改編自:《新一代智能化數控系統》(作者:陳吉紅,楊建中,周會成)
在數控加工中,有很多提高曲面加工質量的手段,如高速高精運動控制、誤差補償和振動抑制。本文主要介紹軌跡平滑和速度優化對曲面加工質量的提升和優化。
**「 **1.曲面加工軌跡平滑方法 」
CAM系統生成的刀具路徑通常是G0連續(僅位置連續)的分段線性路徑。程序段之間G1不連續(切向不連續),會導致數控系頻繁降速,影響加工效率。插補軌跡G2不連續意味著曲率不連續,此時如果降速不充分,會引起較大的加速度波動,造成機床的劇烈振動,影響加工質量。因此,為了保證加工效率和加工質量,Gk(k>=2)連續的刀具路徑平滑是高性能數控系統的重要性能之一。
在數控加工中,刀具軌跡擬合方法主要分為插值和逼近兩種。當刀具軌跡順序通過給定的刀位點時,這種刀具軌跡稱為插值軌跡;當擬合的軌跡不嚴格通過刀位點,只是在設定的誤差范圍內接近給定的刀位點,我們稱這種刀具軌跡為逼近軌跡。目前,在軌跡擬合方面的研究主要分為以下幾類。
1)局部樣條構造軌跡
局部樣條構造方法是通過在每兩個刀位點之間構造一段樣條,并保證樣條的弓高誤差來控制樣條擬合的精度。這種擬合方法具有局部性好,計算簡單,算法實時性好,適用于數控系統的實時數據處理流程。局部樣條構造方法認為刀位點反應了原始模型的特征,構造的樣條嚴格通過每一個刀位點,避免造成零件特性信息丟失影響零件加工精度,如圖1所示。
圖1 刀位點之間的局部樣條構造
樣條構造的一種方式是以相鄰兩個點的坐標及點的切向量為邊界條件,在兩個點之間構造一段樣條。點的坐標值不變,切向量方向可以通過各個點前后點的坐標插值得到,切向量的模長可以利用相鄰的小線段長度進行估算,如圖2所示。通過該方法構造出來的樣條能夠嚴格控制其形狀和對小線段的逼近精度,具有較好的局部特性,但樣條間通常只達到了G1連續。
圖2 兩點之間構造樣條
另外,這種樣條構造的方式對點的切向量估算要求比較高,如果切向量估算不準,容易造成樣條變形。為了提高邊界條件的準確性,有文章中提出在CAM生成刀具軌跡時,利用模型信息將刀位點處的切向量和誤差指向信息同時輸出到文件中,指導數控系統完成更加精確的樣條構造。其中弦誤差指向信息是兩點(P0、P6)之間弦高差最大的位置和方向CHORD_ERR[w,e,l],如圖3中的P3點處,w為小線段上弦高差最大位置的比例,e表示最大的弦高差,l表示弦高差的方向。
圖3 包含切向和誤差指向信息的樣條構造
這種樣條構造的方式可能得到更高的精度和更合適的軌跡形狀,但是對CAM的信息要求較高,目前還不具有通用性。
構造樣條的另一種方式是以小線段為單位,在兩個小線段之間插入過渡樣條,并保證過渡樣條與兩側直線段的連續性。如下圖中的B3(u)和B4(u)兩段樣條即為構造的過渡樣條,這兩段樣條可以通過6個控制點(Q1~Q6)進行描述。
圖4 小線段之間的過渡樣條構造
然而,有文章認為,這類樣條過渡的方式雖然保證了樣條的G2連續,但過渡樣條沒有通過編程刀位點,可能造成零件特性信息的丟失并引起相鄰軌跡的橫向不均勻。為了解決不通過編程刀位點的問題,該文章提出先構造G2甚至G3連續的過渡樣條,再通過迭代的方式對過渡樣條進行變換,使其在很小的誤差范圍內通過編程刀位點,如圖5所示。
圖5 通過編程刀位點的局部過渡樣條
以上局部構造的方法雖然最大程度地通過編程刀位點,但是沒有考慮小線段軌跡中的噪點(缺陷點),對G代碼要求較高,實際工程應用中難以普及。另外,這類方法由于是在兩個刀位點或兩段小線段之間插入局部樣條的方式構造整個刀具軌跡,缺乏全局軌跡擬合的光順特性。
2)插值樣條擬合軌跡
另一些研究人員是通過離散編程點計算每個程序段轉角處所對應的“離散曲率”,并判斷連續小線段軌跡的偏轉情況,將偏轉超過閾值的轉折點作為可光順區域的邊界特征點。然后利用B樣條曲線對邊界特征點之間的點進行插值擬合,以達到整體光順的目的,如圖6所示。
圖6 刀位點的全局插值擬合
該方法避免了兩個特征點之間點的切向不連續問題,軌跡壓縮率較高,可有效提高編程點之間軌跡運行時的進給速度。但是該類方法對光順后的軌跡與原始軌跡之間的誤差并沒有做嚴格的限制,很難保證插值后的加工精度。
為了提高這類插值軌跡的擬合精度,有文章提出選擇性的插值擬合,先將能夠擬合為樣條的小線段軌跡進行分組,例如每5個點一組,采用三次Bezier曲線對一組刀位點的第一個刀位點P1、第三個刀位點P3和最后一個刀位點P5進行插值,然后判斷P2、P4點相對于樣條的誤差是否滿足逼近精度,如果滿足則直接輸出樣條;如果不滿足則對P3處的參數進行調整或插入更多的點,直到滿足中間點的逼近精度,如圖7、圖8所示。
圖7 三次Bezier曲線插值P1、P3、P5示意圖
圖8 增加刀位點重新分組示意圖
在得到一系列Bezier曲線后,利用B樣條的性質,將多條三次Bezier曲線轉換為一整條三次B樣條,形成最終的插值軌跡,這種選擇性地刀位點插值軌跡能夠降低多點擬合的計算復雜度,并能有效提高插值精度。
3)逼近樣條擬合軌跡
還有一些研究和實際應用是利用樣條曲線對離散編程點進行逼近擬合(圖9)。為保證擬合曲線的逼近精度,需要對擬合后的曲線與原始刀位點之間的誤差進行檢查,并通過迭代與分段擬合的方法進一步提高對原有刀位點的逼近程度。這類方法保證了對刀位點的擬合精度,在提高軌跡的全局光順性的同時實現了數據的壓縮,但是其誤差校驗過程中需要計算點到曲線的距離,并可能需要多次迭代,算法耗時較高且具有一定的不確定性,因此這類算法對系統的硬件處理速度和軟件流程具有很高的要求。
圖9 刀位點的全局逼近擬合
在逼近樣條擬合軌跡方面多個知名的數控系統廠商也具有較多的研究和應用。
德國SIMENS的高檔數控系統840D、840D sl及最新的SINUMERIK ONE中均集成了小線段程序壓縮器和可編程角度倒圓功能(圖10)。程序壓縮器能夠根據所設的公差帶將行程指令按順序壓縮成一條平滑的、曲率穩定的樣條輪廓,有利于提高系統速度和加速度,從而提高生產率。可編程角度倒圓是通過預讀,對已知尖銳轉角進行圓弧倒角,即不嚴格通過編程角點。
圖10 SIMENS的程序段壓縮和可編程轉角過渡功能
日本FANUC的30i、31i、32i等高檔數控系統推出了智能平滑公差控制功能(圖11)。與SIMENS類似,智能平滑公差控制功能一方面可以根據指定允差平滑連續微小線段指令的加工路徑,提高精加工的質量;另一方面通過指定公差,可實現不同指令間的轉角過渡,包括直線與直線、直線與圓弧、圓弧與圓弧插補的平滑過渡。
a平滑連續小線段 b允差內轉角過渡
圖11 FANUC的智能平滑公差控制功能
同樣,海德漢(HEIDENHAIN)高檔數控系統TNC620、TNC640等也具有類似的功能,如自動控制平滑處理。這些產品化的高端軌跡平滑技術使得以上企業的產品在高性能數控系統領域中占據了絕對的優勢,但其技術實現目前處于保密狀態,一般的專業人員難以深入了解其技術細節。
從以上軌跡平滑的理論研究和實際應用中可以看出。局部構造樣條軌跡和插值擬合軌跡雖然能夠保證嚴格通過特征刀位點,最大程度忠實于CAM軟件生成的編程軌跡,但是對于存在缺陷點的編程軌跡適用性較差,容易發生軌跡變形和異常降速。全局逼近軌跡能夠過濾編程軌跡中的異常波動,甚至對噪點也能夠起到平滑的作用,曲線光順性較好,對于加工速度的提升具有較大意義,但是全局逼近擬合方法需要計算刀位點與逼近曲線的距離,并需要進行多次迭代才能夠提高軌跡的擬合精度,算法耗時較高,對系統軟件硬件性能要求較高,工程應用中的技巧性較強。
然而,從SIMENS、FANUC和HEIDENHAIN所公布的軌跡平滑功能原理簡介中可以看出,其所用的方法均是全局逼近擬合配合局部轉角過渡的方式進行刀具軌跡的平滑處理,因此可以看出該方法對曲面加工優化具有較高的適用性。
**「 **2.曲面加工速度優化方法 」
在曲面加工中,通常速度越高,加工誤差越大。通過降低加工速度來提升精度會影響零件的加工效率。另外,速度的不平穩、加速度突變可能會導致加工表面出現振紋。速度的橫向不連續會引起加工表面刀紋不均勻。因此,在數控系統插補前需要對加工速度進行合理地優化。速度優化需要考慮兩個方面:一方面是確定單條軌跡上各程序段的合理速度,另一方面是保證相鄰軌跡的速度連續性。其中,如何保證相鄰軌跡的速度連續性是速度優化的難點。
目前,在相鄰軌跡連續性速度優化方面的研究主要分為兩類:一類是在數控系統前瞻階段,通過跨相鄰軌跡的大范圍程序段預讀,在確定單條軌跡速度的同時考慮相鄰軌跡的速度連續性;另一類是在離線環境下,通過對全局軌跡的遍歷和迭代,實現相鄰軌跡間的速度連續。
1)系統前瞻速度優化
前瞻是數控系統相對于當前加工的程序段,超前預讀和處理還未加工到的程序段,并將處理后的待加工程序段放入系統緩存中,等待系統的加工。前瞻是保證系統正常運行、提高加工效率和加工精度的關鍵。在前瞻的過程中需要識別降速區域和拐角尖點,并確定降速區域和拐角尖點處的最大加工速度,保證刀具平穩地通過所有刀位點。根據前瞻范圍的不同又可以劃分為兩類:一類是短距離的預讀,僅識別軌跡行進方向的降速區間和拐角尖點,并計算降速速度;另一類是在大范圍程序段預讀的基礎上,不僅對軌跡行進方向的降速區間和拐角尖點進行識別,還能夠建立多條相鄰軌跡的空間鄰近關系,實現加工速度的橫向連續,避免個別軌跡缺陷點導致的異常降速。
有研究認為,降速區間的分界點通常是刀具軌跡中曲率不連續和切向不連續的特征點,如圖12所示。在前瞻中識別出降速區間和拐角尖點后,再對其降速的速度值進行合理地限定,以保證曲面加工精度和效率。在一個降速區間內,加工速度在邊界處快速變化到指定的速度并保證恒定,直到下一個降速區間或拐角尖點的出現。恒定的速度有助于提高加工過程的穩定性,因此這類速度優化方法在一定程度上能夠改善加工表面質量的均勻性。
圖12 降速區間分界點和拐角尖點
然而這類方法也只考慮了行進方向的降速區間和拐角尖點,沒有考慮相鄰軌跡的降速區間和降速尖點的一致性。為了解決這個問題,需要在大范圍前瞻基礎上,利用相鄰軌跡匹配的算法對降速區間和降速尖點進行一致性規劃。如圖13所示,當刀具加工到當前點時,系統最遠前瞻程序段已經跨越了多條軌跡,通過對前瞻軌跡中的刀位點鄰近關系和軌跡形狀進行匹配,使相鄰軌跡的降速區間邊界點和拐角尖點的位置協調一致,并且保證預規劃速度大小的橫向連續。圖中前瞻范圍內的相鄰4條軌跡的速度標記點V1、V2、V3和V4的位置和大小基本保持一致。
圖13 考慮相鄰軌跡的前瞻速度預規劃
西門子、海德漢和FANUC等系統廠家在這方面具有較深入地研究和應用,在系統性能允許范圍內,盡可能多地預讀程序段,然后通過刀位點的鄰近關系和軌跡的形狀匹配,實現相鄰幾條軌跡的降速區間和拐角尖點的速度協調。
西門子840D及以上版本的高端數控系統推出了連續路徑運行功能和優化后的前瞻預讀功能。連續路徑運行功能通過修改局部編程曲線,在軌跡達到平滑后,使得程序段過渡時軌跡速度不會降到很低,盡可能以穩定的速度運行連續的小線段程序。優化后的前瞻預讀功能通過對相鄰銑削軌跡中相似的軌跡特征進行預處理,使相鄰銑削軌跡上的速度保持協調,對任意形狀表面上的往復加工質量均有良好的效果。
海德漢TNC640高檔數控系統的高級動態預測(ADP)功能同樣對預讀能力進行了擴充。在雙向往復銑削路徑中,使進給速度在往復平行路徑中達到“對稱”,并對速度曲線進行特定的平滑。即使對相鄰路徑刀位點分布不均勻的NC程序,也能縮短加工時間,提高表面光潔度。
FANUC 31i及以上版本高端數控系統的AI輪廓控制功能通過預讀程序指令來提前判斷軌跡形狀,自動區分拐角及曲線的特征,并根據機床的機械性能對速度及加速度進行優化,以提高加工效率。該功能強調了系統預讀能力,在預讀時完成軌跡平滑和速度優化任務,其部分系統型號最大預讀程序段達到1000段。
2)離線全局速度優化
在系統前瞻時進行速度優化,能夠在加工的同時進行優化處理,效率較高。然而,受系統實時性的限制,前瞻范圍雖有所增加但仍然有限,只能考慮相鄰幾條軌跡速度的一致性,無法保證全局軌跡速度的橫向連續。
離線全局速度優化是在系統外部的優化軟件中,在不受實時性和內存的限制下,利用復雜度更高的全局遍歷和迭代優化算法,實現加工軌跡的全局速度優化。離線全局速度優化的結果可以通過文件輸入到數控系統,數控系統按照文件中的速度優化結果進行加工,能夠有效避免由于數控程序缺陷和系統實時性限制導致的加工表面缺陷,提高加工質量和加工效率。如圖14所示,離線全局速度優化標記出的降速區間邊界(白色點),在軌跡橫向上形成連續的“特征線”,特征線上所有標記點的速度大小保證一致性或連續性。
圖14 離線全局速度區間優化
研究發現,數控系統的實時數據在插補點曲面上分布的不連續程度與曲面精加工表面質量缺陷之間存在對應關系。
在以上研究的基礎上,通過采集數控系統加工過程中的實時插補數據,利用插補點壓縮算法和曲面重構算法對各信號(如速度、加速度等)在曲面上分布情況進行可視化,利用實時數據的不連續度量化算法對信號的不連續度進行評價,作為曲面加工全局速度優化的參考依據。
在實時插補數據分析的基礎上,有文章提出通過定位每個刀位點在相鄰軌跡上的投影位置,重構刀位軌跡的橫向信息,利用橫向信息查找特征點的候選點,然后篩選候選點以形成特征線,計算特征線劃分的速度區間的邊界速度,并利用平滑算法對橫向速度區間的目標速度進行一致性優化。
離線優化的方式雖然能夠完全地實現全局速度優化,但是由于需要在系統外部進行額外的預處理,操作流程相對復雜,優化結果在不同系統中無法直接復用,因此主要用于對全局表面質量要求較高、單件零件價值較高的復雜零件。
-
高速
+關注
關注
0文章
118瀏覽量
23583 -
運動控制
+關注
關注
4文章
726瀏覽量
33581 -
數控加工
+關注
關注
0文章
61瀏覽量
10537
發布評論請先 登錄
MATLAB曲面擬合問題
復雜曲面零件超精密拋光
龍華模胚加工廠家告訴您模胚加工工序
FSS曲面數字化加工系統及其關鍵技術的研究
基于伸縮因子的代數曲線曲面變形方法
環形刀銑削復雜曲面路徑規劃
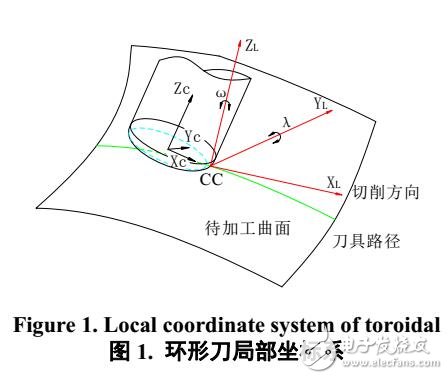
CNC加工中心里面最常用的幾種螺紋加工方法有哪幾種
自由曲面光學元件的三類加工方法
PCBA加工的表面組裝方法有哪些?
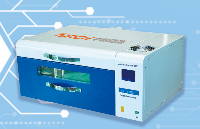
評論