摘 要
Abstract
本文介紹了基于印刷方式下的微孔填充工藝的HTCC金屬化技術, 詳細介紹了印刷填孔工藝在HTCC金屬化的應用及國內印刷填孔設備。并將此印刷填孔工藝廣泛應用于HTCC行業的陶瓷金屬化, 取得了很好的實際應用效果。
0 引 言
高溫共燒陶瓷 (High Temperature co-fired Ceramic, HTCC) 是一種采用材料為鎢、鉬、錳等高熔點金屬發熱電阻漿料, 按照發熱電路設計的要求印刷于92%~96%的氧化鋁流延陶瓷生坯上, 并通過4%~8%的燒結助劑多層疊合, 在1 500~1 600℃的高溫下共燒成一體的多層陶瓷制造技術。具有耐腐蝕、耐高溫、壽命長、高效節能、溫度均勻、導熱性能良好、熱補償速度快等優點, 而且不含鉛、鎘、汞、六價鉻、多溴聯苯、多溴二苯醚等有害物質, 符合歐盟RoHS等環保要求。
因燒結溫度高, HTCC不能采用金、銀、銅等低熔點金屬材料, 必須采用鎢、鉬、錳等難熔金屬材料, 這些材料電導率低, 會造成信號延遲等缺陷, 所以不適合做高速或高頻微組裝電路的基板。但是, 由于HTCC基板具有結構強度高、熱導率高、化學穩定性好和布線密度高等優點, 因此在大功率微組裝電路中具有廣泛的應用前景。
印刷填孔過程是陶瓷金屬化及片式元件行業生產工藝流程中的重要環節之一, 近幾年隨著HTCC技術在電子、通訊、汽車、計算機和醫療等領域的廣泛應用, 精密印刷填孔設備在國內也得到了大力發展。圖1為典型的HTCC基板示意圖, 由此可知采用HTCC工藝制作的基板具有可實現集成電路芯片封裝、內埋置無源元件及高密度電路組裝的功能。
圖1 HTCC基板示意圖
1 HTCC技術工藝流程
HTCC與LTCC技術工藝流程非常相似, 典型的HTCC生產工藝流程包括漿料制備→流延成膜→切片→打孔→微孔填充→印制電極→印制無源元件→單層檢測→疊片→熱壓→切片 (批量生產) →排膠燒結→產品檢測等過程, 圖2為HTCC基板制造的工藝示意圖。
圖2 HTCC生產工藝示意圖
陶瓷的金屬化包括單層的表面金屬化和層與層間的金屬化。單層陶瓷的金屬化, 是在陶瓷表面牢固地粘附一層金屬薄膜, 使之實現陶瓷和金屬間的焊接, 在陶瓷表面形成電路, 不僅可以焊接, 而且能夠作為導線傳輸電流, 這種工藝采用印刷的方法。
HTCC多層基板互連通孔是通過微孔填充的方法形成的, 主要是對打孔后的生瓷片通孔完成金屬漿料填充, 達到電氣互聯導通目的, 最近幾年新開發的一種工藝是在在微孔中注漿并抽空心, 形成空心孔。實心孔與空心孔本質是實現層與層之間的連接的方式, 目前已經處于實際應用階段。
本文著重介紹在HTCC金屬化方面應用廣泛的微孔填充工藝, 并介紹填孔工藝的國內相關設備。
2 填孔工藝在HTCC金屬化的應用
2.1 填孔工藝
通孔填充是HTCC技術的關鍵工藝之一, 陶瓷基片層與層之間的連接填孔工藝, 即微孔填充工藝, 之前多采用擠壓方式, 由于經過長時間的擠壓作用, 漿料中的有機溶劑會大量揮發, 導致漿料粘度不斷增大, 觸變性變差, 填孔變得越來越難, 而且精度差、效率低, 這種工藝目前基本被淘汰。
LTCC微孔填充多采用印刷填孔的方式, 通過刮刀的運動將漿料壓入微孔中, 如圖3所示。填孔工作臺是采用多孔陶瓷, 工作時工作臺下面用真空機抽成負壓, 且在工作臺和填孔基片之間放一張濾紙, 防止金屬漿料從通孔漏到工作臺上。填孔絲網網版一般采用不銹鋼制作, 網版上的孔徑應略小于生瓷帶上通孔的孔徑, 這樣可提高盲孔的形成率。
圖3 LTCC填孔過程示意圖
在實際生產過程中填孔壓力根據漿料的種類和基板厚度不同, 所需壓力也不相同。在LTCC領域, 目前常規生瓷片的厚度為0.127 mm, 采用的漿料為銀漿, 黏度為2 800 Pa·s, 黏度值相對較低, 需要的填孔壓力在100~200 N之間, 采用印刷的方式可以完成。隨著基板厚度增加, 就需要更大的填孔壓力, 基板厚度與填孔直徑之比小于1.2時工藝性較好, 如果大于1.2, 工藝性就變差, 且填孔壓力隨之增加, 因此填孔設備需兼容不同厚度基板, 并適應不同黏度的填充漿料。
2.2 HTCC印刷填孔工藝及相關設備
在HTCC技術領域, 由于所采用的漿料大部分為熔點很高的鎢漿, 漿料黏度變為10 000 Pa·s以上, 黏度很高, 采用印刷的方式需要很高的壓力。同樣以0.127 mm厚度為例, 印刷壓力則達到1 000 N, 這就需要特殊的填孔機。
填孔的原理如圖4所示, 在刮刀向右運動時帶動漿料向右運動, 同時刮刀的壓力施加于漏板, 將漿料以很大壓力壓入漏板的孔中, 多孔陶瓷臺通過透氣紙從生瓷片底部抽真空, 有助于漿料填充在整個微孔的圓柱空腔里。下面的板從上到下依次為漏板、生瓷片、透氣紙及多孔陶瓷臺。
圖4 HTCC填孔過程示意圖
影響HTCC印刷填孔質量的主要因素是, 除填孔設備滿足產品所需的技術指標要求外, 影響填孔質量的主要工藝參數有填孔壓力與速度、刮刀角度與硬度以及真空負壓與拖網延時等。
2.2.1 填孔壓力與速度 微孔填充過程中, 如果使用填孔漿料黏度較大, 一般對應的填孔壓力可達600 N以上, 填孔速度一般在20~50 mm/s之間, 并且保證基片通孔被擠壓填滿后邊沿漿料外邊沒有滲漏。而如果壓力太小或速度太快可能會導致所填基片通孔內部不飽滿, 燒結后影響導通效果。 2.2.2刮刀角度與硬度 在印刷填孔過程中刮刀角度如圖4所示, 且填孔刮刀的硬度一般為肖氏硬度70~90。 2.2.3 真空負壓與脫網延時
在基片填孔過程中多采用多孔陶瓷作為工作臺面, 這樣盡量保證真空負壓均勻, 而真空負壓的大小主要取決于所用漿料的黏度以及臺面紙的透氣性, 如果真空負壓太大會使填到基片通孔中的漿料被吸掉很大一部分, 導致填孔正面塌陷;如果真空負壓太小, 會使填孔底面漿料不夠飽滿;拖網延時也是影響填孔效果的一個重要參數, 拖網太快可能會導致所填漿料被帶出一部分, 一般大于1 s。
國內生產的填孔設備已達到國際先進水平, 完全滿足目前國內填孔工藝的要求。圖5為國內HTCC行業的某主流品牌自動對準填孔設備。采用印刷填孔的方式主要具有以下優點:
(1) 對準精度高;采用兩個高分辨率的CCD相機識別位置, 配以高精度三維運動工作臺校正位置, 對準精度可達10μm。以目前的填孔工藝, 最小孔徑準75μm, 可滿足定位要求。
(2) 填孔壓力大小精密可調;采用比例閥和精密減壓閥相結合的方式調節填孔壓力, 壓力精度可到1 N。
(3) 填孔精度高;采用平面度高及透氣性好的陶瓷工作臺吸附生瓷片, 工作臺與漏板的平行度優于30μm, 保證填孔的一致性。
(4) 效率高;采用自動上、下料的模式, 實現了自動化生產, 提高了效率。
圖5 TY-360型自動對準填孔機
目前主流工藝中HTCC組件微孔填充的孔徑大小都在準100μm, 而未來幾年主流工藝微孔填充大小在準30~50μm以內, 孔徑變化趨勢越來越小, 要求設備的印刷壓力越來越大 (1 200 N) 。
圖6為HTCC基片填孔的效果圖。填孔孔徑準75μm, 壓力1 000 N, 采用0.127 mm厚度的生瓷片。
圖6 HTCC基片孔徑準75μm放大30倍圖
3 結 論
文中介紹了基于印刷方式下的微孔填充工藝的HTCC金屬化技術, 詳細介紹了印刷填孔工藝在HTCC金屬化的應用及國內印刷設備。并將此印刷填孔工藝廣泛應用于HTCC行業的陶瓷金屬化, 取得了很好的實際應用效果。
審核編輯 :李倩
-
電路設計
+關注
關注
6673文章
2451瀏覽量
204167 -
熱導率
+關注
關注
0文章
41瀏覽量
9268
原文標題:微孔填充工藝在HTCC金屬化方面的研究
文章出處:【微信號:中科聚智,微信公眾號:中科聚智】歡迎添加關注!文章轉載請注明出處。
發布評論請先 登錄
相關推薦
無鉛共晶焊料在厚Cu凸點下金屬化層上的潤濕反應
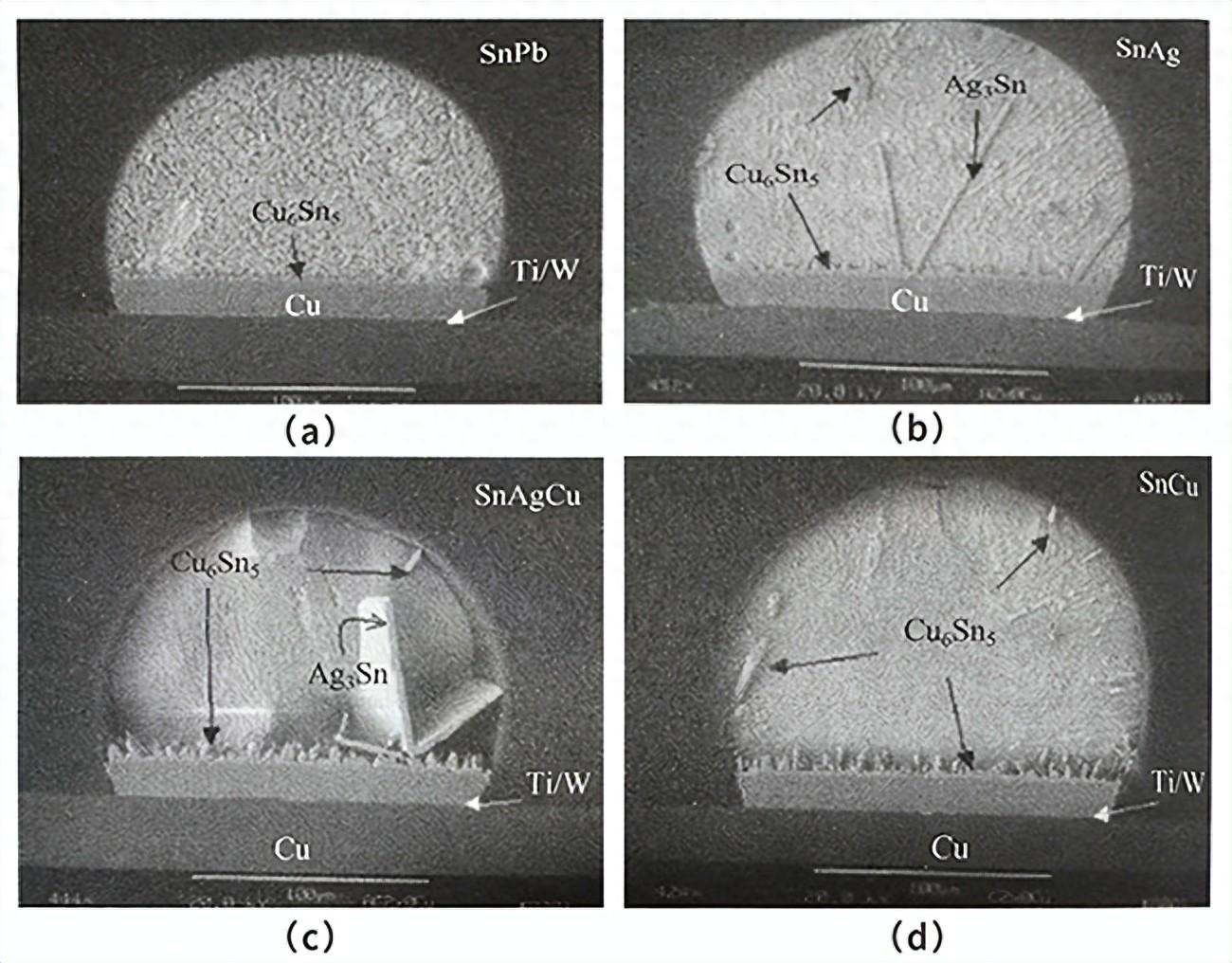
轉移效率和回流曲線對印刷錫膏的影響?
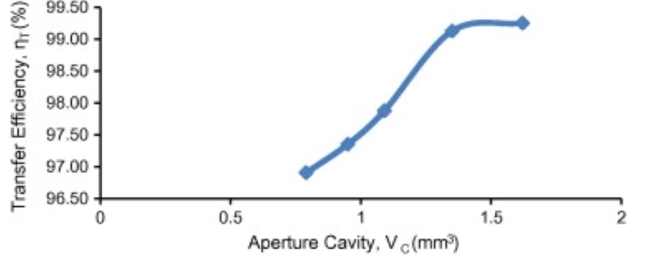
金屬化薄膜電容氧化時方阻會變大嗎
底部填充工藝在倒裝芯片上的應用
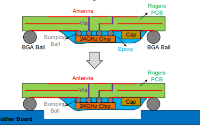
詳解點膠工藝用途和具體要求?
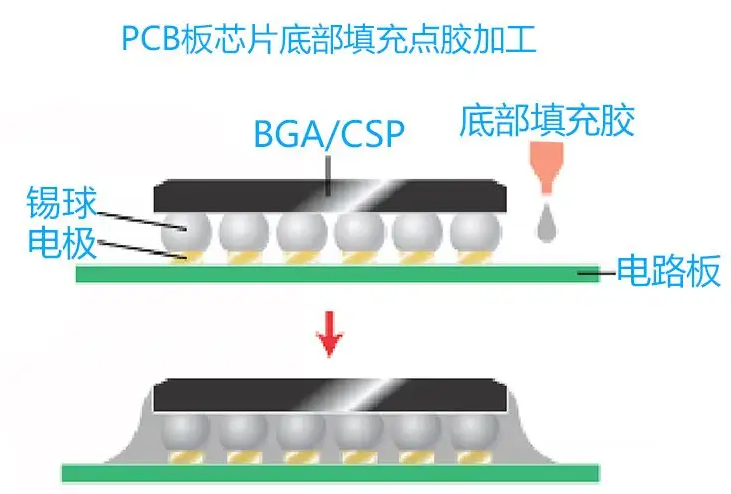
CBB金屬化薄膜電容存在失效問題嗎?
17芯航空插頭為什么要金屬化
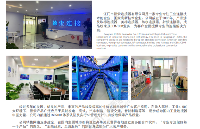
C82和C84也是雙面金屬化聚丙烯薄膜電容?和MMKP82電容有什么區別?
絲網印刷在金屬線路板上的應用——上
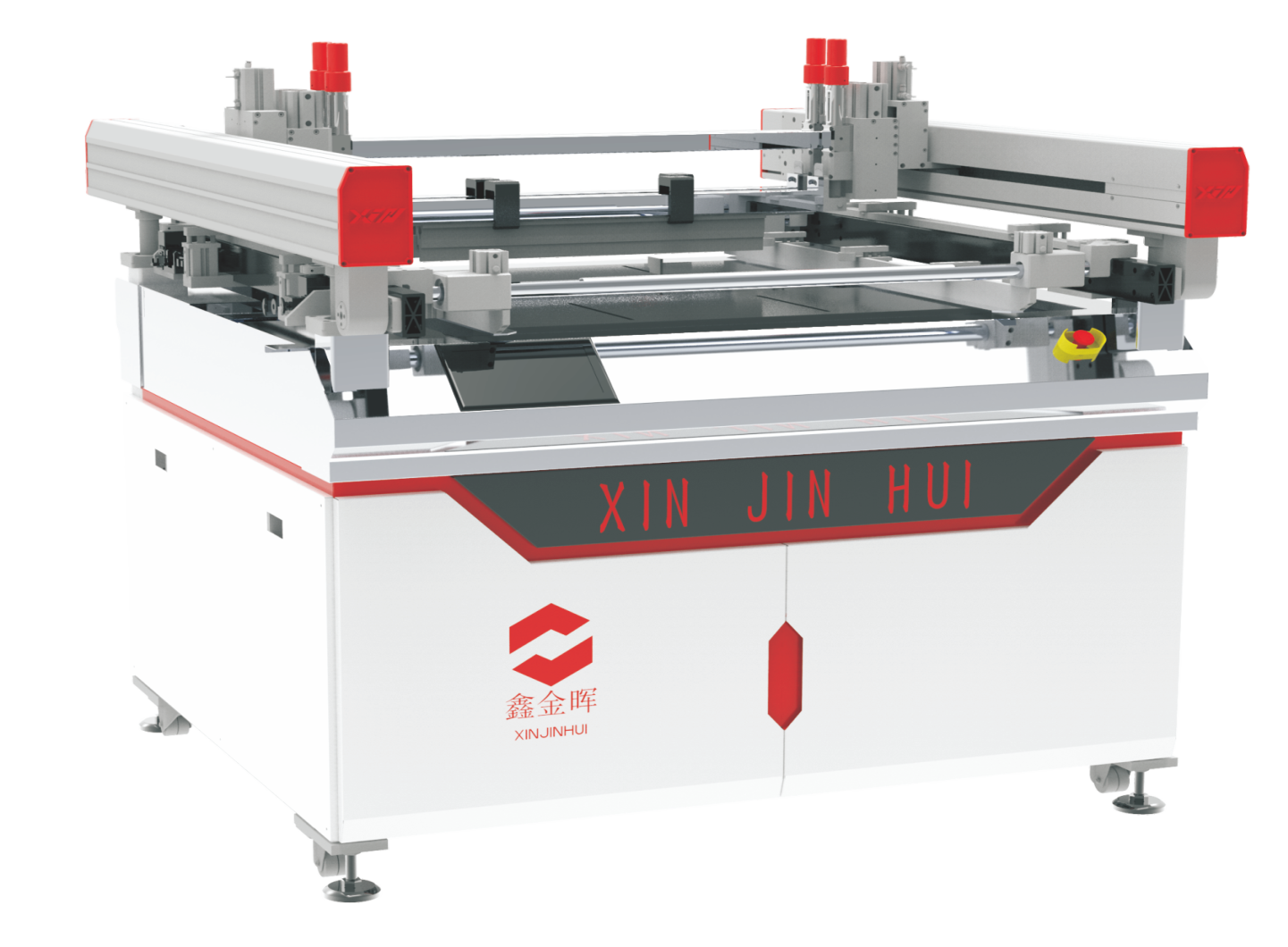
先進封裝表面金屬化研究
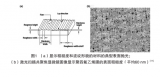
評論