本應用筆記探討了在實施工業(yè)4.0所需的基礎設施之前需要解決的各種系統(tǒng)設計障礙,并探討了一些關鍵的系統(tǒng)挑戰(zhàn)。
介紹
自動化行業(yè)的每個人都聽說過“工業(yè)4.0”的流行語,這是2011年在漢諾威博覽會上首次創(chuàng)造的短語。這種工業(yè)概念設想未來的工廠將更加集成化、自動化和靈活。更快、更高效,他們將生產(chǎn)出不斷變化的市場所需的商品。
工業(yè)4.0,顧名思義,意味著我們已經(jīng)經(jīng)歷了三次工業(yè)革命,并且正處于第四次工業(yè)革命的風口浪尖(圖1)。1
圖1.回顧最近一段時間,我們可以確定工業(yè)自動化發(fā)展的四個不同的關鍵時刻。圖形來源是DFKI。
很明顯,制造和過程自動化的第四次革命將在連接系統(tǒng)的骨干上推進:傳感器、執(zhí)行器、控制系統(tǒng)都通過互聯(lián)網(wǎng)協(xié)議通過不同類型的網(wǎng)絡連接。一旦所有機器/傳感器數(shù)據(jù)都在云上,就可以進行有趣的分析,以優(yōu)化制造、預測故障、安排維護、自動補充庫存,甚至定制成品規(guī)格以反映市場動態(tài)。
工業(yè)4.0的一個有趣的當代例子是通用電氣在紐約斯克內(nèi)克塔迪的最新美國工廠。這家鈉鎳電池制造工廠在 180,000 平方英尺的制造空間中擁有 10,000 多個傳感器;所有傳感器都連接到高速內(nèi)部以太網(wǎng)。2正如麻省理工學院技術評論所寫:“[傳感器]監(jiān)控諸如使用哪些批次的粉末來形成電池核心的陶瓷,使用多高的溫度來烘烤它們,制造每個電池需要多少能量,甚至當?shù)氐臍鈮骸T诠S車間,擁有iPad的員工可以從工廠周圍設置的Wi-Fi節(jié)點中提取所有數(shù)據(jù)。?3
本文從第四次工業(yè)革命正在進行這一前提開始。它認為,車間無處不在的連接將帶來生產(chǎn)力和可預測性的提高,這在很大程度上是由不斷改進的軟件和算法驅(qū)動的。是的,令人印象深刻且相當容易實現(xiàn)。然而,在我們建立基礎設施和這場革命真正進行之前,有各種系統(tǒng)設計障礙需要解決。本文將探討其中的一些關鍵系統(tǒng)挑戰(zhàn)。
工業(yè) 4.0 的系統(tǒng)級設計注意事項
工業(yè)4.0愿景的實現(xiàn)很可能跨越十年或二十年,但它已經(jīng)影響了各種系統(tǒng)設計。自動化顯示了邁向工業(yè) 4.0 時必須實施的三個關鍵系統(tǒng)設計方面。
分布式計算與控制
一個已經(jīng)在進行的關鍵系統(tǒng)級趨勢是計算和控制系統(tǒng)的本地化。需要分布式控制來增加復雜裝配線的靈活性,提供低延遲控制,并減輕主PLC的處理要求。在下一代工廠中,這將變得更加普遍。PLC的尺寸將繼續(xù)縮小,并處理越來越多的模擬和數(shù)字I/O通道。PLC還必須支持各種I / O協(xié)議,包括較新的協(xié)議,如IO-Link標準。?
無處不在的傳感器 那么所有不同的傳感器
呢?工業(yè)4.0的基本前提是制造數(shù)據(jù)是共享的,但這意味著必須首先收集越來越多的數(shù)據(jù)。這種雪崩式的數(shù)據(jù)源于工廠和過程設施內(nèi)傳感器系統(tǒng)數(shù)量的爆炸式增長,并蔓延到遠程操作中。即使過程參數(shù)今天不會影響您的控制算法,仍必須收集其數(shù)據(jù)以備將來使用。我們可以預見,今天在云上運行的算法的快速和預期的創(chuàng)新最終可能會“重新發(fā)明”一個舊的過程參數(shù)來預測一個重要的系統(tǒng)故障機制。業(yè)內(nèi)經(jīng)常用來描述傳感解決方案增長的短語是“普遍傳感”。我們將在下面對此進行更多說明。
經(jīng)過身份驗證的安全性
最后,通過互聯(lián)網(wǎng)協(xié)議連接所有傳感器、控制系統(tǒng)和執(zhí)行器以實現(xiàn)“大”數(shù)據(jù)分析肯定會增加安全問題。大部分工業(yè)安全問題通過軟件防火墻和安全互聯(lián)網(wǎng)交換機/網(wǎng)關得到解決。但安全問題不僅限于這些通信門戶,還包括硬件本身。新的縱深防御標準要求終端設備網(wǎng)絡(例如,用于此討論的傳感器和 PLC)經(jīng)過身份驗證且安全。這種基礎廣泛的軟件和硬件安全性對這些系統(tǒng)的設計有直接的系統(tǒng)級影響。
分布式本地控制:微型PLC的興起 一個更小但功能強大的PLC
可以對過程或裝配線進行本地控制,因此非常有吸引力,因為它可以實現(xiàn)低延遲的分布式控制。但是,微型PLC設計必須應對模擬I/O集成和散熱方面的重大技術挑戰(zhàn),這些挑戰(zhàn)在Maxim開發(fā)的Micro PLC概念驗證設計中得到了成功解決(圖3)。
圖3.這款微型 PLC 概念驗證集成了 32 位微控制器、以太網(wǎng)連接和 25 個 I/O 通道。總面積為 23 立方英寸(406,125 毫米)3).
這款微型PLC適合您的手掌。它集成了必要的32位微處理器和以太網(wǎng)連接;它處理和連接總共 25 個 I/O 通道。具體而言,它提供:
4 個模擬輸入和 1 個模擬輸出通道
8 個數(shù)字輸入和 8 個數(shù)字輸出通道
四通道 IO-Link 模塊,可與 4 個支持 IO-Link 的傳感器連接
成功的模擬集成
我們知道,模擬和分立元件占 PLC I/O 模塊電路板空間的 50% 到 70%。我們還知道,I/O 模塊在任何 PLC 中都需要大量空間。因此,將完整的PLC系統(tǒng)縮小到這種微型尺寸需要我們解決模擬I/O集成挑戰(zhàn)。
實現(xiàn)這種微小外形的一種方法是使用集成模擬器件,而不是大量甚至數(shù)百個分立元件。電路板尺寸縮小,功耗下降,可靠性提高。圖4所示為八通道串行器(MAX31911)和四通道數(shù)據(jù)隔離器(MAX14932),取代了左圖傳統(tǒng)設計中的數(shù)十個分立光耦合器和數(shù)百個電阻和電容。這種緊湊的微型 PLC 解決方案具有與常規(guī) PLC 相同的 I/O 通道容量。
更詳細的圖像。
圖4.這款雙芯片微型 PLC 概念驗證取代了數(shù)百個分立元件。
散熱和高效功率轉換
當您將這些眾多通道集成到如此激進的外形尺寸中時,板載 DC-DC 切換器的散熱和功率轉換效率成為主要問題。更高的電源效率導致更涼爽的運行。
圖5
所示為
MAX17505
DC-DC同步開關穩(wěn)壓器以5V輸出驅(qū)動不同負載電流的功率效率曲線。
圖5.效率與負載電流的關系。數(shù)據(jù)顯示,在很寬的電壓范圍內(nèi),效率高于 90%在和負載電流。
該系列穩(wěn)壓器的效率高于 90%(假設背板輸入電壓為 24V,電流驅(qū)動> 1A),與傳統(tǒng)解決方案相比,運行溫度低 30% 至 50%。這意味著顯著降低溫升,因此更容易將更多的I/O模塊封裝到更小的微型PLC中。
關于MAX17505高效、高電壓、同步整流降壓轉換器,我們可以說很多(圖6)。該器件采用雙路集成 MOSFET,可在 4.5V 至 60V 輸入范圍內(nèi)工作,并提供高達 1.7A 和 0.9V 至 90%V 的電流在輸出電壓。輸出電壓范圍內(nèi)的內(nèi)置補償功能免除了增設外部元件的需要。-40°C至+125°C范圍內(nèi)的反饋(FB)調(diào)節(jié)精度為±1.1%。該下變頻器采用緊湊型 (4mm x 4mm) TQFN 無鉛 (Pb) 封裝,帶裸焊盤。提供仿真模型。
圖6.MAX17505是高效率、高電壓、同步整流降壓轉換器,具有雙路集成MOSFET,工作在4.5V至60V輸入電壓,提供高達1.7A和0.9V至90%V的電流在輸出電壓。
MAX17505采用峰值電流模式控制架構,具有MODE功能,以多種控制方案工作器件:脈寬調(diào)制(PWM)、脈沖頻率調(diào)制(PFM)或非連續(xù)導通模式(DCM)。PWM 操作可在所有負載下提供恒定頻率操作,在對開關頻率敏感的應用中非常有用。PFM 操作可禁用負電感器電流,并在輕負載時額外跳脈沖以實現(xiàn)高效率。MAX17505具有DCM,具有恒定頻率工作特性,負載比PFM模式輕,在輕負載時不跳脈沖,僅禁用負電感電流。DCM 操作提供介于 PWM 和 PFM 模式之間的效率性能。低電阻片內(nèi) MOSFET 可確保滿載時的高效率并簡化布局。
采用 IO-Link 通信標準的普遍檢測
在未來的工廠中,傳感器將無處不在,并通過不同的接口直接連接到網(wǎng)關或PLC。傳感器不再僅僅發(fā)送ON/OFF信號,而是很快將傳輸豐富的數(shù)據(jù)。IO-Link協(xié)議是業(yè)界發(fā)展最快的傳感器通信技術之一,在何時何地變得如此重要。雖然 IO-Link 是 IEC 標準,但它基于已建立的 3 線傳感器和執(zhí)行器連接。?
自 1980 年代以來,工業(yè)現(xiàn)場總線允許更智能的設備、更快的安裝、更少的布線和更輕松的維護。然而,缺乏單一的、普遍接受的現(xiàn)場總線也造成了混亂、培訓挑戰(zhàn)、高成本和設備之間的兼容性問題。IO-Link 協(xié)議是第一個用于與傳感器和執(zhí)行器通信的開放式、現(xiàn)場總線診斷、低成本、點對點串行通信標準。它已被采用為國際標準(IEC 61131-9)。4
IO-Link協(xié)議標準化了世界各地工業(yè)設備之間的互操作性。該標準可以直接存在于PLC上,也可以集成到所有標準現(xiàn)場總線中。這種靈活性很快使其成為與智能設備(如Maxim Integrated的Santa Cruz光學傳感器MAXREFDES23#)進行通用通信的事實標準(圖7)。
圖7.圣克魯斯光學光傳感器的參考設計框圖。
IO-Link技術以及傳感器的持續(xù)小型化,有助于在整個工廠內(nèi)部署超小型、高能效傳感器。圖 8 顯示了圣克魯斯 IO-Link 顏色傳感器。
圖8.MAXREFDES23# 是一款微型 IO-Link 光傳感器,集成了六個傳感器:環(huán)境光(透明)、紅色、綠色、藍色、紅外線和溫度。所有這些都在6.5mm x 25mm的微型印刷電路板(PCB)上。
作為世界上最小的 IO-Link 光傳感器之一,Santa Cruz MAXREFDES23# 系統(tǒng)在微型 PCB 上集成了六個傳感器——環(huán)境光(透明)、紅色、綠色、藍色、紅外和溫度。Santa Cruz設計包括一個行業(yè)標準的Maxim IO-Link器件收發(fā)器(MAX14821);瑞薩電子超低功耗、16位微控制器(RL78),采用Technologie Management Gruppe Technologie and Engineering (TMG TE) IO-Link器件堆棧;以及Maxim集成MAX44008光傳感器(圖7和圖8)。此次合作使圣克魯斯成為符合 IO-Link 版本 1.1/1.0 標準的光傳感器參考設計。像Santa Cruz這樣的緊湊型傳感系統(tǒng)使得部署許多廣泛的傳感器變得簡單方便,這些傳感器通過IO-Link協(xié)議向連接到云或PLC的傳感器集線器提供有用的數(shù)據(jù)。?
今天的工業(yè)傳感器(如Santa Cruz)必須具有超高能效,因為它們體積小且封閉,以確保安全。這些傳感器設計中,越來越多的人將使用高效DC-DC開關穩(wěn)壓器,而不是傳統(tǒng)的LDO。圖9所示的MAX17550/MAX17551 DC/DC穩(wěn)壓器等產(chǎn)品即使在驅(qū)動25mA和50mA小負載電流時也能提供>90%的效率。
圖9.MAX17550/MAX17551高效DC-DC開關穩(wěn)壓器設計用于驅(qū)動傳感器系統(tǒng)應用的低負載電流。
對嵌入式硬件安全的需求
眾所周知,IC供應商并不總是認為安全性至關重要。考慮一下最近由Unisys“與Ponemon Institute合作”贊助的對13個國家的599名全球IT和IT安全高管的調(diào)查。他們的結果發(fā)現(xiàn),只有28%的受訪者認為安全性是整個企業(yè)的五大戰(zhàn)略優(yōu)先事項之一。然而,幾乎60%的人承認網(wǎng)絡威脅使他們的控制系統(tǒng)和SCADA系統(tǒng)面臨風險。5
只有28%的受訪者優(yōu)先考慮安全性。這應該會讓讀者感到不安,因為我們知道分布式控制和無處不在的連接已經(jīng)在推動對安全性日益增長的需求。大多數(shù)安全問題都圍繞著對更好的防火墻、入侵檢測系統(tǒng)和安全交換架構的需求。但同樣重要的是需要可靠的硬件,尤其是I/O模塊和遠程現(xiàn)場傳感器。這些設備可以被克隆或欺騙,尤其是在它們周圍幾乎沒有物理安全性的情況下。當發(fā)生任何此類違規(guī)行為時,根據(jù)從這些設備收集的數(shù)據(jù)做出關鍵決策的工業(yè)互聯(lián)網(wǎng)將受到嚴重損害。因此,確保這些系統(tǒng)經(jīng)過身份驗證和保護至關重要。最終,如果沒有安全的嵌入式硬件,我們將無法充分體驗工業(yè)4.0的潛力。
我們對工業(yè)4.0安全系統(tǒng)的關注必須從將數(shù)據(jù)發(fā)送到云或PLC的可信傳感器開始。遠程安全漏洞的影響是深遠的。例如,如果受損傳感器發(fā)送有關油箱中油位或管道中壓力的虛假數(shù)據(jù),則基于該數(shù)據(jù)采取(或未采取)的操作可能會產(chǎn)生災難性后果。我是不是太戲劇化了?一點也不。但不可否認的是,傳感器數(shù)據(jù)受損造成的災難性后果較小。如果數(shù)據(jù)受到損害,則使用傳感器數(shù)據(jù)預測維護需求的大數(shù)據(jù)分析程序可能會完全被拋棄。這關系到正常運行時間、可預測的維護和整體行業(yè)效率——工業(yè) 4.0 的基石。
并非所有傳感器的物理安全性都可能并不總是可行的,特別是當傳感器非常遙遠時,例如用于監(jiān)測石油和天然氣田的傳感器。無法訪問使其容易受到物理攻擊,因此必須在接受所有這些傳感器的數(shù)據(jù)之前對其進行身份驗證。
幸運的是,幾年前就為醫(yī)療和消費產(chǎn)品(如打印機墨盒)制定了身份驗證方案。如今,身份驗證非常基于標準,必須使用遵守身份驗證協(xié)議的防篡改設備來實現(xiàn)。
基于對稱 SHA 256 算法的基于硬件的身份驗證方案的簡單概念框圖如圖 11 所示。SHA-256協(xié)議基于授權設備之間的質(zhì)詢和響應交換,將在接受和讀取傳感器數(shù)據(jù)之前對傳感器進行身份驗證。SHA-256身份驗證使攻擊者無法連接到網(wǎng)絡并假裝成傳感器,甚至無法用受感染的系統(tǒng)替換傳感器系統(tǒng)。6
圖 11.基于SHA-256的身份驗證,通過HART或任何其他通信標準對遠程現(xiàn)場傳感器系統(tǒng)進行身份驗證。頁面數(shù)據(jù)(32 字節(jié))和密鑰(2 字節(jié))對于傳感器和主機都是已知的。傳輸?shù)淖止?jié)數(shù)將產(chǎn)生較小的開銷。HART是HART通信基金會的注冊商標。無線變送器的圖像由艾默生過程管理提供。?
總結
工業(yè) 4.0...描述互聯(lián)制造運營的現(xiàn)代方式,其中來自不同分布式 PLC、傳感器和其他現(xiàn)場設備的數(shù)據(jù)被聚合,以利用分析和優(yōu)化軟件的優(yōu)勢。工業(yè) 4.0 有望在正常運行時間、定期維護、電源效率和更高效地利用所有資源方面優(yōu)化制造資產(chǎn)。制造數(shù)據(jù)也可以集成到公司的ERP和CRM軟件中,以有效地規(guī)劃制造流程,甚至可以使用客戶的信息來更改裝配線和工藝參數(shù)。
但是,當您開始互連所有不同的制造系統(tǒng)時,需要考慮一些重要的系統(tǒng)設計因素。我們在本文中討論了其中的一些注意事項。我們已經(jīng)展示了如何使用新的硅技術,特別是在模擬/混合信號領域,來解決其中一些工業(yè)系統(tǒng)挑戰(zhàn)。這些新的集成技術不僅允許您縮小傳感器系統(tǒng)和PLC,而且還提供了一種經(jīng)濟高效地在現(xiàn)場一些關鍵IO設備中增加嵌入式安全性的方法。
隨著我們開始工業(yè)4.0的過渡,毫無疑問,我們將在我們的工廠系統(tǒng)中發(fā)現(xiàn)并解決其他系統(tǒng)設計考慮因素。我們一定會使用最新技術來實現(xiàn)所需的功率、性能和通信配置文件。
審核編輯:郭婷
-
傳感器
+關注
關注
2554文章
51700瀏覽量
758544 -
plc
+關注
關注
5021文章
13437瀏覽量
467024 -
工業(yè)4.0
+關注
關注
48文章
2023瀏覽量
119162
發(fā)布評論請先 登錄
相關推薦
數(shù)字衛(wèi)星電視接收器前端設計的系統(tǒng)考慮因素有哪些?
STM32的基本系統(tǒng)主要涉及哪幾個部分
基于STM32的智能家居系統(tǒng)本系統(tǒng)的設計資料分享
基于TMS320VC5402 的DSP基本系統(tǒng)的設計
自制筆記本系統(tǒng)恢復光盤
筆記本系統(tǒng)輕松安裝與使用教程
筆記本系統(tǒng)安裝的方法
Android 3.0 Honeycomb版本系統(tǒng)將亮相MWC2011
基于DSP的聲控電子記事本系統(tǒng)
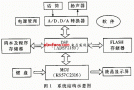
STM32的基本系統(tǒng)介紹
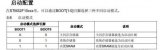
一文讀懂STM32的基本系統(tǒng)
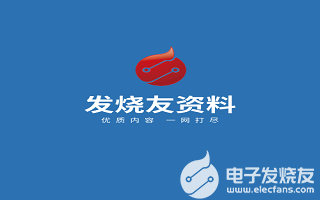
超聲系統(tǒng)考慮因素如何影響前端組件選擇
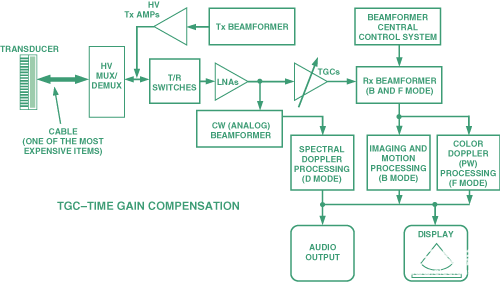
評論