全新電動(dòng)汽車專用平臺 “E-GMP” ,該平臺同樣搭載可以實(shí)現(xiàn)最大 800V 多功能充電系統(tǒng)。Rivian和通用也已經(jīng)計(jì)劃將電壓改為800V。國內(nèi),吉利極氪、小鵬汽車、廣汽埃安、比亞迪e平臺、理想汽車、北汽極狐、嵐圖等車企也已經(jīng)布局了800V快充技術(shù)。
1.2. 電壓高壓化:里程焦慮、充電速度慢問題的最好解決方案
續(xù)航能力是決定新能源汽車普及程度的重要因素。大部分新能源汽車的續(xù)航里程低于600公里,低于燃油車的續(xù)航里程,難以滿足城際間的長里程行駛需求。目前,市場上較暢銷的新能源車型包括特斯拉、比亞迪、蔚來、小鵬等,其中,比亞迪唐和比亞迪宋的續(xù)航里程為505公里;特斯拉的續(xù)航里程范圍為545-675km;小鵬P5續(xù)航里程600km。新能源車的續(xù)航里程仍有較大的上升空間,不足以滿足未來人們長里程駕駛需求。
與燃油車相比,新能源車的補(bǔ)能效率較低。燃油車的加油時(shí)間僅為5分鐘,而目前快充至少需要60分鐘。在高峰期充電排隊(duì)等候的時(shí)間亦進(jìn)一步拉長。目前,主要有以下三種充電方法:
? 在家中充電:家庭用戶使用的三眼插座有10A和16A兩種規(guī)格,約8-10小時(shí)可以充滿。
? 交流充電樁:將電動(dòng)車直接在電流更大的交流電網(wǎng)上,用充電樁進(jìn)行充電,充電時(shí)長約4小時(shí)。慢充電樁功率通常為3.5kW和7kW,取決于車載充電機(jī)的額定輸入功率。
? 直流充電樁:將電動(dòng)車連接到交流電網(wǎng)或直流電網(wǎng)時(shí),使用了帶控制導(dǎo)引功能的直流供電設(shè)備。由大功率非車載直流充電機(jī)直接輸出直流給車輛電池充電。在充電時(shí),充電樁需要提供與電池相匹配的電壓,國標(biāo)規(guī)定直流輸出電流最大不超過250A,多數(shù)電動(dòng)車能獲得不高于102.5 kW的峰值充電功率,充電時(shí)間大約需0.5h。
提高汽車電壓平臺可以大幅提升整車運(yùn)行效率、縮短充電時(shí)長。電阻大小相同情況下,高電壓可使電損耗減少,效率提升。2021年9月,比亞迪發(fā)布e平臺3.0,有800V閃充功能,實(shí)現(xiàn)充電5分鐘續(xù)航150公里,搭載該平臺的車型有望在2022年量產(chǎn);極氪001 具備 400V 和800V 兩種電壓架構(gòu),10%-80% SOC 充電時(shí)間僅需30分鐘,充電5分鐘續(xù)航可增加120 公里;北汽極狐發(fā)布極狐αS Hi 版,具備800V 充電架構(gòu),2.2C 閃充技術(shù)能實(shí)現(xiàn)10 分鐘補(bǔ)充 196 公里續(xù)航的電量,30%-80%SOC 充電時(shí)間僅為 15 分鐘。2021 年 10 月,小鵬汽車公布首個(gè)量產(chǎn)的800V 高壓 SiC 平臺,充電峰值電流超過600A,采用高能量密度、高充電倍率電池,充電 5 分鐘最高可補(bǔ)充續(xù)航200 公里。
1.3. 相較于提高電流,高電壓仍為未來發(fā)展趨勢
根據(jù)P=UI,提升快沖效率的方向有二:提升電壓,將新能源汽車的電壓系統(tǒng)從400V升高至800V后電動(dòng)車的功率提高一倍,大幅降低充電時(shí)間;提升電流,特斯拉是采用提高電流方法的代表。
高電流模式推廣程度低,對熱管理要求高。根據(jù)特斯拉官網(wǎng),特斯拉V3超充樁在400V電壓下可達(dá)到250kW的峰值充電功率。特斯拉電動(dòng)車的充電時(shí)間需要30分鐘左右,大電流超充的推廣難度較高,由焦耳定律Q=I2RT,熱量與電流的二次方成正比,大電流充電過程中產(chǎn)生的熱量大幅增加,對汽車的散熱系統(tǒng)有更高的要求。以特斯拉為例,特斯拉V3 超充樁峰值工作電流超過600A,故需要使用更粗的線束。此外,大電流模式的應(yīng)用場景有限制,目前大電流模式僅在10%-20%SOC 進(jìn)行最大功率充電,在其他區(qū)間充電功率也有明顯下降。
高電壓模式是車廠普遍采用的模式,除減少能耗、提高續(xù)航里程外,還有減少重量、節(jié)省空間等優(yōu)點(diǎn)。根據(jù)焦耳定律,高電壓系統(tǒng)下,電流變小使得整個(gè)系統(tǒng)的功率損耗減小,提高效率。若電流不變,汽車的電機(jī)驅(qū)動(dòng)效率則會提升,從而增加續(xù)航里程、降低電池成本。高電壓模式的有點(diǎn)還包括降低高壓線束重量,同功率情況下,電壓等級的提高客減少高壓線束上的電流,使得線束變細(xì),從而降低線束重量、節(jié)省安裝空間。以保時(shí)捷為例,保時(shí)捷將電壓平臺從400V提高至800V后,實(shí)現(xiàn)300kW充電功率,高壓線束的截面積僅為400V架構(gòu)下的二分之一,線束減重4kg。小鵬也推出800V平臺下的400kW快沖,充電效率可達(dá)5C,實(shí)現(xiàn)充電10分鐘續(xù)航400公里的效果。
1.4. 400V電壓平臺下功率器件使用情況
與燃油車相比,新能源車對電力控制的需求提高,功率器件在新能源車中的占比遠(yuǎn)高于燃油車。在傳統(tǒng)燃料汽車中,汽車電子主要分布于動(dòng)力傳動(dòng)系統(tǒng)、車身、安全、娛樂等子系統(tǒng)中;而在新能源汽車中,功率器件主要集中于“三電系統(tǒng)”,即電池、電機(jī)和電控系統(tǒng),新增 DC-DC 模塊、電機(jī)控制系統(tǒng)、電池管理系統(tǒng)、高壓電路等部件。新能源汽車系統(tǒng)架構(gòu)中涉及到功率半導(dǎo)體應(yīng)用的組件包括:電機(jī)驅(qū)動(dòng)系統(tǒng)、OBC、 AC/DC 和 DC/DC。
不同檔次的電動(dòng)車采用功率器件存在差異。根據(jù)產(chǎn)業(yè)調(diào)研,A00-A0級車售價(jià)集中在2-3萬元,電控系統(tǒng)主要采用最小的MOS方案,以92V的低壓單管為主,主要供應(yīng)商為ST,上汽通用五菱是采用該方案的典型代表;A0-A級車,售價(jià)在10萬元以下,通常采用650V的IGBT方案,低壓IGBT領(lǐng)域目前斯達(dá)半導(dǎo)在國內(nèi)市場的份額最大;10萬-20萬元的電動(dòng)汽車大部分采用750V IGBT,英飛凌占據(jù)該細(xì)分市場最大的市場份額;比亞迪著力于高壓1200V IGBT模組,物流車、商用車等C級車主要采用1200V方案。
主電機(jī)驅(qū)動(dòng):汽車的電機(jī)驅(qū)動(dòng)系統(tǒng)包括傳動(dòng)機(jī)構(gòu)、電機(jī)和逆變器。功率器件主要應(yīng)用于逆變器,400V電壓平臺下,電機(jī)驅(qū)動(dòng)系統(tǒng)中的逆變器主要采用硅基IGBT,約占其成本的50%。
OBC(車載充電系統(tǒng)):車載蓄電池充電機(jī)可將來自電池子系統(tǒng)的DC電源轉(zhuǎn)換為主驅(qū)動(dòng)電機(jī)的AC電源,通常采用硅基IGBT方案,由于SiC器件可使得OBC減少能耗、改善散熱情況,全球范圍內(nèi)汽車廠商陸續(xù)采用SiC功率器件代替硅器件。
AC/DC:車載AC/DC變換器可將高壓直流電逆變成交流電來驅(qū)動(dòng)電動(dòng)機(jī)、空調(diào)工作,通常采用硅基IGBT方案。
DC/DC:車載DC/DC變換器可將動(dòng)力電池輸出的高壓直流電轉(zhuǎn)換為低壓直流電。從車載動(dòng)力電池取電,給車載12V或24V低壓電池充電,并為整車提供全部的低壓供電,通常采用硅基IGBT方案。
1.5. 800V電壓平臺下的電動(dòng)車部件升級
實(shí)現(xiàn) 800V 電壓平臺,需要面對元器件重新開發(fā)、電池模組安全性能提高以及半導(dǎo)體器件路線改變等難題。就電池包而言,4C 以上充電倍率以及電壓和電流的增大會極大的影響電池的穩(wěn)定性和使用壽命,需在 BMS 和電池材料電導(dǎo)率上進(jìn)一步改善。此外,更大的充電功率對電池系統(tǒng)的冷卻提出較大挑戰(zhàn),需對發(fā)熱較為集中的電芯正極區(qū)域進(jìn)行針對性冷卻和熱管理, 保障電池在理想溫度區(qū)間內(nèi)工作。
電壓平臺的升高要求電動(dòng)車的三電系統(tǒng)以及空調(diào)壓縮機(jī)、DC/DC、OBC等部件在800V甚至1000V的電壓下正常工作,即需要各部件耐高壓、耐高溫。
? 電控:800V平臺要求電機(jī)控制器采用碳化硅 MOSFET代替硅基IGBT。硅基IGBT在450V平臺下耐壓650V,汽車電壓平臺升高至800V后,要求功率半導(dǎo)體耐壓等級達(dá)到1200V,硅基IGBT的開關(guān)/導(dǎo)通損耗將大幅升高。而800V下的碳化硅器件在耐壓、開關(guān)頻率、損耗等多個(gè)維度表現(xiàn)優(yōu)異,高電壓平臺將推動(dòng)碳化硅MOSFET發(fā)展。
? 電機(jī):800V逆變器導(dǎo)致電壓變化頻率高,軸電流增大,軸承防腐蝕要求增加,同時(shí),由于電壓/開關(guān)頻率增加,800V電機(jī)內(nèi)部的絕緣/EMC防護(hù)等級要求提升。
? OBC+DC/DC:OBC/DCDC等功率器件集成化趨勢明顯。電壓升高800V后,充電機(jī)OBC將不會使用目前的650V的硅基方案,變?yōu)槭褂锰蓟璧姆桨福豢紤]高頻特性,DC/DC不會使用1700V的IGBT,效率比較低。據(jù)產(chǎn)業(yè)調(diào)研,電壓平臺從400V升高至800V后,充電機(jī)70%以上的功率器件將換為碳化硅方案。
? 連接器+線束:平臺架構(gòu)從 400V 升級至 800V 要求連接器重新選型,為增加大功率快充借口,連接器數(shù)量可能增加;在同等功率條件下,電壓提高,電流減小,線束材料用量更少,但對耐壓、絕緣要求更高。
02
碳化硅物理特性優(yōu)良,適合制備高溫、高壓、高頻器件
2.1. 碳化硅:第三代半導(dǎo)體材料,具備耐高壓、高溫等優(yōu)點(diǎn)
碳化硅光電特性優(yōu)越,耐高溫、高壓、高頻,是800V電壓平臺下功率器件的首要選擇。碳化硅屬于第三代半導(dǎo)體材料,與前兩代半導(dǎo)體材料相比最大的優(yōu)勢是較寬的禁帶寬度,保證了其可擊穿更高的電場強(qiáng)度, 適合制備耐高壓、高頻的功率器件。
SiC適合制備高壓器件。SiC的絕緣擊穿場強(qiáng)是Si的10倍,較大的絕緣擊穿場強(qiáng)使碳化硅能夠以更高的摻雜濃度并且膜厚更薄的漂移層制作出600V~數(shù)千V 的高壓功率器件。高壓功率器件的電阻成分主要由該漂移層的電阻所組成,因此使用SiC 材料可以實(shí)現(xiàn)單位面積導(dǎo)通電阻非常低的高壓器件。理論上當(dāng)耐壓相等時(shí),SiC 在單位面積下的漂移層電阻可以降低到Si 的1/300。使用碳化硅材料,可避免硅基IGBT開關(guān)損耗大、高頻驅(qū)動(dòng)發(fā)熱等問題。SiC 材料能夠以具有快速器件結(jié)構(gòu)特征的多數(shù)載流子器件(肖特基勢壘二極管和MOSFET)實(shí)現(xiàn)高壓化。
SiC可以在高溫場景下應(yīng)用。SiC的帶隙寬度大約為Si的3倍,可以在較寬范圍內(nèi)實(shí)現(xiàn)必要的P 型、N 型控制,超越Si器件的物理極限。因此,SiC可以在高溫條件下穩(wěn)定工作。根據(jù)羅姆官方《SiC功率器件-模塊應(yīng)用筆記》顯示,目前由于受到封裝的耐熱可靠性的制約,只保證到150℃~175℃,但是隨著封裝技術(shù)的發(fā)展,將來也可能達(dá)到200℃以上的保證溫度。
2.2. 碳化硅二極管可替換快速恢復(fù)二極管,在高頻高壓情況下表現(xiàn)優(yōu)異
碳化硅肖特基勢壘二極管具有恢復(fù)損耗小、開關(guān)電源高頻、減小元件體積、降低噪音等優(yōu)點(diǎn)。SiC 能夠以具有 Si 快速器件結(jié)構(gòu)特征的肖特基勢壘二極管(SBD)結(jié)構(gòu),制作出 1200V 以上的高耐壓二極管(Si SBD 的最高耐壓為 200V 左右)。
碳化硅肖特基二極管的正向特性使其適合并聯(lián)使用。SiC SBD的開啟電壓與 Si FRD為同等水平, 都小于 1V。開啟電壓是由肖特基勢壘的勢壘高度所決定的,若降低 VF值,則需要減薄肖特基勢壘的高度, 但這會使器件反向偏壓時(shí)的漏電流增大。“降低開啟電壓” 和“控制漏電流” 存在折中關(guān)系。SiC SBD 的溫度特性與 Si FRD 不同,當(dāng)溫度升高時(shí),隨著工作電阻的增加,VF值也上升,不易發(fā)生熱失控,因此 SiC SBD 更適合并聯(lián)使用。同等溫度條件下,IF=10A 時(shí)碳化硅與硅二極管正向?qū)妷罕葘Γ蓟栊ぬ鼗O管的導(dǎo)通壓降為1.5V, 硅快速恢復(fù)二極管的導(dǎo)通壓降為 1.7V, 碳化硅材料性能好于硅材料。
由于碳化硅肖特基二極管的恢復(fù)特性,SiC SBD可大幅減少損耗,穩(wěn)定實(shí)現(xiàn)器件的正反切換。硅快速恢復(fù)二極管在從正向?qū)顟B(tài)切換到反向截止?fàn)顟B(tài)的瞬間,會產(chǎn)生極大的反向瞬態(tài)沖擊電流,器件從正壓導(dǎo)通轉(zhuǎn)向反壓截止偏壓狀態(tài)。此過程時(shí)間長,電流大,會產(chǎn)生較大的損耗,當(dāng)器件正向電流越大及溫度越高時(shí),恢復(fù)時(shí)間和恢復(fù)電流就越大,損耗也就越大。而碳化硅肖特基二極管是一種多數(shù)載流子導(dǎo)電器件(單極性器件),在工作過程中不會發(fā)生少數(shù)載流子存儲的現(xiàn)象,也不會產(chǎn)生過大的正反向切換瞬態(tài)沖擊電流,只有結(jié)電容放電的小電流,因此碳化硅肖特基二極管的開關(guān)損耗比硅快速恢復(fù)二極管更低。根據(jù)ROHM測試結(jié)果,無論使用溫度和正向電流如何改變,SiC的反向恢復(fù)電流都得到了大幅減小。
2.3. 碳化硅MOSFET在性能上優(yōu)于IGBT
硅基 IGBT 與 SiC MOSFET 在電氣參數(shù)上存在較大差異。
與硅基IGBT對比,SiC MOSFET不僅耐壓性更好,而且可有效減少開關(guān)損耗。雖然IGBT器件可應(yīng)用于600V以上的電壓場景,但是由于少數(shù)載流子的積聚,在關(guān)斷時(shí)會產(chǎn)生拖尾電流,產(chǎn)生較大的開關(guān)損耗。而SiC器件的漂移層電阻比 Si 器件的要小,不必使用電導(dǎo)率調(diào)制,就能夠以具有快速器件結(jié)構(gòu)特征的 MOSFET 同時(shí)實(shí)現(xiàn)高耐壓和低導(dǎo)通電阻。采用SiC MOSFET 可以達(dá)到開關(guān)損耗減小、散熱器小型化的效果。并且,SiC MOSFET可實(shí)現(xiàn)IGBT無法進(jìn)行的高頻驅(qū)動(dòng),有助于實(shí)現(xiàn)被動(dòng)器件的小型化。
SiC MOSFET可以在更寬的電流范圍和溫度范圍內(nèi)穩(wěn)定工作。SiCMOSFET 不存在像 IGBT 那樣的開啟電壓,因此從小電流到大電流的寬電流范圍內(nèi)都能夠?qū)崿F(xiàn)較低的導(dǎo)通損耗。另外,Si MOSFET 在 150℃時(shí)的導(dǎo)通電阻會上升為室溫時(shí)的2倍以上,但是 SiCMOSFET 的上升率相對較低,因此熱設(shè)計(jì)更加容易、高溫下也能夠?qū)崿F(xiàn)較低的導(dǎo)通電阻。
SiC MOSFET在溫度升高時(shí),其導(dǎo)通電阻上升率低于Si MOSFET和IGBT,耐高溫程度高。這是因?yàn)樵谄骷膶?dǎo)通電阻中,漂移層電阻的占比較小,其他電阻成分的占比較大。溝道電阻 RCH 在高溫時(shí)會稍微下降,n+基板的電阻 RSUB 幾乎沒有溫度依存性。650V 產(chǎn)品的漂移層電阻成分較小,因此溫度系數(shù)非常小;1200V 產(chǎn)品的漂移層會變厚,電阻成分較大,SiC MOSFET的優(yōu)勢更加顯著。
03 碳化硅在高壓車型滲透率提升趨勢明顯
3.1. 高壓車型不斷推出,碳化硅滲透趨勢明顯
800V 方案中快充功率可以達(dá)到 400-500kW, 如小鵬 G9 充電十分鐘續(xù)航 400 公里。 目前市面新能源汽車主流電壓平臺介于 400V-500V 之間,理想 ONE 、小鵬汽車和蔚來汽車的換電方案都在嘗試解決里程焦慮和充電速度慢的問題,未來 800V 快充趨勢明顯。
搭載高壓架構(gòu)的車型逐漸趨向經(jīng)濟(jì)型下沉,推動(dòng)碳化硅市場滲透率提升。碳化硅在高壓方面有先天性能優(yōu)勢,只要車企用的是高壓、650V以上的電池,電壓越大,碳化硅的優(yōu)勢越明顯;在車的續(xù)航能力方面,續(xù)航要求越高,碳化硅越有優(yōu)勢。就乘用車而言,300km以上續(xù)航,碳化硅具備優(yōu)勢,電池需求越大,碳化硅優(yōu)勢越明顯。目前在高續(xù)航和快充的市場需求下,新能源汽車由400V向800V架構(gòu)升級趨勢已成大局,未來隨著電池、器件車成本的降低,經(jīng)濟(jì)型電動(dòng)車也有望搭載高壓方案。隨著碳化硅尺寸的增大、產(chǎn)業(yè)鏈的完善,碳化硅襯底成本下降,碳化硅器件會逐漸擴(kuò)展至中低端車市場,SiC市場空間將被進(jìn)一步打開。據(jù)CASA預(yù)測,到2025年新能源汽車中SiC 功率半導(dǎo)體市場預(yù)計(jì)將以38%的年復(fù)合增長率增長。
碳化硅方案能提升電驅(qū)系統(tǒng)性能,減小器件體積,提高30%左右功率密度:碳化硅功率器件主要應(yīng)用于新能源汽車電機(jī)驅(qū)動(dòng)系統(tǒng)中的電機(jī)控制器。2020年比亞迪漢EV車型電機(jī)控制器使用其自主研發(fā)制造的SiC MOSFET控制模塊,使得其可以在更高的電壓平臺下工作,從而減少設(shè)備電阻損失。比亞迪漢在電力電子系統(tǒng)實(shí)現(xiàn)了更小的體積,同功率情況下,體積縮小30%,即功率密度也將提升30%左右,功率達(dá)到了更高的363kW;車輛的加速性能提升明顯,實(shí)現(xiàn)了3.9s內(nèi)0-100公里的加速;延長汽車的續(xù)航里程至600km以上;這均得益于碳化硅低開關(guān)、耐高壓、耐高溫、導(dǎo)熱率高的優(yōu)良特性。
碳化硅器件可使OBC體積減少60%,能量損耗減少30%:根據(jù)Wolfspeed數(shù)據(jù),OBC采用碳化硅器件與硅器件相比,其體積可減少60%,并減少30%的能量損耗,SiC的峰值效率可以達(dá)到97%,比硅器件提升2%,BOM成本將降低15%。據(jù)產(chǎn)業(yè)調(diào)研,目前OBC市場單價(jià)在300元,即單件成本可降低45元左右。在400V系統(tǒng)相同充電速度下,采用SiC方案充電量將實(shí)現(xiàn)翻倍。目前,全球已有超過20 家汽車廠商在車載充電系統(tǒng)中使用碳化硅功率器件,電壓升高至800V以后,OBC將采用1200V的碳化硅方案。據(jù)Wolfspeed 2021年12月7日化合物半導(dǎo)體大會觀點(diǎn),現(xiàn)在用的650V的硅方案將逐漸淡出市場,在2022年11kW將取代6.6kW成為主流的功率等級。據(jù)產(chǎn)業(yè)調(diào)研,每一個(gè)11kW的SiCOBC約用到10顆碳化硅MOS,單價(jià)7美金,合計(jì)70美金,假設(shè)300萬輛新能源車采用,即對應(yīng)2.1億美金市場。
碳化硅電源轉(zhuǎn)換系統(tǒng)(車載 DC/DC)可簡化設(shè)備結(jié)構(gòu),減小體積:電動(dòng)車上的電池電壓一般比較高,400v或者800v,需要用DC/DC部件將其轉(zhuǎn)換成12v,采用碳化硅器件,設(shè)備溫度積累減少,加之材料本身高導(dǎo)熱率、耐高溫的特點(diǎn),散熱設(shè)備可以簡化,從而減小變壓器體積。
碳化硅充電樁充電效率可由95%提升至97%,電路所占的面積減少25%到30%:SiC的高開關(guān)速度保證了快速充電器的充電速度。用SiC MOSFET設(shè)計(jì)的兩級拓?fù)浔裙鐰C/DC轉(zhuǎn)換器更簡單、更小、更高效,同時(shí)可減少元件數(shù)量,基于SiC的設(shè)計(jì)中有6個(gè)有源元件,而基于Si MOSFET的設(shè)計(jì)中有12個(gè)有源元件,兩級IGBT設(shè)計(jì)中有18個(gè)有源元件。在尺寸方面,基于SiC的電路所占的面積減少了25%到30%。
據(jù)產(chǎn)業(yè)調(diào)研,采用碳化硅方案,在電池容量相同的情況下,其續(xù)航里程可提高5-10%;同理,在續(xù)航里程相同的情況下,電池容量可以減少5-10%。同等電池情況下,明顯增加續(xù)航歷程,假設(shè)原車600KM里程,提升7%,意味著提升有效里程到642KM。整合在電機(jī)能量密度上的提升,以及電路面積等的優(yōu)化,如果為了提升里程,充分利用有效面積,可以進(jìn)一步增加電池容量。
3.2. 使用碳化硅并未增加整車成本
整車廠更加關(guān)注整車成本變化而非僅功率器件成本變化,使用碳化硅方案并未增加整車成本。據(jù)產(chǎn)業(yè)調(diào)研, 在中高端車型單個(gè)電驅(qū)硅基 IGBT 價(jià)值量約 1000-1500 元,按中高端車型兩個(gè)電驅(qū)來計(jì)算,總價(jià)值量約 2000-3000 元;OBC 功率器件成本約 300 元,車載空調(diào)功率器件成本約 100 元,其它如助力轉(zhuǎn)向等約 300 元,合計(jì)硅基功率器件用量約 2700-3700 元。目前碳化硅方案成本是硅基 IGBT 的 3 倍左右,使用碳化硅方案總成本增加 5400-7400 元左右。
動(dòng)力電池占純電動(dòng)汽車總成本的40%-50%,假設(shè)某中高端電動(dòng)車價(jià)格為20萬元,電池成本約8-10萬元,假設(shè)碳化硅方案提升里程5%計(jì)算,相同性能的產(chǎn)品條件下,僅電池系統(tǒng)就為總成本節(jié)省4000元-5000元。
根據(jù)戴姆勒奔馳研究,800V高壓平臺下采用碳化硅模塊較Si基IGBT 模塊整車能降低7.6%的能耗,冷卻系統(tǒng)將節(jié)約1000元左右。
高壓平臺碳化硅方案下,線路電流減小,器件更緊湊,對電纜的需求降低,綜合計(jì)算最終使用碳化硅并未增加整車成本。未來碳化硅規(guī)模化量產(chǎn)之后成本會更低,將為整車成本創(chuàng)造更大空間。
04
新能源車用碳化硅市場預(yù)測
4.1. 碳化硅成本下降趨勢可期
襯底制備是碳化硅器件核心難點(diǎn), 襯底工藝進(jìn)步是成本下降主攻方向。新能源汽車中使用的碳化硅器件襯底主要以導(dǎo)電型碳化硅襯底為主, 目前, 以 6 英寸占主流, 8 英寸襯底開始研發(fā);半絕緣碳化硅襯底以 4 英寸為主, 目前逐漸向 6 英寸襯底發(fā)展。6 英寸襯底面積為 4 英寸襯底的 2.25 倍, 相同的晶體制備時(shí)間內(nèi)襯底面積的倍數(shù)提升帶來襯底成本的大幅降低。與此同時(shí), 單片襯底上制備的芯片數(shù)量隨著襯底尺寸增大而增多, 單位芯片的成本也即隨之降低, 因此碳化硅襯底正在不斷向大尺寸的方向發(fā)展。
成本下降方向:結(jié)合目前成本情況及技術(shù)發(fā)展方向,碳化硅襯底的成本可以通過做大尺寸、提高材料使用效率和提高良率等方式下降。
? 做大尺寸:襯底的尺寸越大,邊緣的浪費(fèi)就越小,有利于進(jìn)一步降低芯片的成本。6英寸襯底面積為4英寸襯底的2.25倍,相同的晶體制備時(shí)間內(nèi)襯底面積的倍數(shù)提升帶來襯底成本的大幅降低,與此同時(shí),單片襯底上制備的芯片數(shù)量隨著襯底尺寸增大而增多,單位芯片的成本也即隨之降低。
? 提高材料使用效率:由于技術(shù)限制,長晶時(shí)間很難縮短,而單位時(shí)間內(nèi)長晶越厚成本越低,因此可以設(shè)法增加晶錠厚度;另一方面,目前的切割工藝很容易造成浪費(fèi),可以通過激光切割或其他技術(shù)手段減少切割損耗。
?提高良率:以山東天岳為例,碳化硅襯底產(chǎn)品良率逐年提升。招股書披露,天岳在襯底制造核心生產(chǎn)環(huán)節(jié)的晶棒良品率由 2018 年的 41.00%上升至 2020 年的 50.73%,襯底良率總體保持在70%以上。隨著工藝的逐步提升,碳化硅襯底生產(chǎn)成本將得到進(jìn)一步下降。
4.2. 800V電壓平臺大力帶動(dòng)碳化硅市場
新能源汽車碳化硅功率器件市場規(guī)模推算:根據(jù)中國汽車工業(yè)協(xié)會數(shù)據(jù),我國新能源汽車銷量由2015 年的33.1 萬輛增至2019 年的120.6 萬輛,復(fù)合增長率達(dá)38%,2021年前11個(gè)月新能源車?yán)塾?jì)產(chǎn)量突破300萬輛,銷量接近300萬輛。中汽協(xié)預(yù)計(jì)2021年全年中國新能源汽車銷量有望達(dá)到340萬輛。IDC預(yù)測中國新能源車銷量至2025年的年均復(fù)合增長率(CAGR)將達(dá)到36.1%。目前比亞迪、吉利極氪、小鵬汽車、廣汽埃安、理想汽車、北汽極狐、嵐圖等車企相繼投資800V電壓架構(gòu)產(chǎn)品,合理假設(shè)2025年碳化硅器件滲透率30%,年均價(jià)格降幅10%,僅碳化硅功率器件在電動(dòng)車市場空間達(dá)220億元。
05
目前難點(diǎn)
(1)新能源車發(fā)展不及預(yù)期風(fēng)險(xiǎn)。新能源車為碳化硅功率器件帶來巨大的增量市場。若新能源車銷量不及預(yù)期, SiC 的發(fā)展會隨之受到影響。
(2)800V 架構(gòu)產(chǎn)品量產(chǎn)不及預(yù)期風(fēng)險(xiǎn)。碳化硅器件優(yōu)勢在高電壓平臺架構(gòu)下發(fā)揮明顯,若800V 車型量產(chǎn)不及預(yù)期,SiC 滲透率會受到影響。
(3)SiC 技術(shù)難度大, 產(chǎn)品研發(fā)、 量產(chǎn)不及預(yù)期風(fēng)險(xiǎn)。國外龍頭企業(yè)大力布局 SiC 領(lǐng)域研發(fā),若國內(nèi)企業(yè)產(chǎn)品研發(fā)失敗、產(chǎn)能不足,無法滿足下游應(yīng)用市場要求,對市場前景會產(chǎn)生不利影響。
(4) SiC 成本高居不下, SiC 滲透率不及預(yù)期風(fēng)險(xiǎn)。目前碳化硅功率器件的價(jià)格仍數(shù)倍于硅基器件, 下游應(yīng)用領(lǐng)域仍需平衡碳化硅器件的高價(jià)格與因碳化硅器件的優(yōu)越性能帶來的綜合成本下降之間的關(guān)系, 一定程度上限制了碳化硅器件的滲透率。若碳化硅制造成本無法下降,對市場應(yīng)用進(jìn)展產(chǎn)生不利影響。
審核編輯:郭婷
-
新能源
+關(guān)注
關(guān)注
26文章
5535瀏覽量
107629 -
電動(dòng)車
+關(guān)注
關(guān)注
73文章
3017瀏覽量
114285 -
SiC
+關(guān)注
關(guān)注
29文章
2841瀏覽量
62734
原文標(biāo)題:800V高壓平臺 & SiC 車規(guī)級應(yīng)用
文章出處:【微信號:EDC電驅(qū)未來,微信公眾號:EDC電驅(qū)未來】歡迎添加關(guān)注!文章轉(zhuǎn)載請注明出處。
發(fā)布評論請先 登錄
相關(guān)推薦
如何辨別符合車規(guī)級標(biāo)準(zhǔn)的電子元器件?
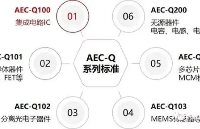
車規(guī)級芯片車身空調(diào)控制方案Demo
瞻芯電子SiC MOSFET技術(shù)新突破,車規(guī)級產(chǎn)品正式量產(chǎn)
瞻芯電子第三代1200V 13.5mΩ SiC MOSFET通過車規(guī)級可靠性測試認(rèn)證
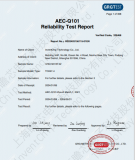
中微愛芯一款車規(guī)級信號鏈芯片和四款車規(guī)級邏輯芯片通過認(rèn)證
瞻芯電子推出一款車規(guī)級1200V SiC三相全橋塑封模塊IVTM12080TA1Z
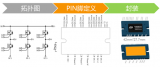
曦華科技推出首款車規(guī)級電容觸控型CVM012x系列MCU
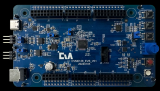
曦華科技車規(guī)級電容觸控型CVM012x系列MCU正式上市!
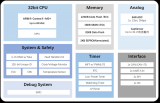
多款產(chǎn)品通過車規(guī)認(rèn)證,國產(chǎn)SiC MOSFET加速上車
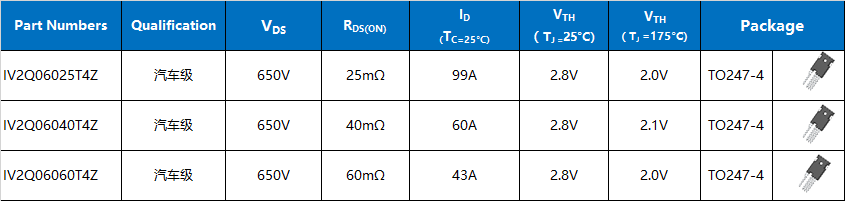
納芯微推出基于創(chuàng)新型振鈴抑制專利的車規(guī)級CAN SIC—NCA1462-Q1
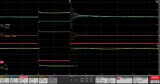
納芯微發(fā)布車規(guī)級CAN SIC NCA1462-Q1
瞻芯電子開發(fā)的3款第二代650V SiC MOSFET通過了車規(guī)級可靠性認(rèn)證
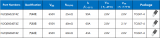
評論