隨著電子技術的不斷進步,散熱問題已經逐漸成為限制功率型電子產品朝著大功率與輕型化方向發展的瓶頸。在功率型電子元器件的封裝應用中,散熱基板不僅承擔著電氣連接和機械支撐等功能,更是熱量傳輸的重要通道。對功率型電子器件而言,其封裝基板應具有較高的導熱性、絕緣性與耐熱性,以及較高的強度和與芯片相匹配的熱膨脹系數。目前市面上常見的散熱基板以金屬基板( MCPCB)和陶瓷基板為主。MCPCB因受制于導熱絕緣層極低的導熱系數,已經越來越難以適應功率型電子元器件的發展要求。陶瓷基板作為新興的散熱材料,其導熱率與絕緣性等綜合性能是普通MCPCB所無法比擬的,而陶瓷基板表面金屬化是決定其實際應用的重要前提。
1
陶瓷表面金屬化研究現狀
表面金屬化對陶瓷基板的制作而言是至關重要的一環,這是因為金屬在高溫下對陶瓷表面的潤濕能力決定了金屬與陶瓷之間的結合力,良好的結合力是 LED封裝性能穩定性的重要保證。因此,如何在陶瓷表面實施金屬化并改善二者之間的結合力成為眾多科技人員研究的重點。目前,陶瓷表面常見的金屬化方法大致可以分為共燒法( HTCC 和 LTCC) 、厚膜法( TFC) 、直接敷銅法( DBC) 、直接敷鋁法( DBA) 及薄膜法( DPC) 等幾種形式。
共燒法(HTCC /LTCC)
共燒多層陶瓷基板因利用厚膜技術將信號線、微細線等無源元件埋入基板中能夠滿足集成電路的諸多要求,在近幾年獲得了廣泛的關注。共燒法有兩種,一種是高溫共燒( HTCC) ,另一種是低溫共燒( LTCC) ,兩者工藝流程基本相同,主要生產工藝流程均為漿料配制、流延生帶、干燥生坯、鉆導通孔、網印填孔、網印線路、疊層燒結以及最后的切片等后處理過程。共燒陶瓷基板在增加組裝密度、縮短互連長度、減少信號延遲、減小體積、提高可靠性等方面具有顯著的優勢。
厚膜法(TFC)
厚膜法是指采用絲網印刷的方式,將導電漿料直接涂布在陶瓷基體上,然后經高溫燒結使金屬層牢固附著于陶瓷基體上的制作工藝。
TFC 燒結后的金屬層厚度一般為 10 ~ 20 μm,最小線寬為 0. 1 mm。由于技術成熟,工藝簡單,成本較低,TFC 在對圖形精度要求不高的 LED 封裝中得到一定應用。同時,TFC 因存在著圖形精準度低( 誤差為± 10%) 、鍍層穩定性易受漿料均勻性影響、線面平整度不佳( 3 μm 以上) 及附著力不易控制等缺點,使其應用范圍受到了一定的限制。
直接敷銅法 (DBC)
DBC 是在陶瓷表面( 主要是 Al2O3 和 AlN) 鍵合銅箔的一種金屬化方法,它是隨著板上芯片( COB) 封裝技術的興起而發展出來的一種新型工藝。
雖然 DBC 在實際工程運用中存在許多優勢,但同時也存在如下不足: ( 1) DBC 工藝需要在高溫條件下引入氧元素使Cu 與 Al2O3 發生共晶反應,對設備和工藝控制要求較高,基板制作成本較高; ( 2) Al2O3 與 Cu 層之間容易產生微氣孔,基板抗熱沖擊性能會受影響; ( 3) DBC 表面鍵合銅箔厚度一般在 100 μm 以上,表面圖形最小線寬一般大于 100 μm,不適合精細線路的制作。
薄膜法(DPC)
薄膜法是主要采用物理氣相沉積( 真空蒸鍍、磁控濺射等) 等技術在陶瓷表面形成金屬層,再采用掩膜、刻蝕等操作形成金屬電路層的工藝過程。其中物理氣相沉積是最常見的薄膜制造工藝。
與其他陶瓷表面金屬化方法相比,DPC 工藝操作溫度低,一般在 300 ℃以下,降低了制造工藝成本,同時有效避免了高溫對材料的不利影響。DPC 不僅降低了封裝體積,還能有效提高封裝集成度。DPC 陶瓷基板雖具有上述諸多優點,但是也存在著諸如電鍍沉積銅層厚度有限,且電鍍廢液污染大、金屬層與陶瓷間的結合強度較低,產品應用時可靠性較低等不足。
直接敷鋁法(DAB)
直接敷鋁法是利用鋁在液態下對陶瓷有著較好的潤濕性以實現二者的敷接。當溫度升至 660 ℃ 以上時,固態鋁發生液化,當液態鋁潤濕陶瓷表面后,隨著溫度的降低,鋁直接在陶瓷表面提供的晶核結晶生長,冷卻到室溫實現兩者的結合。
DAB 陶瓷基板熱穩定性良好,與同結構的 DBC 相比質量可減輕 44%,鋁線鍵合能力佳,鋁/陶瓷之間的熱應力也相對較小,近年來發展迅速。Al2O3-DAB 基板及 AlN-DAB 基板具有優異的導熱特性、良好的抗熱震疲勞性能、出色的熱穩定性及結構質量輕和良好的鋁線鍵合能力。
2
陶瓷金屬化的應用
電力電子領域
電力電子技術是現代高效節能技術,是弱電控制與被控制強電之間的橋梁,是在非常廣泛的領域內支持多項高技術發展的基礎技術。電力電子技術發展的基礎在于高質量器件的出現,后者的發展又必將對管殼提出更高更多的要求。
在射頻/微波領域,氮化鋁陶瓷基板具有其它基板所不具備的優勢:介電常數小且介電損耗低、絕緣且耐腐蝕、可進行高密度組裝。其覆銅基板可應用于射頻衰減器、功率負載、工分器、耦合器等無源器件、通信基站(5G)、光通信用熱沉、高功率無線通訊、芯片電阻等領域。
新能源汽車領域
繼電器是僅次于電子傳感器在汽車產品上應用最多的汽車電子元器件之一,其廣泛用于控制汽車啟動、空調、燈光、油泵、通訊、電動門窗、安全氣囊以及汽車電子儀表和故障診斷等系統,繼電器所用的陶瓷金屬化其部分產品見圖3。
圖3(a) 陶瓷繼電器外殼,(b)陶瓷密封連接器
陶瓷殼體絕緣密封高壓高電流電路斷閉產生的火花并連接電源,高壓直流繼電器帶載開斷時,產生電弧,由于受到陶瓷的冷卻和表面吸附作用,使電弧迅速熄滅。杜絕汽車電路因電弧引發的短路起火,保證整車的安全性能和使用壽命。
IGBT領域
圖4 (a)覆銅基板,(b) IGB斯T模塊內部結構
目前,國內高鐵上IGBT模塊,如圖4(b)所示,主要使用的是由丸和提供的氮化鋁陶瓷基板,隨著未來高導熱氮化硅陶瓷生產成本的降低,或將逐漸替代氮化鋁。氮化硅陶瓷覆銅板因其可以焊接更厚的無氧銅以及更高的可靠性,在未來電動汽車用高可靠功率模板中應用廣泛。美國羅杰斯公司生產的氮化硅覆銅板已應用于電動汽車上的IGBT模塊。
LED封裝領域
圖5 AIN基本覆銅在LED領域應用
氮化鋁陶瓷基板由于其具有高導熱性、散熱快且成本相對合適的優點,受到越來越多的LED制造企業的青睞,廣泛的應用于高亮度LED封裝、紫外LED等。LED封裝用陶瓷基板因其絕緣、耐老化、可在很小單位面積上固裝大功率芯片,擁有了小尺寸大功率的優勢。圖5示出氮化鋁覆銅板及在LED領域中的應用。
審核編輯 :李倩
-
集成電路
+關注
關注
5389文章
11576瀏覽量
362388 -
大功率
+關注
關注
4文章
513瀏覽量
32945 -
銅箔
+關注
關注
5文章
220瀏覽量
16344
原文標題:陶瓷表面金屬化方法及應用領域
文章出處:【微信號:中科聚智,微信公眾號:中科聚智】歡迎添加關注!文章轉載請注明出處。
發布評論請先 登錄
相關推薦
CBB金屬化薄膜電容器應用的優勢是什么
pcb板和陶瓷金屬化產品對比分析
了解金屬化陶瓷基板無銀AMB銅技術粘合的高度可靠性
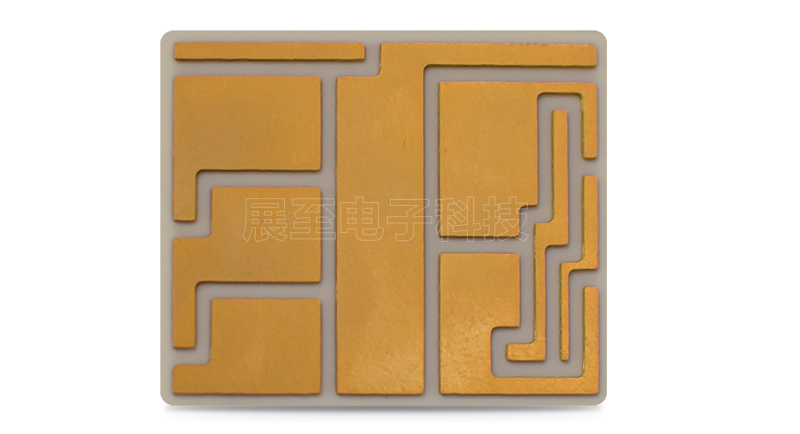
微波介質陶瓷濾波器的低溫陶瓷金屬化工藝
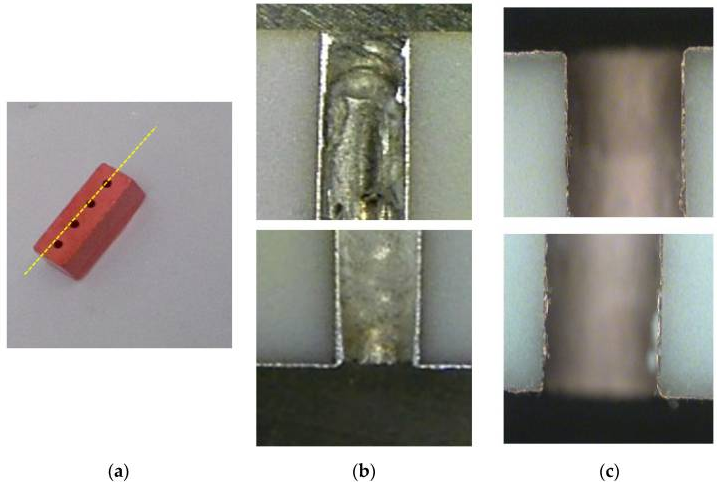
評論