針對(duì)某型雙級(jí)橋等高齒齒輪噪聲高的問(wèn)題,利用KIMOS 軟件從齒形設(shè)計(jì)層面對(duì)該產(chǎn)品進(jìn)行了優(yōu)化,減小了該產(chǎn)品的失配量,降低了產(chǎn)品設(shè)計(jì)的傳動(dòng)誤差,同時(shí)通過(guò)產(chǎn)品的多輪熱試,根據(jù)熱試結(jié)果反調(diào)熱前切齒的理論模型,消除了熱處理變形的影響,穩(wěn)定了產(chǎn)品的加工制造工藝,為降低噪聲提供了解決方案。
隨著現(xiàn)代載貨汽車技術(shù)的發(fā)展,對(duì)載貨汽車齒輪傳動(dòng)性能的要求越來(lái)越高。在高速重載的條件下,既要保證齒輪傳動(dòng)的穩(wěn)定性和可靠性,又要盡可能地控制其振動(dòng)和噪聲。2018年,某車橋廠就提出了齒輪的品質(zhì)提升目標(biāo):2020年底,車橋齒輪類產(chǎn)品全部達(dá)到A 級(jí)標(biāo)準(zhǔn),等高齒齒輪齒輪噪聲≤78 dB。這對(duì)從事齒輪技術(shù)工作的人來(lái)說(shuō),既是挑戰(zhàn)也是機(jī)遇。
以某型雙級(jí)橋等高齒齒輪為例,筆者在現(xiàn)場(chǎng)收集了5 套產(chǎn)品的噪聲數(shù)據(jù)和傳動(dòng)誤差的檢測(cè)記錄,見(jiàn)表1 與表2。從表中我們可以看出未進(jìn)行優(yōu)化前,正車面平均噪聲為90 dB,倒車面平均噪聲為89.8 dB。該噪聲是在空載時(shí),小輪轉(zhuǎn)速1 300 r/min(車速約50 km/h)的條件下,在配對(duì)機(jī)上測(cè)得。與車橋廠的噪聲測(cè)試條件不同:將裝配到整橋上后,在橋殼內(nèi)加入齒輪油,小輪轉(zhuǎn)速1 300 r/min(車速約50 km/h)的條件下在橋包外進(jìn)行噪聲測(cè)量。車橋廠測(cè)量的結(jié)果一般會(huì)比表1 中的結(jié)果低2 ~3 dB。為方便對(duì)比,本文均采用第一種方法進(jìn)行噪聲測(cè)量。
表1 某型雙級(jí)橋等高齒齒輪噪聲記錄 (單位:dB)
表2 某型雙級(jí)橋等高齒齒輪傳動(dòng)誤差記錄 (單位:dB)
優(yōu)化設(shè)計(jì)思路
圓柱齒輪可以通過(guò)熱后的磨齒修形來(lái)降低齒輪嚙入和嚙出產(chǎn)生的振動(dòng)和噪聲,而齒輪因?yàn)椴捎眠B續(xù)分度方法(Face Hobbing)進(jìn)行加工,無(wú)法磨齒,其熱后的精加工工藝只能通過(guò)研齒來(lái)降低嚙合噪聲。因此,針對(duì)等高齒齒輪的修形只能在熱前切齒的過(guò)程中進(jìn)行,利用KIMOS 軟件可以很方便地修改等高齒齒輪的齒面理論模型,配合克林貝格P65 齒輪檢測(cè)中心在切齒過(guò)程中實(shí)現(xiàn)閉環(huán)控制,得到完全符合設(shè)計(jì)要求的半成品齒坯。
因?yàn)樵摦a(chǎn)品已大批量制造,齒坯還有大量庫(kù)存,因此在不改變齒坯形狀和加工刀具的情況下降低噪聲是最優(yōu)的解決方案。在KIMOS 軟件中齒形優(yōu)化設(shè)計(jì)分為三個(gè)部分:第一部分是失配量?jī)?yōu)化(在KIMOS 軟件中叫Easeoff),如圖1 所示;第二部分是接觸區(qū)優(yōu)化,如圖2 所示;第三部分是傳動(dòng)誤差優(yōu)化,如圖3 所示。這三個(gè)部分是相互聯(lián)動(dòng)的,它們的變化可以通過(guò)5 個(gè)參數(shù)的調(diào)整來(lái)實(shí)現(xiàn),這5個(gè)參數(shù)分別是螺旋角誤差dβ,壓力角誤差dα,齒長(zhǎng)方向的鼓形量Lβ,齒高方向的鼓形量Hβ,齒長(zhǎng)方向的對(duì)角變形dv,如圖4所示。
圖1 失配量Ease-off
圖2 接觸區(qū)
圖3 傳動(dòng)誤差
圖4 齒形優(yōu)化的5 個(gè)參數(shù)
其中在降噪優(yōu)化設(shè)計(jì)過(guò)程中需要重點(diǎn)關(guān)注的是齒形的失配量和傳動(dòng)誤差。
單齒面?zhèn)鲃?dòng)誤差被定義為所測(cè)量的轉(zhuǎn)動(dòng)角度與理論計(jì)算的轉(zhuǎn)動(dòng)角度之間的差值,而理論計(jì)算的轉(zhuǎn)動(dòng)角度為主動(dòng)輪所轉(zhuǎn)過(guò)的角度與傳動(dòng)比的倒數(shù)的乘積,如式1 所示。
如果一對(duì)齒廓完全共軛,則當(dāng)它們?cè)趪Ш蠒r(shí),被動(dòng)輪所轉(zhuǎn)過(guò)的角度將與理論計(jì)算應(yīng)轉(zhuǎn)過(guò)的角度完全一致,即傳動(dòng)誤差為零。如果一對(duì)齒輪副存在長(zhǎng)度和齒高方向的鼓形,實(shí)際嚙合過(guò)程中,就會(huì)存在周期性傳動(dòng)誤差,即產(chǎn)生周期性的振動(dòng)和噪聲,傳動(dòng)誤差可以采用傅里葉級(jí)數(shù)進(jìn)行分析,其原理如圖5 所示。
從圖5 中我們可以看出,傅里葉分析頻譜信號(hào)隨階數(shù)增加衰減趨勢(shì)減弱,實(shí)際測(cè)量中一般只關(guān)注一階和二階傳動(dòng)誤差。要達(dá)到降低齒輪嚙合噪聲的目的,只要降低齒長(zhǎng)和齒高方向的鼓形即減小失配量就可以降低傳動(dòng)誤差。
表3 齒面優(yōu)化前、后調(diào)整參數(shù)對(duì)比
圖5 傳動(dòng)誤差分析的原理圖
齒面優(yōu)化設(shè)計(jì)
根據(jù)以上優(yōu)化思路,筆者對(duì)該產(chǎn)品齒面進(jìn)行了優(yōu)化設(shè)計(jì)。優(yōu)化前、后的齒面調(diào)整參數(shù),如表3 所示。我們可以看出,螺旋角誤差dβ 和壓力角誤差dα 略微做了調(diào)整,主要影響接觸區(qū)的在齒長(zhǎng)方向和齒高方向的位置,而齒長(zhǎng)方向的鼓形量Lβ 和齒高方向的鼓形量Hβ 都明顯有了改善。
螺旋角和壓力角及對(duì)角變形的變化對(duì)齒輪接觸區(qū)的影響。從表4 中可以看到,產(chǎn)品正車面螺旋角減小2ˊ40″,接觸區(qū)在齒長(zhǎng)方向往小端移動(dòng),壓力角變小25″,接觸區(qū)在齒高方向往齒根移動(dòng),齒長(zhǎng)方向的對(duì)角變形減小26′6″,即接觸區(qū)的內(nèi)對(duì)角減小;產(chǎn)品倒車面螺旋角減小38″,接觸區(qū)在齒長(zhǎng)9 方向往大端移動(dòng),壓力角增大1′57″,接觸區(qū)在齒高方向往齒頂移動(dòng);齒長(zhǎng)方向的對(duì)角變形增大26′17″,接觸區(qū)的內(nèi)對(duì)角減小。
由表5 和表6 可知,鼓形量的改變對(duì)齒輪的失配量及傳動(dòng)誤差的影響。從表4 和表5 中可以看到產(chǎn)品正車面小端齒頂?shù)淖畲笫淞繌?73 μm 降到了102 μm,大端齒根的最大失配量從233 μm 降到了178 μm,相應(yīng)的傳動(dòng)誤差也從101.2 μrad 降到了81.1 μrad。而倒車面大端齒頂?shù)淖畲笫淞繌?85 μm 降到了122 μm,小端齒根的最大失配量從212 μm 降到了154 μm,相應(yīng)的傳動(dòng)誤差也從103.5 μrad 降到了81.8 μrad。
表4 優(yōu)化前、后接觸區(qū)對(duì)比
表5 優(yōu)化前、后失配量對(duì)比
因此,經(jīng)過(guò)齒面優(yōu)化設(shè)計(jì)之后,理論上產(chǎn)品的嚙合噪聲得到了顯著降低。
實(shí)踐驗(yàn)證
等高齒齒輪產(chǎn)品從鍛坯開(kāi)始到成品入庫(kù)總共分為10 個(gè)工序。在整個(gè)工藝流程中,我們需要重點(diǎn)關(guān)注的是切齒—熱試反調(diào)—一批切的過(guò)程,其中反調(diào)是根據(jù)產(chǎn)品熱處理試驗(yàn)后P65 的檢測(cè)結(jié)果來(lái)調(diào)整理論齒面模型以消除熱處理變形的影響。
表6 優(yōu)化前、后傳動(dòng)誤差
熱前切齒要求實(shí)際齒面坐標(biāo)與理論齒面盡可能達(dá)成一致,通過(guò)P65 檢測(cè)可以很精確地測(cè)量出每個(gè)齒面的誤差情況,從而為接觸區(qū)設(shè)計(jì)和修正提供依據(jù)。切齒完成后進(jìn)行熱處理試驗(yàn),試驗(yàn)的目的在于找出齒面熱處理變形的規(guī)律,然后通過(guò)反調(diào)理論齒面模型以預(yù)補(bǔ)償熱處理變形,從而消除熱處理變形對(duì)設(shè)計(jì)產(chǎn)生的干擾。批切即按照反調(diào)之后的理論齒面模型進(jìn)行切齒。這樣批切的產(chǎn)品經(jīng)熱處理之后,其齒面基本能夠與我們初始優(yōu)化設(shè)計(jì)時(shí)的齒面保持一致,因此,我們可以認(rèn)為批切的產(chǎn)品是滿足優(yōu)化設(shè)計(jì)要求的。
在實(shí)際的制造過(guò)程中,傳動(dòng)誤差是不能在熱處理前進(jìn)行檢測(cè)的,因?yàn)闊崆暗凝X輪硬度只有170 HB 左右,齒面在嚙合過(guò)程中很容易產(chǎn)生劃傷,因此傳動(dòng)誤差的檢測(cè)安排在配對(duì)完成后進(jìn)行。由于傳動(dòng)誤差、失配與接觸區(qū)位置大小是相互關(guān)聯(lián)的,因此在產(chǎn)品試制時(shí)我們只需要控制熱前及熱后接觸區(qū)來(lái)間接控制產(chǎn)品的嚙合噪聲。
研齒配對(duì)過(guò)程中檢測(cè)的產(chǎn)品噪聲記錄見(jiàn)表7,表8 為研齒后600HTT 檢測(cè)機(jī)檢測(cè)的傳動(dòng)誤差記錄。從表8 的噪聲檢測(cè)結(jié)果與表1 的對(duì)比中我們可以發(fā)現(xiàn),正轉(zhuǎn)噪聲經(jīng)過(guò)優(yōu)化后平均噪聲為81.86 dB,平均反轉(zhuǎn)噪聲為83.10 dB,兩個(gè)面的噪聲降低了7 ~8 dB。從表9 和表2 的對(duì)比中可以看到,產(chǎn)品凸面和凹面對(duì)應(yīng)的一階傳動(dòng)誤差也有了大幅度降低。
表7 優(yōu)化后試制產(chǎn)品的噪聲記錄(單位:dB)
表8 研齒后傳動(dòng)誤差檢測(cè)記錄(單位:dB)
結(jié)束語(yǔ)
通過(guò)KIMOS 軟件對(duì)產(chǎn)品的失配和傳動(dòng)誤差進(jìn)行了優(yōu)化,并通過(guò)產(chǎn)品的試制驗(yàn)證該優(yōu)化方案可以大幅降低等高齒螺旋錐齒輪的嚙合噪聲,為我公司等高齒螺旋錐齒輪質(zhì)量提升給出了解決方案。從結(jié)果對(duì)比中我們可以看出,產(chǎn)品還有繼續(xù)優(yōu)化提升的空間,但是失配和傳動(dòng)誤差過(guò)小,將導(dǎo)致產(chǎn)品的接觸區(qū)對(duì)安裝位置過(guò)于敏感,降低產(chǎn)品的一次配對(duì)合格率,導(dǎo)致成本升高。因此,質(zhì)量和成本的平衡點(diǎn)需要設(shè)計(jì)者自己尋找。
-
噪聲
+關(guān)注
關(guān)注
13文章
1140瀏覽量
48036 -
數(shù)據(jù)
+關(guān)注
關(guān)注
8文章
7250瀏覽量
91652 -
軟件
+關(guān)注
關(guān)注
69文章
5144瀏覽量
89119
原文標(biāo)題:雙級(jí)橋等高齒齒輪的降噪優(yōu)化
文章出處:【微信號(hào):EDC電驅(qū)未來(lái),微信公眾號(hào):EDC電驅(qū)未來(lái)】歡迎添加關(guān)注!文章轉(zhuǎn)載請(qǐng)注明出處。
發(fā)布評(píng)論請(qǐng)先 登錄
模擬電源設(shè)計(jì)的LDO低噪聲電源解決方案
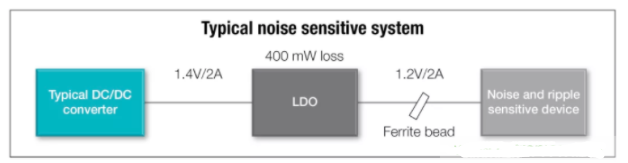
雙伺服電機(jī)驅(qū)動(dòng)的鉆床齒隙模型仿真分析
如何用matlab計(jì)算弧齒錐齒輪的理論齒面點(diǎn)坐標(biāo),求程序
斜齒輪傳動(dòng)是怎么轉(zhuǎn)動(dòng)的,斜齒輪傳動(dòng)的原理
低噪聲解決方案助力設(shè)計(jì)安靜且緊湊的工業(yè)用電源
齒輪傳動(dòng)噪聲形成的主要因素及對(duì)策
齒輪伺服電機(jī)是旋轉(zhuǎn)運(yùn)動(dòng)控制技術(shù)的最佳選擇嗎?還是有更好的解決方案嗎?
如何確定圓柱齒輪加工的齒厚
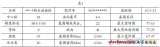
直齒圓錐齒輪與弧齒圓錐齒輪輪齒應(yīng)力比較
順力電機(jī)介紹齒輪減速機(jī)軟齒和硬齒面的區(qū)別
采用具有高重合度的細(xì)高齒設(shè)計(jì)提升電驅(qū)動(dòng)橋NVH性能
新能源圓柱齒輪齒廓齒向傾斜誤差計(jì)算
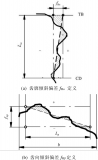
評(píng)論