光伏(PV)行業在過去幾年中一直享有巨大的增長,主要是由于高油價和環境問題。然而,光伏成本仍然是進一步擴張的最大障礙,需要進一步降低才能與傳統的煤基電網電力競爭。除太陽能電池板外,光伏逆變器等電子元件是主要的成本組件。出于安全和操作考慮,并網光伏轉換器需要將收集的直流與交流電網隔離。通常需要隔離以滿足安全法規,以防止直流注入交流電網,從而影響配電變壓器和傳統電表。光耦合器等傳統隔離解決方案無法滿足光伏電池板典型的25年保修。微型逆變器也成為提高系統可用性和遮陽條件下性能顯著提高的趨勢。在這些情況下,PV逆變器安裝在PV面板的背面,那里的高溫會加速光耦合器的退化。本文討論了光伏逆變器的信號和電源隔離需求,以及使用微變壓器集成隔離功能如何提高系統性能和可靠性,并減小系統尺寸和成本。
光伏逆變器有兩種主要類型,無變壓器和變壓器隔離逆變器。無變壓器逆變器可能會遭受大接地漏電流和注入直流電流的影響,因為面板電容大,光伏板和交流電網之間缺乏隔離,如圖1(a)所示。注入電網的交流電流中的直流分量不太理想,因為它可能會使配電變壓器飽和。許多安全標準對直流注入量有嚴格的電網要求,在某些情況下,變壓器隔離是強制性的。面板和電網之間的變壓器隔離將消除由面板相對于電網的電壓變化引起的直流注入路徑,如圖1(b)所示。除直流注入外,并網逆變器還需要滿足其他電網要求,例如總諧波失真和單個諧波電流水平、功率因數和孤島運行檢測。需要準確監測電網電壓和注入電網的電流。如果執行MPPT的控制器和柵極驅動功能位于面板側,則需要隔離這些測量。為了操作光伏電池板以獲得最大效率,需要使用最大功率點跟蹤(MPPT)算法。為了實現MPTT,還需要監控面板電壓和電流。當人們嘗試串聯許多光伏逆變器以最大限度地減少所需的逆變器數量時,面板電壓可能會變得相當高。來自光伏電池板高壓側端子的電流測量也需要隔離。
圖1.(a) 非隔離逆變器的直流注入電網 (b) 通過隔離中斷直流注入
除了隔離的電流和電壓測量外,還需要一些接口功能,如RS-485、RS-232和CAN。RS-485或RS-232通常用于與這些光伏逆變器通信以獲取實時性能數據,并且由于行程距離大且出于安全原因,需要隔離通信總線。隔離CAN也可用于距離不遠的通信。這些收發器還需要將隔離電源從面板側提取到總線側。
傳統上,隔離由光耦合器提供。然而,其當前的傳遞函數會隨著時間的推移而退化,并且可能會在幾年內變得無法運行,比為許多這些太陽能電池板提供的20年終身保修要短得多。在這里,我們提出了基于微變壓器的信號和電源隔離,可以滿足光伏逆變器中的各種集成需求。它不僅可以消除光耦合器的壽命退化限制,還可以集成ADC等檢測功能或柵極驅動器和RS-485或RS-232收發器等接口功能。此外,它還提供隔離電源,為這些檢測IC、隔離式收發器或隔離式柵極驅動器供電。基于光耦合器的柵極驅動器也非常耗電,柵極驅動器時序變化很大。基于微變壓器的柵極驅動器不僅消耗更少的功率,而且還提供更好的匹配柵極驅動器時序,以提高系統總功率轉換效率。隔離信號和電源集成顯著減少了元件數量,從而降低了系統成本并提高了可靠性。
使用微變壓器的信號和電源隔離
微變壓器可用于提供高達 5 kV rms 的集成信號和電源隔離 [1]。對于信號傳輸,輸入數據通常在傳輸到數據變壓器的初級設備之前進行編碼。次級端使用解碼來恢復信號。輸入和輸出之間的隔離由初級線圈和次級線圈之間的絕緣層提供。為了實現跨隔離的高效功率傳輸,使用自振蕩高頻振蕩器驅動電源變壓器的初級,并使用高頻肖特基二極管提供整流直流電壓。調節由次級控制器產生的PWM完成,PWM通過反饋變壓器以遠低于振蕩頻率的頻率打開和關閉振蕩器,如圖2(a)所示。通過反饋變壓器傳輸的反饋信號的工作方式與通過數據變壓器傳輸的其他數據通道信號的工作方式相同。通過獨立的能量轉換和反饋控制路徑,優化能量轉換效率,同時保持穩定的調節。圖2(b)顯示了一個具有四個獨立隔離數據通道的500 mW隔離DC-DC轉換器示例。
圖2.(a) 隔離式DC-DC轉換器原理圖 (b) 具有500 mW隔離電源的4通道隔離器的封裝實現
在本例中,變壓器構建在與編碼器或主芯片以及解碼器或次級芯片不同的芯片上。然而,這主要是出于成本原因,變壓器原則上可以構建在其中一個IC芯片之上。柵極驅動器、收發器和ADC等其他電路功能均可集成。
光伏逆變器中的隔離集成
圖3所示為典型的3級并網光伏逆變器。第一級是可選的升壓轉換器,用于在面板電壓通過隔離式DC-DC轉換器級之前對其進行升壓。隔離式DC-DC轉換器包括通過高頻變壓器進行全橋DC-AC轉換。高頻變壓器具有體積小、效率高的優點。次級處的交流整流至通常高于電網峰值電壓的直流電壓。整流后的直流通過第三逆變器級轉換為電網線路頻率。需要檢測面板輸出電壓和電流并將其饋入微控制器,以執行最大功率傳輸跟蹤(MPTT)算法。微控制器還負責隔離式DC-DC和輸出逆變器的柵極驅動器控制。輸出逆變器位于電網側,接地與直流面板接地不同,從微控制器到逆變器驅動級的通信需要隔離。通常需要四個光耦合器,但它們耗電大,其較大的傳播延遲可能會影響柵極驅動器的定時精度,從而影響逆變器效率,最重要的是,它們支持光伏電池板20至25年保修的能力值得懷疑。另一方面,基于微變壓器的隔離器[1,2]消耗的功率要少得多,傳播延遲要短得多,并且性能不會隨著時間的推移而下降。此外,多通道隔離器還可以與片內DC-DC轉換器集成,為柵極驅動器提供隔離電源。逆變器輸出和并網之間的繼電器用于確保逆變器輸出頻率和相位與市電電壓同步,并通過能夠快速斷開電網故障或當市電電壓或頻率超出可接受限制來實現防孤島保護。電網側需要電壓檢測以檢測過零,電流檢測需要確保正弦波電流饋入負載。檢測信息可以通過隔離式ADC傳送到控制器。隔離式ADC集成了一個16位二階Σ-Δ調制器,具有基于微變壓器的數字隔離,能夠實現3.75 kV隔離,非常適合基于分流的電流檢測。電流互感器可用于電流檢測,但它們價格昂貴、體積龐大,并且對外部磁場敏感。也可以使用霍爾效應傳感器,但它們存在非線性和偏移,會影響電流測量的精度。分流器與集成隔離式ADC相結合,提供了一種可靠且低成本的替代方案。隔離式ADC還需要電網側的隔離電源才能自供電,并且可以集成使用微變壓器的隔離式DC-DC,以節省對分立DC-DC轉換器的需求。在需要PLC通信的情況下,電網側的PLC芯片可以由隔離的DC-DC供電,而其與面板側控制器的通信則通過多通道隔離器進行。
圖3.三級光伏逆變器中的隔離實現
基于微變壓器的隔離還可以與大電流輸出柵極驅動器集成,以提供完全隔離的半橋柵極驅動器。圖4是并網光伏逆變器的柵極驅動方案示例。對于初級側DC-AC全橋開關,通常不需要對低側柵極驅動器進行隔離,特別是對于低功耗逆變器。具有4 A驅動能力的2通道1 kV隔離驅動器適用于兩個高端開關。逆變器的開關位于交流側,因此低壓側和高側都需要隔離式柵極驅動器。
圖4.三級光伏逆變器中的柵極驅動器實現
直流側的微控制器通常需要2.5 kV或5 kV隔離式柵極驅動器,以便直接與交流側逆變器通信。低側柵極驅動器可由集成的DC-DC供電,該電源從面板側獲得電源,而高端柵極驅動器可由自舉解決方案提供。
每個半橋柵極驅動器由3路隔離組成,即輸入和輸出之間有隔離,兩個輸出之間有隔離。輸入至輸出隔離通過片內變壓器提供。圖5(a)是1 kV柵極驅動器的變壓器結構,圖5(b)是5 kV柵極驅動器的變壓器結構。1 kV半橋柵極驅動器采用封裝中的三個芯片、一個輸入芯片和兩個相同的柵極驅動器芯片。
圖5.變壓器結構 (a) 1 kV 柵極驅動器 (b) 2.5 kV 柵極驅動器
如圖5(a)所示,在輸入芯片上實現了兩個1 kV變壓器,每個柵極驅動器輸出一個。輸入連接到底部線圈,底部線圈由 2.64 μm 厚的氧化物與頂部線圈隔離,每個頂部線圈通過橫向氧化物隔離相互隔離。兩個柵極驅動器芯片位于各自的分離焊盤上,并通過類似于[2]所示的芯片到芯片鍵合線連接到輸入芯片的頂部線圈。5 kV柵極驅動器的實現方式類似,不同之處在于頂部線圈通過20 mm厚的聚酰亞胺與底部線圈隔離。
對于多逆變器并聯系統(如組串式逆變器),逆變器之間也需要通信,通常通過需要隔離的RS-485總線、RS-232總線或CAN總線實現。自供電隔離式收發器能夠從面板側獲取總線側的電源。
微型逆變器也開始獲得牽引力,以提高系統的可靠性和性能。它們還解決了組串式逆變器遭受的潛在直流電弧問題。微型逆變器通常安裝在環境溫度可能很高的屋頂面板下方。高溫會加速光耦合器內部的LED退化;另一方面,基于微變壓器的隔離不會隨著時間的推移而降低性能,并且在這些極端條件下工作良好。單級逆變器可用于微型逆變器,而不是全三級逆變器,以降低系統成本。每個微型逆變器只能達到幾百瓦左右,在這個功率水平下,隔離集成提供了許多系統集成的可能性,以降低系統成本并提高系統可靠性。
結論
基于微變壓器的隔離集成是滿足并網光伏逆變器、集中式逆變器或微型逆變器隔離需求的理想解決方案。其集成的信號和電源隔離功能可顯著減少元件數量,提高系統可靠性和使用壽命,其精確的柵極驅動時序可提高逆變器效率。使用微變壓器的隔離式ADC可實現更精確的電網電流和電壓測量,從而為電網提供高質量、單位功率因數的正弦電流。
審核編輯:郭婷
-
變壓器
+關注
關注
159文章
7470瀏覽量
135213 -
轉換器
+關注
關注
27文章
8701瀏覽量
147146 -
逆變器
+關注
關注
283文章
4717瀏覽量
206769
發布評論請先 登錄
相關推薦
基于LLC隔離的光伏并網逆變器設計方案
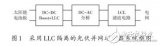
基于CPLD的光伏并網逆變器的鎖相及保護電路的設計怎么實現?
并網光伏逆變器隔離的集成
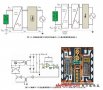
評論