交通運(yùn)輸行業(yè)的全球電氣化需要開發(fā)高效且具有成本效益的電氣化動力系統(tǒng)解決方案。牽引系統(tǒng)中 800 V 的應(yīng)用實(shí)現(xiàn)了快速充電的優(yōu)勢,并可以減少導(dǎo)體的橫截面積以降低重量和成本。
由于電池仍然是電驅(qū)動系統(tǒng)的最主要成本構(gòu)成,因此以最高效的方式使用電池提供的能量是很重要的,從電能到機(jī)械能的轉(zhuǎn)換效率即電驅(qū)動系統(tǒng)效率就顯得及其重要。為了提高效率,必須減少功率損耗:
①逆變器的功率損耗必須保持在較低水平;
②同時(shí)必須降低電動機(jī)的諧波損耗。
碳化硅 (SiC) 技術(shù)的應(yīng)用,為 800 V 系統(tǒng)提供了實(shí)現(xiàn)這兩個(gè)目標(biāo)的可能性。
眾所周知,SiC功率器件比硅Si更高效,因?yàn)檩p載導(dǎo)通損耗和開關(guān)損耗都更低。SiC技術(shù)可實(shí)現(xiàn)更高的開關(guān)頻率,從而通過降低諧波損耗來提高電機(jī)的效率。SiC半導(dǎo)體材料特性、效率優(yōu)化的模塊設(shè)計(jì)以及改進(jìn)的控制技術(shù)相結(jié)合,組成了由逆變器 和電機(jī)組成的高效牽引系統(tǒng)。對于優(yōu)化設(shè)計(jì)后的系統(tǒng),在 WLTP 循環(huán)中,驅(qū)動系統(tǒng)效率可提高4?8%。
01
電驅(qū)系統(tǒng)效率提升
純電動汽車 (BEV) 的成功取決于兩個(gè)主要方面。汽車的購置成本和客戶可用性。BEV 的電池續(xù)航里程仍然是客戶可用性最重要的特征之一。
電池續(xù)航里程定義了每次電池充電的最大行駛距離和長途旅行的充電時(shí)間。這兩個(gè)標(biāo)準(zhǔn)都會受到牽引系統(tǒng)電壓水平的影響。更高的 800 V 系統(tǒng)電壓而不是 400 V 的通用電壓允許在恒定電纜橫截面下更快地為電池充電(大功率充電、超快速充電)。
目前的產(chǎn)品中,IGBT用作逆變器中的開關(guān)元件,在 800 V 的電壓下表現(xiàn)出效率劣勢,因?yàn)镮GBT開關(guān)損耗太大。要高效使用更高的電壓,需要更高效的開關(guān)技術(shù),請參見圖1。
SiC?MOSFET的應(yīng)用,可以滿足在高電壓平臺下高開關(guān)頻率的高效優(yōu)勢,以及高壓擺率 (dv/dt) 。更高的開關(guān)頻率降低了電機(jī)的諧波損耗。因此,SiC是通往更高系統(tǒng)電壓的關(guān)鍵技術(shù)。
如果可以找到電機(jī)和逆變器的兩條隨開關(guān)頻率相反運(yùn)行的損耗曲線之間的最佳平衡,則 WLTP 系統(tǒng)級(800 V Si 系統(tǒng)與 800 V SiC 系統(tǒng)相比)的效率可能提高 4 % 至 8 %)。效率描述了存儲在電池中的能量與用于產(chǎn)生牽引力的能量之比。
因此,更高的效率可以實(shí)現(xiàn)在電池容量相同的情況下更長的里程,或者在電池容量降低的情況下產(chǎn)生里程不變。因此,提高效率是優(yōu)化 BEV 成本的最大措施。SiC 技術(shù)應(yīng)用帶來的是系統(tǒng)成本優(yōu)勢,因?yàn)樗鼈兛梢怨?jié)省更多的電池。
以下基于前大陸動力總成具有 SiC MOSFET 的 800 V 的EMR4 的電力電子控制器(逆變 )來分析。
02
開關(guān)頻率和電壓
壓擺率(dv/dt)在系統(tǒng)層面的影響
在電機(jī)運(yùn)行期間,逆變器將電池提供的直流電壓轉(zhuǎn)換為快速脈沖電壓。該脈沖電壓會產(chǎn)生諧波交流 (AC) 電流。交流相電流產(chǎn)生轉(zhuǎn)子跟隨的旋轉(zhuǎn)電磁場。通過這種方式,脈沖電信號逐漸接近均勻正弦波形(40 kHz 及更高)的最佳值,高頻損耗減小。電流的頻譜變得“更干凈”,從而減少了以發(fā)熱形式出現(xiàn)的諧波損耗。
圖2 顯示了損耗開關(guān)頻率之間的關(guān)系? 其中:
電機(jī)的總損耗 – PL,EM,total
逆變器總損耗 – PL,PE,total
– 在牽引系統(tǒng)的某個(gè)工作點(diǎn)。
電機(jī)損耗曲線為綠色,紅色為電力電子損耗。
特性曲線描述了每個(gè)參數(shù)的開關(guān)頻率的理論相關(guān)性:隨著開關(guān)頻率的增加,電機(jī)諧波損耗Ph,total 逐漸減少,所以總電機(jī)損耗 PL,EM,total 逐步向純正弦電流波形產(chǎn)生的鐵損值收斂 PL,total (水平虛線)。顯示的圖表是電機(jī)高分辨率 FEM 模擬的結(jié)果 。灰色標(biāo)記頻率區(qū)域的頻率相關(guān)功率損耗的準(zhǔn)確性相對于20kHz之前要低,由于仿真的模擬步長為5us。
逆變器總損耗 PL,PE,total 由導(dǎo)通損耗PL,cond和開關(guān)損耗 PL,SW 組成,開關(guān)損耗隨開關(guān)頻率線性增加。同時(shí),該半導(dǎo)體的導(dǎo)通損耗不受開關(guān)頻率的影響。因此,逆變器總損耗預(yù)計(jì)會隨著開關(guān)頻率的增加而線性增加,與開關(guān)損耗的增加相同,見圖2。
上述分析基礎(chǔ)是一個(gè) 800 V 系統(tǒng),逆變器中使用了 SiC MOSFET。特征曲線在圖2 展示了 SiC 技術(shù)在逆變 功率模塊中的關(guān)鍵作用,作為實(shí)現(xiàn)最高系統(tǒng)效率的關(guān)鍵因素。圖2 進(jìn)一步表明,系統(tǒng)級的最佳開關(guān)頻率必須定義為提高效率(平衡點(diǎn))的影響因素。
與Si逆變相比,SiC逆變技術(shù)的全部潛力基于開關(guān)頻率和壓擺率高10倍的可能性。圖3演示了電壓壓擺率 (dv/dt) 對逆變損耗的影響。
帶有 SiC MOSFET 的高效 800 V 牽引系統(tǒng)的當(dāng)前開發(fā)研究了如何在不產(chǎn)生額外的干擾的情況下使用 SiC 技術(shù)的潛力(參見第 3 章和第 4 章),為了充分發(fā)揮 SiC 技術(shù)的潛力,必須考慮系統(tǒng)在高開關(guān)頻率和高電壓壓擺率下的電磁兼容性 (EMC) 以及噪聲振動 (NVH) 問題。如圖2所示,特別是較低的開關(guān)頻率對 NVH 具有關(guān)鍵影響。EMC正好相反,較高的開關(guān)頻率和壓擺率會導(dǎo)致更多的干擾。
03
對逆變器的影響
當(dāng)今最先進(jìn)的 400 V Si?IGBT 逆變 在 8 至 10 kHz 的開關(guān)頻率下運(yùn)行。電壓壓擺率通常高達(dá) 5 kV/μs。圖 4 顯示了單個(gè)逆變系統(tǒng) (Si / SiC) 的差異以及不同輸出功率下產(chǎn)生的損耗。累積的總功率損耗分為開關(guān)損耗和導(dǎo)通損耗。
傳統(tǒng) Si 技術(shù)和 SiC 技術(shù)在 800 V 下的總功率損耗之間存在顯著差異。該圖證實(shí)了 800 V 電壓只能與 SiC 半導(dǎo)體一起使用。
評估逆變器的決定性因素是驅(qū)動系統(tǒng)在 WLTP 循環(huán)工況下的效率。圖 5 說明了逆變器對 WLTP 中系統(tǒng)效率的影響。條形圖的黃色部分顯示了 800 V SiC 相對于 800 V Si 解決方案的優(yōu)勢——盡管在這兩種情況下都只應(yīng)用了 10 kHz 的開關(guān)頻率和 5 kV/μs 的電壓壓擺率。配備 SiC 半導(dǎo)體的逆變 可能會在更高的頻率和轉(zhuǎn)換率下運(yùn)行(典型值:開關(guān)頻率:10 ... 40 kHz,dv/dt:5 ... 50 kV/us)。左側(cè)的第二個(gè)欄圖 5 顯示了如果將 Si 逆變 用于800 V 系統(tǒng),損耗將如何變化。
圖1 - 5所示SiC技術(shù)在不同方面的更高效率是基于嵌入在硅中的碳原子在材料基體中的高載流子遷移率。
由于導(dǎo)通電阻低,在SiC半導(dǎo)體中產(chǎn)生的熱損失很低。這允許更高的開關(guān)頻率,緊湊的封裝空間和減少功率模塊的冷卻能力需求。因此,SiC半導(dǎo)體比Si半導(dǎo)體需要更小的封裝空間,可以實(shí)現(xiàn)更高的功率密度。
3.1 更高導(dǎo)電性的優(yōu)勢
在今天的汽車牽引逆變器(400 V系統(tǒng)電壓水平和高達(dá)10 kHz的開關(guān)頻率)低損耗硅IGBT與一個(gè)并聯(lián)的二極管(自由運(yùn)行分別回流到電池)。反向電壓(反電勢)在650…750之間時(shí),IGBT需要比較復(fù)雜的控制,但由于在額定電壓下的高效率,它就像“完美的開關(guān)”一樣工作。Mosfet(金屬氧化物半導(dǎo)體場效應(yīng)晶體管:簡單地說:電壓控制電阻)更容易控制。在Si基半導(dǎo)體材料基礎(chǔ)上,在開關(guān)過程中Mosfet比硅IGBT有更高的電阻(R)(R在漏/源上= Rdson)。
在400 V時(shí),較高的硅MOSFET功率損耗已經(jīng)不適用,在800 V時(shí),它們被排除在選項(xiàng)之外(見圖5)。硅MOSFET的反向耐壓越高,其Rdson越高。在600v電壓水平以上,這種特點(diǎn)對整體效率有巨大影響。此外,還必須考慮在更高電壓下增加的冷卻成本。
在4H襯底(極高載流子遷移率的四元矩陣)中使用SiC技術(shù)的Mosfet在開關(guān)過程中表現(xiàn)出比使用Si技術(shù)更高的效率。低Rdson的優(yōu)勢是SiC MOSFET半導(dǎo)體在800 V逆變器應(yīng)用的主要原因。
較寬的帶隙和較低的表面電阻上較高的擊穿電壓,允許以較高的壓擺率切換高電壓,以上這些都是SiC的材料優(yōu)勢。由于更低的Rdson,開關(guān)損耗較低,可以應(yīng)用較高的開關(guān)頻率,見圖6。特別是在輕載時(shí),低導(dǎo)通損耗有對工況效率意義巨大。
考慮到所有的限制條件,例如功率模塊的連接接口,SiC技術(shù)可能實(shí)現(xiàn)功率模塊體積減少25…50%。SiC比Si具有更高的導(dǎo)熱系數(shù),這為熱損耗的更好傳導(dǎo)散熱提供了可能。同時(shí),SiC半導(dǎo)體可以在更高的溫度下工作。以上這些這就提供了逆變器設(shè)計(jì)要求的高功率密度條件。
綜合分析表明,SiC可以提高逆變器的效率,降低開關(guān)損耗,減少封裝體積,減少冷卻能力,提高工作溫度,減少功率模塊的重量。
與400V Si逆變器相比,400V SiC逆變器可以設(shè)計(jì)得更加緊湊。800V SiC逆變器需要更大的體積,因?yàn)榕离娋嚯x和電氣間隙要求更大。
原則上,SiC技術(shù)的優(yōu)勢也可以與400V系統(tǒng)結(jié)合使用,但只有在逆變器中才能實(shí)現(xiàn)效率優(yōu)勢。額外的優(yōu)勢,如超高速充電需要更高的電壓。為了研究SiC的優(yōu)勢,在整車上對一個(gè)400V SiC逆變器樣機(jī)進(jìn)行了測試。采用SiC技術(shù)的800V逆變器目前正處于測試階段。
3.2 SiC的壓擺率(dv/dt)優(yōu)勢
如圖7所示,在SiC半導(dǎo)體中,通過增加壓擺率dv/dt可以降低開關(guān)損耗。與硅相比,該技術(shù)具有更大的潛力,因?yàn)閾Q相電路中較高的轉(zhuǎn)頻率和可調(diào)整的雜散電感降低了功率損耗。這就需要優(yōu)化柵極源電路中的雜散電感。由于換相電路中極低的雜散電感的實(shí)現(xiàn)成本相對較高,因此在系統(tǒng)級上定義平衡的dv/dt是優(yōu)化的一部分。
在一定的dv/dt下模擬雜散電感。結(jié)合開關(guān)頻率的增加,可以模擬一個(gè)WLTP周期的總功率損耗。在5…20kv /μs壓擺率范圍內(nèi),雜散電感處于較低水平時(shí),對WLTP損耗是明顯的。
3.3 電磁兼容性
眾所周知,高頻開關(guān)過程會引起電磁干擾。為了在牽引逆變器中應(yīng)用碳化硅Mosfet,必須研究高開關(guān)頻率和壓擺率與高屏蔽和濾波效果之間的權(quán)衡。圖8顯示了開關(guān)頻率加倍(10 kHz到20 kHz)對典型測量中的干擾頻和干擾強(qiáng)度。在20kHz時(shí),干擾強(qiáng)度增加約6dB。僅僅提高開關(guān)頻率并不能得到最優(yōu)解決方案。必須研究SiC的最優(yōu)控制參數(shù),這將使系統(tǒng)具有良好的電磁兼容性能條件下,在可能的開關(guān)頻率下可接受的開關(guān)損耗得到最佳的效率增加。
04
電機(jī)設(shè)計(jì)
800V應(yīng)用的一體化高效電驅(qū)動的開發(fā)基礎(chǔ)是大規(guī)模系列生產(chǎn)的EMR4電機(jī)系統(tǒng)。EMR4將比EMR3有更大的可擴(kuò)展性,更多可能的子組件組合(作為800V逆變器選項(xiàng))。此外,互連設(shè)計(jì)將更加標(biāo)準(zhǔn)化,互連的可擴(kuò)展性也將提高。特別是在低功耗應(yīng)用中,組裝空間將會減少。與EMR4設(shè)計(jì)相比,通過改變互連設(shè)計(jì),800V電機(jī)的線圈數(shù)量增加了一倍。
4.1采用碳化硅技術(shù)提高電機(jī)效率
第3章的功率損耗分析表明,在相同的冷卻能力下,SiC mosfet能夠?qū)崿F(xiàn)更快、更頻繁的開關(guān)。較高的開關(guān)頻率可以提高電機(jī)的效率。開關(guān)頻率越高,諧波電流越小。因此,增加開關(guān)頻率可以降低逆變器提供的諧波輸入功率。
圖9在功率流圖中演示了前面一節(jié)中描述的方面。通常的功率流(灰色)從輸入功率,通過氣隙功率,到軸上的機(jī)械輸出功率。定子和后來的轉(zhuǎn)子的功率損失是通過散熱傳遞的。紅色表示的是完全轉(zhuǎn)化為熱量而不影響機(jī)械功率的諧波輸入功率。采用碳化硅技術(shù)可以降低800V電機(jī)的諧波損耗。
4.2 800V電機(jī)的設(shè)計(jì)參數(shù)
眾所周知,變頻供電的電機(jī)比由恒定頻率的正弦波供電的恒速運(yùn)行的電機(jī)應(yīng)力更大。圖10顯示了快速開關(guān)逆變器對電機(jī)造成的額外影響。800 V SiC技術(shù)的應(yīng)用需要更仔細(xì)地觀察電機(jī)的絕緣系統(tǒng)和軸電流。
雖然逆變器提供的上升時(shí)間很短的高頻電壓脈沖為高效系統(tǒng)創(chuàng)造了基礎(chǔ),但這些脈沖增加了對電機(jī)的壓力。特別是在高輸出功率時(shí),可以觀察到最高的壓擺率。
系統(tǒng)設(shè)計(jì)的目標(biāo)是在低諧波損耗和由于高開關(guān)頻率和壓擺率而增加的絕緣系統(tǒng)要求和電機(jī)的使用壽命之間找到適當(dāng)?shù)钠胶狻_@兩個(gè)方面的最佳平衡對碳化硅牽引系統(tǒng)的設(shè)計(jì)具有重要意義。
電機(jī)的絕緣系統(tǒng)必須承受過沖電壓,這是由于800V的電壓水平與高開關(guān)頻率和dv/dt的結(jié)合而產(chǎn)生的。
這些系統(tǒng)的測試電壓也會增加。電機(jī)和逆變器輸出端子之間的電纜長度必須設(shè)計(jì)得盡可能短,以防止由于反射電壓波而產(chǎn)生額外的電壓過沖。
圖 10 中的反射系數(shù) r 和電機(jī)阻抗 Z 說明了這一方面的問題。通過選擇最佳 dv/dt 以及最佳上升時(shí)間,應(yīng)考慮臨界電纜長度與上升時(shí)間直接相關(guān)。由于這種關(guān)系,電壓上升時(shí)間不能按需要選擇得那么高。這意味著要開發(fā) EMR4 的 800 V平臺,必須研究絕緣系統(tǒng)的行為和使用壽命。
高電壓峰值會導(dǎo)致局部放電,因?yàn)榉逯惦妷海ɡ鐚?dǎo)體和疊片之間的電壓)可以達(dá)到在薄弱點(diǎn)破壞絕緣系統(tǒng)的水平(PDIV問題)。這會導(dǎo)致絕緣系統(tǒng)在短時(shí)間內(nèi)發(fā)生故障。產(chǎn)生的電流會對絕緣系統(tǒng)產(chǎn)生永久應(yīng)力。結(jié)果,系統(tǒng)升溫并老化。
了解電壓脈沖對使用壽命的影響很重要。相應(yīng)的局部放電測量結(jié)果用于絕緣系統(tǒng)的設(shè)計(jì)。
此外,調(diào)速電機(jī)中存在在逆變器運(yùn)行下引起高頻軸承電流的問題。這些包括由電機(jī)軸末端電位差引起的循環(huán)電流(軸、軸承、定子、定子外殼、軸承、軸),以及電容性軸承電流(也稱為 dv/dt 電流)和放電由于共模軸承電壓 Ub 的時(shí)間變化而產(chǎn)生的放電(EDM) 電流。
當(dāng)軸承潤滑劑的潤滑膜容量局部擊穿時(shí),EDM 電流在高振幅放電電流峰值時(shí)出現(xiàn)。在汽車領(lǐng)域,EDM 電流被認(rèn)為與實(shí)際應(yīng)用相關(guān)。共模軸承電壓 Ub 與共模電壓 U0 的比值——所謂的軸承電壓比 (BVR)——可用于對預(yù)期 EDM 電流的初步估計(jì)。在不同工作點(diǎn)的軸承電壓的高分辨率測量中,可以觀察到特征電壓峰值,表明相關(guān)的放電電流。可以根據(jù)軸承的使用壽命確定關(guān)鍵工作點(diǎn)。在確定潛在工作點(diǎn)后,對這些工作點(diǎn)的高比例進(jìn)行連續(xù)測試,并評估軸承的使用壽命。
如圖 10 所示,軸承電壓Ub 通過電容分壓器連接到共模電壓 U0。它由寄生電容(繞組外殼 Cw,h,繞組轉(zhuǎn)子 Cw,r 轉(zhuǎn)子外殼 Cr,h)和軸承阻抗 Zb 組成。等效電路圖顯示了防止 EDM 電流的措施,例如使用軸接地、定子繞組頭的靜電屏蔽或使用控制方法將U0降至最低。
05
系統(tǒng)分析
前面的章節(jié)展示了 SiC 技術(shù)在組件級別的影響和可能性。下一步是在成本和效率方面將優(yōu)勢整合到優(yōu)化的牽引系統(tǒng)中,同時(shí)還要考慮 NVH 和 EMC問題。
5.1 在 WLTP 工況上轉(zhuǎn)移單個(gè)特征點(diǎn)
為了根據(jù)扭矩-速度特性圖中的測量值評估 WLTP 工況下的有效性,選擇 WLTP 中累積最大的點(diǎn)作為測試的測量點(diǎn)。圖 11 顯示了 帶有 EMR4 系統(tǒng)的 D級車驅(qū)動系統(tǒng)直方圖值。定義了 35 個(gè)操作點(diǎn),并在電機(jī)測試臺上以不同的開關(guān)頻率結(jié)合不同的壓擺率進(jìn)行測量。
5.2 測試結(jié)果的討論
對測量結(jié)果的評估揭示了兩個(gè)對 SiC 技術(shù)的進(jìn)一步發(fā)展具有決定性意義的關(guān)鍵發(fā)現(xiàn)。對于基本測量,在逆變器中實(shí)施了高電壓和低壓擺率。在某些操作點(diǎn),高壓擺率對應(yīng)于 10 kV/μs,低至 5 kV/μs。
圖 12 顯示了在中速范圍內(nèi)低扭矩的一個(gè)工作點(diǎn)上器件級別和系統(tǒng)級別的功率損耗差異。逆變器的功率損耗預(yù)計(jì)會隨著開關(guān)頻率的增加而增加,并且在測量精度內(nèi)無法檢測到 5kV/μs 和 10kV/μs 之間的差異。這是由于依賴于操作點(diǎn)的壓擺率,它在低負(fù)載下的影響很小。另一方面,電機(jī)的功率損耗隨著開關(guān)頻率的增加而降低,但也會對 10 kV/μs 的更高電壓轉(zhuǎn)換率做出反應(yīng)。這一優(yōu)勢補(bǔ)償了由于更高的開關(guān)頻率而導(dǎo)致的系統(tǒng)級更高的逆變器損耗。總的來說,它提高了系統(tǒng)效率。
在圖 13 中可以觀察到 10 kV/μs 對更高電流的逆變器級別的優(yōu)勢,因?yàn)檎w逆變器損耗隨著逆變器電流(分別是逆變器輸出功率)的增加而增加。與低速下測得的性能相比,電機(jī)性能可能沒有變化,但在高于 8 kHz 的更高開關(guān)頻率下,在系統(tǒng)級僅觀察到微小的改進(jìn)。通過調(diào)整更高的壓擺率,圖 13 中觀察到的優(yōu)勢應(yīng)轉(zhuǎn)移到特性曲線中的所有操作點(diǎn)。
5.3 WLTP 節(jié)能評估
測量值用于校準(zhǔn)逆變器和電動機(jī)的仿真模型,以識別 WLTP 循環(huán)中的整體效率,并模擬未來的其他工況循環(huán)。為了初步表明 SiC 技術(shù)的效率潛力,系統(tǒng)級的測量損耗已轉(zhuǎn)換為特性圖。已經(jīng)通過適當(dāng)?shù)牟逯捣椒ń⒘俗銐蚓_的網(wǎng)格,以表示驅(qū)動模擬中的整個(gè)循環(huán)。圖 14 顯示了作為示例的特征系統(tǒng)圖,電壓壓擺率為 5 kV/μs,開關(guān)頻率為 12 kHz。
圖 15 顯示了 D 級車輛在 WLTP 循環(huán)中的結(jié)果,限值介于 5 kV/μs(6 和 12 kHz)和 10 kV/μs(6 和 12 kHz)之間。WLTP 中 PWM 頻率的增加導(dǎo)致電機(jī)效率的增加。此外,它證實(shí)了逆變器輸出電壓壓擺率的增加會導(dǎo)致逆變器中 6 kHz 和 12 kHz 的電氣損耗降低。
根據(jù)圖 14 和 15,計(jì)算出的逆變器損耗減少值低于開發(fā)目標(biāo)。因此,測得的工作點(diǎn)效率提高和隨后映射到 WLTP 表明,通過減少碳化硅半導(dǎo)體的開關(guān)損耗,WLTP 可以實(shí)現(xiàn)顯著優(yōu)勢。優(yōu)化的下一步是增加頻率和電壓壓擺率。
5.4 優(yōu)化
從所進(jìn)行的研究可以推斷,通過在逆變器中使用碳化硅半導(dǎo)體,除了調(diào)制方法和開關(guān)頻率變化等控制策略的經(jīng)典參數(shù)外,還可以使用新參數(shù)來提高效率。電壓壓擺率提供了除開關(guān)頻率之外優(yōu)化系統(tǒng)效率的可能性。
06
總結(jié)與展望
由于提高效率的巨大潛力,半導(dǎo)體材料碳化硅的使用面臨著高壓應(yīng)用的突破。系統(tǒng)優(yōu)化提供了實(shí)現(xiàn)逆變器和電機(jī)最大效率的解決方案。使用 D 級車的例子,通部分工作點(diǎn)的效率提升分析,映射到它們對 WLTP 有效性的影響,提升WLTP工況里程。
眾所周知,碳化硅在開關(guān)狀態(tài)下比采用硅 IGBT 的當(dāng)前標(biāo)準(zhǔn)解決方案具有更高的電導(dǎo)率。在車輛層面,與 Si IGBT 相比,使用 SiC MOSFET 可將 800 V 電壓水平的系統(tǒng)效率提高多達(dá) 3%。除了這一優(yōu)勢之外,碳化硅還可以顯著提高逆變器輸出的電壓壓擺率 > 20 kV/μs(理論上),這是當(dāng)今的硅半導(dǎo)體解決方案所不能達(dá)到的指標(biāo)。與 Si IGBT 相比,在相同開關(guān)頻率下的逆變器可以進(jìn)一步提高 2-4% 的效率。這已在某些操作點(diǎn)上得到驗(yàn)證。然而,WLTP 中最佳開關(guān)頻率和電壓壓擺率的全部潛力的發(fā)揮需要進(jìn)一步研究。
通過增加開關(guān)頻率,由于較低的諧波電流和較低動態(tài)損耗,電機(jī)得到了更高的效率。
開關(guān)頻率的增加通常會導(dǎo)致逆變器中開關(guān)損耗的增加。使用碳化硅半導(dǎo)體的解決方案可以通過提高電壓轉(zhuǎn)換率來降低作為逆變器開關(guān)頻率函數(shù)的整體開關(guān)損耗。這種效果可以積極地用于提高逆變器和電機(jī)系統(tǒng)的效率。
總體而言,電動機(jī)頻率的增加導(dǎo)致效率進(jìn)一步提高 1-2%。為了減少效率劣勢,必須在 EMC 約束允許的情況下將電壓壓擺率調(diào)整為最高。通過使用 SiC 代替 Si 半導(dǎo)體,系統(tǒng)優(yōu)化在 800 V 的電壓水平下總共提高了 6 – 8% 的效率。
開關(guān)頻率增加到 20 kHz,電壓壓擺率增加到 15 kV/μs 是開發(fā)過程的下一步。這并不代表碳化硅可以獲得的最大可能值,但考慮到絕緣和 EMC 行為,這些參數(shù)在大規(guī)模批量生產(chǎn)中是可能的。
為了實(shí)現(xiàn) SiC 技術(shù)的效率提升,除了壓擺率和開關(guān)頻率的工作點(diǎn)相關(guān)調(diào)整之外,還必須軟件優(yōu)化及算法優(yōu)化進(jìn)一步提升系統(tǒng)效率。
審核編輯 :李倩
-
電動機(jī)
+關(guān)注
關(guān)注
75文章
4135瀏覽量
97500 -
逆變器
+關(guān)注
關(guān)注
289文章
4798瀏覽量
208616 -
SiC
+關(guān)注
關(guān)注
30文章
2985瀏覽量
63433 -
電驅(qū)系統(tǒng)
+關(guān)注
關(guān)注
0文章
116瀏覽量
2527
原文標(biāo)題:800V SiC電驅(qū)系統(tǒng)深度剖析
文章出處:【微信號:eng2mot,微信公眾號:汽車ECU開發(fā)】歡迎添加關(guān)注!文章轉(zhuǎn)載請注明出處。
發(fā)布評論請先 登錄
相關(guān)推薦
新能源船舶與儲能系統(tǒng)的新選擇:800V變400V變壓器
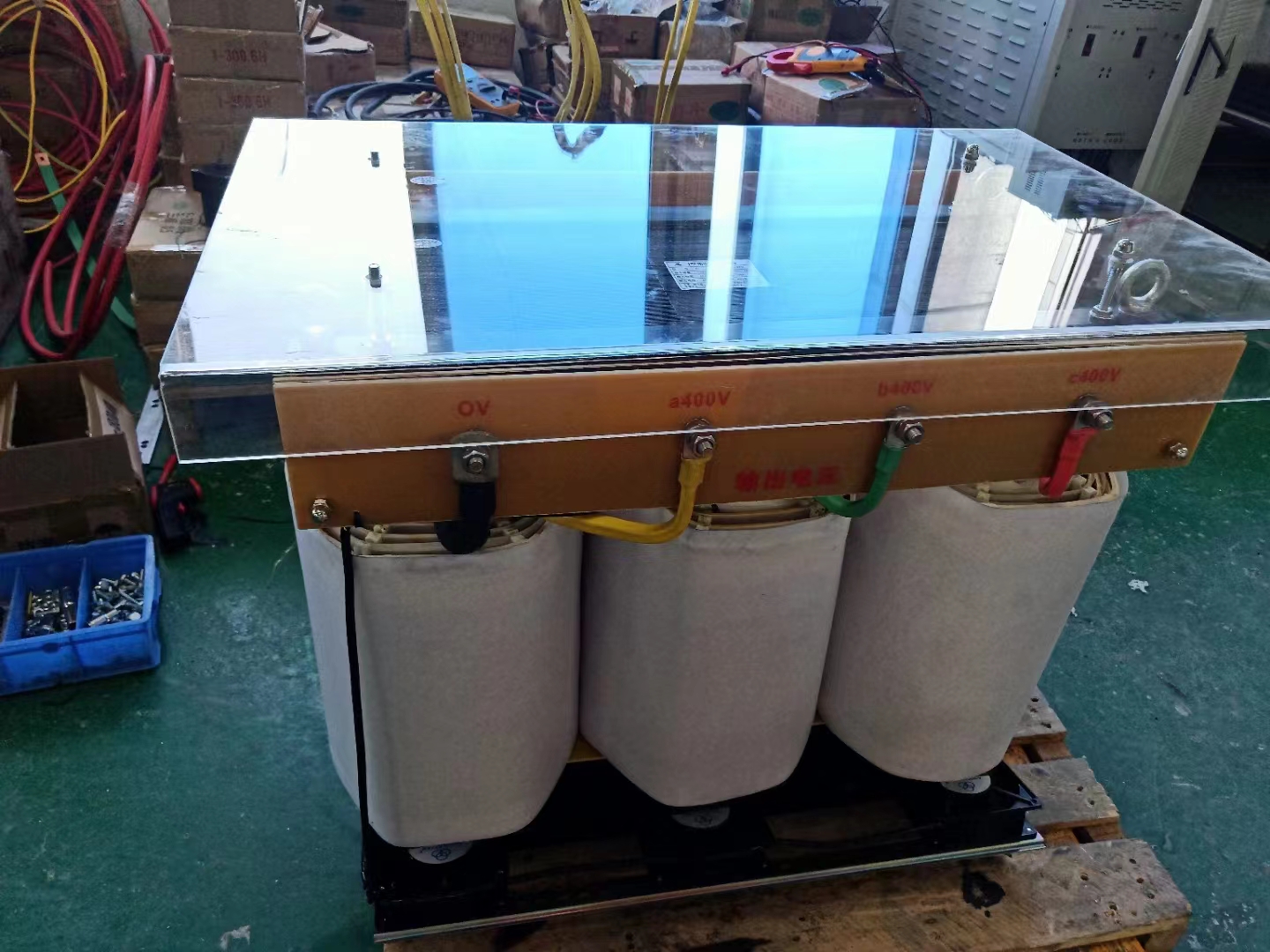
船舶電力革命:800V變400V變壓器的行業(yè)突破
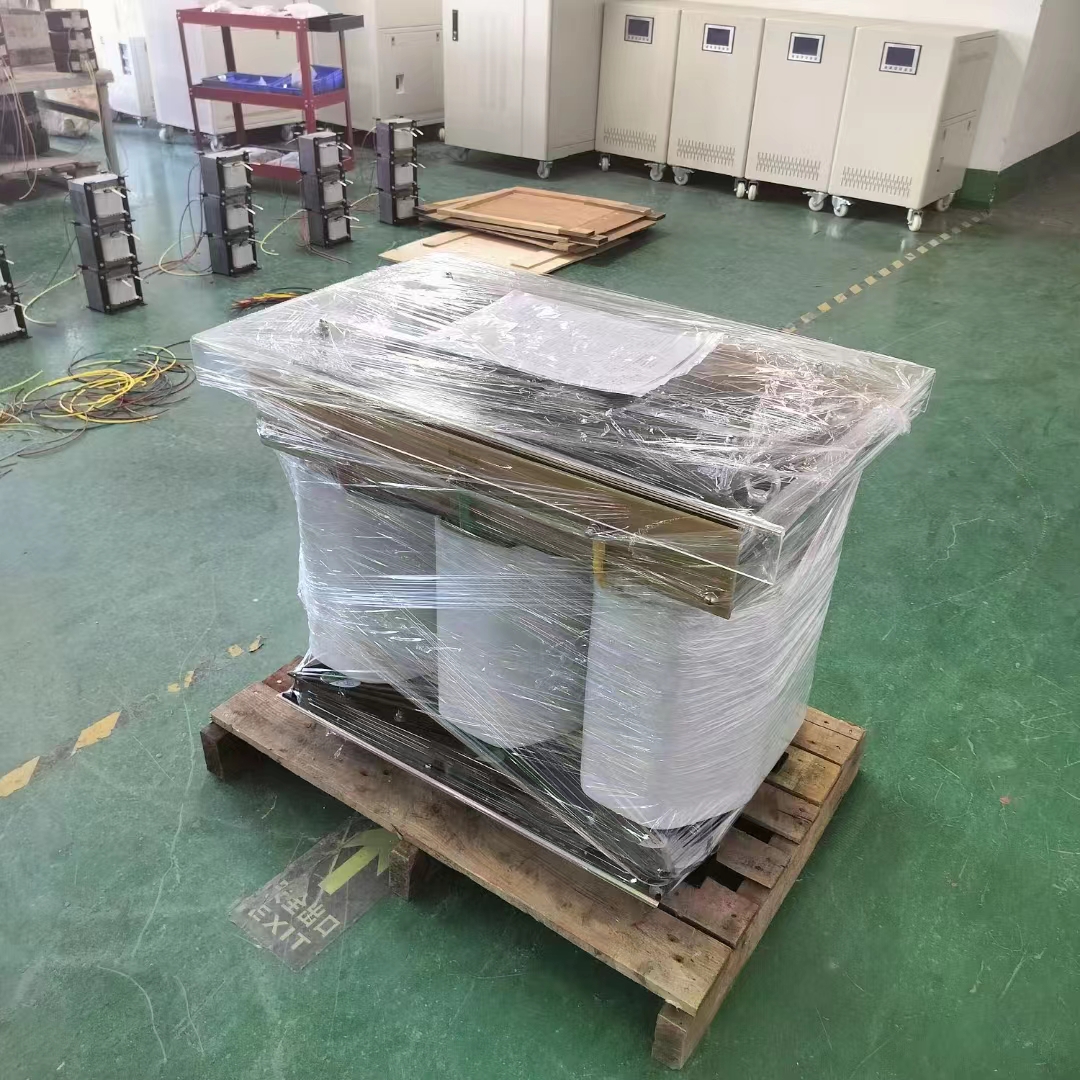
800V變400V變壓器:新能源船舶的“電力心臟”
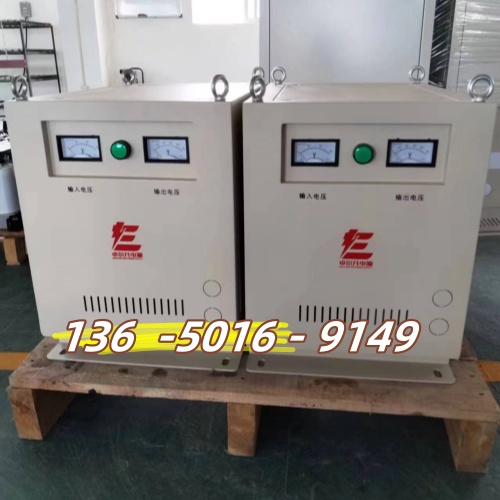
用于800V OBCM應(yīng)用的基于GaN和SiC的500kHz諧振雙向DC/DC設(shè)計(jì)
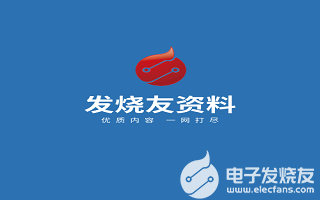
光伏發(fā)電自發(fā)自用 800V變400V變壓器 800KVA/1600KVA
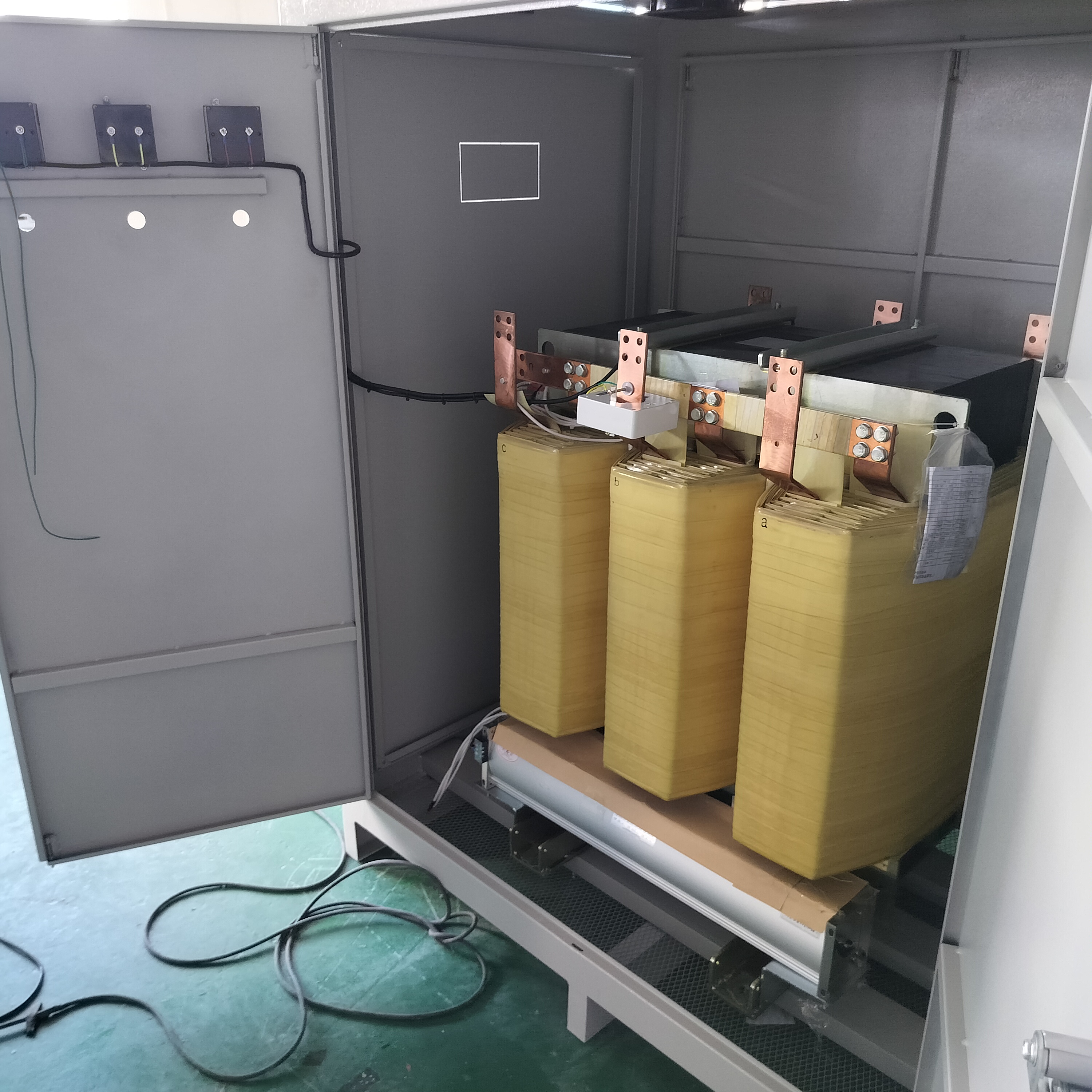
解密:400V變800V,升壓變壓器助您解決能源效率難題
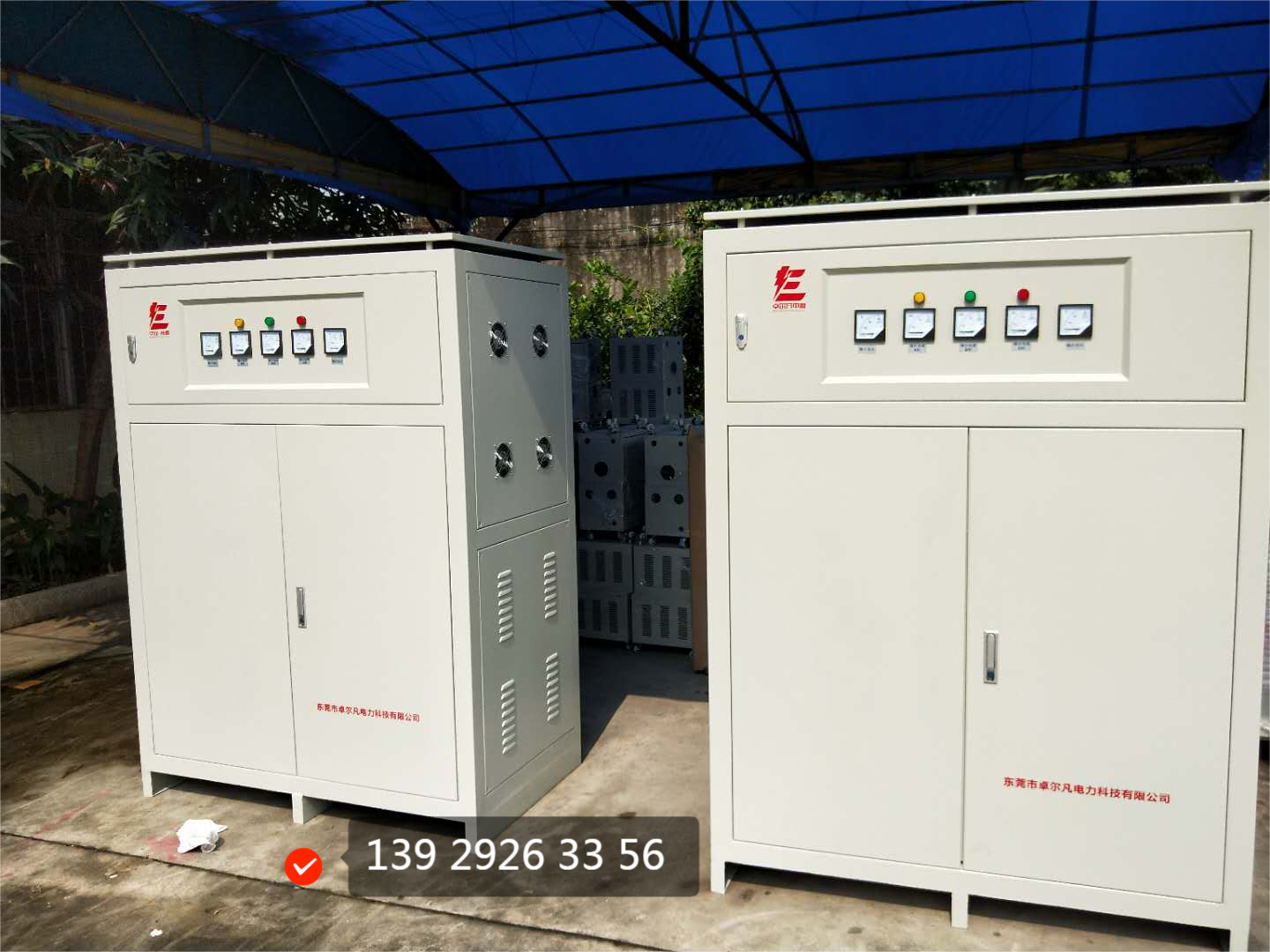
大型光伏電站變壓器800V變380V或800V變400V 提升光伏發(fā)電效能的必備裝備
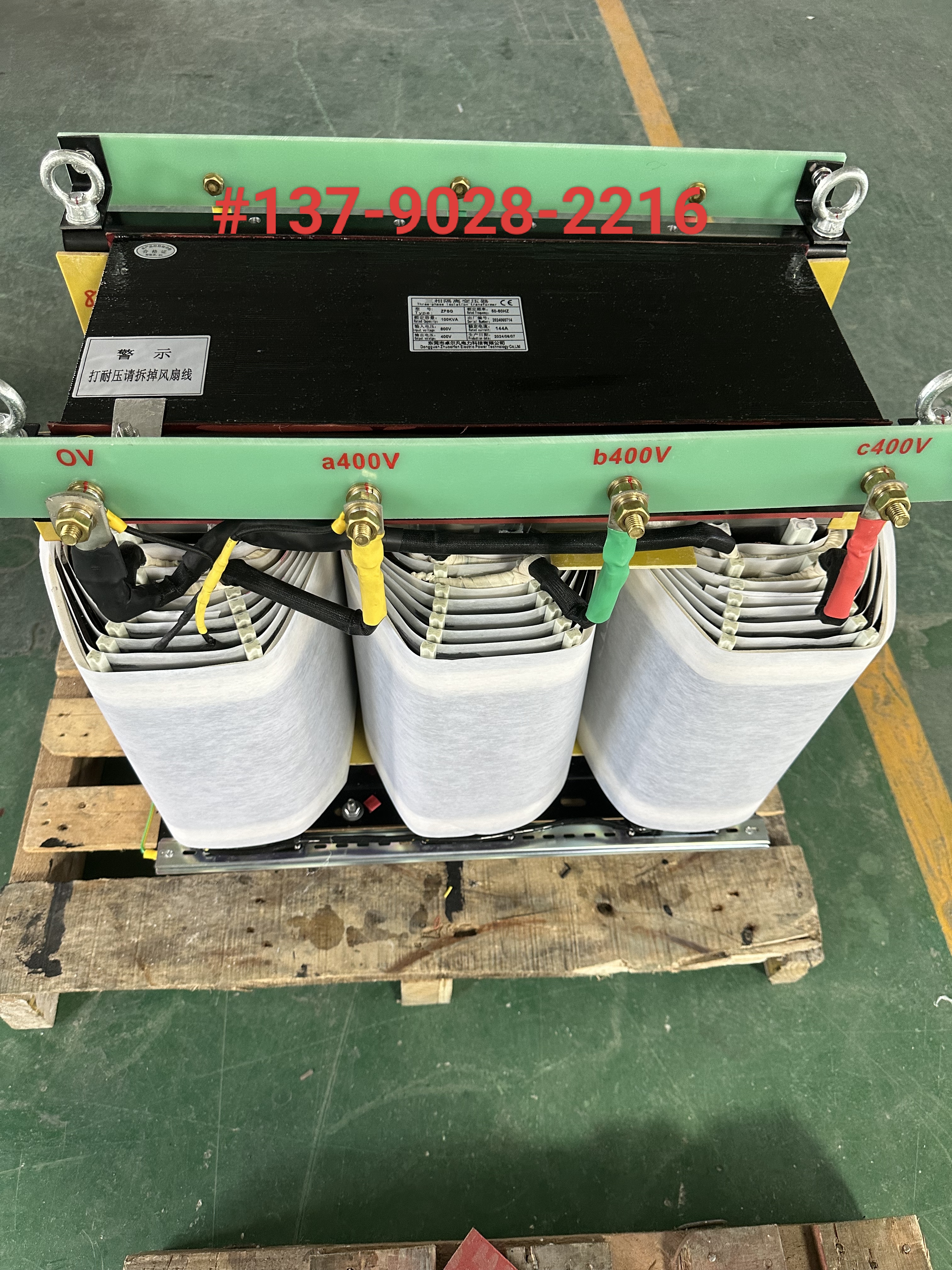
用于800V牽引逆變器的SiC MOSFET高密度輔助電源
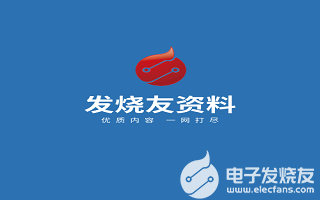
通過800V電池設(shè)計(jì)可靠的牽引逆變器冗余電源
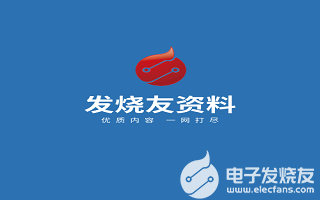
本土IDM廠商SiC MOSFET新進(jìn)展,將應(yīng)用于車載電驅(qū)
800V超充技術(shù)升級,SiC器件如何賦能?
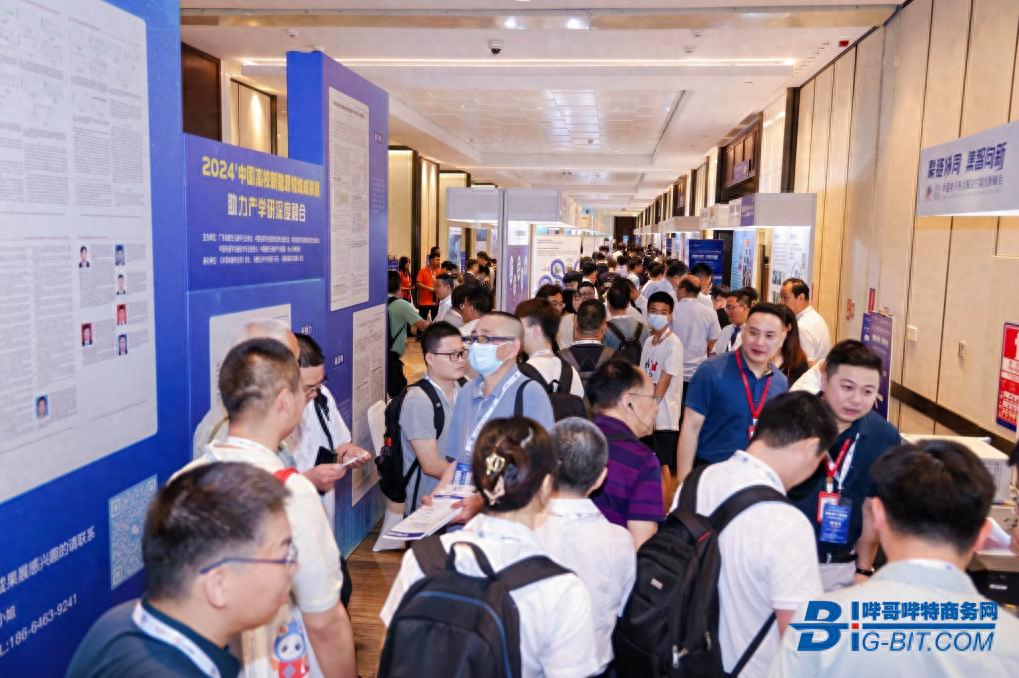
光儲系統(tǒng)高壓化升級,2000V SiC MOSFET開始走進(jìn)市場
宏微科技推出分別針對汽車800V平臺和增程式混動的兩款I(lǐng)GBT模塊
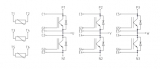
安森美SiC方案助力800V車型加速發(fā)布 解決補(bǔ)能焦慮
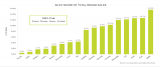
電動汽車采用800V電壓系統(tǒng)的原因解析
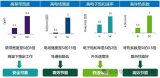
評論