(文/程文智)隨著新能源汽車近幾年滲透率的快速提升,最近國內各大新能源車企也規劃了2023年的銷量目標,從他們公開的銷量目標中可以看到他們的雄心,最少都會比去年提升50%,比如廣汽埃安計劃2023年對比2022年的27萬銷量同比增長85%至50萬~60萬輛;比亞迪則計劃2023年銷售同比增長87%~140%至350萬~400萬輛,而其2022年的銷量是186.85萬輛;極氪計劃同比增長100%至14萬輛;理想汽車計劃同比增長126%至30萬輛;奇瑞新能源計劃同比增長50%至45萬輛;深藍計劃銷售40萬輛,而其2022年的銷量僅為3.3萬輛。
新能源汽車的快速發展,也帶動了電池管理系統(BMS)的進步,因為BMS可以保護電池,且能通過智能充電與放電算法延長電池壽命、預測剩余電池的續航能力,還能在工作狀態下維護電池。特別是新能源汽車普遍采用的鋰離子電芯更是帶來了嚴峻的挑戰,因為其需要精密的電子控制系統。此外,還存在因火災和爆炸而造成傷害的重大風險。因此,BMS需要先進的半導體技術支持,以符合所有性能、安全與成本指標。
BMS工作原理和業界趨勢
典型的BMS架構具有模塊化結構,通常由三個主要子系統組成:電芯監測單元(CSU)、電池接線盒(BJB),及電池管理單元(BMU)。
其中電芯監測單元中包含了非常多數量的電芯,比如400V系統超過了100個電芯,800V系統很可能超過了200個電芯。在這樣的電芯系統中,需要能夠高精度監測每一個電芯電壓的產品。該單元通過監測每個電芯的電壓和溫度,收集所有電芯的參數信息。
圖:典型的BMS架構框圖(來源:TI)
框圖中的右邊是電池接線盒單元,在傳統的電池接線盒中通常有很多引線、接線、接口連接到BMU單元。想要通過BMU單元對電池的電壓,包括電池盒內部的電壓、電流和溫度等參數進行測量,就會需要很多的線束。但智能接線盒的方案,則可以把電池包的高精度電流監測系統、診斷系統以及通信模塊的功能都集成到專門用于智能電池盒的芯片產品中,免去了繁雜的線束。
在接線盒和CSU之間,傳統架構會有很多連線傳輸電池采集的信息,這使得連線非常多。TI BMS 總經理王世斌表示,TI的整套方案可以支持只有兩根線的菊花鏈通信,通過菊花鏈通信就可以非常方便地把電芯里面的各種信息通過兩根線傳輸到電池管理單元,所以,整個通信系統可以降低很多線束的數量,同時,TI支持通過無線通信的方式來實現電池監測的信息傳輸,有利于進一步降低線束數量,給予終端用戶更多選擇。
高精度電芯監測器和電池包監測器助力延長電池續航
據王世斌介紹,隨著電動汽車越來越受歡迎,先進的BMS有助于克服阻止電動汽車廣泛普及的關鍵障礙,改善電動汽車的駕乘體驗。因為電池電壓的測量準確度和精度對消費者的駕駛體驗至關重要。即使細微的溫度變化也能對電動汽車的續航里程產生重大影響;特別是寒冷的天氣,對電池電壓范圍影響的幅度可高達40%。這些變化會為電池電壓和預期的電動汽車續航里程造成相當大的不確定性。
為此,TI近期推出了兩款BMS系列中的全新產品:BQ79718-Q1 電芯監測器和 BQ79731-Q1 電池包監測器。據王世斌介紹,BQ79731-Q1和BQ79718-Q1在測量電池電壓、電流和溫度方面提供了出色的準確度和精度,可有效確定車輛的真實續航里程、延長電池包的整體壽命并提高其安全性。
他特別指出,此次的更新迭代主要在三個方面。首先,就是在電池電芯監測上精度更高,BQ79718-Q1的異常檢測精度可以高達1mV的數量級,并具備300mA電流能力的被動式電池平衡功能,且支持與BQ79731-Q1電池包監測器進行電壓和電流同步測量,以提供更精確的健康狀態和電池電量信息計算。這意味著這種產品可以適用于不同化學成份的電池,包括主流的鎳錳鈷(NMC)和磷酸鐵鋰(LFP)等化學成份鋰離子電池,這使得電動汽車在里程計算方面可以達到更高的精度。因為TI知道磷酸鐵鋰的曲線相對平緩,對于精度要求更高,新品正好可以滿足這方面的要求。
第二點,則在功能安全方面。此次新品完全支持ASIL-D的要求,如冗余設計,錯誤狀態報錯等能力都能滿足客戶在汽車功能安全相關的要求。
最后一點,整個方案中電芯監測產品與電池包監測產品夠實現高精度同步,在設計中準確監測數據,對電池狀態的評估也更加準確,對于汽車剩余里程的計算都有非常大的幫助。
BQ79718-Q1電芯監測器主要是用于測量電壓,在接線盒里的BQ79731-Q1電池包監測器主要是用于測量電流。在電壓和電流的測量間,有一個非常好的同步功能,它們同步的時延非常小,只有128微秒的時間,使得TI的產品能夠非常準確地計算電動車當前的參數,這些準確的參數使得整個系統可以更好地評估汽車后續能夠行駛的里程數量。
王世斌舉例說,以一個比較典型的車輛的狀態來看。假設一輛車剩余里程300公里,目前主流的電池方案是鎳鈷錳鋰電池,現在很多的應用逐漸轉向磷酸鐵鋰電池技術,以這兩個技術為例來看一下新產品是如何提高續航里程計算精度的。
圖:電池化學放電曲線(紅色為鎳錳鈷鋰電池;藍色為磷酸鐵鋰電池)
對于鎳鈷錳鋰電池的方案,它的放電曲線相對比較陡一些,這種情況下,如果基于10mV精度的計算,可能會導致9.7公里左右的里程誤差,當我們把OCV計算精度提升到1mV數量級時,換算到里程精度計算上,就可以達到僅僅只有0.8公里的里程誤差,這意味著通過我們技術的提升,假設把精度從10mV提升到1mV以后,在這種情況下,對剩余里程計算精度就可以提高8.9公里。
對于磷酸鐵鋰電池來說,這一改進的變化就非常大了。因為磷酸鐵鋰整個放電曲線電壓斜率比較小,所以,如果有10mV誤差的情況下,整個對應的里程誤差就會達到125.5公里這樣一個數字,如果把電壓誤差值降到1mV,這時候里程誤差一下子就降到只有24.1公里。把整個誤差縮小了101.4公里,這意味著車輛計算剩余里程時的不確定性整整降低了101.4公里。
王世斌特別強調,磷酸鐵鋰電池,如果基于10mV精度,車輛很有可能誤差會達到30%,這個誤差確實非常大。這意味著當你開到還剩下30%的電時,就不能顯示出30%。TI這一代的產品相比上一代產品,在電壓監測精度上做了很大的提升。從3.5個mV的精度現在提升到1mV的精度。讓誤差可以變得更小,從而改善了消費者的駕乘體驗。
TI也非常注重提高整個車輛安全的等級,也就是車規要求的ASIL的精度。“對所有參數的檢測,我們有主要的檢測通路,同時還有冗余通路,兩者同時對一個參數進行檢測。當主通路和冗余通路產生一個誤差值,當這個差值大于一定的參數時,我們就認為這個檢測是有問題的,監測器就會把這個問題作為一種異常的狀態立刻匯報給處理器。如果我們發現這兩個參數檢測值沒有差異,或者差異小于一定的范圍時,我們的監測器就不會匯報。這樣的機制可以確保電芯狀態出現異常的時候得到及時匯報。”王世斌表示。
另外一個產品是能夠實現智能接線盒的BQ79731-Q1電池包監測器。該芯片能對智能電池包進行非常高精度的電流參數的監測,并滿足客戶對電壓、電流同步測量的需求。電池包里的產品和現有的一些電芯監測器產品可以配套使用,它們互相配合可以滿足很高的電流電壓同步測量的要求,以達到預期的測量效果。因為更小的同步延時可以更準確的去評估電池包的荷電狀態并做到更精確的評估。
結語
更好的BMS的技術,可以使得整個電動汽車的未來路線獲得更好的提升,精度更高、安全性更好的BMS可以使得車輛行駛更長的里程并提升電動汽車使用的效率和未來發展的普及率。
-
電動汽車
+關注
關注
156文章
12107瀏覽量
231426 -
ti
+關注
關注
112文章
7985瀏覽量
212516 -
bms
+關注
關注
107文章
1005瀏覽量
66041
發布評論請先 登錄
相關推薦
SiC解決方案:硅陽極能否增加電動汽車的續航里程
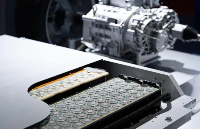
無線充電技術:電動汽車未來的里程焦慮解藥
全球電動汽車銷量8月增20%
東芝為電動汽車BMS推出新款900 V輸出耐壓的車載光繼電器
歐洲寶馬電動汽車銷量大漲,勝過特斯拉
韓國電池制造商SK On陷入危機,電動汽車銷量低迷拖累電池業務
電動汽車四個常用BMS拓撲結構
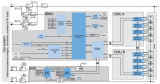
評論