電池包殼體輕量化,對(duì)于提升電池包能量密度有著重大意義。
研究以鋁合金型材為主體結(jié)構(gòu)的電池包殼體,對(duì)鋁合金型材斷面、攪拌摩擦焊接接頭、連接工藝等方面進(jìn)行了分析研究,并在成本、工藝性等方面進(jìn)行綜合比較,通過CAE對(duì)設(shè)計(jì)方案進(jìn)行分析驗(yàn)證。
合理的結(jié)構(gòu)設(shè)計(jì)和連接方式,可以有效地保證殼體整體強(qiáng)度,降低加工難度,使殼體減重,為電池包殼體的輕量化設(shè)計(jì)提供參考。
經(jīng)過近幾年的高速發(fā)展,目前我國已成為世界新能源汽車產(chǎn)銷第一大國。隨著國家2019年新能源汽車補(bǔ)貼政策的出臺(tái)和續(xù)航里程要求的提高,對(duì)電池系統(tǒng)能量密度提出了更高的要求。
提升電池能量密度有兩種路徑:一是增加單體電芯的比能量;二是電池包的結(jié)構(gòu)輕量化。提升單體電芯的比能量,技術(shù)難度大,研發(fā)周期長,資金投入大,相比之下,使電池包的結(jié)構(gòu)輕量化則更容易實(shí)現(xiàn)。
鋁合金在汽車上的應(yīng)用早已屢見不鮮。鋁合金具有密度低、比強(qiáng)度高、熱穩(wěn)定性、耐腐蝕性及導(dǎo)熱性良好、無磁性、成型容易、回收價(jià)值高等諸多優(yōu)點(diǎn),因此是電池包輕量化設(shè)計(jì)的理想材料。
目前,電池包殼體用材主流方案是擠壓鋁合金殼體+PP/玻纖復(fù)合材料上蓋。
就目前發(fā)展來看,鋁合金殼體和塑料上蓋的方案具有輕量化前景。殼體采用鋁擠壓型材 + 攪拌摩擦焊 + MIG焊的方案,綜合應(yīng)用成本低,性能滿足要求,且可實(shí)現(xiàn)水冷電池的循環(huán)水道的集成。
上蓋采用非金屬上蓋,主要用到PP/玻纖 + LFT-D模壓工藝,既能提高生產(chǎn)的效率也可滿足火焰燃燒和密封性能的要求,且模具成本較低。
鋁合金電池包殼體已在多款新能源汽車上應(yīng)用,例如,比亞迪宋和唐、蔚來 ES8、北汽EV系列等。該殼體可提升電池包能量密度,增加續(xù)航里程。由此可見,鋁合金電池包殼體具有廣闊的市場(chǎng)前景。
01鋁合金電池包殼體結(jié)構(gòu)
典型的鋁合金拼焊電池包殼體如圖1所示。殼體主要由鋁合金型材邊框和鋁合金型材底板構(gòu)成,采用6系擠壓型材拼焊而成。
為保證焊接強(qiáng)度和密封性,選用低應(yīng)力變形小的攪拌摩擦焊,鋁合金型材適用的標(biāo)準(zhǔn)件一般有鋼絲螺套、拉鉚螺母、壓鉚螺母。
除標(biāo)準(zhǔn)件外,其余為100%鋁合金材質(zhì)。該殼體強(qiáng)度高、重量輕、耐腐蝕性好。
圖 1 鋁合金電池包殼體圖
02設(shè)計(jì)方案介紹
1 斷面結(jié)構(gòu)及材質(zhì)
邊框和底板為鋁合金擠壓型材,材料一般選用6061-T6(屈服強(qiáng)度 240 MPa, 抗拉強(qiáng)度260MPa)、6005A-T6(屈服強(qiáng)度215 MPa,抗拉強(qiáng)度255 MPa)和6063-T6(屈服強(qiáng)度170 MPa,抗拉強(qiáng)度215 MPa)等,根據(jù)斷面復(fù)雜程度、成本、模具消耗等因素考慮具體選用何種牌號(hào)。
這幾種材料的強(qiáng)度大小,依次為:6061-T6>6005A-T6>6063-T6,同等斷面擠壓難度為:6061-T6>6005A-T6>6063-T6。
圖 2 是邊框的典型斷面,由多個(gè)空腔組成,材質(zhì)為6061-T6,壁厚最薄處 2 mm。
邊框主要有兩種加工方案:一是進(jìn)行整體型材擠壓,然后機(jī)加工,零件一體性好,強(qiáng)度有保證,但加工量大,成本較高;另一種是采用型材拼焊的方式,此種方案成本較低,但焊縫強(qiáng)度較弱,需要驗(yàn)證焊縫強(qiáng)度是否滿足要求。
在實(shí)際生產(chǎn)中應(yīng)綜合考慮,選擇最佳的設(shè)計(jì)方案。
圖 2 邊框斷面
圖 3 是底板的典型斷面,由多個(gè)空腔組成,包括上部凸起,上部凸起主要用于電池模組的安裝。
因斷面尺寸較大,且厚度只有2mm,所以選擇材質(zhì)6005A-T6。上部凸起如需要安裝鋼絲螺套,可將上部空腔做成實(shí)心。
非安裝部位可用CNC設(shè)備去除,在保證強(qiáng)度的同時(shí),能使重量最輕。
圖 3 底板斷面
邊框和底板是電池模組的承載者,對(duì)強(qiáng)度要求比較高,所以一般都選用具有型腔的雙層斷面來保證強(qiáng)度,底板厚度一般為10mm左右,壁厚2mm。較少使用單層鋁板。
6063-T6由于材質(zhì)偏軟,主要用于復(fù)雜斷面或者受力較小的零件。
2 連接設(shè)計(jì)
鋁合金電池包殼體的主要連接方式有:攪拌摩擦焊接、MIG、拉鉚、壓鉚以及少量弧焊和膠粘。
底板與底板、底板與邊框主要用攪拌摩擦焊連接。焊縫強(qiáng)度可達(dá)母材80%左右。
攪拌摩擦焊接與普通熔焊方案相比較,具有以下突出的優(yōu)點(diǎn):
屬于固態(tài)焊接技術(shù),焊接過程不存在焊接材料融化;
焊接接頭質(zhì)量好,焊縫為細(xì)晶鍛造組織結(jié)構(gòu),沒有氣孔、裂紋、夾渣等缺陷;
不受焊縫位置的限制,可實(shí)現(xiàn)多種接頭形式的焊接;
焊接效率高,在 0.4-100 mm 厚度范圍內(nèi)可以實(shí)現(xiàn)單焊道焊接成型;
焊件中殘余應(yīng)力低,變形小,可實(shí)現(xiàn)高精度焊接;
接頭強(qiáng)度高、疲勞性能好,沖擊韌性優(yōu)異;
焊接成本低,沒有焊接過程消耗,不需要填絲和保護(hù)氣體;
焊接操作簡單,便于實(shí)現(xiàn)自動(dòng)化焊接。
圖 4 為底板型材攪拌摩擦焊接接頭,底板與底板之間采用板對(duì)接接頭雙面焊接。雙面焊接強(qiáng)度高,變形小。
在攪拌摩擦焊接過程中會(huì)對(duì)工件有一個(gè)很大的下壓力,所以,就需要增加型腔內(nèi)筋和圓角厚度,焊接深度越大,筋和圓角就越大。
表 1 為焊接厚度與型材尺寸的對(duì)應(yīng)關(guān)系。
圖 4 底板斷面
表 1 焊接厚度與型材厚度對(duì)應(yīng)關(guān)系
邊框和底板之間主要有兩種連接方式:一是雙面攪拌摩擦焊接;二是外部攪拌摩擦焊接和內(nèi)部弧焊 + 涂膠。
兩種不同的連接方式采用的鋁合金接頭也不一樣。
圖 5 是邊框與底板雙面攪拌摩擦焊接接頭形式。為給攪拌頭預(yù)留出足夠的空間,邊框與底板連接處伸出長度要足夠長,避免邊框和攪拌頭干涉,以免增加邊框型材的尺寸和擠壓難度。但雙面焊接強(qiáng)度高、變形小,這也是它的主要優(yōu)勢(shì)。
圖 6 為外側(cè)攪拌摩擦焊接+內(nèi)側(cè)MIG焊接。底板外側(cè)需搭接在型材邊框上,且型材邊框搭接處應(yīng)做成實(shí)心,滿足攪拌摩擦焊接要求,給焊接提供支撐力;內(nèi)側(cè)則采用MIG焊接,視情況選擇滿焊或者斷續(xù)焊接。
此種連接方式效率高、難度小、成本低,但是因?yàn)閮?nèi)部采用了弧焊,焊縫可能有漏水的風(fēng)險(xiǎn),所以,還要再涂一遍密封膠來保證密封性,這也是它的一個(gè)弊端。
圖 5 邊框與底板雙面攪拌摩擦焊接圖
圖 6 邊框與底板外部攪拌摩擦焊接+內(nèi)部MIG焊接
3 密封設(shè)計(jì)
由于整車行駛環(huán)境的復(fù)雜性,尤其是電池包安裝在車輛底盤下方或者位置較低的區(qū)域,當(dāng)電動(dòng)車輛遇到涉水、暴雨等危險(xiǎn)工況時(shí),可能會(huì)因水汽的侵襲導(dǎo)致電池的電氣故障、短路、漏電等危害,因此必須為電池系統(tǒng)提供防水、防塵的環(huán)境。
電池包的密封性直接影響到電池系統(tǒng)的工作安全,從而影響到電動(dòng)車輛的使用安全。
通常,電池包密封防護(hù)等級(jí)要求達(dá)到IP67才能保證電池包密封防水,這樣電池組才不會(huì)因?yàn)檫M(jìn)水而短路。
鋁合金電池包殼體的底板與底板之間宜采用攪拌摩擦焊接。由于攪拌摩擦焊接屬于固相連接技術(shù),在焊接過程中金屬基材不融化,因此,相比熔化焊接減少了氣孔、裂紋等缺陷的發(fā)生率。所以,為了較好地保證密封性,焊接應(yīng)優(yōu)先選用此種焊接方式。
如果邊框與底板內(nèi)部采用弧焊,則需要涂焊縫密封膠來保證密封性。殼體與上蓋之間雖然采用發(fā)泡硅膠來保證密封,但是,連接的標(biāo)準(zhǔn)件自身也要保證其密封性,殼體法蘭一般采用M5拉鉚螺母。
目前,已有廠家生產(chǎn)可以專門用于電池包的防水密封的表面帶膠的拉鉚螺母,通過拉鉚螺母塑性變形,使膠起到密封作用。
前端使用的盲孔壓鉚螺母,由于自身具有一定的密封效果,且外部附件也有密封圈,所以不再做單獨(dú)處理。
如發(fā)現(xiàn)泄漏,可以進(jìn)行涂膠處理。
4 電池包殼體鋼與鋁合金的重量對(duì)比
鋁的密度約是鋼的 1/3,是輕量化的理想材質(zhì)。
表2為某款鋼質(zhì)電池包殼體鋁化的情況。從表2數(shù)據(jù)可知,減重效果達(dá)到26.7%。電池包殼體的鋁代鋼不僅可以提升電池包能量密度,也增加了車輛續(xù)航里程。
表 2 鋼與鋁合金電池包殼體重量對(duì)比
03仿真分析
根據(jù)GB/T 31467.3—2015電動(dòng)汽車用鋰離子動(dòng)力蓄電池包和系統(tǒng)第三部分:安全性要求與測(cè)試方法,對(duì)鋁合金電池包殼體強(qiáng)度、振動(dòng)、擠壓等方面進(jìn)行仿真分析。
圖 7 為某鋁合金電池包殼體仿真分析結(jié)果
其中:
圖 7(a)3G 向前工況應(yīng)力最大值為 29.4 MPa,
圖 7(b)振動(dòng)應(yīng)力最大值為55.98MPa,最大值均小于6005A屈服強(qiáng)度215 MPa,
圖 7(c)擠壓最大位移7.081 mm,電池模組安全距離為10mm(每個(gè)電池包結(jié)構(gòu)不同,安全距離也會(huì)不同,需要客戶確認(rèn)),滿足要求。
04經(jīng)驗(yàn)結(jié)論
1、6061-T6 和 6005A 兩種材質(zhì)的性能均可以較好地滿足設(shè)計(jì)要求。
2、擠壓斷面結(jié)構(gòu)的一體化雖然加工量大且成本高,但有利于電池包強(qiáng)度的提高,可綜合考慮。
3、攪拌摩擦焊接在保證焊縫強(qiáng)度的同時(shí)還可以保證密封性,是電池包殼體的最佳焊接方式。
4、標(biāo)準(zhǔn)件選用具有防水功能的拉鉚螺母。
5、型材拼焊的鋁合金電池包殼體具有成本低、減重效果好等特點(diǎn),減重效果在25%以上,可應(yīng)用于新能源汽車上,提高電池包能量密度,延長續(xù)航里程。
審核編輯:湯梓紅
-
工藝
+關(guān)注
關(guān)注
4文章
654瀏覽量
29148 -
焊接
+關(guān)注
關(guān)注
38文章
3362瀏覽量
60748 -
結(jié)構(gòu)設(shè)計(jì)
+關(guān)注
關(guān)注
0文章
37瀏覽量
11100 -
電池包
+關(guān)注
關(guān)注
3文章
174瀏覽量
14827 -
電池
+關(guān)注
關(guān)注
84文章
10877瀏覽量
133272
原文標(biāo)題:電池包解析:殼體結(jié)構(gòu)設(shè)計(jì)及連接工藝
文章出處:【微信號(hào):智享新動(dòng)力,微信公眾號(hào):智享新動(dòng)力】歡迎添加關(guān)注!文章轉(zhuǎn)載請(qǐng)注明出處。
發(fā)布評(píng)論請(qǐng)先 登錄
相關(guān)推薦
結(jié)構(gòu)設(shè)計(jì)的加工工藝性
操作系統(tǒng)結(jié)構(gòu)設(shè)計(jì)
招聘結(jié)構(gòu)設(shè)計(jì)師
招聘--結(jié)構(gòu)設(shè)計(jì)師
淺談產(chǎn)品結(jié)構(gòu)設(shè)計(jì)特點(diǎn)
希澈科技誠聘結(jié)構(gòu)設(shè)計(jì)工程師
軸系結(jié)構(gòu)設(shè)計(jì)實(shí)驗(yàn)
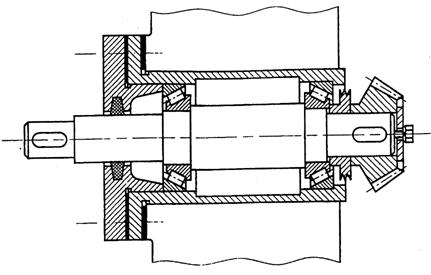
淺談產(chǎn)品結(jié)構(gòu)設(shè)計(jì)類別及產(chǎn)品結(jié)構(gòu)設(shè)計(jì)的重要性
產(chǎn)品結(jié)構(gòu)設(shè)計(jì)在工業(yè)設(shè)計(jì)中的地位是怎樣的
5針M16接口結(jié)構(gòu)設(shè)計(jì)
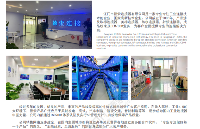
評(píng)論