摘要:
電子產品印刷電路板表面貼片安裝生產中,各種器件的逐漸走向微小化,不少生產線開始為檢測出合格的焊接質量設計了不少“關卡”,如現在廣為應用的三維檢測法。在電子器件組裝過程中,焊膏印刷效果對焊接質量有極大的影響,本文將簡單闡述焊膏印刷工藝當中的SMT技術以及焊膏印刷效果對焊接質量的影響,著重介紹焊膏印刷工藝中的三維檢測方法。
0引言
焊板印刷技術被廣泛應用在電路板的貼片工藝中,對焊膏印刷的檢測來說,現階段比較成熟的有AOI檢測技術、SPI錫膏測厚技術。焊膏印刷過程中,存在諸多因素,導致焊膏印刷效果參差不齊,其中涉及到焊膏的材料、印刷的工藝等,如何減輕、消除這些因素帶來的影響,成為焊膏印刷技術提升的重點。此外,在SPI錫膏測厚技術的加持下,能精確控制PCB板上焊膏的各項數值,提升焊膏引述的質量。三維檢測技術的發展,不僅從根本上提高了焊膏焊接產品的質量,把控產品的生產效率,更讓焊膏印刷技術有了質的飛躍。
1SMT技術
SMT技術(Surface Mounted Technology)在當下電子原件裝行工藝中是最為常見的工藝,簡單來說就是電子器件表面貼裝技術。在貼片組裝過程中,一般會將無引腳或短引線表面組裝元器件(簡稱SMC/SMD)安裝在印制電路板(Printed Circuit Board)的表面或其它基板的表面上,再通過回流焊焊接組裝,這就完成電子器件裝行的第一步。
SMT技術相比傳統的制作工藝,有很多獨到的特點。如組裝密度高,這就很好的呼應了現在行業標準對電子器件的要求。此外,電子器件體積小、占據空間小、質量小,這些特點,都是現在工藝所追求的標準。SMT技術隨著當下技術水平以及市場要求的變化,逐漸形成了了可靠性、生產效率高、產品性能強等特點,消除了以往抗振能力差、PCB焊點缺陷頻率高等缺點,減少了生產過程中電磁和射頻干擾。技術水平的提高意味著產品擁有了更多的可能性。
但是SMT技術并非沒有缺點,總的來說,具體有以下幾點。某些情況下,連接SMT在機械應力條件下不實用因素起作用,例如物理連接將頻繁附著和分離的地方。接頭尺寸有時也是SMT技術的缺點之一,由于SMT技術韋促進較小的組件進行連接,焊接連接較小,這導致每次接觸中使用的焊料量較少,可能會影響某些焊點的可靠性。高功率應用也是SMT技術的缺點之一,電路中需要大型元件的地方例如大電容或大型連接器,使用起來的功率較大,不能保證生產線上所有得到機器都能穩定運轉,存在一定的隱患。綜上所述,SMT技術在制造PCB電路板的工藝中,并不是最佳生產方案。
2焊膏印刷對焊接質量的影響
2.1材料的影響
焊膏的成分較為復雜,一般有焊料合金顆粒、助焊劑、粘度控制劑、溶劑等;在其他不同種類的焊膏中,成分也不盡相同,造成焊膏最終的品質也不同。
2.1.1焊膏的粘度
焊膏粘度過大時,焊盤上的線條會出現少、缺等現象;粘度太低,線條容易脫落且不平整,分辨率也大大降低。這兩種情況都會造成產品生產不合格,會影響生產的效率。
2.1.2焊膏顆粒的大小與其均勻性
焊盤上高清晰度的印條意味著焊膏顆粒直徑較小,但是焊膏顆粒直徑取極小的情況下,印條就會出現塌邊、易氧化等現象;反之焊膏顆粒過大,則會造成印條模糊不清、印刷不均勻等情況。
2.1.3焊膏中的金屬含量
焊膏中的金屬含量能有效增加回流焊厚度,當焊膏中的金屬含量過低時,焊料的橋連傾向會降低,造成產品生產不合格。
2.2網板的影響
網板的材料以及刻制都會影響焊膏印刷質量,能最終決定焊膏印刷的精密度。網板上的開孔尺寸,過大過小都會與對應焊盤不吻合,導致印刷過程無法進行下去。網板的厚度,要根據相關的引線間距來決定,一般情況下采用0.12~0.15mm的網板,網板厚度過小,則不利于焊膏的釋放。
2.3絲印機參數的影響
2.3.1刮刀壓力
該處壓力應盡量降低,這樣焊膏才能完全附著在焊盤上,達到工藝標準。操作不標準,壓力太大,焊膏就不能完全印在焊盤上,會過分進入絲網模板開口處,甚至會擠入焊盤的縫隙當中。
2.3.2印刷速度
該處速度要適當控制,一般來說要低于30mm/s。若速度過快,焊膏就不能很好的填充在絲網模板的開口處。
2.3.3刮刀材料
一般來說,現在生產過程中所采用的都是材質較為軟的橡膠刮板,若刮刀軟硬不合格如硬度過大,會導致絲網模板變形。
2.4焊膏印刷產生不良效果的原因
焊膏在印刷過程中經常會因為一些因素而產生印刷不良等效果。最為常見的有印刷位置發生偏離,在印刷過程中,模板跟PCB的位置沒有完全對準,當然也存在模板制作工藝水準不達標等因素。若焊膏印刷填充量存在不足,說明焊膏的量本身就存在量少等問題;焊膏量少的情況下,會出現未填充、缺焊、少焊等生產故障。焊膏填充量不達標準不僅直接對電子器件的組裝有影響,也會間接影響到印刷板的壓力、刮刀速度等。
3焊膏印刷對焊接質量的影響解決方案
3.1對焊膏材料
焊膏的粘度:在選用不同粘度的焊膏時,可用精確粘度儀進行測量。
焊膏顆粒的大小與其均勻性:根據實際情況,按照引腳間距和焊料顆粒的關系,選定合適的焊料顆粒直徑。
焊膏中的金屬含量:在焊膏厚度一定時,可參照金屬含量對回流焊厚度的影響參數,進行設定。
3.2對網板
網板材料及開孔、厚度、開孔方向與尺寸的選擇,需要根據實際焊盤的參數以及生產設計要求來選擇。在網板材料的設計生產工藝當中,則可以根據相關的設計標準來設計生產。
3.3對絲印機相關參數
刮刀壓力與刮刀材料:適當控制刮刀壓力,就需要采用軟硬適中的材料,如較硬的刮刀或者金屬材料的刮刀。
印刷速度:在具體的生產過程中,也要結合實際狀況來設置刮刀壓力跟速度的具體數值。
4SPI錫膏測厚技術
4.1SPI錫膏測厚技術原理
SPI(SolderPaste Inspection)的全稱是錫膏檢測系統,SPI錫膏測厚儀的設計原理中運用到了激光非接觸三維掃描密集取樣技術,這個設備能將PCB板上的錫膏的面積體積以及具體的厚度逐個測量出來,大大完善了原有的檢測系統,收集的數據更加真實、完全、可靠。近幾年來這款設備在SMT生產鏈中備受關注,作為生產環節中的核心檢測步驟,SPI錫膏測厚技術不僅做到精準測量PCB板上焊膏的面積體積以及具體的厚度,更能結合控制軟件(SPC)對上述測量數據進行統計分析,用更加直觀的圖表形式來體現制作工藝中不穩定因素是否存在,起到一個預警、提前預知未知錯誤的作用,更好的優化產品。
在SPI錫膏測厚儀中,研發者巧妙的運用了PMP(相位調制輪廓測量技術)以及Laser(激光三角測量技術),在這兩個技術的融合下,SPI錫膏測厚儀能輕易的測出各種細小的焊膏的相關數據。
4.2激光三角測量技術
激光三角測量技術利用相機拍下光束在不同時間內在焊膏上圖像,后期整理出相關數據,進行統計計算,最終就能得出該焊膏的相關數據,得出測量結果。在這里,由于激光三角測量技術中巧妙的用到了激光,而激光能在高低不同的平面上產生畸變,照相機才能捕捉到畸變數據。
激光三角測量技術優缺點非常明顯,優點就是能在很短的時間內對大量的PCB板進行檢測,生產效率高;缺點則比較多,首先是激光束分辨率只能控制在10 - 20um級,分辨率較為單一;其次機器在執行過程中只能單次的檢測,導致數據的重復性精確度不是很高;由于激光束的運動模式容易受外界的影響,所以在外界有干擾的情況下,實驗所測得的數據準確性較低。
4.3相位調制輪廓測量技術
如果說激光三角測量技術有不小的缺陷,那么相位調制輪廓測量技術就很好的能填補激光三角測量技術的漏洞。由于使用白色光源,相位調制輪廓測量技術能利用結構光柵在PCB板上的相位變化,得出焊膏的相關數據,彌補了激光束測量的不足;利用結構光柵在PCB板上的灰度變化,能夠得出數據更加精確的高度值;此外,還能對PCB板進行多次測量、采樣,重復性測量得到更高精度的高度值,彌補了激光三角測量技術易受外界干擾了缺陷。
從上述描述來看,相位調制輪廓測量技術優點不少,首先就是很好的削減了外界的不穩定因素,比如震動,大大提高了機器的穩定性;還能有效的進行多次測量,提高了重復性精度。
4.4錫膏測厚儀3D技術方案
(1)激光測量,錫膏測量精度達到納米級,有效分辨率56nm(0.056um)。
(2)高重復精度(0.5um),人為誤差小,GRR高。
(3)數字影像傳輸:抗干擾,自動糾錯,準確度高。
(4)高分辨率圖像采集:有效像素高達彩色400萬像素。
(5)高取樣密度:每平方毫米上萬點(平均每顆錫球達6~20取樣點)。
(6)多點基板扭曲修正功能:不但可以修正傾斜,還可以修正扭曲變形。
從這些相互影響的不確定參數中,如何找出問題?這里就會利用帶SPI獨特的能力了,在印刷時能讓操作人員簡單明了地理解當前印刷的結果。在控制印刷工藝中,印刷轉移效率(TE)的百分比以及焊膏沉積的標準差是每個人都會關心的問題。一般情況下下,實際體積(Measured Volume) 和目標體積(Target Volume)的百分比能決定印刷質量的優與劣,控制產品相關參數在合適的范圍內一定程度上也能決定產品最后的效果。
5結語
三維檢測技術不僅提供了新的檢測方案,還能通過測量焊盤上焊膏的體積來保證回流后焊點的可靠性,這一點在高端電子產品的SMT生產線中得到了充分的驗證。SPI技術不是簡簡單單控制印刷機的,而是在印刷機中找尋最合適的生產模式,使得產品的質量得到了把控。從生產效率上來看,三維檢測技術是產品質量水準的閥門,從生產工藝上來看,能夠改變原有的生產模式,實現工藝管控。
-
焊接
+關注
關注
38文章
3168瀏覽量
59881 -
smt
+關注
關注
40文章
2910瀏覽量
69392 -
焊膏
+關注
關注
0文章
43瀏覽量
10398
原文標題:焊膏印刷效果對焊接質量的影響與三維檢測方法
文章出處:【微信號:半導體封裝工程師之家,微信公眾號:半導體封裝工程師之家】歡迎添加關注!文章轉載請注明出處。
發布評論請先 登錄
相關推薦
焊接方法對焊接質量的影響
SMT貼片工藝中錫膏印刷的關鍵細節及優化策略
詳解錫膏印刷對回流焊接的影響
手焊、回流焊和波峰焊三種焊接方法,怎樣操作才能保證SIM卡座的質量
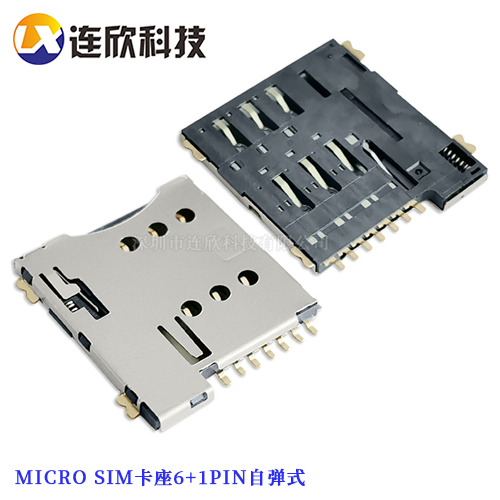
常見的影響錫膏印刷質量的因素有哪些?
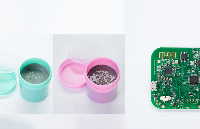
評論