增材制造,更具體地說是金屬增材制造(或金屬3D打印),正在通過消除傳統工藝固有的一些設計限制來改變制造業。許多行業都受益于這項技術,包括國防電子領域,其中晶格結構已應用于單板計算機(SBC)組件,以減輕重量,同時保持性能和加固要求。
增材制造過程逐層創建零件,而不是通過計算機數控(CNC)操作去除材料。金屬增材制造用于生產關鍵的航空航天部件,如火箭發動機或商用飛機結構,在減輕重量方面具有明顯的優勢。鋁和鈦等金屬可以高精度和可重復性打印成復雜的形狀,如圖1所示。
VITA 48.2 傳導冷卻 SBC 主要組件(帶有連接器和組件的電路卡)夾在主蓋和次蓋之間。蓋子由機加工鋁制成,通過楔形鎖系統為底盤提供機械接口,彎曲剛度可避免組件振動疲勞失效,散熱器功能可降低組件工作溫度。由于其巨大的性質,初級和次級蓋都是增材制造工藝的完美候選者,主要目標是減少質量,同時在結構和熱方面保持可比的性能。
晶格結構
這個過程的另一個關鍵部分是利用大地測量和晶格結構。大地測量或格子結構是一種設計類型,它使用許多緊密間隔的對角線桁架元素來提供結構完整性,而不會受到大型結構的重量損失。
巴恩斯·沃利斯爵士在 1930 年代開創了飛機設計中的大地測量結構。維克斯惠靈頓轟炸機的格子結構可以承受難以置信的傷害而不會斷裂,同時減輕了40%或更多的重量。高裝配成本和復雜性使得戰時所需的大批量生產不切實際。
使用當前的金屬增材制造工藝,制造晶格結構現在是一種簡單快捷的過程,可以應用于許多不同類型的結構,如圖2所示,帶來相同的有益剛度/重量比。
[caption id=“” align=“alignnone” width=“450” caption=“Figure 2:圖中是晶格設計的示例。
晶格芯設計的目標是降低蓋子的重量,在我們的例子中重量為2.25磅,同時保持與標準設計相當的結構和熱性能。為了符合接口要求和 VITA 48.2 約束,該設計保留了標準主蓋的所有外部特征,但使用空心/晶格芯,如圖 3 中的橫截面所示。
[caption id=“” align=“alignnone” width=“450” caption=“圖 3:如圖所示為晶格橫截面。
四面體圖案晶格結構使用專有算法TEN TECH LLC定義,旨在均勻分布晶格梁,并允許基于幾何曲率公差或剛度要求的密度變化。選擇面板厚度,為結構提供足夠的支撐和熱質量。用于主要部件和螺釘凸臺的散熱器直接穿過萊迪思核心,并在需要時提供剛度和/或熱質量。
結果
通過這種設計,我們可以實現近50%的重量減輕:新的主蓋重1.23磅,減輕了約1磅的重量。與標準 VITA 48.2 設計相比,我們還看到了 40% 的重量減輕。每個 SBC 減輕 2 磅的重量可以減輕 5 到 20 磅的整體系統重量。此外,第一固有頻率足夠高,以避免與底盤和設備的動態耦合,固有頻率與 MIL-STD-810 感興趣的正弦和隨機振動范圍內的 VITA 48.2 蓋板相當。我們注意到,盡管溫度濃度略高,但由于通芯突起,晶格蓋能夠充分散熱組件。
第一階段研究的重點是原始晶格設計的可行性,并通過仿真證明了這一點。第二階段研究將側重于開發和原型設計,以實現可重復和可預測的產品能夠取代標準的VITA 48.2組件。即使它應用于 6U VITA 48.2 主蓋,格子核心設計也可以輕松應用于 3U 有效載荷甚至底盤下部結構,基本上用更輕的格子設計取代了大型機加工鋁板。
審核編輯:郭婷
-
計算機
+關注
關注
19文章
7489瀏覽量
87870 -
3D打印
+關注
關注
26文章
3547瀏覽量
109036
發布評論請先 登錄
相關推薦
樹莓派與其他單板計算機的比較
3d打印機器人外殼模型ABS材料3D打印噴漆服務-CASAIM
Pine64 發布 Oz64 單板計算機:Arm、RISC-V任你切換
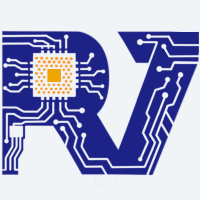
Ubuntu現已適配RISC-V單板計算機Milk-V Mars
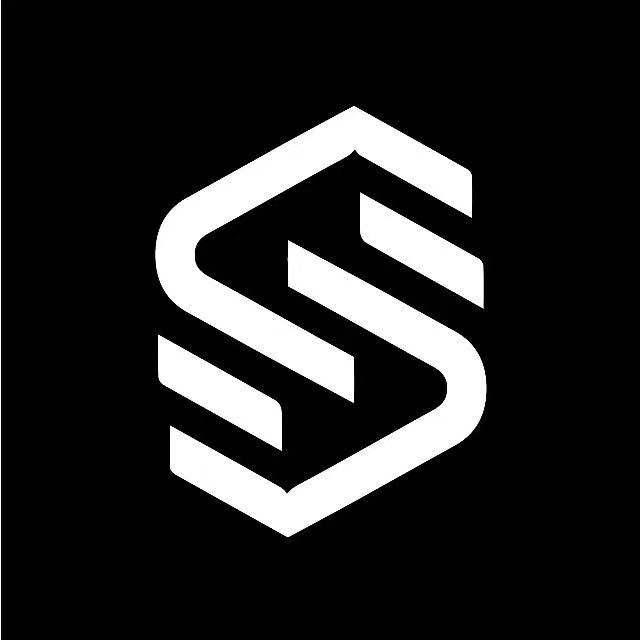
工業無風扇計算機的優點
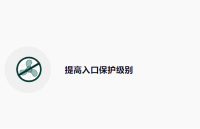
信用卡大小的 RISC-V 單板計算機介紹
【昉·星光 2 高性能RISC-V單板計算機體驗】為 Ubuntu 安裝 Docker 及常用軟件
昉·星光2 RISC-V單板計算機體驗(三) - SSH連接
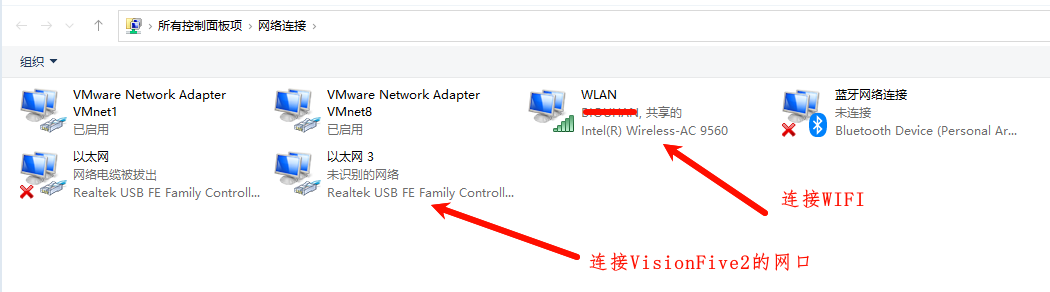
昉·星光2 RISC-V單板計算機體驗(二) - 系統環境
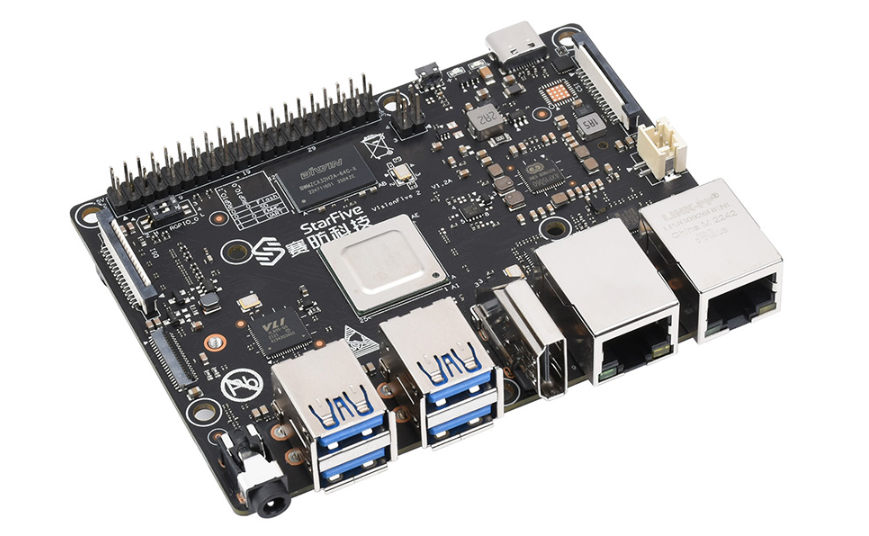
昉·星光2 RISC-V單板計算機體驗(一) - 開箱
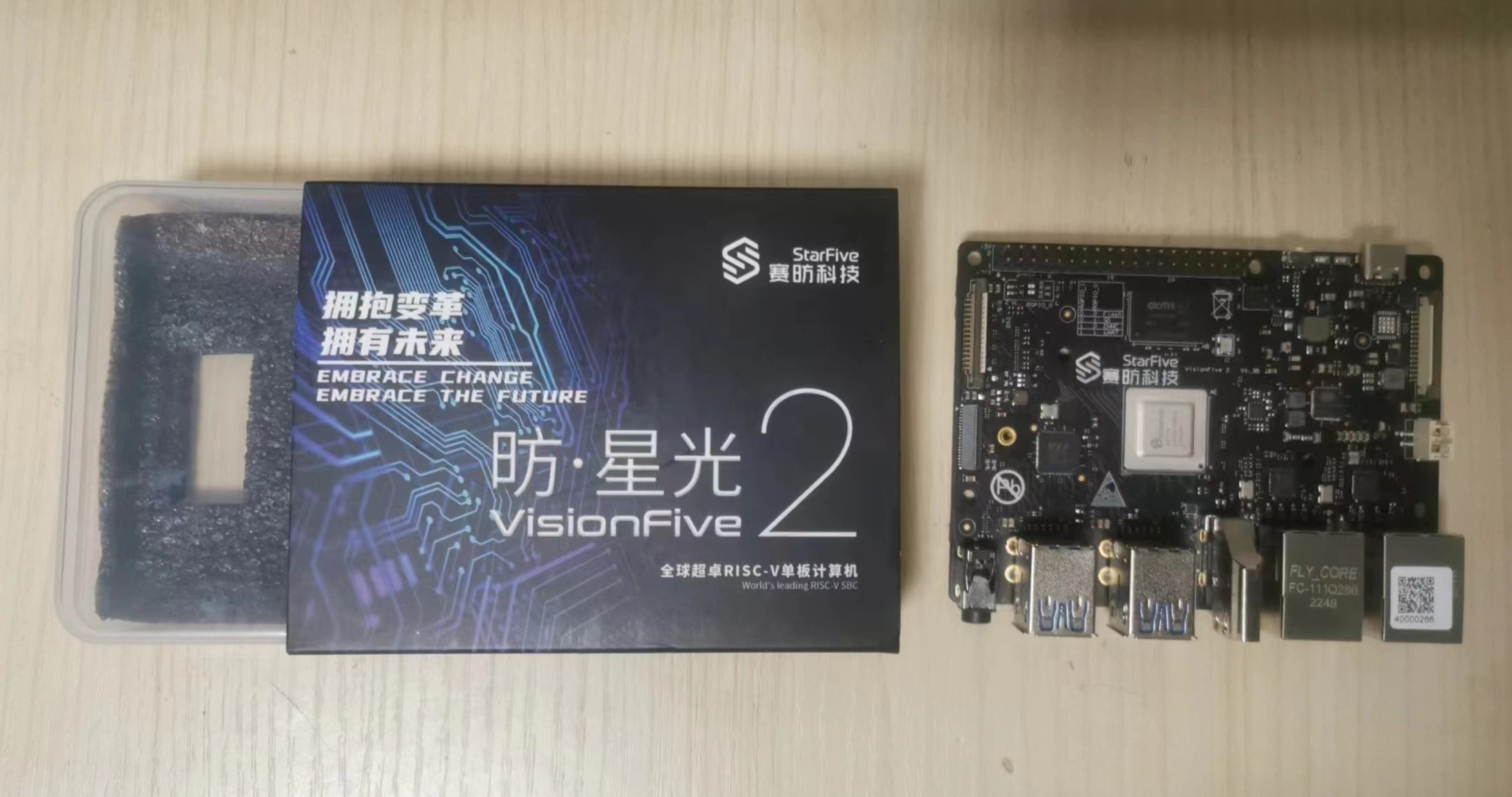
不同類型的嵌入式計算機及其用途
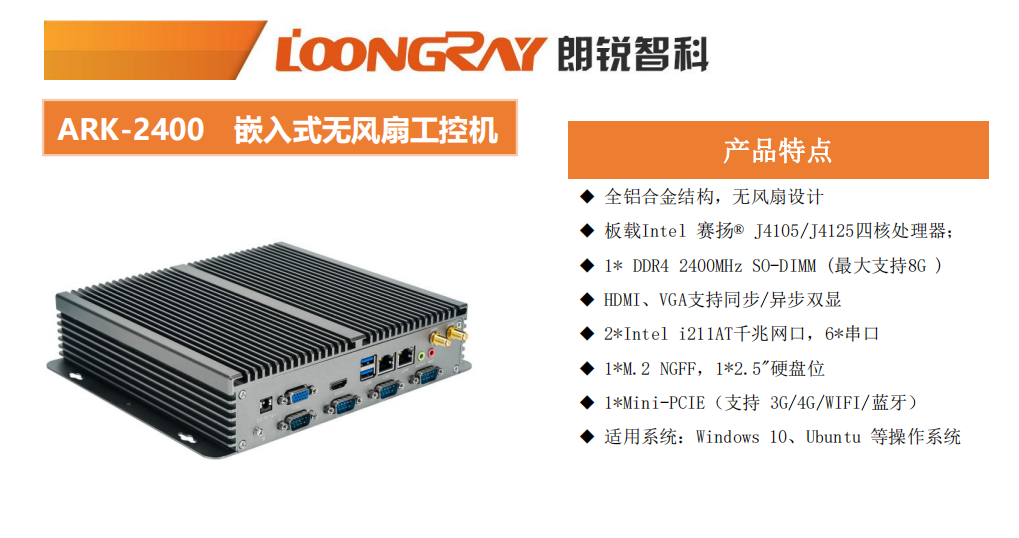
評論