引言
顆粒污染是許多行業產量損失的主要原因,精密的光學表面需要盡可能地不含污染顆粒。半導體制造對其清洗過程(晶片清洗)提出了最嚴格的要求。在加工過程中由化學反應引入的顆粒,或通過人工或自動晶圓處理沉積的顆粒,隨后可以屏蔽光刻復制,導致氧化引起的堆積故障,并導致短路和開路。在制造最先進的集成電路的過程中,也必須控制薄膜和離子污染。
在典型的超聲波頻率(40-100 kHz,用于其他行業中較不關鍵的部件)下清洗在半導體制造中不是最明智的選擇,因為相關的空化內爆會造成表面損傷。然而,英思特半導體公司研究發現0.8至0.9 MHz范圍內的聲波清洗(稱為“大電子”清洗)可以有效去除表面污染物而不會造成損害。英思特得出的結論是,在超電子頻率下,波道之間沒有足夠的時間來形成空腔和內爆發生。
實驗與討論
在40~862 kHz的多個頻率下測量了顆粒去除效率。在沉積前,使用SC1(1氫氧化銨:1過氧化氫:5水)浴清洗晶片,并使用PMS激光表面掃描儀(0.1μm分辨率)進行掃描,以建立背景粒子計數。在聲波清洗前后的粒子數中,從晶片上的粒子總數中減去這個未知來源的粒子數。用0.1μm過濾空氣的噴霧器霧化,并沉積在晶片上。每個晶圓片上大約沉積了150到300個顆粒,導致預清洗前的顆粒計數相對較低(1.1-2.4個顆粒/cm2)
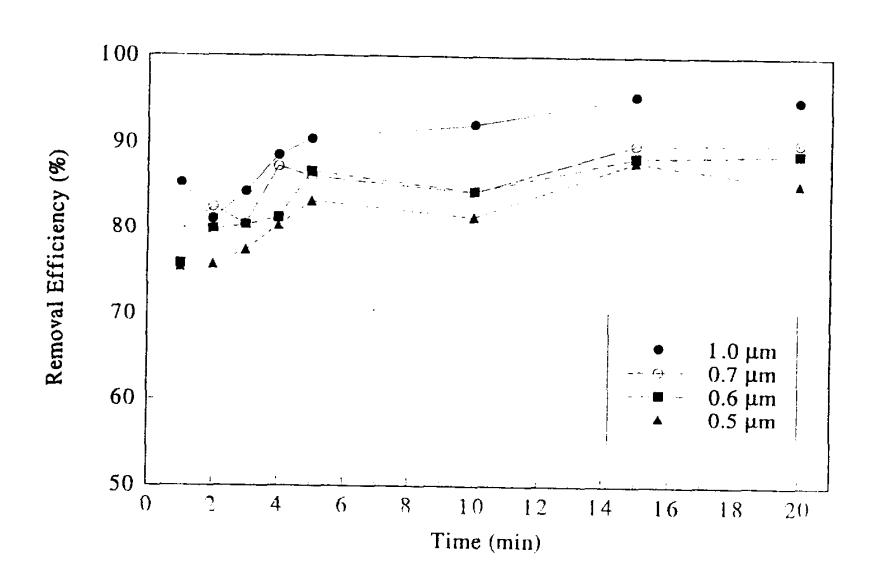
圖1、2和3分別顯示了PSL、二氧化硅和氮化硅顆粒在去離子水中去除效率的。數據采集于862 kHz,對傳感器的功率為150 W。結果表明,在幾乎所有情況下,去除效率都隨著粒徑的增加而提高。此外,雖然對二氧化硅和PSL的去除效率相當,但對氮化硅顆粒的去除效率明顯較低。
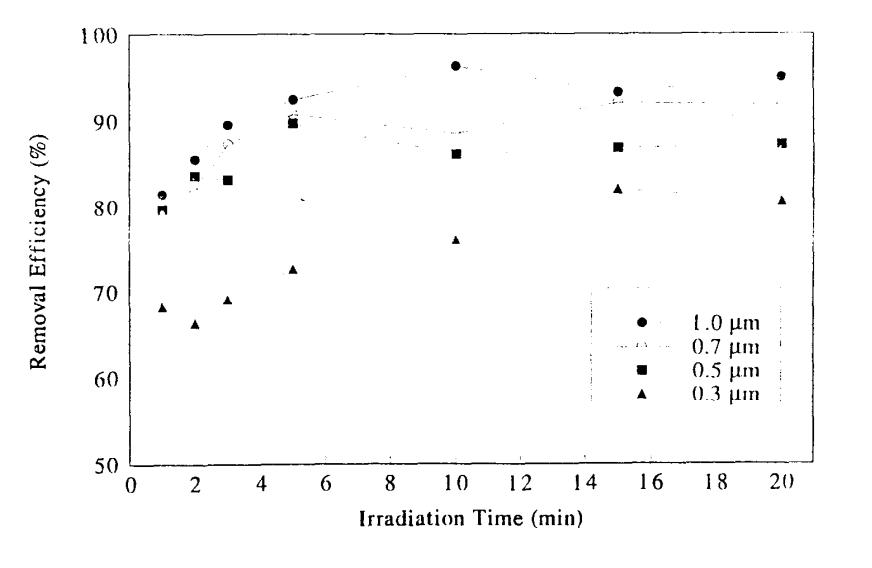
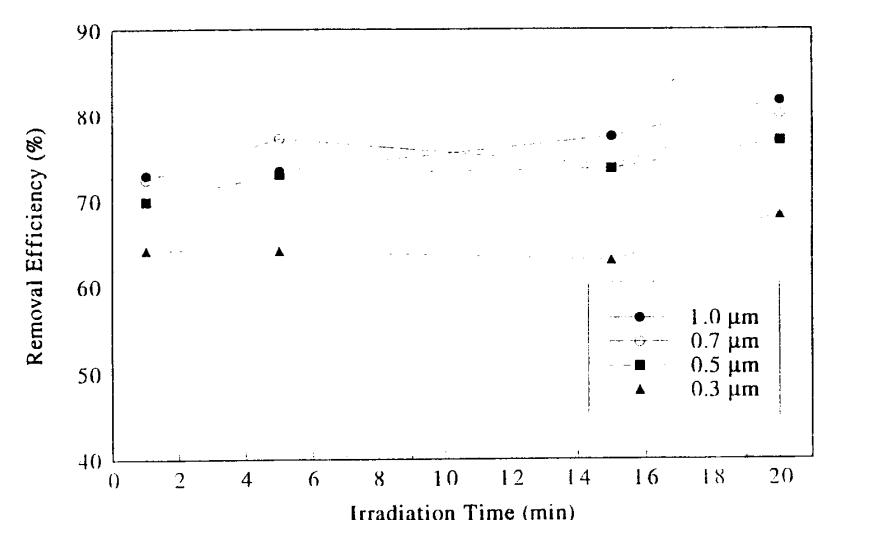
結論
硅片清洗已經是半導體制造中的一項關鍵技術,隨著電路尺寸的減小,它也越來越重要。雖然非常有前途,但聲波清洗過程在傳統上還沒有被很好地理解。本文通過理論和實驗來闡明表面粒子的基本原理。英思特目前的研究在聲波清洗中進一步優化了操作參數。此外,由于SC1溶液的小規模蝕刻行為,硅晶片表面的微裂化是目前關注的一個領域,因為它對隨后沉積的薄膜有有害影響。為了最大限度地清潔,同時最小化粗化的研究正在進行中。
江蘇英思特半導體科技有限公司主要從事濕法制程設備,晶圓清潔設備,RCA清洗機,KOH腐殖清洗機等設備的設計、生產和維護。
審核編輯黃宇
-
半導體
+關注
關注
334文章
27292瀏覽量
218104 -
超聲波
+關注
關注
63文章
3014瀏覽量
138350 -
超電子
+關注
關注
0文章
2瀏覽量
5304
發布評論請先 登錄
相關推薦
超聲波液位計的工作原理 超聲波液位計與其他液位計的比較
超聲波和次聲波的頻率范圍和應用
超聲波測速的原理、方法及應用
超聲波震動清洗的結構原理與特點
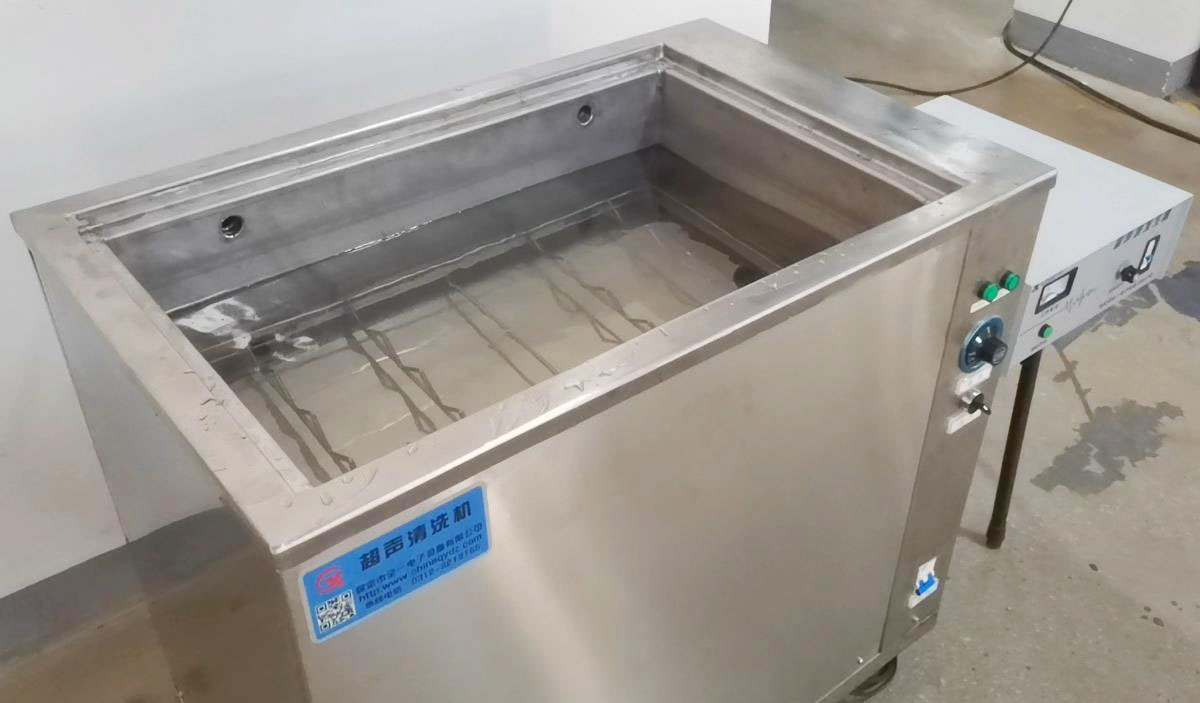
評論