電池工藝
光伏發電原理:
(來源:公開資料)
在解釋原理之前,先解釋下兩個名詞,“電子”和“空穴”
“電子”和“空穴”:
在熱力學溫度零度和沒有外界能量激發時,價電子受共價鍵的束縛,晶體中不存在自由運動的電子,半導體是不能導電的。
但是,當半導體(如硅)收到外界因素(如光照)使溫度升高,某些共價鍵中的價電子獲得了足夠的能量,足以掙脫共價鍵的束縛,躍遷到導帶,成為自由電子,同時在共價鍵中留下相同數量的空穴。電子帶負電,空穴帶正電。
原理:
太陽光照射到光伏電池表面,其吸收具有一定能量的光子,在內部產生處于非平衡狀態的“電子-空穴”對。
在P-N結內建電場的作用下,電子和空穴分別被驅先N、P區,從而在P-N結附近形成與內建電場方向相反的光生電場。
光生電場抵消P-N結內建電場后多余的部分使P、N分區分別帶正、負電,于是就產生N區指向P區的光生電動勢。
當外界負載后,則有電流從P區流出,經負載從N區流入光伏電池。
而電池片環節的主要核心是提升光電轉換效率。
總的來說,晶硅電池經歷了三次技術發展。
1)鋁背場 BSF 電池,在 2015 年之前,它是最主流的電池,市占率超過了 90%。
2)PERC 電池:改進BSF電池,形成了PERC電池。與鋁背場BSF電池相比,其只新增了背面沉積鈍化膜和背面開槽兩道工序。非常便于BSF電池生產線直接升級。
(BSF電池和PERC電池都是基于P型硅的電池)
3)當前(2021年),基于N型硅太陽能電池的發展(N-PERT,TOPCon,HJT),晶硅電池迎來第三次技術革命。
1、BSF電池
鋁背場電池BSF是指在PN結制備完成后,在硅片的背光面沉積一層鋁膜,提高光的反射率從而提高轉換效率。
生產流程包括:清洗制絨(又稱“前清洗”)、擴散制結(又稱“擴散”)、刻蝕/去PSG(Phospho Silicate Glass,磷硅玻璃)(又稱“拋光”)、正面沉積減反膜、背面印刷鋁膜、絲網印刷、高溫燒結。
清洗制絨(前清洗):
由于硅片在切割過程中會產生損傷,且會引入一些金屬雜質和油污。如果損傷和雜質油污清洗不徹底,在后續處理過程中會向硅片內部延伸,影響電池的性能。
因此,清洗制絨的目標有3點:一是用酸液或堿液去除硅片表面的機械損傷層;二是清除表面油污和金屬雜質;三十形成起伏不平的絨面,減小太陽光的反射。
清洗和制絨是一道工序。單晶硅片采用的是堿液腐蝕技術,能夠與硅反應,清洗損傷和雜質的同時能夠在表明形成金字塔絨面結構。
多晶硅片則采用酸液腐蝕,清洗的同時形成蟲孔狀絨面結構。
由于絨面結構的存在,入射光線會經過絨面的多次反射才入射到空氣中,這樣能夠多次利用入射光線,從而減少反射率,增加了光的利用率。
擴散制結(擴散):
即制備太陽電池的 PN 結。(從上面電池的工作原理,我們知道這個非常重要)
對于P型硅片,是要在其表面制備N層,對于N型硅,則要在其表妹制備P層。
P和N硅片的區別主要在于雜質。
N型硅施主雜質主要是如磷、砷、銻等。
P型硅施主雜質主要是如硼、鋁、鎵等。
那么在P型硅表面制備N層,則可以通過在其表妹擴散磷元素來制備。
制備過程簡單描述:
P型硅片放入石英容器,加熱并通入含磷氣體,使容器類充滿含磷的蒸氣。
含磷整齊附著到硅片上可產生磷原子。
由于硅片的原子之間存在空隙,這些磷原子可以從空隙中進入硅片的表面層,并先內部滲透擴散。
若是擴散進去的磷原子濃度,高于P型硅的雜質(比如硼)濃度,則P型硅的表面薄層就轉變成了N型硅。
N型硅和P型硅的交界處就形成了PN結
對于N型硅片,則與之相反,通入喊硼氣體即可。
刻蝕/去PSG(拋光):
在上一步的擴散制結工藝中,硅片的側邊和背面邊緣將不可避免地存在擴散的磷原子,,形成磷硅玻璃PSG。
當電池片受到光源照射,PN結的正面收集到的光生電子將沿著邊緣擴散到有磷的區域,再流到PN結的背面,從而造成短路。
刻蝕工序可去除硅片邊緣帶有磷的部分,避免了PN結短路。
同時可以祛除硅片背面的絨面。
刻蝕工可以分成濕法刻蝕工藝和干法刻蝕工藝。
背面鈍化(PERC 電池工藝):
沉積背鈍化介質膜,分別對硅片背面起鈍化及保護作用,可以增強背面鈍化反射能力。
制備減反射膜(前表面減反膜 ):
在硅片的表面,利用增強型等離子化學氣相沉積法沉積摻氫氮化硅薄膜,以獲得合適的厚度以及折射率,降低表面光反射,同時能夠起到鈍化作用,增加抗腐蝕性。
激光開槽(PERC 電池工藝):
用激光打開硅片背表面鈍化層,從而提取電荷載流子,打通鈍化疊層形成電學通路(用于PERC 電池工藝)
絲網印刷:
將導電銀漿印刷在電池的正背面,形成電極,用于收集和傳輸電流。
正面印刷銀漿正極細柵與主柵,背面印刷電極主柵和鋁背場,其目的是用于電池的電極成形。
高溫燒結:
排出漿料的有機成分,使電極和硅片形成良好的歐姆接觸,實現較小的串聯電阻、較大的并聯電阻和理想的背表面鈍化。
硅片經過絲網印刷機后,會傳送到燒結爐中,經過烘干排焦、燒結和冷卻過程來完成燒結工藝,最終達到上下電極和電池片的歐姆接觸。
高溫燒結的核心過程是:
當電極力的金屬和硅片達到一定溫度時,硅原子會融入到電極材料中。
當融入到電擊材料中的硅原子里含有足量多的與原硅片材料中導電類型相同的雜質成分,就形成了歐姆接觸。
從而可以提高電池片的開路電壓和填充因子,使電極的接觸具有電阻特性,并因此達到較高的轉化率。
若存在的是導電類型不同的雜質成分,則獲得了用合金法工藝形成的 PN 結。
測試分選:
對電池進行 I-V 測試,并按電池的實際效率和電流進行分檔。
總結電池工藝如下:
(來源:天合光能招股說明書)
一個光伏電池看起來是這樣(3主柵:縱向白色線;細柵:橫向白色線):
2、PERC電池
PERC電池全稱:鈍化發射極與背面接觸電池。
原理是在BSF電池背面附上介質鈍化疊層( Al2O3+SiNx),通過產生更多反射光以增加額外電流,從而較大程度減少光電損失。
該技術路線的生產流程主要在常規BSF電池生產環節中增加兩道額外工序。
一是背面沉積鈍化膜(增強背面鈍化反射能力)。
二是背面開槽(打通鈍化疊層形成電學通路)。
無需另開生產線。需要增加的設備是背部鈍化設備和激光開槽設備。
工藝流程在BSF電池上有介紹。
PERC 技術日趨成熟,“PERC+”成為 PERC 工藝升級,提升光電轉換效率的重要方向,PERC 工藝升級路線主要包括 PERC+SE、 PERC+MWT、雙面 PERC 等。
3、TOPCon電池
TOPCon電池,即隧穿氧化層鈍化接觸太陽能電池。
N型硅襯底電池背面制備一層超薄氧化硅,然后再沉積一層摻雜硅薄層,二者共同形成了鈍化接觸結構。
與現有傳統的 P 型電池設備制程相比, TOPCon 電池的生產流程只需將擴磷改為擴硼,并增加薄膜沉積設備,無須背面開孔和對準,便可與當前的量產工藝兼容。
4、HJT電池
具有本征非晶層的異質結(Heterojunction with Intrinsic Thin Layer)——在電池片里同時存在晶體和非晶體級別的硅,非晶硅的出現能更好地實現鈍化效果。
是晶硅太陽能電池技術和薄膜光伏技術的融合體并且兼具兩者的優點
HJT工藝主要分為制絨清洗、非晶硅薄膜沉積、TCO薄膜制備、電極制備,步驟相對簡單,但是工藝難度大,產線與傳統電池不兼容,新增設備投資較大。
5、ICB電池
交指式背接觸(Interdigitated Back Contact)——把正負電極都置于電池背面,減少置于正面的電極反射一部分入射光帶來的陰影損失。
6、PERT
發射極鈍化和全背面擴散(Passivated Emitter Rear Totally-diffused )——PERC 技術的改進型,在形成鈍化層基礎上進行全面的擴散,加強鈍化層效果。
相比于 P-PERC,N-PERT 需要增加硼擴散和清洗步驟,且由于在效率提升方面不及 PERC,已被被證明為不經濟的技術路線。
7、各種電池總結如下
(資料來源:CPIA)
8、各種電池技術平均轉換效率
2020 年,規模化生產的 P 型單晶電池均采用 PERC 技術,平均轉換效率達到 22.8%,較 2019年提高 0.5 個百分點;
采用 PERC 技術的多晶黑硅電池片轉換效率達到 20.8%,較 2019 年提高0.3 個百分點;常規多晶黑硅電池則效率提升動力不強,2020 年轉換效率約 19.4%,僅提升 0.1個百分點,未來效率提升空間有限;
鑄錠單晶 PERC 電池平均轉換效率為 22.3%,較單晶 PERC電池低 0.5 個百分點;
N 型 TOPCon 電池平均轉換效率達到 23.5%,異質結電池平均轉換效率達到 23.8%,兩者較 2019 年均有較大提升。
未來隨著生產成本的降低及良率的提升,N 型電池將會是電池技術的主要發展方向之一。
(資料來源:CPIA)
9、各種電池技術市場占比
2020 年,新建量產產線仍以 PERC 電池產線為主。隨著 PERC 電池片新產能持續釋放,PERC電池片市場占比進一步提升至 86.4%。
隨著國內戶用項目的產品需求開始轉向高效產品,原本對常規多晶產品需求較高的印度、巴西等海外市場也因疫情導致需求量減弱,2020 年常規電池片(BSF 電池)市場占比下降至 8.8%,較 2019 年下降 22.7 個百分點。
N 型電池(主要包括異質結電池和 TOPCon 電池)相對成本較高,量產規模仍較少,目前市場占比約為 3.5%,較 2019 年小幅提升。
(資料來源:CPIA)
隨著成本的主鍵降低,未來N型電池(主要是TOPCon電池,HJT電池(異質電池))將是主要發展方向。
上圖中很明顯。
BSF電池將逐漸被淘汰。
PERC電池在未來一段時間內還是主流。
TOPCon電池和異質結電池(主要指HJT電池)未來將是主要發展方向。
10、電池片金屬化及銀漿技術
(要了解詳細情況請搜索:《深度分析光伏電池片金屬化及銀漿技術》 )
10.1 銀漿成本
金屬化是光伏電池片關鍵工藝之一,主要用于制作光伏電池電極,將PN結兩端形成歐姆接觸,實現電流輸出。金屬化工藝對于電池的可靠性、成本、轉化效率、工藝路線均有較大影響,目前絲網印刷是最成熟且普遍金屬化工藝。
對于各種電池片來說,銀漿成本是僅次于硅片的第二大成本占比。尤其對于TOPCON、HJT技術來說,銀漿成本從PERC的10-11%顯著提升至16%-24%以上,成為限制產業化推廣的重要因素,傳統絲網印刷工藝無法滿足新型高效電池需求,因此探索金屬化的升級優化意義重大。
經分析,金屬化技術升級主要通過兩大途徑:1)采用新型金屬化工藝降低銀漿耗量(可用于PERC、TOPCON、HJT等各技術路線);2)采用國產化、新型漿料材料降低銀漿耗量(銀包銅僅可用于HJT技術)。
1)TOPCON:TOPCON技術對于工藝和設備相較于PERC差異不大,但TOPCON采用高溫雙面銀漿,單片耗量在130-150mg左右,高于雙面PERC的85mg/片耗量。根據TRENDFORCE數據,當前漿料占TOPCON成本15.8%左右,因此如何優化技術化工藝、銀漿漿料成本對于降低TOPCON電池生產成本至關重要。
2)HJT:由于HJT電池采用非晶硅薄膜需要溫度限制在200℃的低溫環境,因此HIT電池通常使用可在低溫下固化的特殊低溫銀漿,較傳統高溫銀漿貴2000元/kg。同時,異質結雙面銀漿的耗量相對于TOPCON進一步提升,當前耗量在250mg/片左右,當前漿料占HJT成本24.3%左右。
10.2 金屬化工藝升級
1)多主柵:提升效率降低銀漿耗量,當前各電池路線主流技術
多主柵技術又稱MBB(Multi-Busbar),通常指主柵線在6條及以上。由于主柵線數量增加能夠使得柵線做的更細,從而減少了電池表面的遮擋;同時縮短了電流在細柵上傳導距離,可有效降低組件的串聯電阻;此外因主柵線及細柵線寬度減少,還能夠顯著降低銀漿耗量。
以 5 主柵電池組件為例,其主柵寬度為 1mm,而多主柵電池組件的主柵可窄至 0.1mm,可大幅降低銀漿耗量。
多主柵技術擁有較強兼容性,可疊加多晶、單晶、黑硅、PERC、TOPCON、HJT、雙面、單玻、雙玻等多項主流技術。同時多主柵技術升級主要體現為組件串焊機設備的更迭,對于電池設備來說變化不大,主要需要絲印設備網版的更換調節,以及分選設備的精準度提升。
因此MBB技術也進一步推動N型電池片的加速滲透,將HJT銀漿耗量從300mg/片降低至200-250mg/片以下。9BB、12BB已經成為當前各技術路線電池金屬化、組件串焊的主流技術,但當前銀漿成本仍然較高,仍需進一步優化金屬化技術。
10.3. 國產化及銀包銅等新型漿料的應用
除了對于金屬化工藝的優化升級,對于銀漿材料本身的降本優化同樣具備較大意義, 降本后的銀漿能夠疊加大多新型金屬化工藝,實現銀漿成本的進一步降低。
漿料的降本優化一方面體現在銀漿的規模化、國產化降低其本身價格,根據索比光伏網,目前國產漿料廠商晶銀新材、帝科股份、常州聚和,以及在國產化投資設廠日本銀漿龍頭KE均在積極推進漿料降價;
另一方面,邁為聯合華晟、鈞石能源積極推進銀包銅等漿料產業驗證,金辰也在聯合上下游積極儲備新型漿料及金屬化技術,也將顯著降低銀漿耗量。
銀包銅的本質在于通過調節漿料中的銀、銅摻雜比例,用低價金屬替代高價金屬從而降低整體的漿料成本。
通過調整漿料中銀的摻雜比例,能夠將銀含量從90%降低至60%上下,甚至更進一步可降低至45%上下,疊加SMBB測算可降低銀漿耗量至65mg/片,甚至可以低于PERC的銀漿耗量
參考資料:
1 公開資料
2 國家標準
3 天合光能招股說明書、和相關公司年報
4 新材料行研筆記
5 中國光伏產業發展路線圖(2020年版)
6 《深度分析光伏電池片金屬化及銀漿技術》
錯別字來不及修改,先發。
文末劃重點。
鄭重說明:文中涉及公司相關是我個人觀點,不作為投資依據。各位需要自行斟酌!!
股市有風險,投資需謹慎!
參考資料來源于網上公開資料,如有侵權,請聯系作者刪除。
更多好公司分享,請關注公眾號:尋找好公司
關注公眾號,能快人一步了解好公司分析和估值。
-
半導體
+關注
關注
334文章
27626瀏覽量
221148 -
晶體
+關注
關注
2文章
1367瀏覽量
35501 -
熱力學
+關注
關注
0文章
43瀏覽量
9322
發布評論請先 登錄
相關推薦
電池片隱裂的原因、如何識別及預防方法
單晶硅電池片的驗收
電池片工藝流程_電池片的種類
光伏電池片焊帶剝離測試標準
AOI對電池片的外觀缺陷和顏色分選
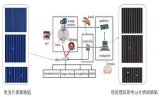
評論