摘 要:為了穩步推進雙碳目標,在能源消費強度和消費總量的“雙控”背景下,企業需要考慮如何應對能耗雙控以保障正常生產。現有大部分企業依然采用電、水、氣、冷、熱等各種能源供應系統“單獨規劃、單獨設計、獨立運行”的模式。普遍存在計量檢測到配備不足;計量設備計量精度不高、計量數據不準確;人工抄表可靠性低;難以合理監測和評估主要耗能設備的用能效率;缺少決策數據支持,對于節能評估無法提供可靠參考數據;缺乏合理的企業能效評估指標體系,能耗管理措施難以落地等情況。本文介紹的企業能源管控平臺,采用自動化、信息化技術,實現從能源數據采集、過程監控、能源介質消耗分析、能耗管理等全過程的自動化、合理化、科學化管理,使能源管理、能源生產以及使用的全過程結合起來,運用良好的數據處理與分析技術,進行離線生產分析與管理,實現全廠能源系統的統一調度,優化能源介質平衡、合理利用能源,提高能源質量、降低能源消耗,達到節能降耗和提升整體能源管理水平的目的。
關鍵詞:雙碳;雙控;企業能源管控;節能降耗
1 概述
工業企業內部情況復雜,子系統眾多,根據企業定制開發對接這些子系統周期長,靈活度差。所以我司針對這個情況,開發了工業物聯網組態平臺,解決了各種子系統,第三方儀表接入展示困難,靈活度差的問題。
2.應用案例介紹
案例一 浙江春風動力股份有限公司
項目概況
計量體系分為廠區、車間、產線,監測區域涵蓋車架、發動機、機加工、涂裝、整車等車間,行政樓、研發樓等辦公樓以及各配電房。監測的能源類型包括電、水、天然氣和壓縮空氣。項目一期接入170塊電表和10塊水表,二期接入80塊電表和3塊水表,三期接入300個點位。
企業痛點
人工抄表費時費力 管理者不了解工廠的用能狀況,無法進行有效調控 萬元產值能耗、容需量電費、電費分攤等統計困難,工作量大 用能異常無法及時警示,造成用能浪費 設備運行無法實時監測,延誤處理時機 各類系統多且獨立,無法做到數據共享,統一管理
解決方案
實現自動抄表、統計報表、異常告警等功能,降低人力成本,每個月節省75個工時。
在線監測諧波含量和三項不平衡度,保證用電質量,避免精密儀器產生故障或損壞,減少用戶損失。
24小時預警告警,及時發現和定位故障節點,通過多種方式快速提醒相關人員干預切除,保證能源供應安全。
提供容需量電費統計,幫助企業降低基本電費。為調整負載、削峰填谷、無功補償等節能改造提供數據支持。
案例二 某鋁制品公司
項目概況
監測區域涵蓋化一車間、化二車間、腐蝕車間、純水車間、預處理車間、高溫純水車間等主要車間及其他剩余各車間。監測的能源種類包括電和水,總計接入332塊電表、140塊水表、若干原有水表及若干原有的智能設備。
企業痛點
無法實時掌握電、水的使用情況
無法實時了解配電系統及設備的運行狀態,異常處理不及時
缺乏精準量化的數據,無法量化能耗考核對象的績效,人工統計困難,工作量大
無法及時發現能量在使用過程中的跑冒滴漏和異常用能等問題,存在能源使用浪費的情況
無法計算產品的單位能耗,生產成本偏高 無法對核心數據進行有效的安全管控
解決方案
實現分車間的能源績效評定,為KPI考核提供數據支持。
提供電、水的消耗量及對應的費用數據,了解整個企業能源費用成本的詳細分布情況。
自動記錄平臺用戶登錄和操作記錄,對核心數據的權限進行管控,確保核心數據安全不泄露。
全面掌握產品單位成本,為改善工藝提供依據,結合節能改造的實施,實現單耗下降約8%。
3 系統應用價值
3D可視化建模展示系統的出現,大幅度提高了工廠可視化、數字化水平,其集中工廠的特性更合理低增強了工廠管理與維護的能力。從而大大提升了工廠交互效率,降低工廠信息損耗和時間損耗,確保信息傳遞的準確性和及時性,降低了信息查詢和瀏覽的難度,使運維管理人員能夠大幅度提升工廠操控管理效率,加速相應速度,縮短處理時間。
4 結語
安科瑞企業能源管控平臺采用自動化、信息化技術和集中管理模式,對企業的生產、輸配和消耗環節實行集中扁平化的動態監控和數據化管理,監測企業電、水、燃氣、蒸汽及壓縮空氣等各類能源的消耗情況,通過數據分析、挖掘和趨勢分析,幫助企業針對各種能源需求及用能情況、能源質量、產品能源單耗、各工序能耗、重大能耗設備的能源利用情況等進行能耗統計、同環比分析、能源成本分析、用能預測、碳排分析,為企業調整負載、調整負荷率、削峰填谷、無功補償、更新設備提供基礎數據和支持,幫助企業加強能源管理、提高設備運行效率和能源利用效率、保證設備經濟運行、挖掘節能潛力,成本低,回收期短,經濟效益明顯,不僅可以提高企業的核心競爭力,同時是保護環境和社會可持續發展的基礎和源泉,積木及響應國家對于節能降耗的政策。
審核編輯黃昊宇
-
能源管控
+關注
關注
0文章
63瀏覽量
9012
發布評論請先 登錄
相關推薦
安科瑞能耗在線監測系統助力雙碳應用
新能源光伏工廠的安全防線——安科瑞母線槽紅外測溫上線
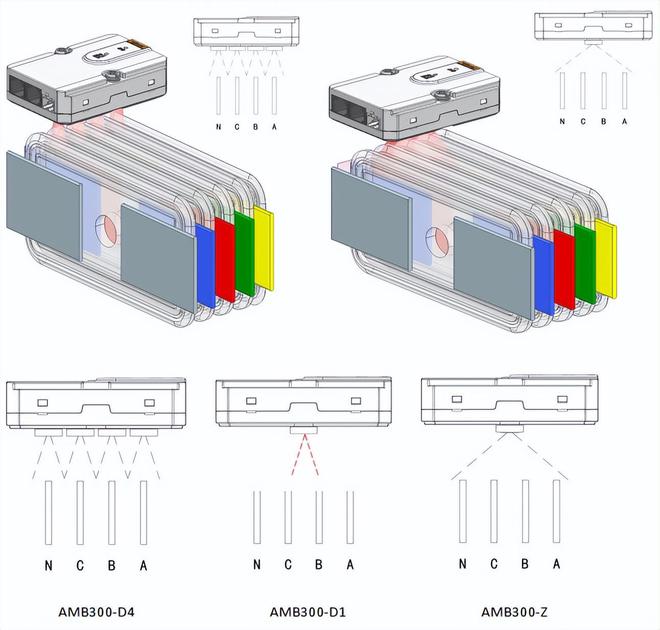
安科瑞企業能源管控平臺在石化行業的應用
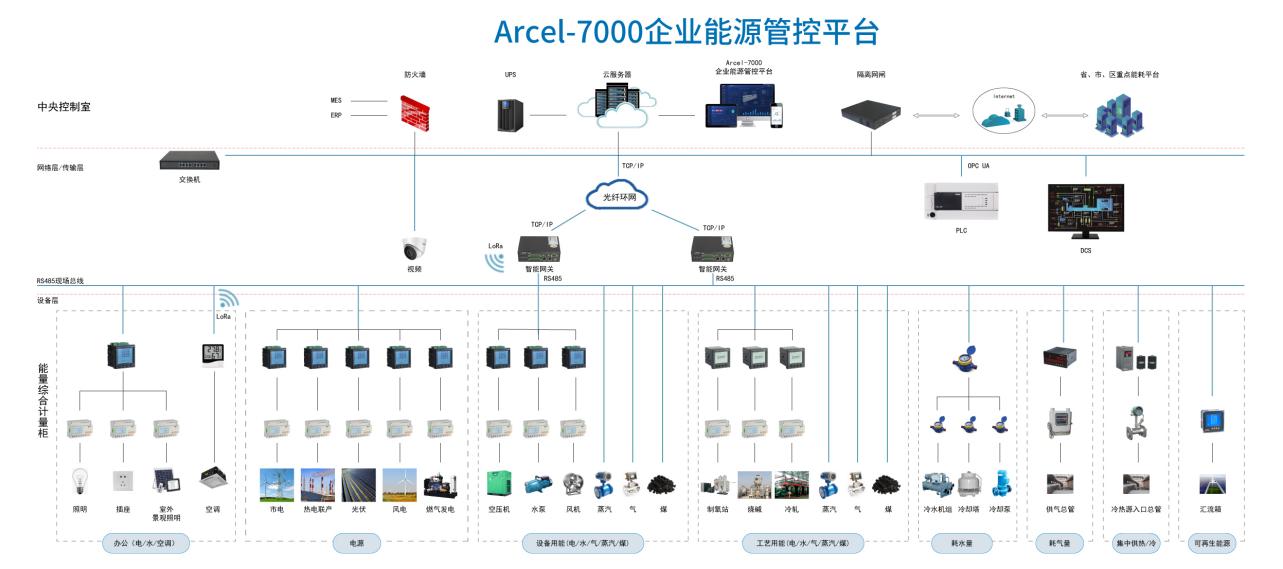
評論