齒輪系統在運動過程中的傳動比固定不變,是十分重要的傳動件[5]。不同的運動工況將影響到齒輪結構性能的好壞及其使用壽命,從而影響到整個換擋執行機構的可靠性[6-7]。目前,已有許多學者對換擋執行機構進行了大量的研究并取得了一定成果,這些研究大多是考慮換擋執行機構的換擋性能以及換擋舒適性,沒有過多考慮零部件本身的結構問題[8-10]。
本文應用Inspire 軟件對換擋執行機構中的齒輪系統進行多體動力學仿真分析,基于分析結果對輸出齒輪和輸出軸結構薄弱部位進行改進設計并進行仿真分析和試驗驗證,改進后結構應力值顯著降低且在實驗過程中未出現斷裂失效現象。
1 齒輪系統結構及其主要參數
換擋執行機構齒輪系統主要由電機、一級主動輪、一級從動輪、蝸桿、輸出齒輪和輸出軸組成,齒輪系統結構如圖1 所示。電機作為整個系統的輸入端,在電機的運轉下帶動一級主動輪,一級主動輪和一級從動輪連接,一級從動輪又與蝸桿連接,蝸桿和輸出齒輪相連接,輸出齒輪與輸出軸相連,輸出軸作為整個系統的動力輸出。齒輪系統各零件的材料參數如表1 所示。
圖1 齒輪系統結構
Fig.1 Structure of gear system
表1 齒輪系統零件材料參數
Tab.1 Material parameters of gear system
2 齒輪系統分析及改進 2.1 現有齒輪系統存在的問題
齒輪傳動系統設計完成之后,將其投入到試驗中,電機轉速用0.1 s 加速至7 636 r/min,輸出軸端的負載扭矩為15 N·m,依據實際工況對其進行動力學試驗,試驗過程中,輸出齒輪扇形根部發生斷裂,如圖2所示。
圖2 輸出齒輪發生斷裂
Fig.2 Output gear fracture
試驗結果表明輸出齒輪應力已經超過其材料的屈服強度,將會影響到整個換擋執行機構在工作過程中的可靠性和穩定性,因此需要對齒輪傳動系統結構進行改進設計。為了解齒輪系統工作過程中的受力情況,建立齒輪系統有限元模型進行多體動力學仿真計算。
2.2 齒輪系統仿真分析
2.2.1 建立有限元模型
將齒輪系統三維模型導入到Inspire 軟件,切換到結構仿真模塊為各零部件添加材料,分別輸入不同材料的彈性模量、泊松比和密度,再定義兩個剛體組,剛體組1 由一級從動輪和蝸桿組成,剛體組2 由輸出齒輪和輸出軸組成。切換到運動模塊在一級主動輪和一級從動輪之間以及蝸桿和輸出齒輪之間定義接觸,接觸類型設置為靜態和動態接觸,靜態摩擦因數和動態摩擦因數分別為0.1 和0.05。在此次分析中,電機轉速設置為用0.1 s 加速至7 636 r/min,運行時間0.16 s,轉動電機角速度曲線如圖3 所示。在輸出軸加載以z軸為中心逆時針方向的負載扭矩作為外部激勵,大小為15 N·m,設置求解步長為0.001 s,求解時間為0.16 s。齒輪系統多體動力學分析模型如圖4 所示。
圖3 轉動電機角速度曲線
Fig.3 Angular velocity curve of rotating motor
圖4 齒輪系統多體動力學模型
Fig.4 Multi-body dynamic model of gear system
2.2.2 仿真計算結果分析
對齒輪系統進行多體動力學仿真分析,得到剛體組2 的加速度如圖5 所示,輸出齒輪和輸出軸的von Mises 應力云圖分別如圖6 和圖7 所示。
圖5 剛體組2 的加速度
Fig.5 Acceleration of rigid body group 2
圖6 輸出齒輪應力云圖
Fig.6 Stress cloud diagram of output gear
圖7 輸出軸應力云圖
Fig.7 Stress cloud diagram of output shaft
由圖5 和圖6 可知,在運動時間為0.56 s時,剛體組2 的加速度達到最大值8 232 m/s2,與輸出齒輪和輸出軸最大von Mises 應力出現的時間相同,驗證了有限元模型的正確性。
由圖5 可知,在整個運動過程中,輸出齒輪的最大等效應力出現在運動時間為0.056 s時,大小約為143 MPa,已經大于輸出齒輪材料PA9T+GF30 的屈服強度115 MPa,分析原因是輸出齒輪在運動過程中受力復雜,同時承受蝸桿方向傳來的繞z軸順時針方向的力和以z軸為中心逆時針方向的負載扭矩,且輸出齒輪基部區域結構存在棱角,最終導致在該部位出現應力集中。應力結果表明在現有加載條件下,輸出齒輪強度已經不滿足要求,需對其結構進行改進。
輸出軸在運動過程中主要承受與輸出齒輪相接觸面的扭轉力以及輸出端加載的負載扭矩。由圖7 可知,在整個運動過程中,輸出軸的最大等效應力出現在運動時間為0.056 s時,大小約為110 MPa,已經接近輸出齒輪材料高碳粉末冶金的屈服強度120 MPa,分析原因是輸出軸在運動過程中受力復雜,同時承受以z軸為中心順時針方向的力和以z軸為中心逆時針方向的負載扭矩,且輸出軸與輸出齒輪接觸位置的輸出軸結構存在尖角,最終導致在該部位出現應力集中。雖然輸出軸的強度在當前工況下滿足要求,但其應力值已經接近材料屈服強度是比較危險的狀態,為提高整個系統的可靠性和穩定性,需對輸出軸結構進行改進。
2.3 齒輪系統結構改進設計
由輸出齒輪應力結果可知,輸出齒輪最大應力出現在齒輪基部且已超過材料的屈服強度,為提高齒輪基部的強度,簡單實用的方法就是將該部位封閉將其平滑過渡,避免局部位置受力產生應力集中,輸出齒輪扇形根部的應力值較其他部位更大,為了提高輸出齒輪扇形根部的強度,在此處作加筋處理。
由輸出軸的應力結果可知,輸出軸的最大等效應力位置出現在與輸出齒輪接觸部位,該部位應力值普遍較其他部位更大,為了改善這種情況,將輸出軸凹陷部位填平并加粗,且將該接觸部位結構改為過渡圓角,增大輸出齒輪和輸出軸之間的接觸面積,減小應力集中,結構改進后的輸出齒輪和輸出軸三維模型如圖8所示。
圖8 改進后齒輪系統結構
Fig.8 Gear system structure after improvement
3 改進后齒輪系統仿真及實驗驗證 3.1 改進后齒輪系統仿真分析
采用相同的方法對改進后的結構進行多體動力學仿真分析,改進后剛體組2 的加速度如圖9 所示,輸出齒輪和輸出軸的von Mises 應力云圖分別如圖10 和圖11 所示。
圖9 改進后剛體組2 的加速度
Fig.9 The acceleration of rigid body group 2 after improvement
圖10 改進后輸出齒輪應力云圖
Fig.10 Stress cloud diagram of output gear after improvement
由圖9 可知,在運動時間為0.54 s時,剛體組2 的加速度達到最大值254 m/s2,與輸出齒輪最大von Mises 應力出現的時間相同,驗證了有限元模型的正確性。
由圖10 可知,在整個運動過程中,輸出齒輪的最大等效應力出現在運動時間為0.054 s時,大小約為40.7 MPa。仿真結果表明,結構改進后的輸出齒輪在現有加載條件下,強度方面是安全的。結構改進后的輸出齒輪應力值比改進前應力值大小普遍下降約80 MPa,最大應力值下降約100 MPa,減小了69.9%。
由圖11 可知,在整個運動過程中,輸出軸的最大等效應力出現在運動時間為0.159 s時,大小約為72.3 MPa,結構改進后的輸出齒輪應力值比改進前應力水平普遍下降約40 MPa,最大應力值下降約38 MPa,減小了34.5%。此處輸出軸的最大應力值出現時間不與剛體組2 出現最大加速度時間相同,分析原因是此時輸出軸承受輸出齒輪傳遞的以z軸為中心順時針方向運動的力已經減小,相當于在該時刻輸出軸主要承受以z軸為中心逆時針方向的負載扭矩,導致在0.159 s 時輸出軸出現最大等效應力。
圖11 改進后輸出軸應力云圖
Fig.11 Stress cloud diagram of output shaft after improvement
3.2 過載荷試驗驗證
將結構改進后的輸出齒輪和輸出軸安裝到換擋執行機構殼體中,對齒輪系統進行試驗驗證,輸入端電機參數如前所述,在輸出軸負載端施加扭矩,扭矩方向分別為順時針和逆時針,扭矩大小皆為22 N·m,如圖12所示。
圖12 齒輪系統試驗驗證
Fig.12 Experimental verification of gear system
試驗結果表明,在承受超出正常工況負載扭矩46.7%的情況下,輸出齒輪和輸出軸未出現斷裂失效現象,驗證了本次結構改進設計的合理性和可行性。
4 結論
本文針對在試驗過程中換擋執行機構輸出齒輪扇形根部發生斷裂的現象,應用有限元分析的方法對齒輪系統進行仿真計算并進行結構改進設計。結構改進后的輸出齒輪最大應力由143 MPa 減小到40.7 MPa,減小了69.9%,輸出軸最大應力由110 MPa 減小到72.3 MPa,減小了34.5%。將改進后的齒輪系統安裝到變速器換擋執行機構殼體中進行試驗驗證,未出現斷裂失效現象。結構改進后的齒輪系統在當前工況下強度方面已經滿足要求,本次的結構改進設計提高了齒輪系統工作過程中的穩定性和可靠性,節省了其在使用過程中的維修成本。
-
軟件
+關注
關注
69文章
5072瀏覽量
88628 -
齒輪
+關注
關注
3文章
271瀏覽量
25405 -
動力學
+關注
關注
0文章
107瀏覽量
17122
原文標題:換擋執行機構齒輪系統仿真及結構改進設計
文章出處:【微信號:EDC電驅未來,微信公眾號:EDC電驅未來】歡迎添加關注!文章轉載請注明出處。
發布評論請先 登錄
相關推薦
電力拖動系統的動力學課件
基于多體系統動力學的空氣懸架大客車平順性試驗仿真研究
帶齒輪傳動的機車-軌道空間耦合動力學模型
灰色預測模型的系統動力學仿真
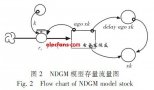
四配流窗口軸向柱塞馬達多體動力學聯合仿真分析
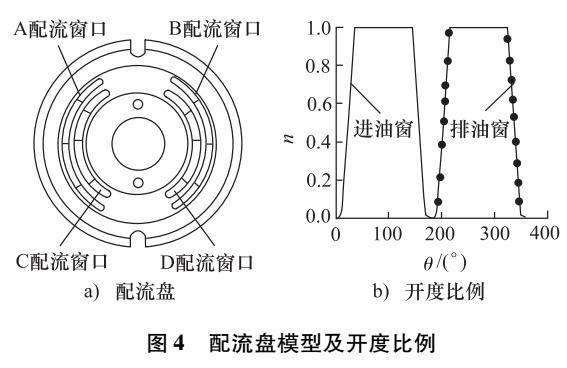
基于風電機組傳動鏈動力學仿真設計
50 m天線輪軌接觸動力學仿真
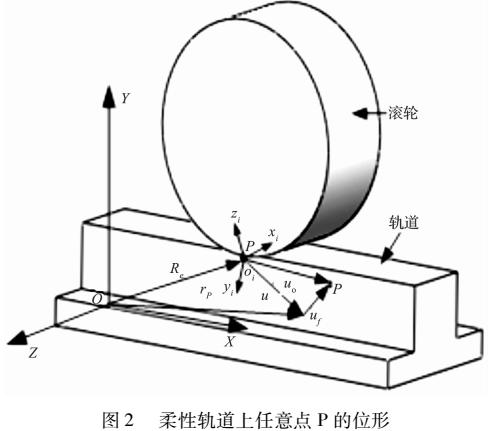
機械系統動力學分析及ADAMS應用電子教程免費下載
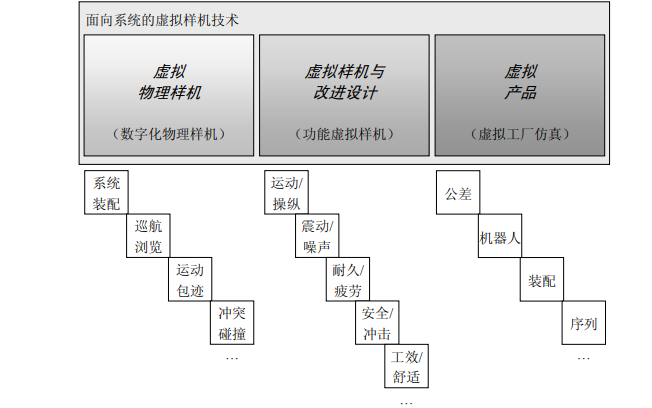
評論