“動力電池成本占到新能源汽車的40%、50%、60%,不斷提價,電池成本占到一部車的60%,那我現在不是在給寧德時代打工嗎?” 2022年,在一個論壇上,廣汽集團高層這樣吐槽。這樣看起來,似乎新能源汽車想賺錢非常難。
但特斯拉2022年財報發布后,筆者發現并非如此。報告顯示,特斯拉全年營業收入814.62億美元,同比增長51.35%,GAAP凈利潤同比翻倍,達到了126億美元,全年營業利潤率為16.8%,毛利率更是達到了28.5%。
以致于2月初的時候,威馬汽車首席數據官(CDO)梅松林在微博上感慨道:“特斯拉單臺車凈利潤是大眾的十倍,這賺錢能力還有誰。特斯拉給傳統汽車行業打了個樣,汽車可以像高科技產品一樣有高利潤。只要特斯拉還想降價,隨時都可以,降價空間還很大。”
實際上特斯拉也是這么做的。
進入2023年,特斯拉宣布國產車型大幅降價,Model 3起售價調整至22.99萬元,Model Y起售價調整至25.99萬元,創下歷史新低。而且不止是中國市場,特斯拉在北美、歐洲等市場也進行了不同程度的價格下調。
馬斯克表示,1月份全球大降價后,訂單量達到了產量的2倍,史上最強勁。2023年,特斯拉生產目標為180萬-200萬輛,期望同比增長37%-50%。
而特斯拉之所以能任性的降價收割訂單,一個核心優勢便是成本。當然這一點幾乎所有的車企都清楚,但他們想要做到卻很難。
▍規模效應帶來的連鎖反應
特斯拉的單車毛利率之所以高,人們首先想到的原因是規模效應。這里我們先了解一個專業術語——最小有效規模。
馬克西-西爾伯斯通在研究了60年代英國的汽車產業后,提出了最小有效規模的概念和曲線,用以描述汽車工業發展過程中的規模經濟問題。最小有效規模,是指企業的平均成本逐漸減少至最低點時所對應的企業最小規模。
根據“馬克西-西爾伯斯通”曲線,隨著年產量的爬坡,單一車型的平均成本會大幅下降,之后下降幅度趨緩,接著將達到最小有效規模MES臨界點。
根據“馬克西-西爾伯斯通”曲線及國外的相關經驗:當小轎車產量由1千輛增加到5萬輛時,單車成本將下降40%;由10萬輛增加到20萬輛,單車成本將下降10%;由20萬輛增加到40萬輛,成本將下降5%。一條發動機生產線的最小有效規模是50萬臺,沖壓設備生產線是100萬套,轎車的規模產量為40萬輛,輕型車為6萬輛,卡車為15萬輛。
在達到最小有效規模前,隨著產量的增加,成本下降幅度會迅速加大。電動汽車的生產過程中,固定資本占的比重大,這也使得產量對單車成本的變化極為敏感。
于是,當特斯拉的季度銷量達到10萬輛、20萬輛、30萬輛時,規模效應的優勢就出來了,單車成本快速走低,單車利率也實現了躍升。
結合以往數據可以看到,特斯拉的季度銷量低于5萬輛時,單車凈利率為負;季度銷量從5萬輛增長至10萬輛時,特斯拉的單車凈利率逐漸開始由負轉正;突破20萬輛時,凈利率實現了從5%到10%的跨越;而當季度銷量突破30萬輛后,單車凈利率隨銷量持續增長,從14.5%飆升到了19.7%。
這種規模效應體現在供應商端,是更高的議價能力。
同樣是零部件供應需求,由于特斯拉采購量更大,能拿到的價格就會更有優勢。就像買菜一樣,買1斤要4塊錢,但買3斤可能只需10塊錢。在131萬輛的年銷量面前,顯然特斯拉在供應商面前有足夠的底氣。
以電池為例,數據顯示,特斯拉在美國市場的電池電芯成本為每千瓦時142美元,通用汽車的成本為每千瓦時169美元,而整個電動車產業的平均值為每千瓦時186美元。與產業均值相比,特斯拉電芯成本低了23.7%。
規模效應的另一好處,是品牌價值的提升。
消費市場有一個例子很有代表性,在燃油車時代,你很難想象汽車主機廠會在品牌層面集體漲價,然而特斯拉可以。近兩年受供應鏈變動影響,造車成本有所上升,特斯拉便曾通過全系漲價來保持利潤率水平。在此之前,這種操作在其他車企看來就是作死,但特斯拉就這么做了,而且后來還能被消費者接受,其背后的深層原因無非是對其品牌價值、產品價值的認可。
再看中國市場的蔚小理,銷量沒有完成2022年年初制定的KPI,毛利率一直在低位徘徊,仍然處于賣一輛虧一輛的狀態,這種背景下,規模效應幾乎無從談起,自然也在成本方面處于優勢。
▍供應鏈本土化的雙贏局面
在新能源汽車領域,特斯拉只有一個,但特斯拉背后的供應商卻成百上千。
加入特斯拉供應鏈,意味著供應商能拿到巨額訂單。而成為特斯拉的供應商,對于不少零部件企業來說,是業界認可的金字招牌,可以提高它與其他汽車企業的議價能力。
從這方面也可以看出特斯拉的品牌附加值。
有了這一環,為了進入特斯拉供應鏈,有些供應商給到的報價就會極低。
更關鍵的是,供應商本土化本身便拉低了特斯拉的單車成本。供應鏈高度本土化,意味著上海超級工廠在材料生產成本、材料運輸成本、關稅成本等方面,都大幅下降。
2022年特斯拉上海超級工廠第100萬輛整車下線時,特斯拉曾表示上海工廠供應鏈本地化率已經超過了95%,電池、整車沖壓模具、車身鈑件、內飾、電子設備等供應商基本都來自本土品牌,這一數字在2019年年底時還只有40%左右。
20萬元價位的新能源汽車市場,本就沒有太多故事和情懷可講,更低的價格、更高的配置、更長的續航才是消費者最看重的因素。特斯拉利用其成本優勢,一次次舉起“屠刀”,價格一降再降,正在將多數新勢力企業一步步逼入墻角。
▍“高研發高回報” 自研技術所帶來的成本縮減
特斯拉的先進技術、在制造環節的創新,也是單車成本更低的關鍵因素。
圈內都知道,特斯拉在技術研發、整車制造創新方面的投入一向是比較豪放的,單車研發費用約為行業平均水平的3倍。
2020年的一項數據顯示,當年特斯拉在研發上的單車平均支出比其他車企都高,單車研發費用2984美元,一臺在北美售價4萬美元的特斯拉,近8%的費用都用在了研發上。
同期,福特的單車研發費用為1186美元,豐田1063美元,通用878美元,克萊斯勒784美元,特斯拉幾乎是行業平均單車研發費用1000美元的近3倍。
研發上的高投入,帶來了非常直接的回報,使得特斯拉的制造和運營成本遠低于行業水平。
比如在芯片方面,特斯拉采用自主設計的車用芯片,較對外采購成本低很多,并且還減少了對供應商的依賴。同時,特斯拉做的許多定制化功能,并不需要考慮芯片通用性,這使得成本進一步下降。
又比如圈內所熟知的一體化壓鑄技術。
特斯拉上海超級工廠,一臺重達410噸的巨型機器“轟隆”一聲響,原來由70多個零件沖壓、焊接而成的Model Y后車架,在不到2分鐘內便被一體壓鑄成型。
壓鑄機器,特斯拉使用了擁有自身技術專利的6000噸鎖模力大型壓鑄機,通過動力擠壓將液態金屬擠壓入磨具,冷卻后形成零部件,一體成型一步到位。其實這項工藝很早前就有,特斯拉的創新性在于,將一體壓鑄的應用范圍從小部件,拓展到了大體積結構件。
好處顯而易見,Model Y后車架變成了一個整體,制造時間從1-2小時縮短至45秒-2分鐘,制造過程減少了300臺機器人,同時縮短了生產線,節省了30%的占地面積。
車輛減重10%和15%,可以分別減少6.3%和9.5%的能量損耗,相應地,一體化壓鑄技術加持下的車體總成,重量能降低30%,新技術所帶來的節能效果相當可觀。
工廠勞動力上,主流汽車工廠焊裝車間一般需要配200-300名工人,一體式壓鑄車間只需要20-30名,特斯拉稱一體化壓鑄技術給Model Y節省了約20%的制造成本。
未來特斯拉還計劃將前車架&座艙、地板&電池殼也采用一體化壓鑄工藝,如果這些全部實現,就能代替原本370多個零部件的沖壓焊接,整車減重10%,續航提升14%。
高投入高回報,技術上的優勢,幫助特斯拉在競爭中,始終掌握著自己的“命門”。
▍4680電池革命
純電動汽車的瓶頸在哪兒?當然是動力電池。特斯拉給出的下一代解決方案是4680電池。這種電池直徑為46毫米,高度80毫米,因此得名。2020年9月,4680電池一經發布就震驚了整個行業。
相比于現今的2170電池,4680電池的容量是它的5倍,輸出功率提升了6倍,成本下降了56%。特斯拉介紹,4680電池采用高鎳正極+硅碳負極材料,以及無極耳技術,能量密度達300Wh/kg,搭載4680電池的電動汽車續航里程可以提高16%。
好消息是,近來特斯拉在社交平臺表示,4680大型圓柱電池的量產取得了重大突破,加州弗里蒙特工廠已經生產了86.8萬顆大圓柱型電芯,能夠滿足1000輛Model Y裝車。2023年,4680電池或將迎來批量化生產裝機。
特斯拉的長期目標,是讓內部生產的電池遠遠超過10億千瓦時,并繼續使用其他電池供應商。據了解,松下版4680電池將于今年3月投產,LG版4680電池將于今年下半年投產。
未來,除了Model3,特斯拉全部車型都會采用或部分采用4680,尤其是高性能版、長續航版、Cybertruck和Semi。預計2025年特斯拉4680車型銷量有望達到121萬輛,對應電池裝機量約178GWh,到時車輛滲透率接近30%,2022-2025年特斯拉4680裝機量的復合增速高達186%。
寫在最后:
總體來看,特斯拉目前所具備的優勢是綜合性的,單車成本低只是直觀結果,原因則是特斯拉的規模優勢、技術壁壘、大筆研發,行業先行者的優勢+持續的技術創新,讓特斯拉有了品牌溢價,降價后的低價策略也能使其實現了更大的規模效應,再度反哺研發與技術,開始了良性循環。
當然,具備類似規模、技術和研發優勢的還有中國品牌比亞迪,所以便有了“絕代雙雄”的新能源市場頭部格局。
對于特斯拉的造車成本,你有什么想說的?歡迎留言討論。
審核編輯 :李倩
-
動力電池
+關注
關注
113文章
4533瀏覽量
77618 -
汽車行業
+關注
關注
0文章
305瀏覽量
15361 -
特斯拉
+關注
關注
66文章
6311瀏覽量
126551
原文標題:特斯拉的造車成本,為什么比同行低那么多?
文章出處:【微信號:e700_org,微信公眾號:汽車工程師】歡迎添加關注!文章轉載請注明出處。
發布評論請先 登錄
相關推薦
LoRa/LoRaWAN模組,型號那么多,怎么選?
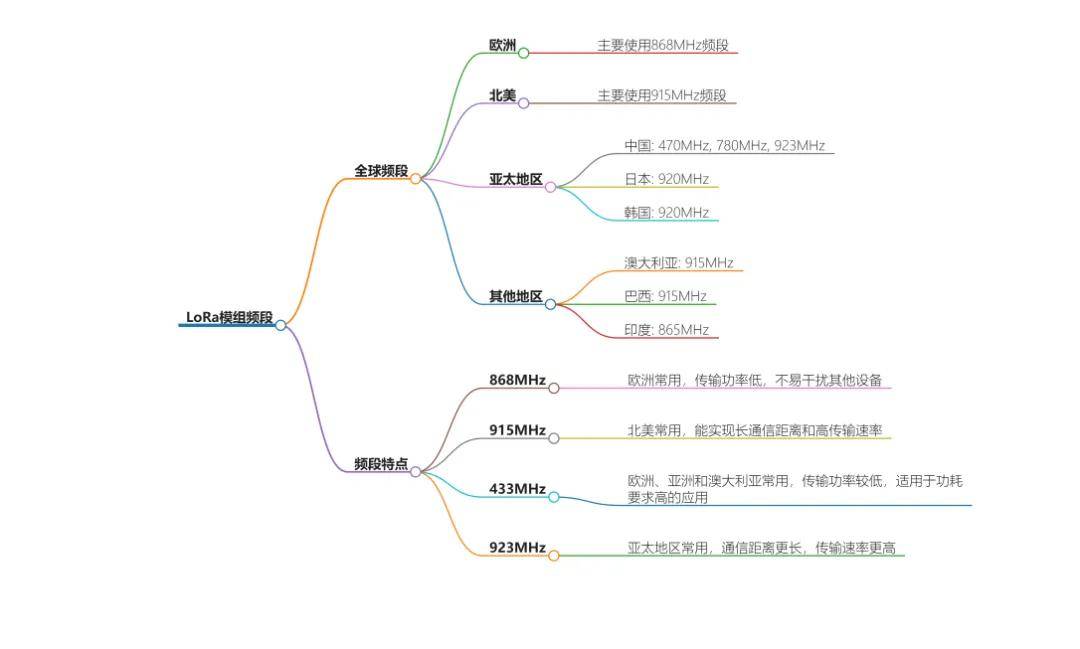
TLV320AIC3104內置ADC實現MIC數據采集的準確度,為什么Codec測得的數據比原始信號要大那么多?
為什么total noise在1K左右的位置INA118比INA333多出那么多倍不是更低的噪聲嗎?
INA301為什么在共模信號給到5V多一點點的時候,偏置電流會突然變大那么多?
特斯拉線圈的疑惑
蘋果造車之路的曲折與華為的魄力
為什么那么多PCB設計師,選擇鋪銅?非鋪不可?
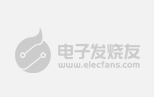
為什么那么多PCB設計師,選擇鋪銅?非鋪不可?
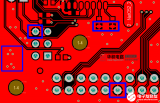
評論