電子發(fā)燒友網(wǎng)報道(文/梁浩斌)幾乎與電動汽車產(chǎn)業(yè)同步,碳化硅器件的發(fā)展也在近十多年間高速發(fā)展。作為第三代半導體,采用碳化硅材料所制造的半導體器件在電氣特性上的優(yōu)異表現(xiàn),讓它在電動汽車應用上受到了業(yè)界關注,隨著市場對電動汽車長續(xù)航、高壓電氣架構(gòu)、快充等需求,碳化硅正在電動汽車上加速普及。
近幾年可以看到國內(nèi)多家廠商,包括整車廠、功率器件廠商等都在陸續(xù)推出車規(guī)級碳化硅功率模塊產(chǎn)品,同時也有國內(nèi)廠商推出車規(guī)碳化硅MOSFET產(chǎn)品,那么碳化硅模塊與碳化硅MOSFET有什么區(qū)別?
碳化硅模塊和碳化硅MOSFET的區(qū)別
一般我們說碳化硅MOSFET的時候是指碳化硅MOSFET單管,即將碳化硅MOSFET芯片封裝在一個獨立的封裝中,比如典型的TO-220、TO-247封裝。碳化硅MOSFET單管通常有三個引腳,分別對應輸出端的Drain(漏極)、輸入端的Source(源極)和控制端的Gate(柵極)。
而當應用在大電流電路中時,出于對損耗以及散熱性能的要求,由多個單管、二極管等元件封裝在一起形成模塊的產(chǎn)品應運而生。碳化硅模塊又分為碳化硅MOSFET +碳化硅SBD構(gòu)成,以及只由多個碳化硅單管構(gòu)成的模塊兩種,而常用的結(jié)構(gòu)又有H橋、半橋、全橋等。
圖源:賽米控
根據(jù)賽米控的數(shù)據(jù),采用全碳化硅模塊在最大開關頻率下能夠最多相比同規(guī)格硅基IGBT功率模塊降低85%的開關損耗。而即使相比碳化硅MOSFET單管,碳化硅模塊的工作效率也由于在封裝中的寄生電感更低,開關損耗更低,因此工作效率、工作開關頻率更高,可以幫助減少無源器件的尺寸,以及整體模塊的尺寸。
不過,在前面提到碳化硅模塊的兩種形式之外,也有車企以及電控供應商采用單管并聯(lián)的方案來設計功率模塊。比如第一款大規(guī)模應用碳化硅功率器件的電動車型特斯拉Model 3上,采用了一種名為TPAK的封裝模塊并聯(lián),在主驅(qū)逆變器功率模塊上共有24顆TPAK,采用單管并聯(lián)的方式排列,每顆TPAK封裝中有兩顆碳化硅MOSFET芯片,功率模塊整體有共48顆碳化硅MOSFET。
另外陽光電源此前推出的雙電機控制器中也采用了并聯(lián)TPAK的方案,并兼容硅基以及碳化硅基功率半導體。
碳化硅模塊的主要難點
碳化硅模塊主要難點可以分為兩大方面,一是引線鍵合、二是散熱。
引線鍵合是在一種在封裝中將多個器件之間進行互連的方式,一般使用細金屬線,利用熱、壓力、超聲波等使金屬引線與基板焊盤緊密焊合,但在模塊中復雜的互聯(lián)結(jié)構(gòu)會產(chǎn)生較大的寄生電容或寄生電感。由于碳化硅器件具有高頻特性、柵極電荷低、開關速度快等特性,在實際應用中容易出現(xiàn)電壓過沖和振蕩現(xiàn)象,造成器件電壓應力、損耗增加和電磁干擾等問題。
因此在互連方面,目前正在從傳統(tǒng)的鋁線鍵合以及超聲焊接,逐步轉(zhuǎn)向鋁包銅線、銅線鍵合等方式,同時引線框架也采用銀燒結(jié)技術來代替?zhèn)鹘y(tǒng)的鉛/錫合金焊。
在散熱方面,盡管碳化硅器件可以工作在更高的溫度,理論最高工作溫度可以超過500℃,但與此同時碳化硅功率模塊在相同功率等級下體積大幅降低,也就是功率密度較高,因此對散熱的要求其實反而更高了。即使是耐熱性能較好的碳化硅器件,在工作溫度過高的情況下也會造成性能下降,加上封裝材料的熱膨脹系數(shù)失配等,容易造成可靠性隱患。
所以目前在碳化硅模塊散熱上,通過優(yōu)化傳熱距離以及傳熱面積的封裝,來提高散熱性能,比如通過雙面散熱、降低結(jié)構(gòu)層數(shù)等方式來提升散熱效率。
小結(jié):
隨著碳化硅模塊產(chǎn)品大規(guī)模落地,新能源汽車應用案例的增多,碳化硅模塊會在不久的將來成為電動汽車的標配。
-
碳化硅
+關注
關注
25文章
2752瀏覽量
49027
發(fā)布評論請先 登錄
相關推薦
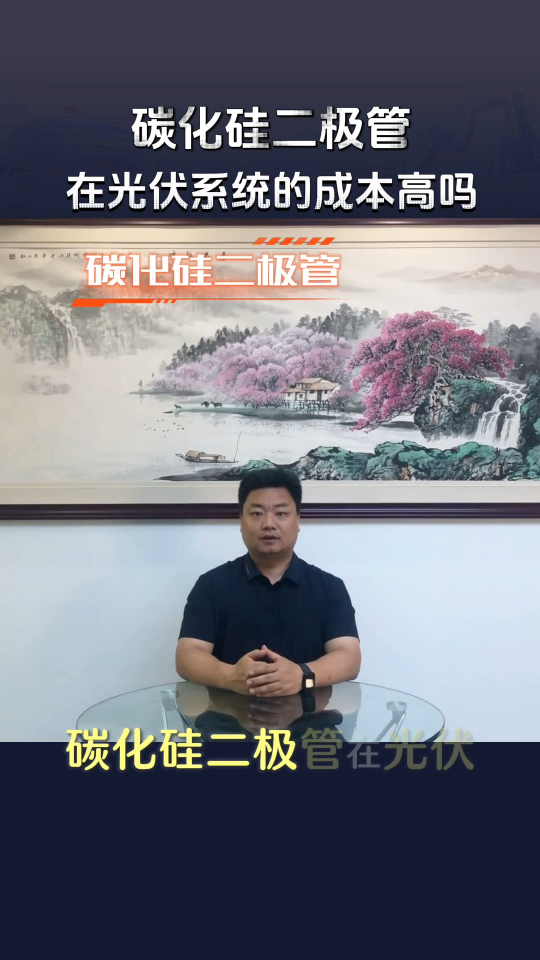
碳化硅功率器件的工作原理和應用
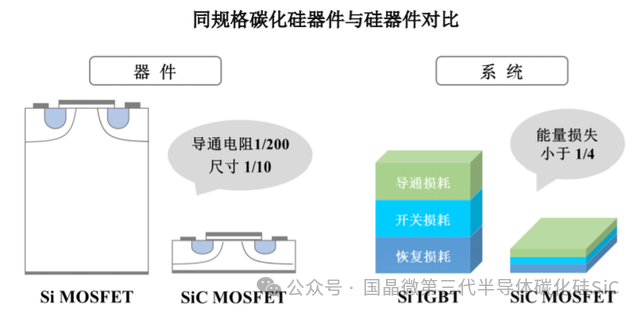
碳化硅功率器件的優(yōu)勢和應用領域
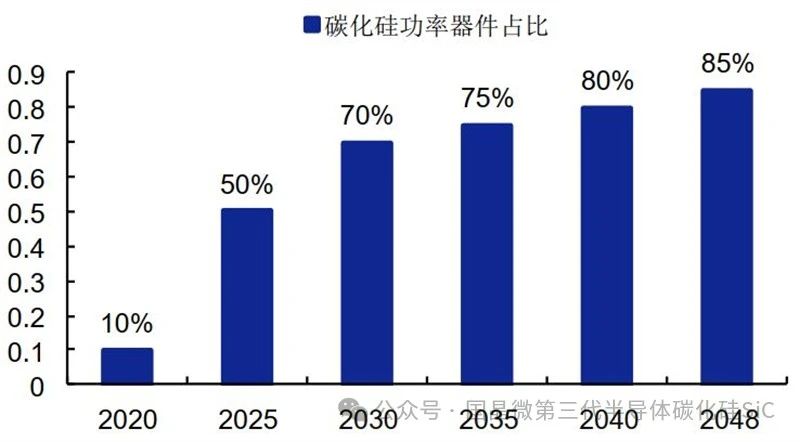
Wolfspeed推出創(chuàng)新碳化硅模塊
碳化硅功率器件的優(yōu)點和應用
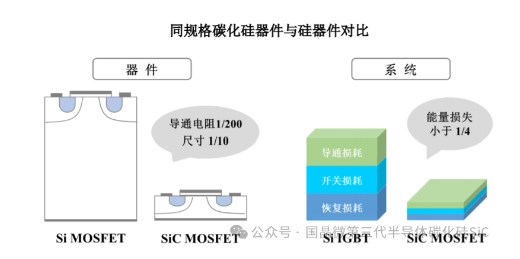
碳化硅功率器件有哪些優(yōu)勢

使用碳化硅模塊的充電設備設計
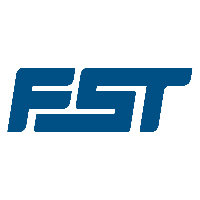
碳化硅(SiC)功率器件的開關性能比較
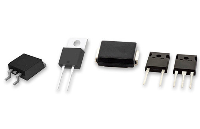
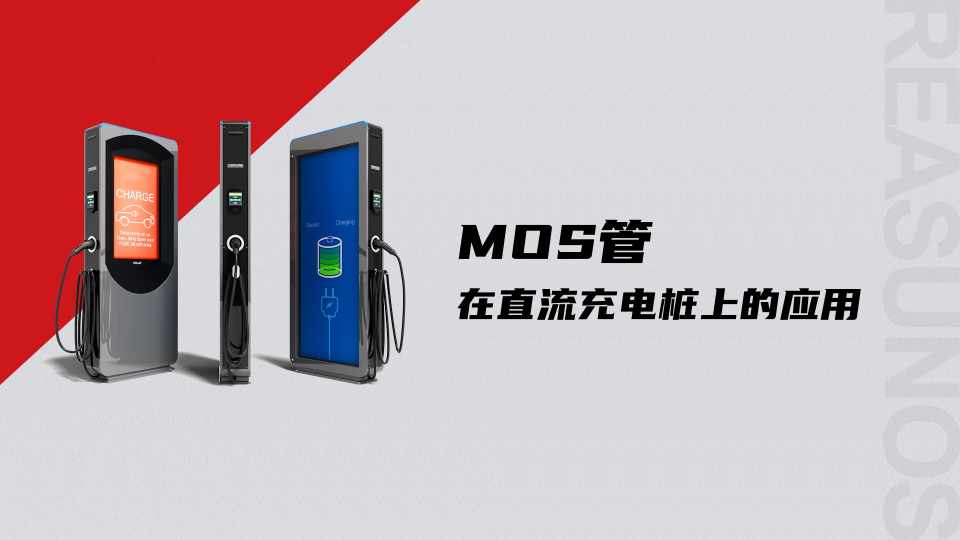
碳化硅壓敏電阻 - 氧化鋅 MOV
碳化硅產(chǎn)業(yè)鏈圖譜
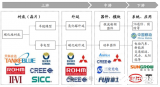
碳化硅器件封裝與模塊化的關鍵技術
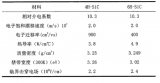
評論