PCB板作為現代電子設備的重要組成部分,是集成各種電子元器件的信息載體,在電子領域中有著廣泛的應用,其質量可直接影響到產品的性能。
而隨著電子科技技術的發展和電子制造業的發展,由于貼片元器件體積小,安裝密度大,這就要求PCB板的集成度進一步提高。
生產線的傳統檢測
在工業生產早期,產品的質量檢測主要靠人工來完成,并且這也是生產的最后一個環節。但是隨著制造業規模化和自動化的發展,大規模的產品堆積,質檢員很難跟上檢測速度、配備多名質檢員,又不能隨著工單的數量機動配置。加之質檢任務的單調性和重復性,導致檢測水平良莠不齊,很難保證客戶的滿意度。外觀檢測是質檢環節中非常重要的一部分,對檢測的精度、效率、速度等方面都有很高的要求。PCB的內部工藝復雜,除了芯板結構層壓、鉆孔、布線外,還需要考慮埋置元件、表面涂飾、清潔和蝕刻等。由于對生產設備的精度和材料性能依賴程度高,一般在設計制作過程中,很容易出現以下各類問題:
PCB工藝邊設計不合理,導致設備無法貼裝。 PCB定位孔問題,導致設備不能準確、牢固地定位。 螺絲孔金屬化,導致過波峰焊后堵孔。 PCB焊盤問題,焊接時出現虛焊、移位、立碑,或焊點少錫。 Mark點設計問題,造成機器識別困難。 位號或極性標志缺失,位號顛倒,字符過大或過小等。 測試點、元件之間的距離放置不規范,可維修性差。
傳統的檢測采用人工檢測方法,容易漏檢、檢測速度慢、檢測時間長、成本高,已經逐漸不能夠滿足生產需要。為了保證電子產品的性能,PCB板缺陷檢測技術已經成為電子行業中非常關鍵的技術。
隨著PCB日趨超薄型、高密度、細間距,PCB線路板上元器件上的線寬、間距等已經達到微米級,人工檢測已經遠不能滿足如此高精密度的檢測需求。
機器視覺檢測技術是建立在圖像處理算法的基礎上,通過數字圖像處理與模式識別的方法來實現,與傳統的人工檢測技術相比,提高了缺陷檢測的效率和準確度。
機器視覺系統一般采用CCD或CMOS工業相機攝取檢測圖像并轉化為數字信號,再通過計算機軟、硬件技術對圖像數字信號進行處理,從而得到所需要的各種目標圖像特征值,并由此實現零件識別或缺陷檢測等多種功能。
識別分類檢測
通過視覺檢測PCB外形、尺寸、內孔,與系統加載入的產品黑白特征圖匹配來識別板子的編號。
鉆孔編碼檢測
鉆孔記號根據編碼規則進行解碼。
焊盤外觀檢測
在PCB生產工藝中,顯影線后會出現焊盤蓋油的現象,在此工位及時的檢測發現問題,可減少后面的一系列工序,可節省成本。
字符讀取檢測
檢測PCB板字符碼形態是否符合標準,是否清晰無缺失,線條是否光滑無凸點,是否存在線體重合、重影、麻點、變形、色差、偏位、錯印等缺陷。
外觀檢測
機器視覺檢測技術,可以實現包括PCB、BGA、管腳和貼片檢測,以及焊點、元件缺失、方向錯誤等方面的完整性檢測。比如:PCB板表面是否有污漬、雜物、凹坑、錫渣殘留;表面字符和符號是否清晰;焊盤上錫是否均勻,等等。
機器視覺技術在PCB檢測上的應用
PCB檢測方案主要分為2D與3D兩類。2D可實現諸如短路、空焊、錫洞及少錫等多種缺陷檢測,針對不同種缺陷采用硬件種類及系統布局方案有所不同;而3D常用激光線掃/PMP等設備,既可實現輪廓掃描,亦可實現如細小的QFN、LGA元件檢測,二者應用場景及針對缺陷種類有所不同。
2D檢測
以電路板元器件檢測案例為例:
產品檢測
要求:
1、檢測電容是否漏裝,正負極是否貼反。
2、檢測連接器是否漏裝,正反是否裝反。
檢測原理
根據電容上面兩端印刷圖案的不同,通過機器視覺技術來區別它的正反差異,即電容極性。
檢測結果
合格產品檢測的結果
?一個電容裝反后檢測的結果
?漏裝一個電容后的檢測結果
3D檢測
針對PCB領域的3D檢測方案,業界主要采用激光線掃/正弦條紋PMP等方案實現。
激光線掃方案通常利用激光輪廓儀結合傳送機構(類似2D線陣檢測系統),實現PCB表面建模及自動檢測;
案例一:紐扣電池安裝到位檢測
圖左:電池安裝到位狀態,圖右:電池未安裝到位狀態
圖左:電池安裝到位狀態,圖右:電池未安裝到位狀態
案例二:電阻漏裝檢測
圖左:電阻正常焊接狀態,圖右:電阻漏焊狀態
圖左:電阻正常焊接狀態,圖右:電阻漏焊狀態
案例三:電阻撞歪檢測
圖左:電阻正常安裝狀態,圖右:電阻安裝撞歪狀態
圖左:電阻正常安裝狀態,圖右:電阻撞歪狀態
審核編輯:郭婷
-
pcb
+關注
關注
4319文章
23111瀏覽量
398237 -
機器視覺
+關注
關注
162文章
4378瀏覽量
120393 -
AI
+關注
關注
87文章
30996瀏覽量
269285
原文標題:AI機器視覺在PCB板中的全方位識別檢測
文章出處:【微信號:actSMTC,微信公眾號:actSMTC】歡迎添加關注!文章轉載請注明出處。
發布評論請先 登錄
相關推薦
機器視覺檢測應用場景:缺陷檢測、尺寸測量、引導定位、運動控制
使用TI Edge AI Studio和AM62A進行基于視覺AI的缺陷檢測
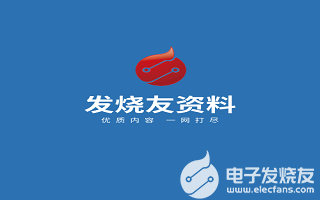
評論