研究背景
鋰離子電池(LIBs)電池的應用激增,在可預見的未來電池壽命為8?10年后,最終將導致大量消耗。對這些廢電池的處理不當可能會引起人們對安全和環境污染的嚴重擔憂。此外,電動汽車市場的快速擴張需要越來越多的原材料和資源,如鋰、鈷、石墨、銅和鋁,這也導致了材料短缺和價格上漲。因此,電池的回收對于減輕資源的限制和潛在的危害是至關重要的和必不可少的。除了這些最終使用壽命壽命外,電池電極碎片在電池制造過程中不斷產生(~10%),這也不容忽視。
與廢棄的鋰電池不同,電極廢料具有其獨特的優勢,如不需要拆卸電池、完整的活性材料和完全已知的化學成分,因此是一種價值更高的資產,需要高效回收利用。 目前,主要的回收方法包括商業上可獲得的法法和濕法冶金方法和直接回收方法,主要是在實驗室開發的方法。焦法冶金的重點是通過高溫碳熱還原(超過1400℃)回收高價值金屬,其中鈷、鎳和銅作為合金收集,而石墨和其他材料通常以礦渣、燃料或還原劑的形式燃燒,并有嚴重的廢氣排放。在濕法冶金術中,廢電池中有價值的金屬被浸出并溶解到混合溶液中,然后通過復雜的化學過程沉淀并分離成純金屬鹽。此外,從廢過的LIB陽極中回收1公斤石墨的廢水高達幾噸,導致污染和危害增加。相比之下,直接回收的目的是收集活性材料,收集到的材料可以通過修復結構缺陷進行再生以供電池應用,或轉化為其他高價值的功能材料。因此,直接回收是電池回收的一種理想途徑,電池消耗少、耗時短,回收污染低、經濟價值高的材料。
然而,在直接回收中,獲得活性材料首先需要電極材料與集電器有效分離(即材料回收),這是由于強大的粘結劑和卷密致密電極而困難的。此外,回收材料的質量和以下所有處理(即材料再生)都強烈依賴于分離的有效性。粉碎電池或電極,然后進行篩分是一個成熟的材料回收過程;不幸的是,這種回收材料的收率總是很低,而且含有大量的金屬雜質。7 wt%銅在石墨中。實驗室開發了幾種更好的分離方法,如管式爐退火、電化學分離、超聲輔助酸洗滌、低溫熔鹽法等。它們通常獲得含有較少雜質的可回收的活性物質。然而,由于效率、經濟效益或可伸縮性有限,許多這些分離方法仍然不適合工業采用。
成果簡介
近日,華中科技大學黃云輝教授&浙江大學陸俊教授在本文報告了通過沖擊式加熱(1500℃,1 s)或連續滾動加熱(~ 5 m/min)對> 97%回收率和~100%完整金屬箔的電池材料的瞬時回收,從而顯示了極高的能量、時間和材料效率。此外,熱模擬和原位質譜表明,電極的溫度分布是空間均勻,粘結劑網絡可以有效地分解為氣體和非晶碳涂層。超短的煅燒時間對電池材料的影響最小,從而有利于簡單和有效的再生。文章演示了來自不同公司的負極、各種正極的一般回收,特別是電池碎片,這些電池碎片可以在卷對卷設備中連續和自動地回收。與濕法冶金相比,EverBatt分析顯示,瞬態電池回收顯著降低能源和碳足跡(~50X減少),接近零廢物產生,和更高的利潤(甚至4.78$/公斤的負極),從而使其實用的直接回收電池材料具有杰出的效率、可持續性和可擴展性。
研究亮點
通過沖擊式加熱(1500℃,1 s)或連續滾動加熱(~ 5 m/min)對> 97%回收率和~100%完整金屬箔的電池材料的瞬時回收。
粘結劑網絡可以有效地分解為氣體和非晶碳涂層。超短的煅燒時間對電池材料的影響最小,從而有利于簡單和有效的再生。
不同的負極、各種正極都可以進行回收,特別是電池碎片,這些電池碎片可以在卷對卷設備中連續和自動地回收。
瞬態電池回收顯著降低能源和碳足跡(~50X減少),接近零廢物產生,和更高的利潤(甚至4.78$/公斤的負極),從而使其實用的直接回收電池材料具有杰出的效率、可持續性和可擴展性。
圖文導讀
在這里,文章報道了一種基于瞬態加熱的干燥、可擴展和快速的直接循環利用廢電極的方法,這可以通過沖擊式加熱(如1500℃,1 s)或連續滾筒加熱(如1500℃,~5 m/min,圖1a)來實現。以廢舊負極為例,將電極片在高溫下快速煅燒,以分解粘合劑(苯乙烯-丁二烯橡膠,SBR)。負極石墨顆粒可以很容易地與銅集電極分離,可以得到98.7%和~100%完整的Cu箔(圖1b)。與濕法冶金方法相比,瞬態循環具有顯著更高的能量和時間效率(減少50-900倍),并產生高純度的材料(雜質減少10倍),以及最小的廢物產生和碳足跡(圖1c)。此外,瞬態回收方法一般適用于來自不同電池公司的各種負極、正極,特別是可以以滾動方式回收的電池廢料,使其能夠直接回收效率高、可擴展性和可持續性的電池材料。
圖1.(a)通過翻轉加熱的銅箔瞬態回收示意圖。(b)在分離前后的負極。(c)濕法冶金和瞬態回收方法中材料回收過程的能量輸入和工藝時間,以及回收石墨中銅雜質的含量。
圖2顯示了石墨負極循環利用的沖擊式加熱過程。在整個過程中,使用碳化紙作為平臺,通過電焦耳加熱誘導高溫沖擊式加熱。如圖2a所示,溫度曲線顯示了一個尖峰狀的加熱過程,其中加熱器的最高溫度在一秒鐘內接近1500℃。短時間加熱方法的一個獨特特點是促進粘合劑的快速分解和降解,同時避免可能的材料變質和元素擴散。用掃描電鏡分析的方法研究了沖擊型加熱過程前后石墨的形貌。直接從廢負極上刮取廢石墨(SG)片,用于掃描電鏡表征。如圖2b所示,SG的表面很光滑,并涂有一層果凍層和顆粒,這應該是粘結劑和導電顆粒。
經過高溫沖擊式加熱(1500℃,1 s)后,石墨層從銅收集器中剝離,我們得到的石墨顆粒(HTG)顯示,顆粒之間沒有果凍層連接,表明粘合劑的熱解。為了研究瞬態加熱過程中材料的物質演化,采用熱解-氣相色譜/質譜(Py-GC/MS)分析了SG的瞬態加熱過程,具有相似的熱解條件(加熱速率為2000℃/s)。圖2c中的總離子色譜顯示了五種主要化合物:磷酰氟、異戊二烯、甲苯、苯乙烯和碳酸乙烯(EC)。磷化氟來自于LiPF6的熱解。EC是電解質中的一種溶劑,在石墨顆粒表面被吸收。
其他三種物質(異戊二烯、甲苯和苯乙烯)是由含有苯環或烯烴鍵的SBR分解產生的。粘合劑的分解可以通過FT-IR測量來驗證(圖2d)。與廢石墨(SG)在與有機官能團相關的400 ~ 2000 cm-1范圍內包含多個吸附峰相比,這些峰在高溫石墨(HTG)中消失,表明在快速處理過程中,盡管持續時間較短,但粘合劑完全分解。 瞬態加熱的另一個優點是整個電極厚度的加熱均勻性,這對于粘合劑的完全熱解和所獲得的材料的有效剝離非常重要。因此,我們進行了傳熱分析,并利用接近真實情況的參數模擬了熱解過程中沿厚度方向的溫度分布(圖2e-g)。如圖2e所示,電極的布局為夾心結構,石墨厚度為61 μm,銅箔厚度為10 μm,與我們的電極樣品相同。
在加熱器和電極之間設置了一個10 mm的間隙來模擬加熱過程。熱輻射、傳導和自然對流都是考慮了從加熱器到陽極電極的傳熱過程(詳見實驗部分)。圖2f中所示的電極溫度在整個電極材料中呈相當均勻的空間分布。在加熱器瞬態加熱到1500℃時,電極溫度快速上升到最高溫度1260℃,電極內的溫度分布均勻(圖2g)。溫度分布的均勻性可以歸因于銅和石墨的高導熱系數,而薄電極的總厚度只有132 μm。
圖2. 沖擊式加熱過程中的過程分析和結構演化。(a)沖擊式加熱的溫度分布。(b)沖擊型加熱處理前后廢石墨的(b)掃描電鏡圖像。(c)SG在Py-GC/MS中熱解的總離子色譜,顯示了粘合劑分解的成分。SG和HTG的(d) FTIR光譜。(e)熱模擬模型的說明和模型的空間配置。(f)1s時的溫度-距離曲線通過負極厚度的溫度分布具有優越的均勻性。(g)在距離加熱器不同距離下加熱1500℃,1 s的模擬三維溫度曲線。
經過沖擊型加熱后,我們得到了HTG粒子。雖然瞬態循環過程對HTG顆粒的影響最小,但這些顆粒仍然含有電解質和分解的粘合劑中的雜質,有些顆粒表面損壞,會降低其電化學性能。因此,需要適當的再生來恢復其結構和性能。再生過程如圖3a所示,這是從天然石墨生產的電池級石墨中獲得的。HTG首先在室溫下用2M硫酸純化1小時,以去除表面雜質。用純水洗滌干燥后,純化的石墨涂上聚丙烯腈(PAN),在1100℃的Ar氣體中熱解,得到具有無定形碳涂層的再生石墨(RG)。使用這些商業的工藝可以在很大程度上確保我們的HT石墨顆粒可以被視為石墨生產的原材料,作為一個可持續的石墨供應。
除了廢負極外,電池制造過程中產生的負極廢料也很容易通過瞬態回收收集。負極廢料的優點是石墨顆粒完整,不需要再生。通過電感耦合等離子體分析來測定元素的含量和雜質(圖3b)。在SG中,Cu最初是由電極集流器引入的,而鋰應該來自電解質(LiPF6)或反應副產物(如SEI,其他死lithium)在長時間的充放電循環過程中,少量的鋁和鐵可能來自正極。經過沖擊型加熱后,HTG的雜質保持相似,這表明雖然使用了高溫,但持續時間很短,原子的擴散在很大程度上僅限于產生進一步的雜質。
相比之下,通過濕法冶金的機械破碎(機械破碎G)獲得的石墨中的Cu雜質高達72100 ppm,10個HTG的量(7122 ppm)。由于硫酸可以溶解大部分雜質,包括SEI層(無機化合物如LiF/Li2CO3)和元素金屬顆粒,經過硫酸純化后,Li、Cu、Fe和Al的雜質含量急劇下降到幾個ppm。回收的廢石墨(廢G)即使沒有凈化,也很少有雜質,注意HTG中的鋰含量很少,但也可以在再生之前回收。 SG、HTG、RG和Scrap G樣品的x射線衍射(XRD)如圖3c所示。它們都具有六方石墨的特征峰,如(002)、(100)、(101)、(004)和(110)(JCPDS no. 00-012-0212)。我們還測量了HTG的粒徑分布,它在3 ~ 20 μm的范圍內,與新的商業石墨(CG)相當,表明了類似的制造兼容性。這些特征表明,SG在長期循環后仍保持層狀結構(體相),直到電池報廢,沖擊式加熱沒有引起相的變質或石墨尺寸的變化。
此外,我們還測量了SG和HTG的拉曼光譜。HTG的平均ID/IG比值為0.4,略大于SG的0.34,說明HTG的結構更為無序,可能來自于粘合劑分解產生的表面附著的非定形碳。進一步的透射電鏡圖像顯示,經過沖擊式加熱后,石墨表面出現了~尺寸為100nm的小顆粒,在電子束輻照下不穩定,逐漸消失。因此,表面納米顆粒要么應該是粘合物中的熱解碳,要么應該是電解質中的無機產物(如LiPF6和五氟化磷)。以上結果表明,雖然SG和HTG的體層狀結構保持良好,但由于表面缺陷,其石墨化程度有所降低(圖3d)。
在高分辨率透射電子顯微鏡下觀察了SG、HTG和RG的晶體結構。SG和HTG表面周圍的(002)晶面的石墨層間距離分別為0.361和0.337 nm。SG在表面的層間距離越大,說明長時間循環后結構破壞越小,而HT石墨層間距離的減小意味著沖擊型加熱后石墨結晶度的提高。這種緊湊的層間結構被繼承下來,并在RG(0.335 nm)中略有下降,表明石墨結構的再生和恢復。為了進一步驗證回收和再生過程的有效性,我們對不同石墨樣品的電化學性能進行了評估,包括SG、HTG、RG和ScrapG(圖3e-g)。
此外,還以CG作為對照樣品。由于去除雜質和通過表面涂層修復結構,在RG中恢復了電化學性能。圖3e總結了不同樣品的初始庫侖效率(ICE),RG和Scrap G比SG有更高的ICE,由于SEI的形成,略低于CG的90%。圖3f中也列出了1、50和100個循環的比容量,其中RG顯示出與CG相當的容量,并表現出良好的循環穩定性(額外180個循環后>保留98%)(圖3g)。此外,RG的速率性能(圖S13b和c)和電化學阻抗譜與CG相當,優于SG。上述電化學性能表明,RG的性能與CG相當,因此,回收的HTG可直接用于再生后的電池生產,或作為電池級石墨生產的原料,以延長石墨的使用壽命。更重要的是,電池廢料具有完整的材料,而且性能最高,不需要再生。
圖3. 再生和電化學性能。(a)從廢負極和負極廢料中提取石墨顆粒的工藝流程。(b)機械破碎G、SG、HTG、RG和廢料G中不同元素的含量SG、HTG、RG和廢G的(c) XRD模式HTG和RG的(d) SEM圖像。(e)初始庫侖效率,以及(f)CG、SG、HTG、RG和廢料G在不同循環數下的比容量。(g)CG、SG、HTG、RG和廢料G的循環性能.
石墨的生產是高度能耗和耗時的,特別是石墨化過程(需要在2800℃加熱幾天)。考慮到對石墨負極的巨大需求(~180,000噸/年),負極回收可以成為石墨供應的一個好場所,并顯著減少石墨生產中的碳足跡。然而,與正極材料回收的蓬勃發展相比,負極石墨的回收往往被忽視。由于石墨還沒有像鋰或鈷那么昂貴,它對于通過傳統的熱法冶金或濕法冶金方法回收石墨是一個虧損的業務。因此,為了揭示能源、環境和經濟影響,我們在能源消耗、廢物排放、成本和潛在效益方面比較了廢石墨的瞬態回收方法。 這些過程如圖4a所示。
在火法冶金中,石墨燃燒有大量的二氧化碳排放,沒有石墨回收,回收后只能獲得合金和礦渣。另一方面,雖然濕法冶金可以獲得石墨產品,但它有多種化學過程,涉及大量的廢水。此外,銅箔多次浸入Cu2+離子或壓成碎片,與鋁和鋼混合,這不僅需要大量的化學品和能源,而且需要進一步的能源和工藝來重新制造銅箔。在我們的瞬態回收中,活性材料和完整的金屬箔可以通過瞬態加熱(< 1s)獲得,顯示出顯著更高的能量、時間和材料效率,同時也將廢物轉化為價值,大大減少碳足跡。
為了量化環境和經濟優勢,我們使用了阿貢國家實驗室開發的EverBatt模型來評估我們的瞬時循環利用的整個循環流程,并將其與火法冶金和濕法冶金方法進行了比較。能源消耗由直接的能量輸入和材料輸入組成(圖4b)。具體而言,瞬態循環工藝的能耗為2.48 MJ/kg電池(只有電能),遠低于火法工藝(18.23 MJ/kg電池,材料7.72,能量10.51 MJ/kg電池)和濕法工藝(102.19 MJ/kg,材料17.45,能量84.74 MJ/kg電池)。此外,熱法冶金和濕法冶金需要許多化學藥劑,如鹽酸、過氧化氫、氫氧化鈉、氫氧化鈉、石灰石、沙子、硫酸。相比之下,對于我們的瞬態回收方法,不需要添加額外的材料來輔助回收。
由固體、液體和氣體廢物組成的廢物排放也出現了同樣的趨勢(圖4c)。瞬態循環工藝的排放量最低(0.26 kg/kg電池),僅為熱法冶金和濕法冶金的7.7%和1.8%。需要注意的是,在廢氣排放中,大多數(>95%)是二氧化碳排放,這表明瞬態循環過程的碳足跡要低得多。 文章還仔細比較了三種回收方法的成本和潛在利潤(4d)。成本包括電池費用、電池拆卸、公用事業、材料、人工、其他直接成本、折舊和其他固定成本。濕法冶金回收成本最高,達到4.00 $/kg電池,高溫法和瞬態循環過程的成本分別為2.63 $/kg電池和2.95 $/kg電池,其中大部分成本來自電池費用(2.0 $/kg電池)。
瞬態回收可以進一步節省成本,因為使用的材料和公用設施要少得多。基于成本分析和回收材料的價格,我們可以通過不同的方法評估電池回收的潛在利潤(圖4d),其中利潤是通過材料收入減去成本計算的。瞬態回收的最高利潤為15.55 $/kg電池,因為(1)它獲得了所有有價值的材料,具有非常高的材料回收率(即更有價值的材料效益)和(2)回收的能源和材料成本最低(即成本最低),因此利潤至少是熱冶金法和濕法冶金法的2倍。特別是,為了展示負極回收的利潤,我們將石墨陽極的成本效益分析分開,如圖4e所示。
在許多情況下,石墨負極的回收成本高和材料成本低導致利潤刺激較少,因此石墨負極的回收利用較少。這在圖4e中可以體現,熱法和濕法冶金法石墨陽極回收的利潤為2.39(不回收石墨)和2.73 $/kg負極,以及巨大的環境犧牲:大量的廢物和二氧化碳排放。相比之下,瞬態回收的利潤增加了307%(4.78$/kg陽極),但產生的廢物最少或可忽略不計。
圖4. 不同回收方法的經濟和環境分析。(a)對不同回收工藝的簡要比較。EverBatt分析了(b)的總能源消耗(能量和材料輸入),(c)的廢物排放(水和固體)(氣體、水和固體),以及(d)電池回收和(e)石墨負極回收,通過比較熱法、濕法冶金和瞬態回收方法的利潤。
為了驗證瞬態回收方法的通用性,我們從Sumwoda、ATL、索尼和CALB等不同制造商生產的故障智能手機和車載電池中回收了SG。如圖5a所示,Sumwoda、ATL、Sony和CALB的材料回收效率分別為99.7%、95.9%、98.7%和99.4%,銅箔回收率為100%,具有優越的材料回收效率。值得注意的是,所有消耗過的負極都是在不知道它們的充電狀態、健康狀態或任何其他處理前直接拆卸的,如DMC清洗去除電解質、預烘烤溶劑蒸發,從而顯示出優越的處理效率。考慮到這些因素,高回收效率表明我們的方法足夠適合各種廢電池的復雜負極的變化。
重要的是,正極的活性材料也可以很容易地從鋁(Al)箔中分離出來。需要注意的是,我們使用了較低的沖擊溫度(例如,1200℃,相比Cu(1083℃),因為Al(660℃,1s)。我們演示了各種廢正極(表示為S-LCO、S-LFP、S-NCM)的有效回收,獲得了回收的活性材料(即HT-LCO、HT-LFP、HT-NCM)。它們的回收效率高達98.8%(LFP)、99.5%(LCO)和98.7%(NCM),顯示了沖擊式加熱的通用性,能夠實現高效的回收(圖5b)。因此,考慮到我們的加熱溫度(如負極1500℃,正極1200℃)遠遠高于各種粘合劑的分解溫度,如CMC(250℃)、SBR(350℃)、PVDF(320℃)等,我們的方法一般適用于各種電池系統。
同時,我們還用ICP-MS法測定了上述樣品的Al雜質。如圖5c所示,我們的沖擊式加熱方法回收的材料與廢棄的正極材料(手工刮取的電極)相似,說明我們的方法在材料回收后沒有很大程度上引入鋁雜質。相比之下,通過機器粉碎獲得的黑色質量顯示鋁雜質含量高出40倍。回收活性材料的結構表征也如圖5d所示。從XRD模式來看,廢正極材料和通過沖擊型加熱的回收材料之間沒有明顯的差異。我們的沖擊式加熱方法對材料結構的影響很小,將減少下一次再生的難度。
例如,我們使用水熱法,通過補充Li和結構恢復來再生HT-LCO樣品。RLCO和S-LCO的電化學性能評價如圖S22所示。雖然S-LCO的比容量極低,但R-LCO在1C(1 mA 4.1g?1.1.1C),表現出優異的循環性能,在100次額外循環后容量保留87.8%,速率性能從0.1 C恢復到10 C。這些結果表明,由于無損結構和低雜質含量,通過沖擊式加熱使回收材料高效再生的可行性和優勢。 在這里,我們演示了通過使用自制的卷對卷設備來實現的瞬態回收方法在陽極廢料上的應用(圖5e)。負極廢帶以5 m/min的速度釋放,通過加熱器和機械應力部分,石墨可以自發地連續落入集電器中。
我們證實了卷卷回收石墨中粘合劑的完全分解。與此同時,銅箔被收集在輥上,有一個干凈的表面。通過結合我們的瞬態回收來分離正極和負極活性材料,可以有效地收集繞組電池中的所有固體組件。此外,通過瞬態加熱(用于快速粘結劑分解)結合商業分離技術(用于物理分離),也可以有效地回收廢堆疊或破碎電極的活性材料。 電池拆卸是目前電池直接回收領域的一個普遍挑戰,特別是考慮到LIB電池和各種電池形式的堅固密封。如果電池拆卸能夠以高效和可擴展的方式處理消耗的電池,直接回收過程的可行性和影響將得到很大的提高。到目前為止,在方便拆卸電池方面已經做了很多努力。在學術界,許多著名的專家都呼吁建立一個細胞組裝的統一標準。
在行業方面,許多公司正在努力開發通用的電池拆卸機,其中一些已經實現了對方形軟包裝電池的大批量拆卸。可以預見的是,在未來的未來,當電池自動拆卸成熟時,直接回收方法(如本研究中報道的)可以使可持續的回收電池產生更經濟、社會和環境的影響。
圖5.瞬態循環利用方法的可擴展性演示。通過沖擊型加熱方法對各種(a)負極和(b)正極活性材料的回收效率。(c)各種正極樣品中鋁雜質的含量(ppm)。沖擊式加熱處理前后各種正極材料的(d) XRD模式。(e)負極廢料及卷對卷回收示意圖及圖片。
總結與展望
綜上所述,在這項工作中,文章報道了一種干燥、綠色和可擴展的電池回收方法,通過瞬態加熱(處理時間< 1 s)方法,顯示了優越的材料回收效率98.7%(石墨)和~100%完整的銅箔。超短的煅燒時間也對活性材料的影響最小,從而有利于有效的再生。石墨可以很容易地再生,具有良好的性能(在0.5 C下340mAh/g,額外180次循環后容量保留>98%),可與商業新鮮石墨相媲美。這種瞬態循環工藝一般適用于不同電池公司的各種負極,也適用于不同類型的負極(如LCO、NCM、LFP),材料回收效率>為97%。
作者還證明了這種方法完全與卷對卷過程兼容,特別有利于連續和自動回收電池碎片(~5 m/min)。Everbatt分析表明,與傳統的熱煉法和濕法冶金回收方法相比,瞬態回收方法需要最少的能量輸入,產生最少的廢物,并具有最高的潛在利潤。重要的是,與以前燃燒或廢棄的石墨負極相比,瞬態回收使石墨回收經濟且有利可圖(4.78 $/kg陽極)。因此,瞬時電池回收顯示了前所未有的能源和時間效率,顯著減少了廢物和碳足跡,以及在可持續電池回收和再制造方面的卓越的可擴展性和自動化性。
審核編輯:劉清
-
鋰離子電池
+關注
關注
85文章
3238瀏覽量
77686 -
鋰電池
+關注
關注
260文章
8101瀏覽量
169959 -
車載電池
+關注
關注
0文章
18瀏覽量
8366 -
電解質
+關注
關注
6文章
811瀏覽量
20049
原文標題:華中科技大學黃云輝教授&浙江大學陸俊教授EES:高效、低碳、卷對卷電池材料回收!
文章出處:【微信號:清新電源,微信公眾號:清新電源】歡迎添加關注!文章轉載請注明出處。
發布評論請先 登錄
相關推薦
創建一個5G的邏輯卷
汽車行業究竟要卷到什么時候
倍加福線性定位系統在電池卷料OHT天車搬運系統的應用
鐵威馬NAS教程 為什么修復文件系統、為卷擴容、增加及刪除 SSD 緩存等操作失敗?
按照這樣學習C語言,成為卷王不是夢!
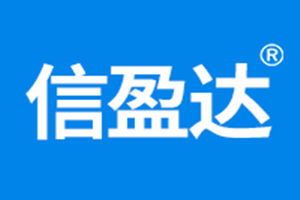
評論